- お役立ち記事
- Basics of polishing processing and effective use of polishing simulation
月間77,185名の
製造業ご担当者様が閲覧しています*
*2025年2月28日現在のGoogle Analyticsのデータより
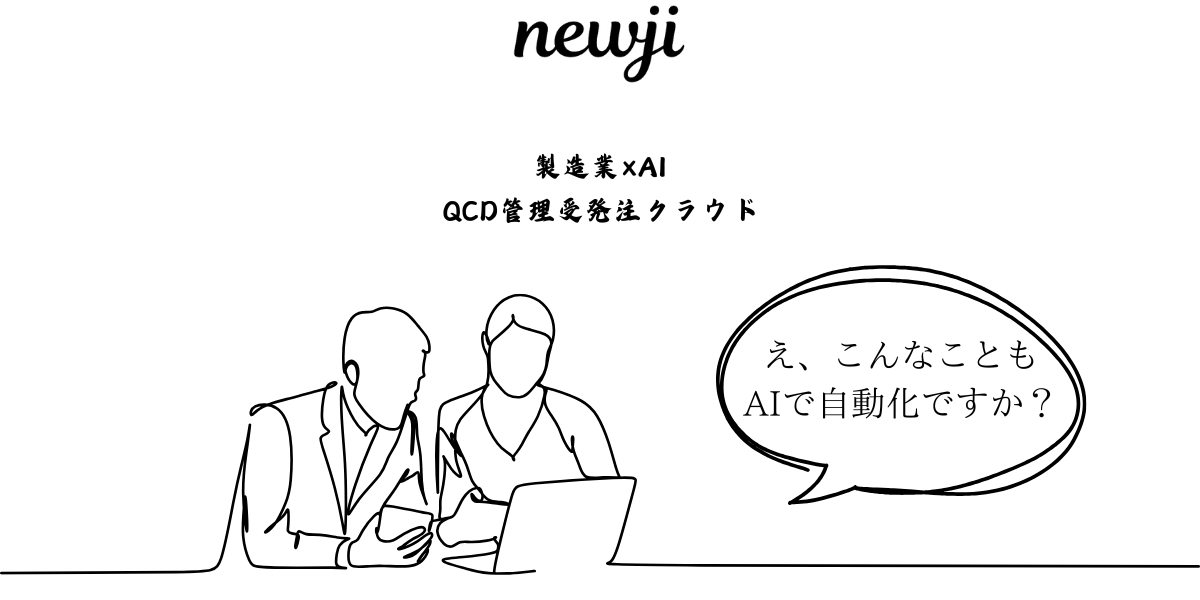
Basics of polishing processing and effective use of polishing simulation
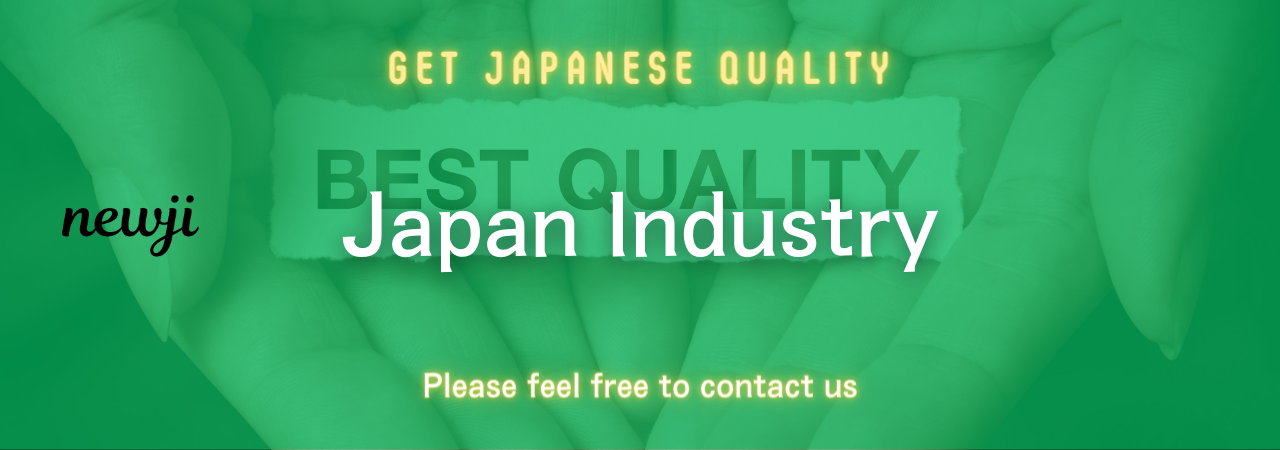
目次
Understanding Polishing Processing
Polishing processing is a fundamental technique used in various industries to enhance the surface quality of materials.
This process involves removing material from an item’s surface to make it smoother, shinier, and more refined.
The primary goal is to improve both aesthetic appeal and functionality by reducing roughness and eliminating imperfections.
In polishing processing, different techniques and tools are employed based on the material and desired outcome.
These can include mechanical polishing, chemical polishing, and electrochemical polishing.
Each method has its own advantages and specific applications, making it essential to choose the right one for the task at hand.
Common Polishing Techniques
One of the most common methods is mechanical polishing, which involves using abrasives to wear down the surface.
