- お役立ち記事
- Basics of PID control system and high-precision implementation method in digital control
月間76,176名の
製造業ご担当者様が閲覧しています*
*2025年3月31日現在のGoogle Analyticsのデータより
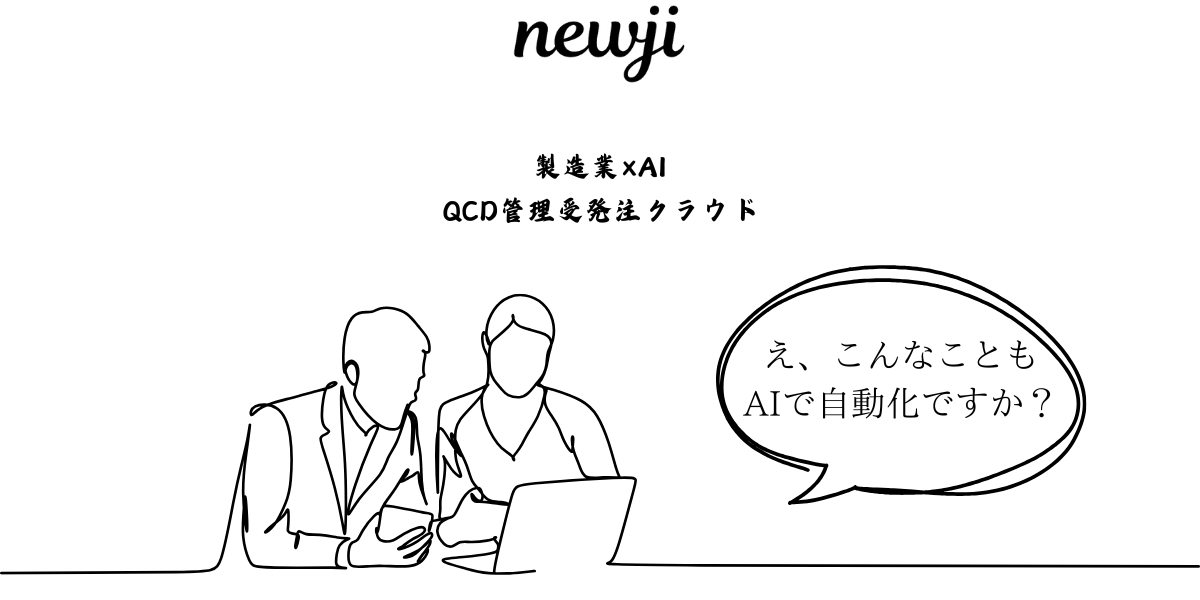
Basics of PID control system and high-precision implementation method in digital control
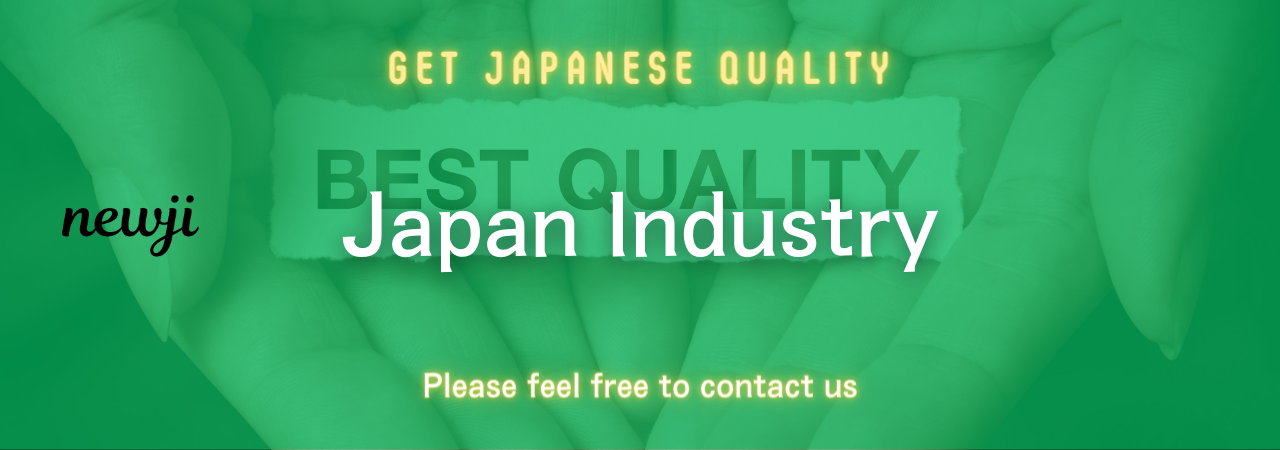
目次
Understanding PID Control Systems
PID control systems are a core component in the world of automation and control engineering.
The acronym PID stands for Proportional, Integral, and Derivative, which are the three fundamental elements of the system.
These systems are used to maintain a desired level of control over a process by minimizing the deviation from a setpoint.
Proportional Control
The proportional element in a PID controller is responsible for adjusting the control signal based on the current error value.
Error is defined as the difference between the setpoint and the process variable.
