- お役立ち記事
- Basics of plating, efficient process control techniques, and troubleshooting
月間76,176名の
製造業ご担当者様が閲覧しています*
*2025年3月31日現在のGoogle Analyticsのデータより
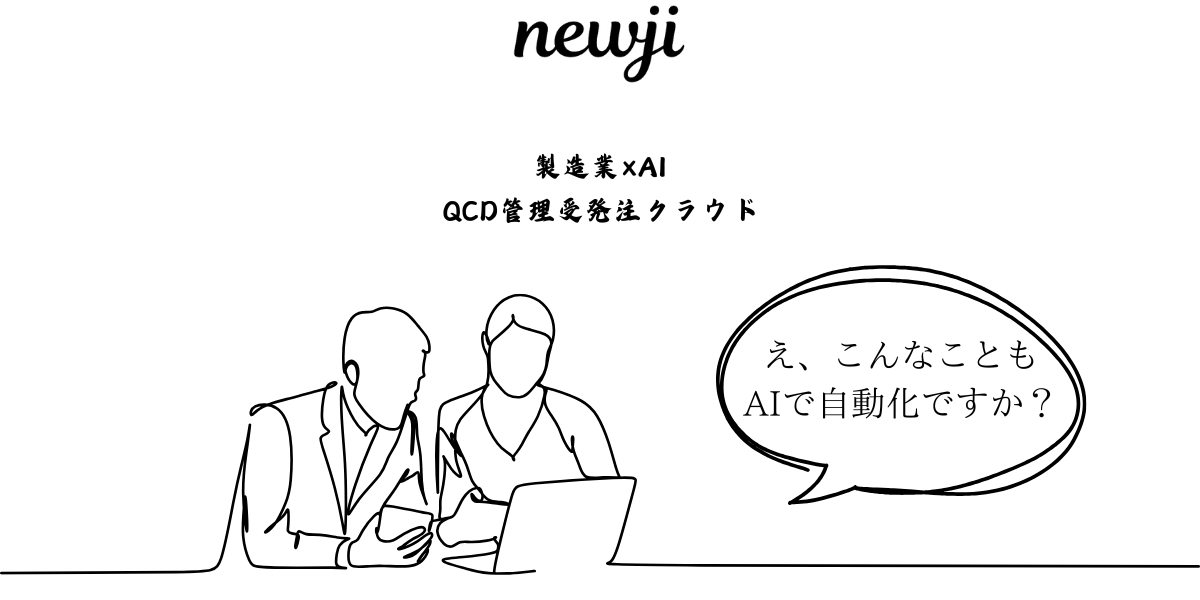
Basics of plating, efficient process control techniques, and troubleshooting
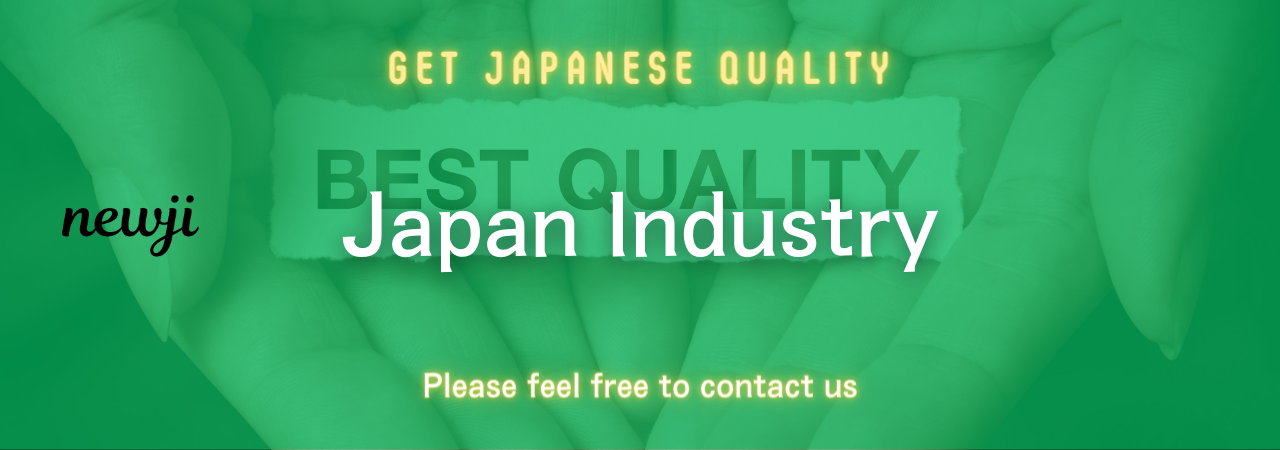
Plating is a technique used in various industries to coat a metal surface with a thin layer of another metal. This process not only enhances the appearance of the metal object but also provides resistance to corrosion, wear and tear, and enhances electrical conductivity. Understanding the basics of plating and mastering the efficient process control techniques are crucial for maintaining quality and productivity.
