- お役立ち記事
- Basics of PLC control and application to effective use of factory data and productivity improvement using IoT
Basics of PLC control and application to effective use of factory data and productivity improvement using IoT
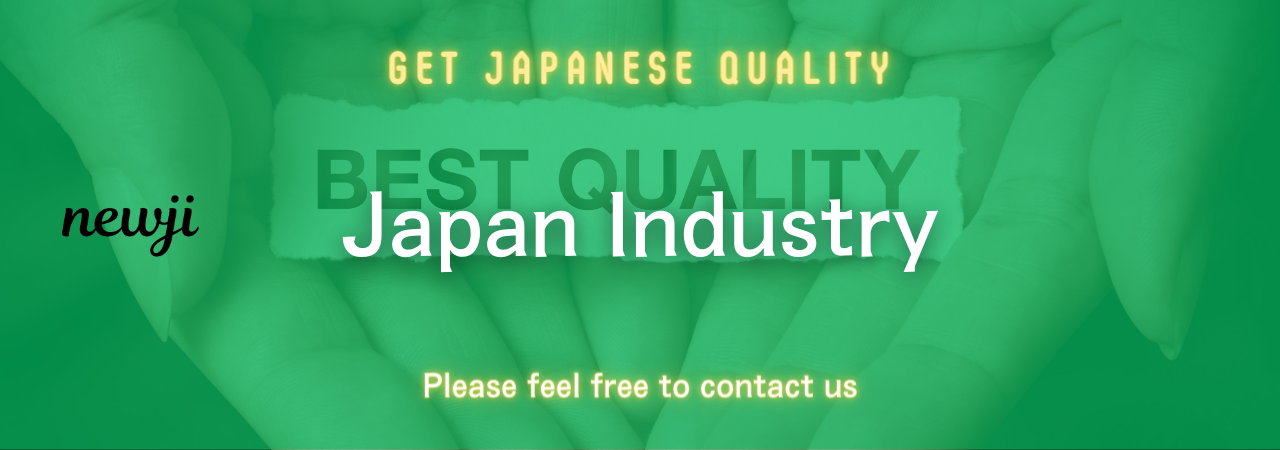
目次
Understanding PLC Control
A Programmable Logic Controller, commonly known as a PLC, is a crucial component in industrial automation and process control.
Essentially, a PLC is a specialized computer designed to manage manufacturing processes, like assembly lines and robotic devices, where they continuously monitor the state of input devices and make decisions based on a custom program to control the state of output devices.
Understanding how PLCs work can enhance efficiency and productivity across various industries.
PLCs operate on the principle of logic control and sequencing.
They have a variety of input and output ports where sensors and actuators are connected.
The PLC reads inputs from sensors, such as temperature, pressure, or proximity sensors, and processes the data using a pre-written program to turn on or off specific outputs such as motors, valves, or alarms.
This sequential operation is vital for automation because it ensures the seamless interaction between machines and processes.
Components of a PLC
To gain a comprehensive understanding of PLC control, it is essential to know its fundamental components.
Central Processing Unit (CPU)
The CPU is the brain of the PLC where all computations and control instructions are processed.
It processes the input data according to the sequence of instructions contained in the programmed logic.
Power Supply
PLCs require a stable and reliable power source to operate.
The power supply unit converts the AC voltage to the DC voltage needed by the PLC components.
Input and Output Modules
Input modules receive data from sensors or user inputs, while output modules send control signals to actuators.
These modules ensure data flows seamlessly between the PLC and other components of the industrial system.
Memory Unit
The memory unit is where the PLC’s operating system and control programs are stored.
Memory types include RAM, EPROM, and EEPROM, each serving different purposes from temporary data storage to retaining programs during power loss.
Importance of PLCs in Industrial Automation
PLCs play a vital role in modern manufacturing processes, as they are designed to withstand harsh industrial environments and provide high reliability.
Increased Productivity
By automating routine tasks, PLCs reduce human intervention, which speeds up the entire production process, thereby increasing productivity.
Precision and Accuracy
PLCs allow for precise control and measurement of manufacturing processes.
This ensures significant quality control and minimizes error margins, leading to consistent product output.
Flexibility and Adaptability
With PLCs, changes in production or the introduction of new operations can be easily accommodated by reprogramming the logic without needing to install new hardware.
Application to Effective Use of Factory Data
Incorporating PLCs with IoT technology paves the way for the effective use of factory data, transforming traditional industries into smart factories.
Data Collection and Analysis
PLC systems connected with IoT devices gather real-time data from various points in the production line.
This data is analyzed to identify inefficiencies, predict maintenance needs, and optimize operations.
Remote Monitoring
IoT integration enables remote monitoring and control of PLCs.
Operators can access and manage plant data from anywhere, saving time and resources by minimizing the need for physical presence on the factory floor.
Predictive Maintenance
With constant data flow to a cloud-based system, PLCs can alert users for maintenance before equipment failure occurs.
This predictive maintenance helps in reducing downtime and extending machinery life.
Improving Productivity Using IoT
The combination of PLC with IoT technologies significantly enhances productivity across various industries.
Enhanced Communication
IoT enables seamless communication between different machines and systems through the Internet.
This ensures operations are synchronized and provides a more integrated workflow process.
Scalability
IoT allows for easy scalability of operations.
As demand increases, additional devices and sensors can be seamlessly integrated into the existing network without significant disruption.
Real-time Data Access
Real-time access to data can lead to proactive decision-making.
Companies can react to changes promptly, ensuring operations remain efficient and productive even during fluctuations in demand.
In summary, understanding the basics of PLC control and its integration with IoT can revolutionize industrial automation, leading to enhanced operational efficiency and productivity.
By leveraging these technologies, industries can effectively utilize factory data, optimize resources, predict equipment failures, and achieve a significant competitive advantage in the marketplace.
資料ダウンロード
QCD調達購買管理クラウド「newji」は、調達購買部門で必要なQCD管理全てを備えた、現場特化型兼クラウド型の今世紀最高の購買管理システムとなります。
ユーザー登録
調達購買業務の効率化だけでなく、システムを導入することで、コスト削減や製品・資材のステータス可視化のほか、属人化していた購買情報の共有化による内部不正防止や統制にも役立ちます。
NEWJI DX
製造業に特化したデジタルトランスフォーメーション(DX)の実現を目指す請負開発型のコンサルティングサービスです。AI、iPaaS、および先端の技術を駆使して、製造プロセスの効率化、業務効率化、チームワーク強化、コスト削減、品質向上を実現します。このサービスは、製造業の課題を深く理解し、それに対する最適なデジタルソリューションを提供することで、企業が持続的な成長とイノベーションを達成できるようサポートします。
オンライン講座
製造業、主に購買・調達部門にお勤めの方々に向けた情報を配信しております。
新任の方やベテランの方、管理職を対象とした幅広いコンテンツをご用意しております。
お問い合わせ
コストダウンが利益に直結する術だと理解していても、なかなか前に進めることができない状況。そんな時は、newjiのコストダウン自動化機能で大きく利益貢献しよう!
(Β版非公開)