- お役立ち記事
- Basics of plastic injection molding technology and practical points to prevent molding defects
月間77,185名の
製造業ご担当者様が閲覧しています*
*2025年2月28日現在のGoogle Analyticsのデータより
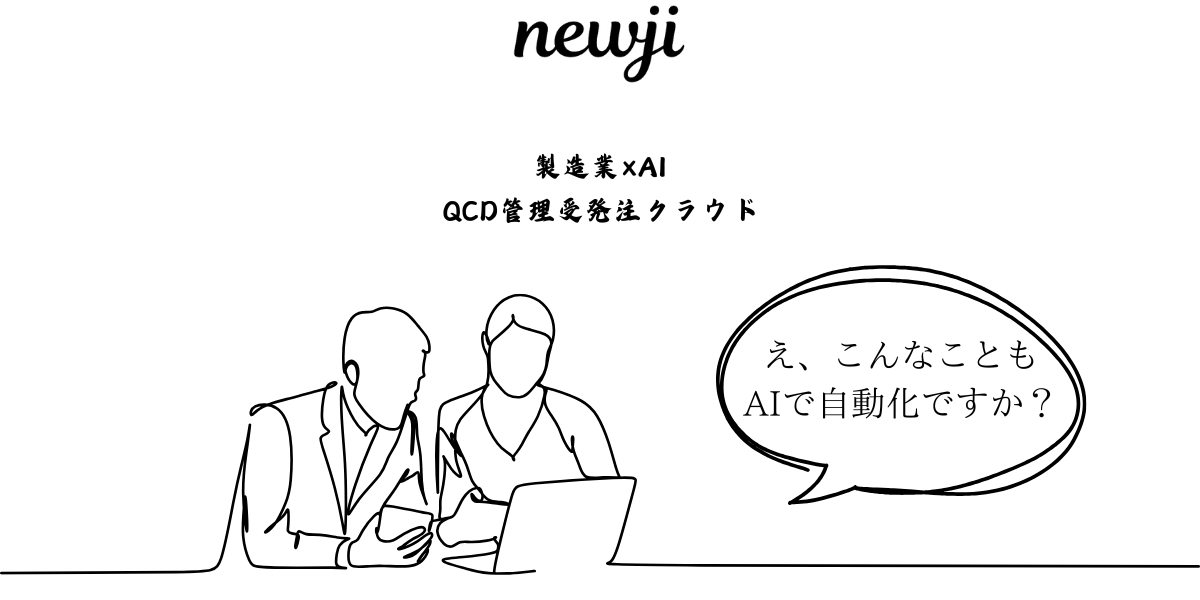
Basics of plastic injection molding technology and practical points to prevent molding defects
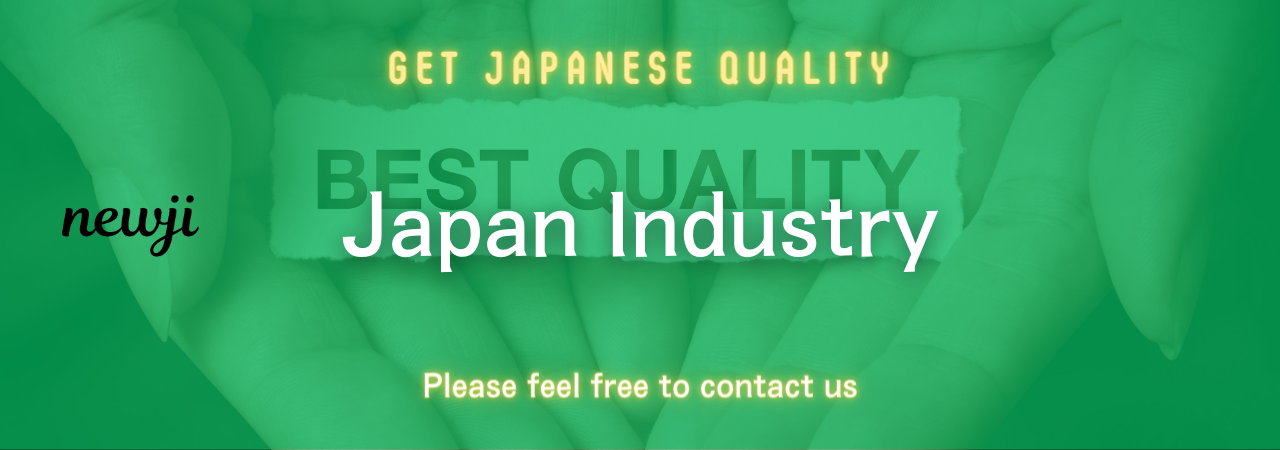
目次
What is Plastic Injection Molding?
Plastic injection molding is a manufacturing process used to create a wide array of plastic parts and products.
This process involves melting plastic pellets and injecting them into a mold cavity where the material cools and solidifies into the desired shape.
Injection molding is popular because it enables efficient mass production and allows for complex designs.
Key Components of the Injection Molding Process
Several key components make up the injection molding process.
