- お役立ち記事
- Basics of plastic injection molding technology and key points of molding defect prevention technology
月間76,176名の
製造業ご担当者様が閲覧しています*
*2025年3月31日現在のGoogle Analyticsのデータより
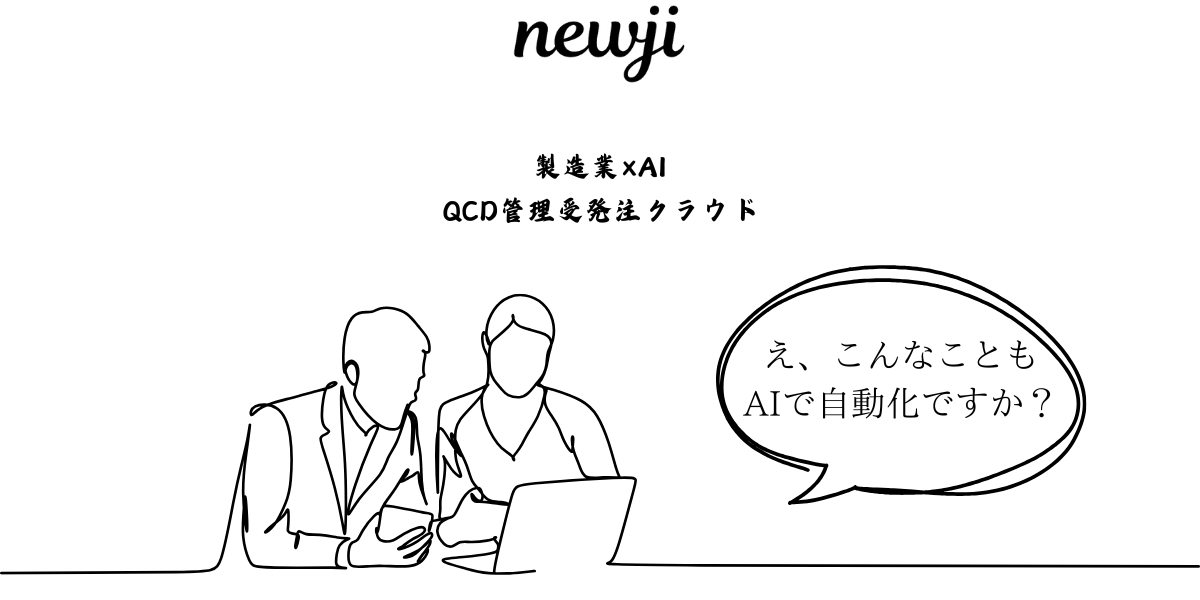
Basics of plastic injection molding technology and key points of molding defect prevention technology
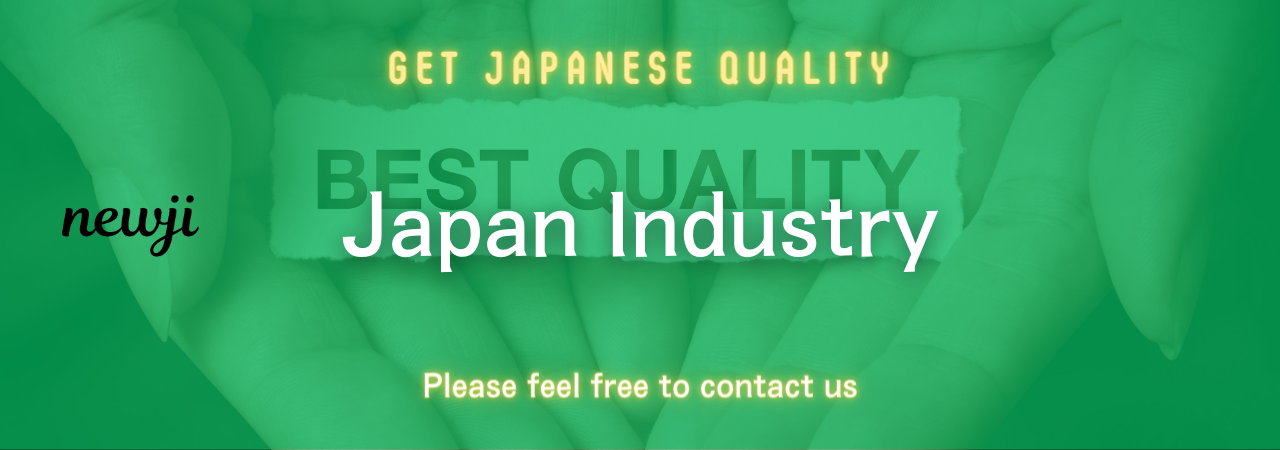
目次
Understanding Plastic Injection Molding
Plastic injection molding is a manufacturing process used to create a wide range of plastic products.
It involves injecting molten plastic material into a mold cavity, allowing it to cool and solidify into the desired shape.
