- お役立ち記事
- Basics of PID control, optimal PID tuning technology and its examples
月間77,185名の
製造業ご担当者様が閲覧しています*
*2025年2月28日現在のGoogle Analyticsのデータより
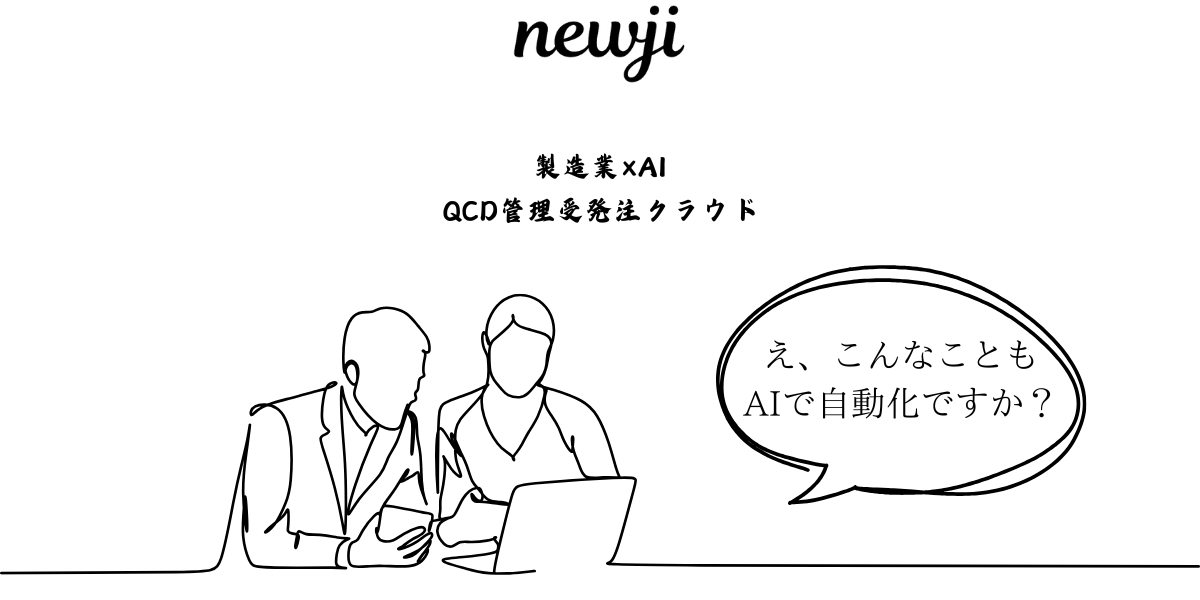
Basics of PID control, optimal PID tuning technology and its examples
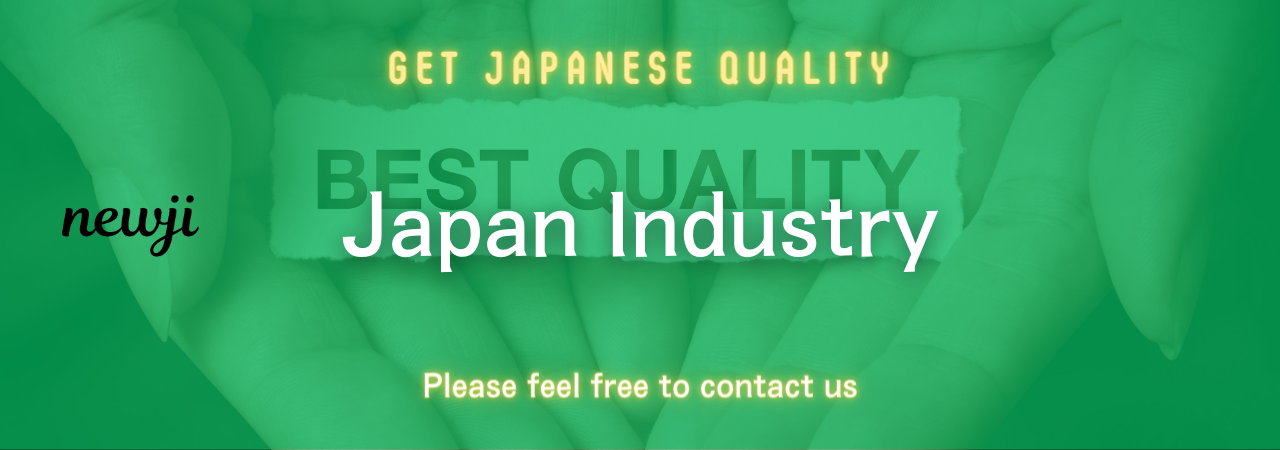
PID control, or Proportional-Integral-Derivative control, is a popular feedback control strategy widely used across various industries for process control applications.
Its versatility and simplicity make it a go-to method for regulating systems such as temperature, speed, pressure, and other variables.
Understanding the basics of PID control and the principles behind optimal PID tuning can greatly enhance the efficiency and performance of a system.
目次
Understanding PID Control
PID control is a closed-loop mechanism that continuously calculates an error value as the difference between a desired setpoint and a measured process variable.
