- お役立ち記事
- Basics of position control, speed control, and force control in robots and their applications and points for robot manipulators
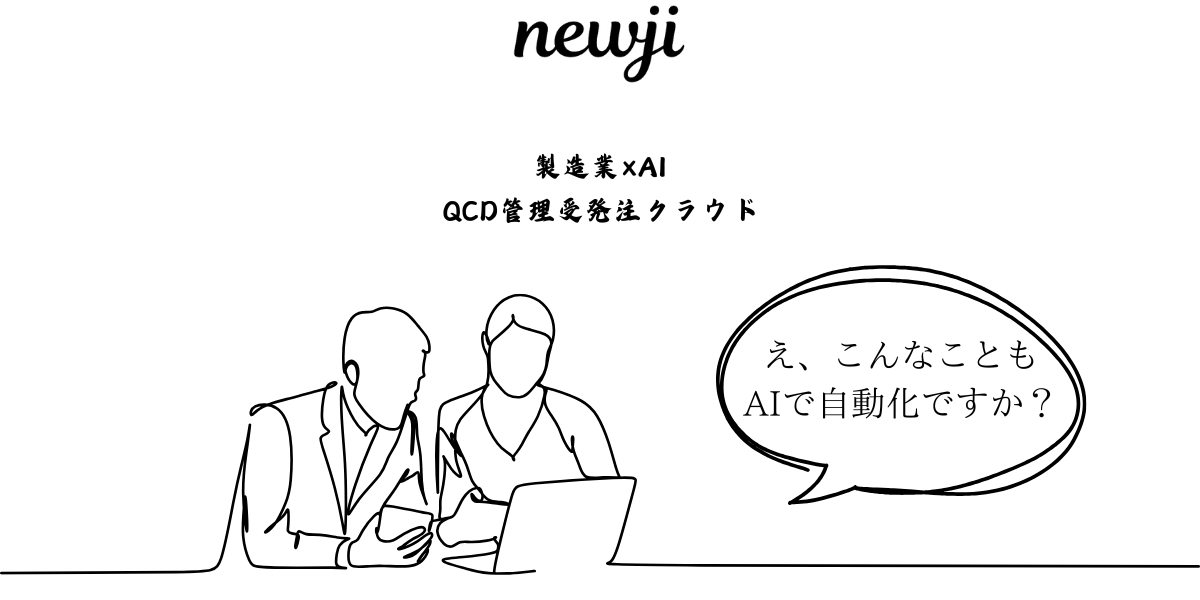
Basics of position control, speed control, and force control in robots and their applications and points for robot manipulators
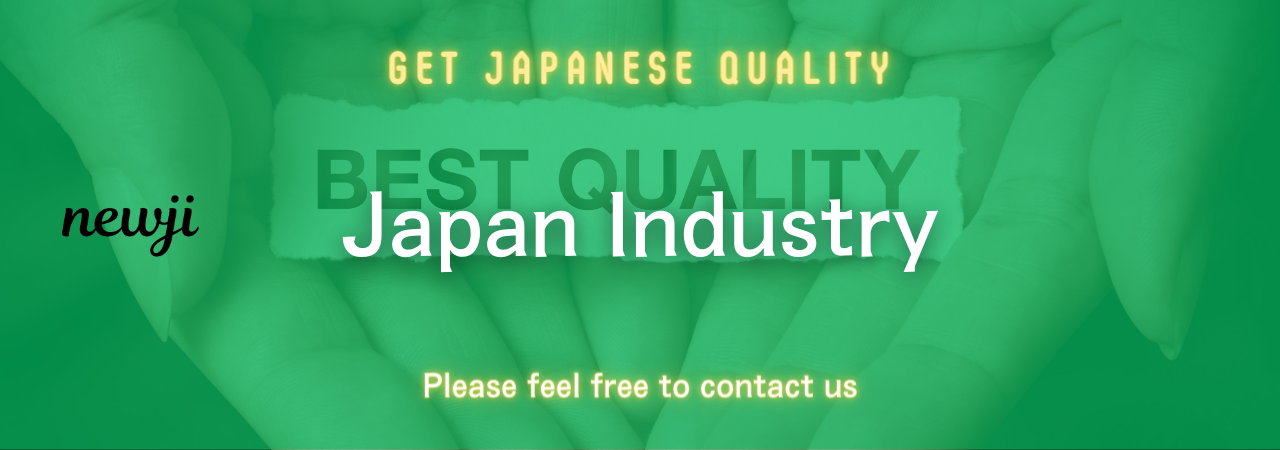
目次
Introduction to Robot Control Systems
Robots have become a crucial part of industries and our daily lives, performing tasks with precision and reliability.
To achieve this, they require sophisticated control systems.
In this article, we explore the basics of position control, speed control, and force control in robots.
We will also delve into their applications and considerations for robot manipulators, making these concepts clear and understandable for anyone interested in robotics.
Understanding Position Control
Position control is the fundamental aspect of robotic movement.
It is responsible for determining the precise location of a robot’s parts or end effectors.
When performing tasks, robots need to move to specific positions with high accuracy.
This is where position control plays a vital role.
