- お役立ち記事
- Basics of PLC control and application to IoT/AI
月間77,185名の
製造業ご担当者様が閲覧しています*
*2025年2月28日現在のGoogle Analyticsのデータより
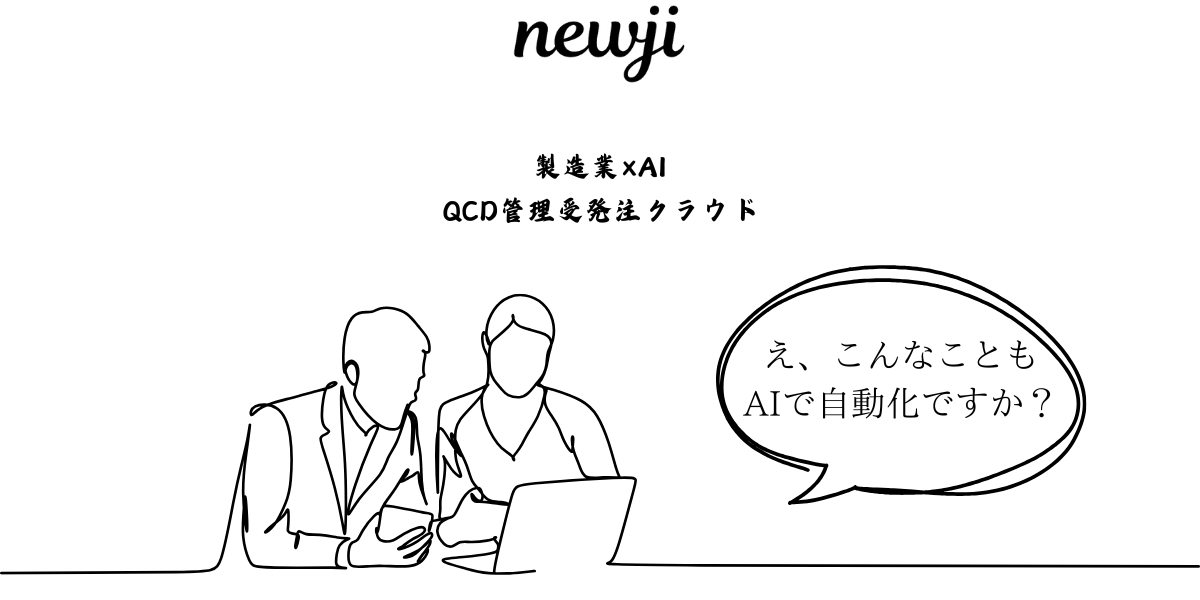
Basics of PLC control and application to IoT/AI
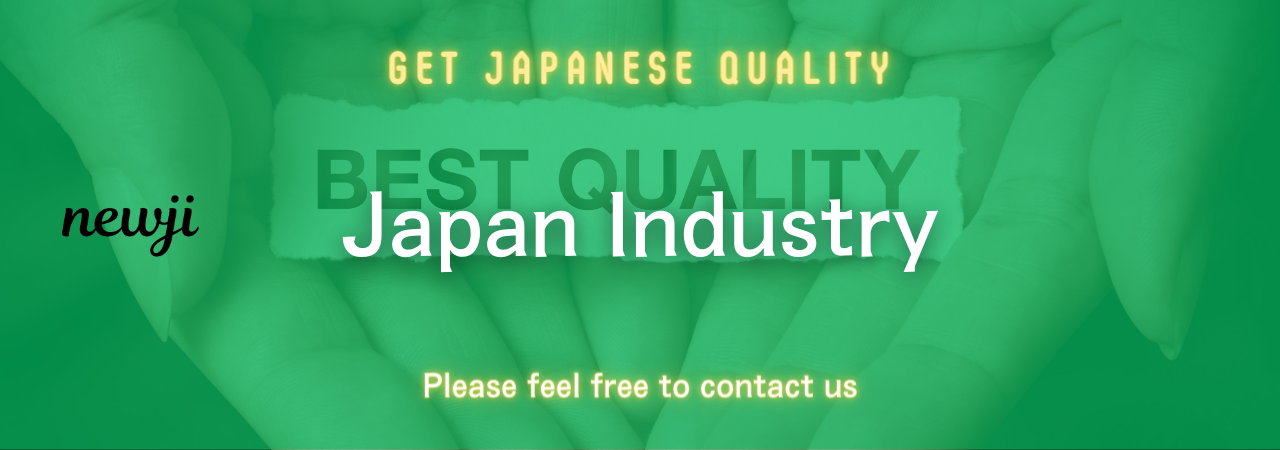
目次
Understanding PLC Control
Programmable Logic Controllers, commonly known as PLCs, are vital components in the automation industry.
They are used to control machinery and processes in manufacturing environments.
PLC control involves the use of specialized computers designed for industrial applications, where they monitor inputs, make decisions based on their programmed code, and control outputs to automate machines and processes.
At its core, a PLC is a digital computer designed to handle real-time tasks.
They are built to withstand harsh industrial environments such as extreme temperatures, dust, and vibration.
Unlike ordinary computers, PLCs have rugged hardware components and must provide reliable performance that aligns with industrial needs.
The primary task of a PLC is to receive inputs from various sensors, process these inputs logically, and send outputs to control devices like motors and actuators.
This makes PLCs crucial for the automation of factory equipment, ensuring efficient and high-precision operations.
