- お役立ち記事
- Basics of plastic injection molding, countermeasures against molding defects, and how to utilize them in molded product design
月間76,176名の
製造業ご担当者様が閲覧しています*
*2025年3月31日現在のGoogle Analyticsのデータより
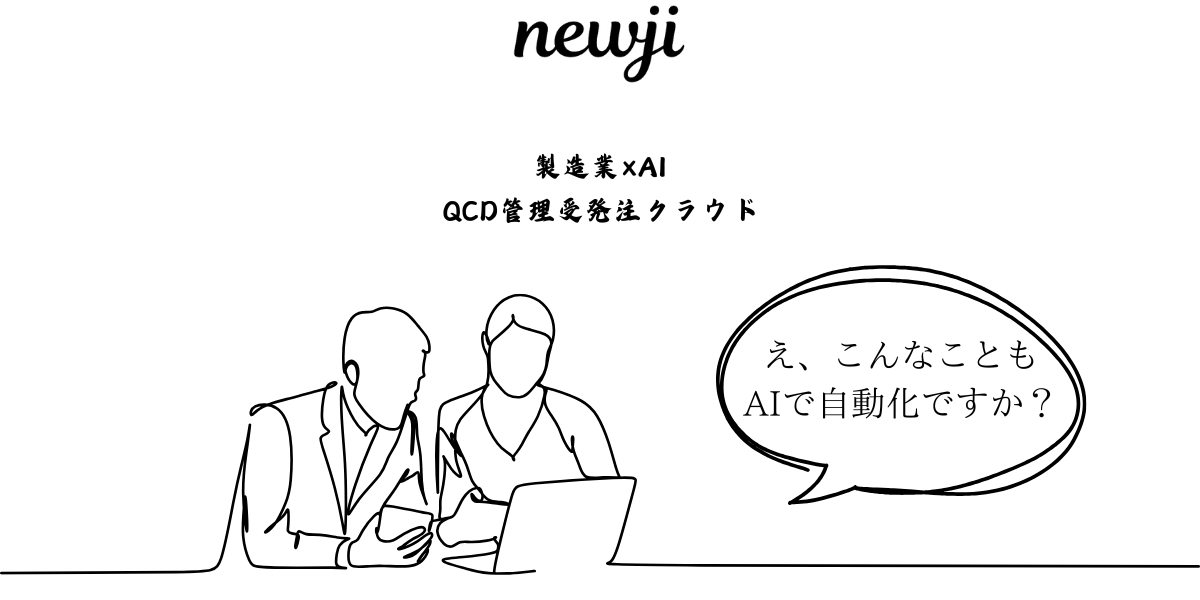
Basics of plastic injection molding, countermeasures against molding defects, and how to utilize them in molded product design
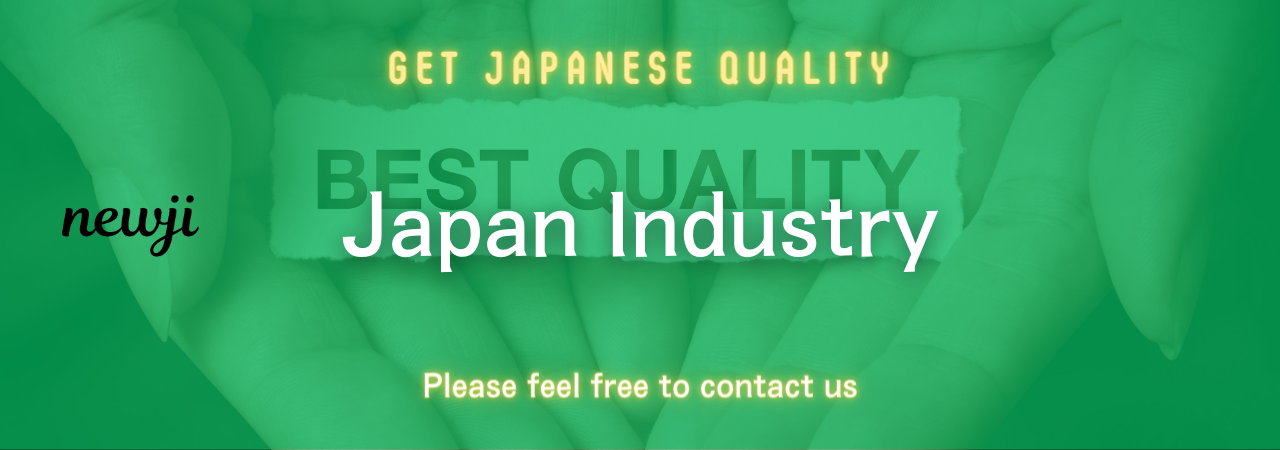
目次
Understanding Plastic Injection Molding
Plastic injection molding is a widely-used manufacturing process for producing a variety of plastic parts.
It involves injecting molten plastic into a mold cavity, allowing it to cool and harden, and then ejecting the finished part.
This method is popular because of its ability to produce high volumes of parts with excellent precision and consistency.
