- お役立ち記事
- Basics of plastic injection molding technology, causes of molding defects, and countermeasure points
月間76,176名の
製造業ご担当者様が閲覧しています*
*2025年3月31日現在のGoogle Analyticsのデータより
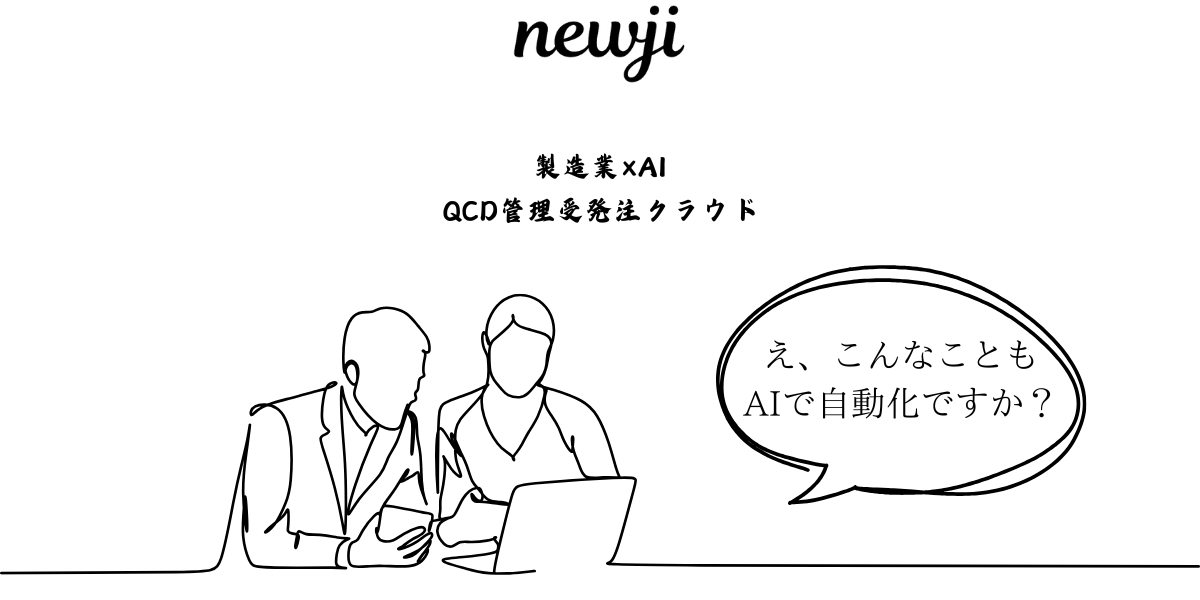
Basics of plastic injection molding technology, causes of molding defects, and countermeasure points
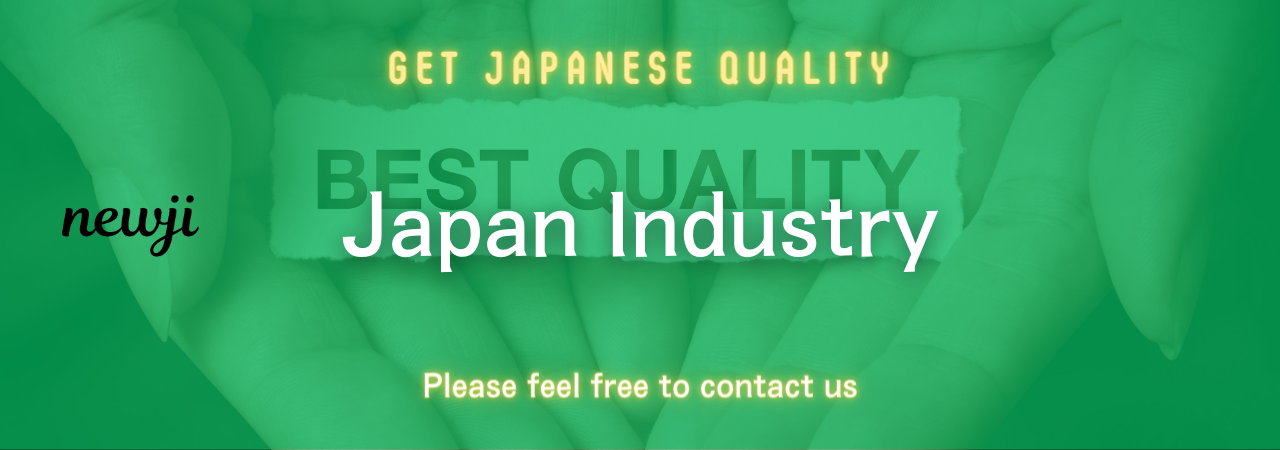
目次
Understanding Plastic Injection Molding Technology
Plastic injection molding is a widely used manufacturing process that allows for the mass production of parts and components in various shapes and sizes.
This technique involves injecting molten plastic material into a mold cavity, where it cools and solidifies into the desired shape.
Injection molding is highly efficient and cost-effective, making it a popular choice for producing a wide range of plastic products.
The process starts with the design and manufacturing of a mold, which can be quite complex.
Molds are usually made from steel or aluminum, and they consist of two halves that form the desired shape of the part.
Once the mold is ready, plastic pellets are heated until they melt and become pliable.