Abrasives come in various forms, such as sandpaper, polishing pads, and specialized polishing compounds.
Mechanical polishing is often utilized for metals, plastics, and ceramics, allowing precise control over the finish quality.
Chemical polishing uses chemical reactions to dissolve surface materials, offering a more even finish over complex shapes.
This method is beneficial for polishing materials that are difficult to handle with mechanical means.
Industries such as electronics and optics frequently employ chemical polishing for its precision and efficiency.
Electrochemical polishing is another vital technique, especially for metals.
This process involves creating an electrochemical reaction to smoothen and enhance surfaces by removing microscopic layers.
Electrochemical polishing is often used in medical device manufacturing and other industries requiring highly polished, contamination-free surfaces.
The Benefits of Proper Polishing
Polishing processing is paramount in ensuring products meet certain standards and aesthetic requirements.
A polished surface can significantly increase a product’s value by improving its appearance and enhancing its functionality.
Reduced surface roughness can decrease friction and wear, promoting longer lifespan and efficiency for the product.
Moreover, polished surfaces are easier to clean and maintain.
They prevent the accumulation of dirt and grime, which contributes to maintaining hygiene and enhancing product durability.
In industries where cleanliness is crucial, such as food processing and pharmaceuticals, polished surfaces are indispensable.
Polishing processing is also essential for optical and glass applications.
By creating a perfectly smooth surface, polishing ensures that light is refracted or reflected precisely as intended.
This is critical for devices like lenses, mirrors, and other optical components where clarity and precision are paramount.
Introduction to Polishing Simulation
As technology progresses, the need for more efficient and cost-effective polishing methods has led to the development of polishing simulation.
Polishing simulation is a computer-aided engineering tool that predicts the outcomes of a polishing process.
This allows engineers and technicians to simulate different polishing scenarios without physical trials, saving time and resources.
How Polishing Simulation Works
Polishing simulation involves creating a virtual model of the item to be polished.
Advanced algorithms and software analyze the material properties, the polishing technique, and the desired finish.
Engineers can then adjust variables to optimize the process before actual implementation.
This technology offers insights into how various factors affect the final result, such as tool path, pressure, speed, and abrasive type.
By simulating different conditions, operators can identify the most efficient and effective methods to achieve the desired level of polishing without wasting materials or labor.
The Advantages of Using Polishing Simulation
Utilizing polishing simulation offers numerous advantages to industries relying on precision surface finishes.
One of the most significant benefits is the reduction in time and costs associated with trial and error in physical polishing processes.
By simulating, users can foresee potential issues and adjust parameters accordingly before machining begins.
Polishing simulation also enhances the quality and consistency of the finish.
By leveraging accurate data and models, companies can produce higher-quality products with fewer defects.
This consistency is critical in sectors like aerospace and automotive, where precision manufacturing is necessary for both safety and performance.
Additionally, polishing simulation improves flexibility in product development.
Designers can experiment with new materials and designs, benefiting from faster innovation cycles without incurring the costs of physical testing.
This capability fosters creativity while ensuring that new products meet stringent quality standards.
Effective Practices in Polishing Simulation
To benefit fully from polishing simulation, companies must integrate several best practices into their operations.
Firstly, investing in advanced simulation software and ensuring the team is adequately trained is imperative.
Software solutions that offer realistic modeling and analysis enable more accurate predictions and better outcomes.
Additionally, collecting and analyzing data from actual polishing processes is essential.
This real-world information can be used to validate simulation results, creating a feedback loop that enhances both confidence in the simulations and the quality of the finished products.
Collaboration between design, engineering, and production teams is crucial.
By sharing insights and data, these teams can align their objectives and optimize polishing processes effectively.
Communication ensures that the simulation reflects real-world conditions accurately.
In conclusion, understanding the basics of polishing processing and the effective use of polishing simulation can significantly elevate the manufacturing process.
By embracing these techniques, industries can enhance product quality, reduce costs, and innovate more efficiently, maintaining a competitive edge in the rapidly evolving marketplace.
資料ダウンロード
QCD管理受発注クラウド「newji」は、受発注部門で必要なQCD管理全てを備えた、現場特化型兼クラウド型の今世紀最高の受発注管理システムとなります。
ユーザー登録
受発注業務の効率化だけでなく、システムを導入することで、コスト削減や製品・資材のステータス可視化のほか、属人化していた受発注情報の共有化による内部不正防止や統制にも役立ちます。
NEWJI DX
製造業に特化したデジタルトランスフォーメーション(DX)の実現を目指す請負開発型のコンサルティングサービスです。AI、iPaaS、および先端の技術を駆使して、製造プロセスの効率化、業務効率化、チームワーク強化、コスト削減、品質向上を実現します。このサービスは、製造業の課題を深く理解し、それに対する最適なデジタルソリューションを提供することで、企業が持続的な成長とイノベーションを達成できるようサポートします。
製造業ニュース解説
製造業、主に購買・調達部門にお勤めの方々に向けた情報を配信しております。
新任の方やベテランの方、管理職を対象とした幅広いコンテンツをご用意しております。
お問い合わせ
コストダウンが利益に直結する術だと理解していても、なかなか前に進めることができない状況。そんな時は、newjiのコストダウン自動化機能で大きく利益貢献しよう!
(β版非公開)