Applications of PLCs
PLCs have a plethora of applications in different industries ranging from food processing and automotive manufacturing to pharmaceuticals.
They are extensively used in assembly lines, conveyor systems, and complex machine tools.
The importance of PLCs in these environments cannot be overstated due to their ability to improve efficiency, productivity, and safety.
In the automotive industry, for example, PLCs manage the assembly process by controlling robotic arms and conveyors.
They ensure that each part is put together quickly and accurately, reducing the margin for error.
In the food industry, PLC systems regulate the baking, freezing, and packaging processes, maintaining consistency and quality of the products.
Additionally, PLCs find use in utility services.
They are deployed in water treatment plants to manage pumps and filtration systems, ensuring the purification process runs smoothly.
Further applications can be found in telecommunications, mining, and even amusement parks where they manage ride controls.
Basics of IoT Integration with PLCs
The Internet of Things (IoT) refers to a network of interconnected devices that communicate and transfer data using embedded sensors.
By integrating IoT technology with PLCs, industries unlock a new level of efficiency and innovation.
With IoT integration, PLCs can now go beyond controlling physical machinery and become a part of a smart network.
This integration allows for remote control and monitoring of PLCs via the internet, providing real-time data to enhance decision-making and predictive maintenance capabilities.
Through IoT, PLCs are interconnected with sensors, cameras, and other smart devices, allowing them to share data automatically.
This synergy enhances the ability to predict issues before they occur, reducing downtime and ensuring uninterrupted production cycles.
Communication Protocols in IoT-PLC Systems
For IoT and PLC systems to function cohesively, compatible communication protocols are crucial.
Some of the commonly used protocols include MQTT, CoAP, and OPC UA.
These protocols ensure that vast amounts of data can be transmitted securely and reliably.
MQTT (Message Queuing Telemetry Transport), for example, is a lightweight messaging protocol ideal for IoT devices that require low bandwidth.
It is designed for efficient volume consumption and is perfect for PLC systems where real-time updates are crucial.
Similarly, OPC UA (Open Platform Communications Unified Architecture) plays a pivotal role in ensuring seamless integration between PLCs and other systems.
It provides a platform-independent service, supporting complex communication needs within industrial automation.
The Role of AI in Enhancing PLC Systems
Artificial Intelligence (AI) brings revolutionary advancements to PLC systems by introducing learning and decision-making capabilities.
AI algorithms can analyze historical and real-time data captured by PLCs to predict equipment failures, optimize processes, and reduce energy consumption.
By harnessing AI, PLC systems become smarter and more adaptive.
They can adjust operational parameters dynamically based on real-time inputs, minimizing the dependency on human intervention.
For instance, AI-integrated PLCs can automatically adjust the speed of production lines in response to varying demand, ensuring efficiency without compromising product quality.
Furthermore, AI techniques like machine learning algorithms empower PLC systems to self-correct and continually improve their performance.
They can identify patterns and trends that are not easily noticeable, paving the way for more accurate predictions and proactive maintenance actions.
Implementing AI in PLC Systems
The integration of AI into PLC systems involves several steps beginning with data collection.
Real-time data must be captured from connected sensors and devices, paving the way for AI models to provide actionable insights.
Next, AI algorithms need training to recognize patterns and delineate actionable recommendations.
This requires a comprehensive dataset for the AI to learn from, ensuring its predictions are accurate and reliable.
Collaboration between software engineers, data scientists, and automation specialists is crucial to successfully embedding AI into PLC systems.
This joint effort ensures contextual understanding, seamless integration, and robust performance in industrial settings.
Conclusion
The advent of IoT and AI has transformed the traditional role of PLCs, turning them into powerful tools that drive efficiency and innovation across industries.
Integrating these advanced technologies enables real-time monitoring, predictive maintenance, and smart decision-making, resulting in unparalleled operational benefits.
The synergy between PLCs, IoT, and AI continues to reshape industrial automation, promising a future where processes are not only automated but intelligent.
Staying abreast of these technologies opens up a realm of possibilities, equipping industries with a competitive edge in an increasingly digitalized world.
資料ダウンロード
QCD管理受発注クラウド「newji」は、受発注部門で必要なQCD管理全てを備えた、現場特化型兼クラウド型の今世紀最高の受発注管理システムとなります。
ユーザー登録
受発注業務の効率化だけでなく、システムを導入することで、コスト削減や製品・資材のステータス可視化のほか、属人化していた受発注情報の共有化による内部不正防止や統制にも役立ちます。
NEWJI DX
製造業に特化したデジタルトランスフォーメーション(DX)の実現を目指す請負開発型のコンサルティングサービスです。AI、iPaaS、および先端の技術を駆使して、製造プロセスの効率化、業務効率化、チームワーク強化、コスト削減、品質向上を実現します。このサービスは、製造業の課題を深く理解し、それに対する最適なデジタルソリューションを提供することで、企業が持続的な成長とイノベーションを達成できるようサポートします。
製造業ニュース解説
製造業、主に購買・調達部門にお勤めの方々に向けた情報を配信しております。
新任の方やベテランの方、管理職を対象とした幅広いコンテンツをご用意しております。
お問い合わせ
コストダウンが利益に直結する術だと理解していても、なかなか前に進めることができない状況。そんな時は、newjiのコストダウン自動化機能で大きく利益貢献しよう!
(β版非公開)