Understanding these components is essential for creating high-quality parts and minimizing defects.
Injection Unit
The injection unit is where the plastic pellets are heated and melted.
A reciprocating screw or a plunger pushes the molten plastic towards the mold.
The process must be carefully controlled to achieve the correct temperature and consistency for the plastic material being used.
Mold
The mold is the negative of the part to be produced.
It consists of two halves: the core and the cavity.
These halves come together to create the mold cavity which shapes the melted plastic.
Materials for molds are typically metals such as steel or aluminum due to their durability and ability to withstand high-pressure conditions.
Clamping Unit
The clamping unit holds the mold halves together during the injection process.
It ensures that the mold remains securely closed while the plastic is being injected and prevents any leakage.
Once the plastic cools and solidifies, the clamp is released, and the part is ejected.
The Injection Molding Cycle
The injection molding cycle consists of several stages: clamping, injection, cooling, and ejection.
Each stage needs to be precisely timed to produce high-quality parts efficiently.
Clamping
In the clamping stage, the two halves of the mold are closed by the clamping unit.
Consistent and accurate clamping is vital as any misalignment can lead to defects.
Injection
During the injection stage, the molten plastic is injected into the mold cavity.
The injection speed and pressure must be carefully managed to fill the mold completely and create uniform products.
Cooling
The cooling stage is where the injected plastic solidifies as it cools down within the mold.
Proper cooling time ensures that the part retains its shape and functionality.
A rapid cooling time can lead to warping or stress in the molded part.
Ejection
The ejection stage involves removing the solidified part from the mold.
Ejector pins or other mechanical means push the part out of the mold.
Proper ejection techniques are necessary to prevent damage to the part.
Common Molding Defects and How to Prevent Them
Injection molding, while efficient, can sometimes result in defects that affect the quality and functionality of the product.
Identifying these defects and knowing how to prevent them is crucial.
Burn Marks
Burn marks appear as black or brown discolorations on the surface of the part.
They are usually caused by trapped air or overheating.
To prevent burn marks, reduce the injection speed and pressure, and ensure proper venting in the mold.
Short Shots
Short shots occur when the mold cavity is not completely filled, resulting in incomplete products.
Increasing the injection pressure and ensuring the plastic has the appropriate flow can prevent short shots.
Check for any blockages or restrictions in the mold as well.
Flash
Flash happens when excess material leaks out of the mold cavity, creating thin layers around the part.
This can be controlled by ensuring that the clamping unit provides sufficient force to keep the mold tightly closed and that the mold is not damaged.
Warping
Warping refers to the deformation of the part due to uneven cooling.
To minimize warping, ensure uniform cooling by optimizing cooling time, temperature, and coolant flow.
Tips for Improving Injection Molding Quality
Paying attention to details and implementing best practices can lead to improved injection molding quality.
Material Selection
Choosing the right material for your application is critical.
Consider the mechanical properties, thermal properties, and cost of different materials to ensure you select one that aligns with your product requirements.
Design Considerations
Design the part and mold with manufacturing in mind.
Implement draft angles to facilitate easy ejection and add ribs or gussets for structural integrity without increasing thickness.
Preventative Maintenance
Routine maintenance of the injection molding machine and molds can prevent unexpected downtimes and defects.
Regularly inspect and clean the mold, check for wear and tear, and ensure all components are functioning correctly.
Training and Skill Development
Ensure that operators and technicians are well-trained in the latest techniques and technologies related to injection molding.
Continual training can lead to better troubleshooting and optimization skills.
By understanding the basics of plastic injection molding technology and implementing effective strategies to prevent defects, manufacturers can produce high-quality parts efficiently.
This knowledge is essential for maintaining a competitive edge in the industry and meeting customer demands effectively.
資料ダウンロード
QCD管理受発注クラウド「newji」は、受発注部門で必要なQCD管理全てを備えた、現場特化型兼クラウド型の今世紀最高の受発注管理システムとなります。
ユーザー登録
受発注業務の効率化だけでなく、システムを導入することで、コスト削減や製品・資材のステータス可視化のほか、属人化していた受発注情報の共有化による内部不正防止や統制にも役立ちます。
NEWJI DX
製造業に特化したデジタルトランスフォーメーション(DX)の実現を目指す請負開発型のコンサルティングサービスです。AI、iPaaS、および先端の技術を駆使して、製造プロセスの効率化、業務効率化、チームワーク強化、コスト削減、品質向上を実現します。このサービスは、製造業の課題を深く理解し、それに対する最適なデジタルソリューションを提供することで、企業が持続的な成長とイノベーションを達成できるようサポートします。
製造業ニュース解説
製造業、主に購買・調達部門にお勤めの方々に向けた情報を配信しております。
新任の方やベテランの方、管理職を対象とした幅広いコンテンツをご用意しております。
お問い合わせ
コストダウンが利益に直結する術だと理解していても、なかなか前に進めることができない状況。そんな時は、newjiのコストダウン自動化機能で大きく利益貢献しよう!
(β版非公開)