The Process of Plastic Injection Molding
The process begins with the melting of plastic pellets in a heated barrel.
Once the plastic reaches the desired viscosity, it is injected into a mold under high pressure.
The mold, which is typically made from steel or aluminum, shapes the plastic into the desired form.
After the plastic cools and solidifies, the mold is opened, and the part is ejected.
This cycle is repeated to produce multiple identical parts.
Materials Used in Injection Molding
A vast range of thermoplastics can be used in injection molding, each offering unique properties to suit specific applications.
Some common materials include polypropylene, ABS, nylon, and polycarbonate.
The choice of material depends on factors such as strength, flexibility, temperature resistance, and cost.
Additives and colorants can also be mixed with the base material to achieve particular characteristics like flame retardancy or UV resistance.
Countermeasures Against Molding Defects
While injection molding is a highly efficient process, it is not without its challenges.
Defects can occur, impacting the quality of the final product.
Understanding these defects and their countermeasures is essential for maintaining production standards.
Common Molding Defects
1. **Warpage**: Warpage occurs when different areas of a molded part cool unevenly, leading to distorting or twisting.
Proper mold design and uniform cooling rates can help mitigate warpage.
2. **Flash**: This refers to thin layers of plastic that overflow at the parting line of the mold.
Ensuring precise alignment of mold plates and maintaining optimal clamping pressure are effective measures to prevent flash.
3. **Sink Marks**: These depressions on the surface of the part occur due to shrinkage in thick areas.
Adjusting cooling time and using uniform wall thickness can reduce sink marks.
4. **Weld Lines**: These lines appear where two flows of molten plastic meet.
Improving melt temperature and injection speed can enhance the bonding and eliminate weld lines.
5. **Short Shots**: This defect occurs when the mold cavity is not completely filled.
Ensuring proper injection pressure and material flow can prevent short shots.
Addressing Defects Through Design and Process
Defects can often be traced back to design or process factors.
For instance, part design with consistent wall thickness can significantly reduce sink marks and warpage.
Mold design is also crucial; incorporating features like adequate venting and balanced cooling channels can minimize defects.
Process parameters such as temperature, pressure, and cycle time need to be optimized for the chosen material and part geometry.
Implementing a robust quality control process and employing technologies like computer-aided design (CAD) can also forecast potential issues and address them before production begins.
Utilizing Injection Molding in Product Design
Design plays a crucial role in successful injection molding.
To fully leverage this method, designers must integrate molding considerations early in the product development phase.
Design for Manufacturability
Design for manufacturability (DFM) is a principle that ensures products are designed with manufacturing capabilities in mind.
For injection molding, this means incorporating features like draft angles to facilitate easy ejection and avoiding undercuts that complicate mold designs.
Simplifying the geometry can reduce production costs and improve the overall quality of the molded part.
Prototyping and Iteration
Before commencing large-scale production, the creation of prototypes allows designers to test their designs for functionality and aesthetic appeal.
Rapid prototyping techniques, such as 3D printing, can be used to verify design feasibility and make necessary adjustments without the expense of creating a full mold.
Iteration through various prototype phases can ensure that the design is optimized for both performance and manufacturability.
Sustainability Considerations
As sustainability becomes a critical concern, incorporating eco-friendly practices in injection molding is increasingly important.
Designing for reduced material usage and recycling of scrap materials can minimize environmental impact.
Additionally, selecting recyclable or biodegradable materials contributes to sustainable manufacturing and product lifecycle management.
Conclusion
Plastic injection molding is a versatile and efficient manufacturing method.
By understanding the process, identifying potential defects, and designing with production in mind, manufacturers can produce high-quality, consistent parts.
Incorporating DFM principles and considering environmental impacts can further enhance the benefits of injection molding, supporting both innovation and sustainability in product design.
資料ダウンロード
QCD管理受発注クラウド「newji」は、受発注部門で必要なQCD管理全てを備えた、現場特化型兼クラウド型の今世紀最高の受発注管理システムとなります。
ユーザー登録
受発注業務の効率化だけでなく、システムを導入することで、コスト削減や製品・資材のステータス可視化のほか、属人化していた受発注情報の共有化による内部不正防止や統制にも役立ちます。
NEWJI DX
製造業に特化したデジタルトランスフォーメーション(DX)の実現を目指す請負開発型のコンサルティングサービスです。AI、iPaaS、および先端の技術を駆使して、製造プロセスの効率化、業務効率化、チームワーク強化、コスト削減、品質向上を実現します。このサービスは、製造業の課題を深く理解し、それに対する最適なデジタルソリューションを提供することで、企業が持続的な成長とイノベーションを達成できるようサポートします。
製造業ニュース解説
製造業、主に購買・調達部門にお勤めの方々に向けた情報を配信しております。
新任の方やベテランの方、管理職を対象とした幅広いコンテンツをご用意しております。
お問い合わせ
コストダウンが利益に直結する術だと理解していても、なかなか前に進めることができない状況。そんな時は、newjiのコストダウン自動化機能で大きく利益貢献しよう!
(β版非公開)