The proportional gain, often represented as ‘Kp’, determines how much the control output will be adjusted in response to the error.
A higher proportional gain will result in a more aggressive response, while a lower gain will lead to a smoother response.
However, if the gain is too high, it can cause the system to become unstable, oscillating around the setpoint.
Integral Control
Integral control aims to eliminate the residual steady-state error that can exist in a control system.
This component accumulates the error over time and integrates it to the control output using the integral gain, ‘Ki’.
The integral action continually adjusts the control output until the error reaches zero.
However, excessive integral action can lead to overshooting and oscillations, as it could overcompensate for past errors.
Derivative Control
The derivative component of a PID controller predicts future errors by calculating the rate of change of the process variable.
It provides a damping effect, smoothing out the control action by considering how quickly the error is changing.
The derivative gain, ‘Kd’, determines how much the control signal should be adjusted based on the rate of error change.
While beneficial in reducing overshooting and providing stability, excessive derivative action can amplify noise in the system, leading to erratic behavior.
High-Precision Implementation in Digital Control
Implementing a PID controller in a digital control context involves several crucial steps to ensure precision and robustness.
Discretization of PID Controller
In digital control systems, continuous-time PID controllers must be discretized.
This involves converting the continuous PID equations into discrete equivalents that can be used in digital processors.
Common methods include the forward Euler, backward Euler, and trapezoidal (Tustin) methods.
Choosing the right method impacts the accuracy and stability of the digital PID controller, with the Tustin method often preferred for its balance of characteristics.
Tuning PID Parameters
Tuning the PID parameters (Kp, Ki, and Kd) is critical for high-precision performance.
Several techniques are available, ranging from manual tuning to more sophisticated methods like the Ziegler-Nichols method, Cohen-Coon method, and using software-based PID optimization tools.
Correctly tuned parameters will ensure a PID controller responds accurately without instability or excessive overshoot.
Implementation Challenges
When implementing PID controllers digitally, challenges that arise include sampling rate selection, handling of time delays, and execution delays due to processor limitations.
The sampling rate should be high enough to capture system dynamics but balanced with processor capabilities to prevent excessive computational load.
Managing time delays involves implementing compensatory measures such as Smith predictors or designing the control system to be robust to inherent delays.
Anti-Windup Techniques
Integral windup is a common issue in PID control where the integral term accumulates excessively due to actuator limits.
This can cause significant delay in settling time or overshoot when the system resumes normal operation.
Implementing anti-windup techniques, such as clamping or back-calculation, prevents the integral component from growing beyond a useful range, stabilizing system behavior.
Noise Filtering and Reduction
In high-precision digital control, reducing system noise is crucial to maintain accurate control signals.
Noise adversely affects the derivative term and may destabilize the PID system.
Low-pass filters or smoothing algorithms can be employed to minimize the impact of noise without sacrificing real-time response.
Applications of PID Control Systems
PID controllers are ubiquitous in various industries due to their simplicity and effectiveness.
They are integral in process industries like chemical manufacturing, where temperature, pressure, and flow rates require precise control.
In automotive systems, PID controllers regulate speed and engine parameters for optimal performance.
Robotics and aerospace also rely on PID systems to maintain stability and control of complex mechanisms.
Future Trends and Innovations
As technology evolves, PID control systems are being integrated with advanced algorithms and machine learning for enhanced performance.
Adaptive PID controllers adjust parameters in real-time, accommodating system changes for increased accuracy.
The integration of IoT devices provides new opportunities for remote monitoring and control, expanding the capabilities of digital PID systems in various applications.
In summary, a comprehensive understanding of PID control systems and their implementation in digital control is essential for achieving high-precision control in various applications.
Through effective parameter tuning, addressing implementation challenges, and leveraging technological advancements, PID systems continue to play a critical role in modern automation and control systems.
資料ダウンロード
QCD管理受発注クラウド「newji」は、受発注部門で必要なQCD管理全てを備えた、現場特化型兼クラウド型の今世紀最高の受発注管理システムとなります。
ユーザー登録
受発注業務の効率化だけでなく、システムを導入することで、コスト削減や製品・資材のステータス可視化のほか、属人化していた受発注情報の共有化による内部不正防止や統制にも役立ちます。
NEWJI DX
製造業に特化したデジタルトランスフォーメーション(DX)の実現を目指す請負開発型のコンサルティングサービスです。AI、iPaaS、および先端の技術を駆使して、製造プロセスの効率化、業務効率化、チームワーク強化、コスト削減、品質向上を実現します。このサービスは、製造業の課題を深く理解し、それに対する最適なデジタルソリューションを提供することで、企業が持続的な成長とイノベーションを達成できるようサポートします。
製造業ニュース解説
製造業、主に購買・調達部門にお勤めの方々に向けた情報を配信しております。
新任の方やベテランの方、管理職を対象とした幅広いコンテンツをご用意しております。
お問い合わせ
コストダウンが利益に直結する術だと理解していても、なかなか前に進めることができない状況。そんな時は、newjiのコストダウン自動化機能で大きく利益貢献しよう!
(β版非公開)