目次
What is Plating?
Plating involves the application of a metallic layer on a surface for purposes such as protection, decoration, or increased functionality. The most common types of plating include electroplating, electroless plating, and anodizing.
Electroplating
Electroplating uses an electrical current to reduce dissolved metal cations so that they form a coherent metal coating on an electrode. Common metals used include gold, silver, nickel, and chrome. This method is widely used in industries spanning from automotive to jewelry making due to its reliability and strength.
Electroless Plating
Unlike electroplating, electroless plating does not require an electric current. Instead, it relies on a chemical reaction that deposits metal onto a substrate. Nickel and copper are commonly used in this process. Electroless plating is often employed in industries where complex parts are involved, providing uniform coating thickness on complex geometries.
Anodizing
Anodizing is an electrochemical process that converts the metal surface into a decorative, durable, corrosion-resistant anodic oxide finish. It is primarily used for aluminum but is applicable to other metals like titanium and magnesium. Anodizing is popular in the aerospace and consumer electronics industries.
Efficient Process Control Techniques
Process control is critical to ensure consistent quality and efficiency in plating. Here are several key techniques that can improve process control:
Pre-cleaning
Before plating, substrates must be thoroughly cleaned to remove any surface impurities. If these impurities remain, they can inhibit adhesion and result in plating defects. Using methods like ultrasonic cleaning, alkaline cleaning, or acid dipping can help ensure surfaces are pristine.
Solution Maintenance
Regularly monitor and maintain the plating solution to ensure chemical concentrations remain within specifications. This involves routine sampling and testing to detect any deviations early on. Maintaining optimal temperature, pH, and chemical balance is essential for achieving quality results.
Adhering to Environmental Parameters
Environmental factors such as temperature, humidity, and ventilation can impact the plating process. These parameters must be controlled to avoid issues like uneven plating thickness or blotchy appearance. Using temperature controls, dehumidifiers, or proper ventilation can effectively stabilize environmental conditions.
Regular Equipment Calibration
Proper and regular calibration of plating equipment such as voltage regulators, current meters, and solution baths is crucial. This ensures that machinery operates within optimal parameters, preventing errors that could lead to defects or inefficiencies.
Troubleshooting Common Issues in Plating
Despite the best practices, issues can still arise in the plating process. Here are some common problems and their potential solutions:
Poor Adhesion
If the metallic coating doesn’t adhere properly to the substrate, it could be due to insufficient pre-cleaning. Ensuring that the surface is properly prepared and free from oils and contaminants is key. Consider evaluating the cleanliness process and possibly implementing additional cleaning stages.
Smoothness of Finish
A rough or uneven finish may result from improper chemical concentrations or environmental conditions. Checking and adjusting the bath composition and temperature can resolve this. Additionally, inspect the filtration system to ensure there are no particulates affecting the finish.
Discoloration
Discoloration often indicates an imbalance in the plating solution or foreign materials in the bath. Conduct a thorough analysis of the solution, checking for contaminants or incorrect pH levels. Proper solution management and filtration can address these issues.
Cracking or Peeling
Cracking or peeling of the plated layer is often a result of dehydration or internal stresses due to swift cooling or uneven deposition. Adjust the plating process by controlling the cooling rate and ensuring uniform deposition to alleviate these problems.
Understanding the basics of plating, employing efficient process control techniques, and being equipped for troubleshooting are vital components to achieving a high-quality finish. Adopting these practices contributes to better productivity, fewer defects, and ultimately, satisfied clients. As with any technical process, continuous learning and adaptation to new technologies and methods can enhance outcomes in plating work.
資料ダウンロード
QCD管理受発注クラウド「newji」は、受発注部門で必要なQCD管理全てを備えた、現場特化型兼クラウド型の今世紀最高の受発注管理システムとなります。
ユーザー登録
受発注業務の効率化だけでなく、システムを導入することで、コスト削減や製品・資材のステータス可視化のほか、属人化していた受発注情報の共有化による内部不正防止や統制にも役立ちます。
NEWJI DX
製造業に特化したデジタルトランスフォーメーション(DX)の実現を目指す請負開発型のコンサルティングサービスです。AI、iPaaS、および先端の技術を駆使して、製造プロセスの効率化、業務効率化、チームワーク強化、コスト削減、品質向上を実現します。このサービスは、製造業の課題を深く理解し、それに対する最適なデジタルソリューションを提供することで、企業が持続的な成長とイノベーションを達成できるようサポートします。
製造業ニュース解説
製造業、主に購買・調達部門にお勤めの方々に向けた情報を配信しております。
新任の方やベテランの方、管理職を対象とした幅広いコンテンツをご用意しております。
お問い合わせ
コストダウンが利益に直結する術だと理解していても、なかなか前に進めることができない状況。そんな時は、newjiのコストダウン自動化機能で大きく利益貢献しよう!
(β版非公開)