The primary goal of PID control is to minimize this error over time by adjusting the control inputs.
PID controllers are composed of three basic components: Proportional, Integral, and Derivative.
Proportional Control
Proportional control is the simplest part of the PID controller.
It outputs a control signal that is directly proportional to the current error value.
The proportional gain, denoted as Kp, determines the ratio to which the error is multiplied to yield the output.
While proportional control can significantly reduce the error, it does not fully eliminate it, especially in systems with a steady-state error.
Integral Control
The integral component addresses the shortcoming of proportional control by accumulating the error over time and integrating it.
The integrated error is then multiplied by the integral gain, Ki.
This approach helps eliminate steady-state error, ensuring the process variable reaches the setpoint.
However, excessive integral control can lead to oscillations and instability.
Derivative Control
Derivative control predicts future error based on its current rate of change.
By considering the slope of the error, the derivative component can dampen the system’s response, increasing its stability.
The derivative gain, Kd, adjusts how much the derivative effect influences the control signal.
While useful, derivative control is sensitive to noise and requires careful tuning.
Optimal PID Tuning
The effectiveness of a PID controller is largely dependent on the precise tuning of its parameters: Kp, Ki, and Kd.
Optimal tuning entails finding the right balance among these values to achieve the desired system performance without unnecessary oscillations or lag.
Several methods exist for tuning PID controllers.
Ziegler-Nichols Tuning Method
The Ziegler-Nichols method is one of the most traditional and commonly used approaches.
It involves conducting a series of tests to determine the ultimate gain and oscillation period of the system.
Based on these results, heuristic rules are applied to estimate the PID parameters.
While effective for many systems, it can lead to aggressive settings and is not always suitable for all types of processes.
Cohen-Coon Tuning Method
The Cohen-Coon tuning method offers an alternative approach, especially useful for processes with significant lag.
This technique focuses on the process’s dead time and time constant to adjust the PID parameters.
Though less aggressive than Ziegler-Nichols, it still requires a good understanding of the system’s dynamics to apply properly.
Software-Based Tuning
Modern control systems often incorporate software solutions for PID tuning.
These automated tools utilize algorithms to iteratively adjust the PID parameters until an optimal configuration is reached.
Software-based tuning is advantageous as it reduces manual effort and often yields more precise results.
However, the cost and complexity of these solutions can be a drawback for smaller applications.
Examples of PID Control Applications
PID control finds applications in a multitude of fields due to its adaptability and efficiency.
Here are a few illustrative examples:
Temperature Control
In industrial processes such as furnace operation or chemical reactions, maintaining a specific temperature is crucial.
A PID controller can adjust the heat input to a system based on the temperature difference from the setpoint, ensuring a stable and controlled environment for optimal reactions.
Speed Control
Electric motors are commonly controlled using PID controllers, particularly in conveyor belts, robotics, and automotive systems.
The PID controller adjusts the voltage supplied to the motor, regulating its speed to remain constant despite changes in load or resistance.
Pressure Control
PID control is instrumental in maintaining desired pressure levels in systems like pipelines, where fluctuations could lead to disruptions.
By modulating valve positions or pump speeds, a PID controller ensures the pressure stays within specified limits.
Level Control
In storage tanks or reservoirs, maintaining a desired liquid level is essential.
PID controllers regulate inputs such as inflow and outflow rates to keep the liquid levels consistent, preventing overflow or shortage.
Conclusion
PID control remains a cornerstone of modern process control, providing a robust solution for a variety of challenges.
Understanding its components—proportional, integral, and derivative—as well as the tuning methods, enables you to harness its full potential.
Whether applied in temperature, speed, pressure, or level control, PID controllers pave the way for efficient, stable, and reliable systems.
Exploring further into real-world applications and fine-tuning techniques could deepen comprehension and mastery of this invaluable tool.
資料ダウンロード
QCD管理受発注クラウド「newji」は、受発注部門で必要なQCD管理全てを備えた、現場特化型兼クラウド型の今世紀最高の受発注管理システムとなります。
ユーザー登録
受発注業務の効率化だけでなく、システムを導入することで、コスト削減や製品・資材のステータス可視化のほか、属人化していた受発注情報の共有化による内部不正防止や統制にも役立ちます。
NEWJI DX
製造業に特化したデジタルトランスフォーメーション(DX)の実現を目指す請負開発型のコンサルティングサービスです。AI、iPaaS、および先端の技術を駆使して、製造プロセスの効率化、業務効率化、チームワーク強化、コスト削減、品質向上を実現します。このサービスは、製造業の課題を深く理解し、それに対する最適なデジタルソリューションを提供することで、企業が持続的な成長とイノベーションを達成できるようサポートします。
製造業ニュース解説
製造業、主に購買・調達部門にお勤めの方々に向けた情報を配信しております。
新任の方やベテランの方、管理職を対象とした幅広いコンテンツをご用意しております。
お問い合わせ
コストダウンが利益に直結する術だと理解していても、なかなか前に進めることができない状況。そんな時は、newjiのコストダウン自動化機能で大きく利益貢献しよう!
(β版非公開)