The molten plastic is then injected into the mold cavity under high pressure, filling the hollow space completely.
As the material cools, it takes the shape of the mold, resulting in a finished product that is precise and durable.
Key Steps in Plastic Injection Molding
1. **Designing the Mold**: The first step is to create a detailed design of the mold, which serves as the blueprint for the final product.
Engineers use computer-aided design (CAD) software to ensure accuracy and efficiency.
2. **Selecting Materials**: Different types of plastic materials have unique properties, such as heat resistance, flexibility, and strength.
Selecting the right polymer is crucial for the application’s intended use.
3. **Melting and Injection**: The plastic pellets are melted in an injection molding machine.
Once liquefied, the plastic is injected into the mold cavity at high pressure.
4. **Cooling and Solidifying**: The mold is allowed to cool so that the plastic can solidify.
Cooling time depends on the thickness and complexity of the part.
5. **Ejection and Finishing**: After cooling, the mold is opened, and the part is ejected.
Any excess plastic, known as “flash,” is trimmed away to achieve the final product.
Causes of Molding Defects in Plastic Injection Molding
Despite its advantages, plastic injection molding is not free from challenges.
Occasionally, molding defects can occur, impacting the quality and performance of the final product.
Understanding the causes of these defects is essential to prevent production issues and maintain product integrity.
Common Molding Defects
1. **Flash**: Flash is the excess plastic that escapes from the mold cavity, usually forming a thin layer around the part’s edges.
It can be caused by excessive injection pressure, poor mold design, or insufficient clamping force.
2. **Warping**: Warping refers to the distortion of the part as it cools, resulting in an uneven surface.
It often results from uneven cooling or an improper material choice.
3. **Sink Marks**: Sink marks appear as depressions on the surface of the part, typically due to inadequate cooling or low packing pressure.
They can affect the part’s aesthetic appearance and dimensional accuracy.
4. **Short Shots**: A short shot occurs when the mold is not completely filled, leaving empty spaces within the part.
This can happen due to insufficient injection pressure or an incorrectly sized mold gate.
5. **Burn Marks**: Burn marks are dark discolorations that form on the surface of the part.
They are often caused by trapped air in the mold or high melt temperatures.
Countermeasure Points for Molding Defects
To minimize the occurrence of defects and ensure the production of high-quality parts, manufacturers can implement several countermeasures.
These measures focus on optimizing the injection molding process and addressing the specific causes of defects.
Strategies to Prevent Flash
– Ensure proper clamping force to keep the mold halves tightly closed during injection.
– Review and adjust mold design to ensure precise alignment and fit.
– Reduce injection pressure and speed to prevent material from escaping the mold cavity.
Preventing Warping
– Use materials with a consistent shrinkage rate to minimize uneven thermal expansion.
– Ensure uniform cooling by designing appropriate cooling channels and using temperature control systems.
– Adjust the mold temperature and cooling time to promote uniform solidification.
Eliminating Sink Marks
– Increase packing pressure to fill any voids that can lead to sink marks.
– Design the mold with uniform wall thickness to promote even cooling and solidification.
– Adjust the cooling time to allow the part to fully solidify before ejection.
Addressing Short Shots
– Increase injection pressure and speed to ensure complete mold filling.
– Verify the runner and gate size to facilitate smooth flow of the molten plastic.
– Check for any obstructions in the mold cavity or injection path.
Preventing Burn Marks
– Reduce the melt temperature to avoid overheating the plastic material.
– Optimize venting in the mold to allow trapped air to escape effectively.
– Adjust the injection speed to minimize trapped air and reduce the risk of burning.
By understanding the fundamentals of plastic injection molding, along with the common defects and their countermeasures, manufacturers can optimize their production processes.
This knowledge ensures high-quality outputs, reduces waste, and enhances the overall efficiency of manufacturing operations.
With the right approach, plastic injection molding remains a powerful tool in producing consistent and precise products across various industries.
資料ダウンロード
QCD管理受発注クラウド「newji」は、受発注部門で必要なQCD管理全てを備えた、現場特化型兼クラウド型の今世紀最高の受発注管理システムとなります。
ユーザー登録
受発注業務の効率化だけでなく、システムを導入することで、コスト削減や製品・資材のステータス可視化のほか、属人化していた受発注情報の共有化による内部不正防止や統制にも役立ちます。
NEWJI DX
製造業に特化したデジタルトランスフォーメーション(DX)の実現を目指す請負開発型のコンサルティングサービスです。AI、iPaaS、および先端の技術を駆使して、製造プロセスの効率化、業務効率化、チームワーク強化、コスト削減、品質向上を実現します。このサービスは、製造業の課題を深く理解し、それに対する最適なデジタルソリューションを提供することで、企業が持続的な成長とイノベーションを達成できるようサポートします。
製造業ニュース解説
製造業、主に購買・調達部門にお勤めの方々に向けた情報を配信しております。
新任の方やベテランの方、管理職を対象とした幅広いコンテンツをご用意しております。
お問い合わせ
コストダウンが利益に直結する術だと理解していても、なかなか前に進めることができない状況。そんな時は、newjiのコストダウン自動化機能で大きく利益貢献しよう!
(β版非公開)