- お役立ち記事
- Basics of plating processing and quality control points for troubleshooting and prevention
Basics of plating processing and quality control points for troubleshooting and prevention
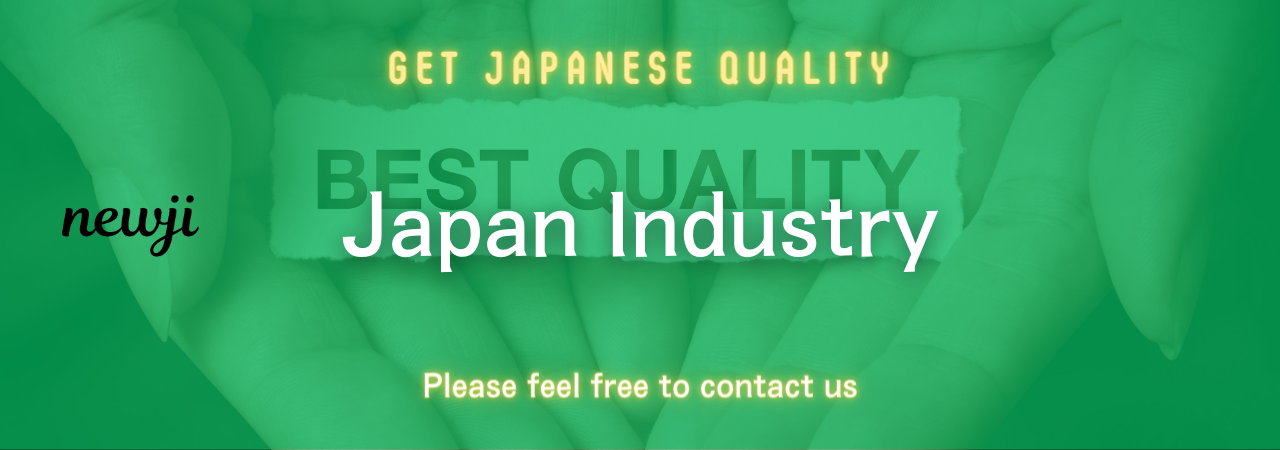
目次
Understanding Plating Processing
Plating is a crucial process in various industries, including electronics, automotive, and jewelry.
It involves coating a substrate—often metal or plastic—with a thin layer of another material, usually metal, to enhance its appearance, durability, corrosion resistance, or conductivity.
There are several methods of plating, each having its distinct applications and benefits.
Types of Plating Methods
1. Electroplating
Electroplating is one of the most common methods used in the plating industry.
In this process, an electric current is passed through a solution containing metal ions and the substrate.
The electric current facilitates the transfer of metal ions onto the substrate, forming a smooth, even coating.
2. Electroless Plating
Unlike electroplating, electroless plating does not require electricity.
It uses a chemical reaction to deposit a metal layer onto the substrate.
This method is often used for more complex shapes as it allows for an even coating over all surfaces.
3. Mechanical Plating
Mechanical plating involves peening a metal powder onto a substrate in a tumbling action, often enhanced by glass beads.
This method is ideal for coating materials susceptible to hydrogen embrittlement and provides a uniform, adherent finish.
4. Immersion Plating
This method uses a chemical reaction to deposit a metal coating from a solution until the reaction naturally halts.
It is often employed for small-scale applications and provides a basic level of corrosion resistance.
Importance of Quality Control in Plating
Quality control is essential in plating processes to ensure the final product meets industry standards and customer requirements.
Effective quality control helps in identifying defects early, reducing waste, and improving overall product quality.
Key Quality Control Steps
1. Substrate Preparation
Preparation of the substrate is vital for a successful plating process.
This step includes cleaning, degreasing, and sometimes etching the surface to remove contaminants and improve adhesion.
2. Bath Composition
The plating bath’s composition and temperature must be regularly monitored and maintained.
Any deviation can lead to defects such as roughness or uneven thickness in the coating.
3. Thickness Testing
Verifying the thickness of the coating is crucial.
There are several methods for measuring the thickness of a plated layer, such as X-ray fluorescence (XRF) and coulometric analysis, ensuring the coating is within specified limits.
4. Adhesion and Hardness Testing
Testing for adhesion helps determine whether the plating has correctly bonded to the substrate.
Hardness tests can also indicate the quality of the coating, ensuring it meets specified mechanical properties.
Troubleshooting Common Plating Issues
Even with stringent quality controls, plating processes can face challenges.
Below are some common issues and solutions for troubleshooting:
1. Rough or Uneven Coatings
Roughness usually indicates contamination in the bath or excessive current.
To resolve this, clean or replace the bath solution and adjust the current to appropriate levels.
2. Poor Adhesion
Poor adhesion can result from inadequate surface preparation or incorrect plating parameters.
Ensuring thorough cleaning and proper parameter settings can mitigate adhesion issues.
3. Pitting or Blistering
Pitting and blistering might be due to gas entrapment or impurities.
Ensuring the removal of gaseous byproducts and maintaining clean bath solutions can prevent these issues.
4. Discoloration
Discoloration often arises from impurities or variations in bath temperature.
Careful monitoring and regular maintenance of bath conditions are crucial to prevent this defect.
Preventive Measures for Efficient Plating
To maintain a high standard in plating operations, preventive measures must be implemented.
1. Regular Maintenance of Equipment
Scheduled maintenance of plating equipment is essential to identify and rectify issues before they escalate.
2. Operator Training
Operators should be well-trained in handling plating processes and dealing with common problems.
Regular training sessions can enhance their skills and awareness of quality standards.
3. Use of Quality Raw Materials
Using high-quality materials for substrates and plating baths can significantly reduce the risk of defects.
Quality materials ensure better finish and longevity of the plated products.
4. Detailed Record Keeping
Maintaining comprehensive records of all processes can help in tracing back issues to their root cause, enabling more efficient troubleshooting and process improvements.
Understanding the basics of plating processing and implementing strict quality control measures are vital for producing high-quality plated products.
By addressing common issues proactively and taking preventive measures, industries can enhance their plating processes’ efficiency and reliability, ensuring better outcomes and customer satisfaction.
資料ダウンロード
QCD調達購買管理クラウド「newji」は、調達購買部門で必要なQCD管理全てを備えた、現場特化型兼クラウド型の今世紀最高の購買管理システムとなります。
ユーザー登録
調達購買業務の効率化だけでなく、システムを導入することで、コスト削減や製品・資材のステータス可視化のほか、属人化していた購買情報の共有化による内部不正防止や統制にも役立ちます。
NEWJI DX
製造業に特化したデジタルトランスフォーメーション(DX)の実現を目指す請負開発型のコンサルティングサービスです。AI、iPaaS、および先端の技術を駆使して、製造プロセスの効率化、業務効率化、チームワーク強化、コスト削減、品質向上を実現します。このサービスは、製造業の課題を深く理解し、それに対する最適なデジタルソリューションを提供することで、企業が持続的な成長とイノベーションを達成できるようサポートします。
オンライン講座
製造業、主に購買・調達部門にお勤めの方々に向けた情報を配信しております。
新任の方やベテランの方、管理職を対象とした幅広いコンテンツをご用意しております。
お問い合わせ
コストダウンが利益に直結する術だと理解していても、なかなか前に進めることができない状況。そんな時は、newjiのコストダウン自動化機能で大きく利益貢献しよう!
(Β版非公開)