This versatile technique is widely used due to its efficiency, precision, and ability to produce complex geometries.
The process begins with the melting of plastic granules, which are then fed into a heated barrel.
The material is mixed and homogenized before being injected into the mold under high pressure.
Once inside the mold, the plastic material cools and solidifies, taking the form of the mold cavity.
The Importance of Mold Design
One of the critical components of plastic injection molding is the design of the mold itself.
Mold design is crucial because it directly affects the quality, performance, and cost of the final product.
Design considerations include the material flow, cooling time, ejection mechanism, and the number of cavities.
A well-designed mold ensures that the material flows uniformly, preventing defects such as sink marks or warping.
In addition, efficient mold designs facilitate quicker cooling and ejection, reducing cycle times and increasing production efficiency.
Key Points in Preventing Molding Defects
Preventing defects in plastic injection molding is crucial to maintaining high product quality and reducing waste.
Common molding defects include sink marks, warping, flashing, and voids.
Here are key tips for minimizing these issues:
Optimizing Processing Parameters
Carefully controlling the processing parameters is essential to preventing molding defects.
Key parameters include temperature, pressure, and cooling time.
1. **Temperature:** Maintaining the optimal temperature for both the mold and the molten plastic is critical.
If the temperature is too high, it can cause warping or degrade the material.
If too low, it may result in incomplete filling of the mold.
2. **Pressure:** Adequate pressure ensures that the material fills the entire mold cavity.
Insufficient pressure can lead to voids or incomplete parts.
3. **Cooling Time:** Proper cooling time allows the plastic to solidify uniformly.
Insufficient cooling can cause warping or deformation.
Choosing the Right Material
The choice of plastic material greatly impacts the molding process and the final product quality.
Different plastics have varying flow characteristics, shrinkage rates, and thermal properties.
1. **Material Compatibility:** Ensure that the selected material is compatible with the intended application and the design specifications.
2. **Shrinkage Rate:** Consider the material’s shrinkage rate during cooling to prevent dimensional inaccuracies.
3. **Thermal Properties:** Materials with appropriate thermal properties reduce the risk of warping or deformation.
Designing for Manufacturability
Product design plays a crucial role in preventing molding defects.
Consider the following design principles to ensure manufacturability:
1. **Uniform Wall Thickness:** Maintaining consistent wall thickness helps reduce stress concentrations and warping.
2. **Ribs and Bosses:** Incorporate ribs and bosses to reinforce the structure and minimize sink marks.
3. **Draft Angles:** Apply appropriate draft angles to facilitate easy ejection from the mold, reducing the risk of part damage.
Regular Mold Maintenance
Regular maintenance of molds is vital to preserving their performance and longevity.
Neglecting mold maintenance can lead to defects and increased production downtime.
1. **Cleaning:** Regularly clean the mold surfaces to prevent buildup of material or debris.
2. **Inspection:** Conduct routine inspections to check for wear, damage, or misalignment that may affect the molding process.
3. **Lubrication:** Ensure proper lubrication of moving parts to prevent friction and wear.
Conclusion
Plastic injection molding is a sophisticated manufacturing process that requires precise control over various parameters and careful design considerations.
By optimizing processing conditions, choosing the right materials, and emphasizing manufacturability in design, manufacturers can effectively prevent molding defects.
Regular mold maintenance further ensures consistent quality and efficiency.
Understanding and implementing these key points result in reliable and high-quality plastic products, meeting the demands of diverse industries.
Leveraging best practices in injection molding is crucial to achieving success and maintaining a competitive edge in the market.
資料ダウンロード
QCD管理受発注クラウド「newji」は、受発注部門で必要なQCD管理全てを備えた、現場特化型兼クラウド型の今世紀最高の受発注管理システムとなります。
ユーザー登録
受発注業務の効率化だけでなく、システムを導入することで、コスト削減や製品・資材のステータス可視化のほか、属人化していた受発注情報の共有化による内部不正防止や統制にも役立ちます。
NEWJI DX
製造業に特化したデジタルトランスフォーメーション(DX)の実現を目指す請負開発型のコンサルティングサービスです。AI、iPaaS、および先端の技術を駆使して、製造プロセスの効率化、業務効率化、チームワーク強化、コスト削減、品質向上を実現します。このサービスは、製造業の課題を深く理解し、それに対する最適なデジタルソリューションを提供することで、企業が持続的な成長とイノベーションを達成できるようサポートします。
製造業ニュース解説
製造業、主に購買・調達部門にお勤めの方々に向けた情報を配信しております。
新任の方やベテランの方、管理職を対象とした幅広いコンテンツをご用意しております。
お問い合わせ
コストダウンが利益に直結する術だと理解していても、なかなか前に進めることができない状況。そんな時は、newjiのコストダウン自動化機能で大きく利益貢献しよう!
(β版非公開)