Position control systems use sensors and feedback loops to monitor the robot’s current position and compare it with the desired position.
The system calculates any deviation and sends corrective signals to the motors to ensure that the robot reaches the intended location.
For example, in a robotic arm, position control ensures that the arm reaches out and picks up an object at a specific point in space.
Applications of Position Control
Position control is essential in various robotic applications.
One common example is in manufacturing, where robots assemble products or perform welding tasks.
These robots need precise positioning to ensure that components fit together correctly or that the weld is placed precisely.
In the medical field, surgical robots rely on position control to navigate delicate procedures with utmost precision, minimizing human error.
Position control also plays a critical role in robotic-assisted rehabilitation, helping patients perform exercises at accurate positions.
Diving into Speed Control
Speed control, also known as velocity control, focuses on regulating the speed at which a robot moves.
In many applications, maintaining a consistent speed is crucial for efficiency and safety.
Robots use speed control to adjust their movement rate according to the task’s requirements.
Speed control systems employ similar techniques as position control, utilizing sensors and feedback mechanisms.
These systems monitor the current speed of a robot and adjust it to match the desired velocity.
By doing so, robots can move smoothly and avoid abrupt changes in speed that could lead to wear and tear or accidents.
Applications of Speed Control
Speed control is widely used in conveyor systems within factories, where products need to be transported at a steady pace to maintain production efficiency.
In autonomous vehicles and drones, speed control ensures safe navigation in environments with varying traffic conditions.
Speed control is crucial in painting and coating applications, where the robot must move at a consistent speed to apply materials evenly.
It is also important in entertainment robots, where synchronized movement and timing are required for performances.
The Role of Force Control
Force control involves managing the force exerted by a robot when interacting with objects or environments.
Unlike position and speed control, which focus on movement, force control emphasizes how much force a robot applies during its tasks.
Force control is essential when robots need to perform delicate tasks, such as handling fragile items or applying specific pressure levels.
The system monitors the interaction force and adjusts it to avoid damage or achieve the desired result.
Applications of Force Control
Force control is crucial in collaborative robots, or cobots, that work alongside humans.
These robots need to ensure they apply appropriate force to avoid causing injury during interaction.
In material handling, force control ensures robots apply the right pressure when gripping various objects, preventing damage to the items.
Force control is vital in tasks like polishing and grinding, where the robot must exert a consistent force for a smooth finish.
In prosthetics and rehabilitation robotics, force control is used to mimic human touch and ensure comfort and safety.
Considerations for Robot Manipulators
When designing or working with robot manipulators, understanding control systems is essential.
Each control type—position, speed, and force—has unique considerations and challenges.
Position Control Considerations
Accuracy and precision are paramount for position control systems, requiring high-quality sensors and fine-tuned feedback loops.
The choice of actuators, like servomotors or stepper motors, impacts the system’s ability to achieve precise positioning.
Environmental factors such as temperature, load variations, and mechanical wear can affect position accuracy and should be monitored.
Speed Control Considerations
For speed control, maintaining a consistent velocity is crucial, and deviations must be promptly addressed.
In dynamic environments, real-time adjustments in speed might be necessary to avoid obstacles or adapt to changing conditions.
The energy consumption of a speed-controlled system can impact operational costs, requiring efficient energy management.
Force Control Considerations
Calibration of force sensors is critical to ensure accurate force measurements and control.
Understanding the material properties and interaction dynamics of objects manipulated by the robot is important to set appropriate force levels.
Safety measures, such as emergency stop mechanisms, should be integrated to prevent excessive force application, especially in human-robot collaborative settings.
Conclusion
Robotics control systems—position, speed, and force control—form the backbone of robot functionality across various applications.
Each control type has distinct roles, applications, and considerations that contribute to the efficiency, safety, and precision of robotic systems.
As the field of robotics continues to advance, understanding these control basics will remain fundamental in designing, operating, and innovating robot manipulators for diverse tasks.
With the increasing integration of robots into everyday life, mastering these control systems will be key to unlocking their full potential.
資料ダウンロード
QCD調達購買管理クラウド「newji」は、調達購買部門で必要なQCD管理全てを備えた、現場特化型兼クラウド型の今世紀最高の購買管理システムとなります。
ユーザー登録
調達購買業務の効率化だけでなく、システムを導入することで、コスト削減や製品・資材のステータス可視化のほか、属人化していた購買情報の共有化による内部不正防止や統制にも役立ちます。
NEWJI DX
製造業に特化したデジタルトランスフォーメーション(DX)の実現を目指す請負開発型のコンサルティングサービスです。AI、iPaaS、および先端の技術を駆使して、製造プロセスの効率化、業務効率化、チームワーク強化、コスト削減、品質向上を実現します。このサービスは、製造業の課題を深く理解し、それに対する最適なデジタルソリューションを提供することで、企業が持続的な成長とイノベーションを達成できるようサポートします。
オンライン講座
製造業、主に購買・調達部門にお勤めの方々に向けた情報を配信しております。
新任の方やベテランの方、管理職を対象とした幅広いコンテンツをご用意しております。
お問い合わせ
コストダウンが利益に直結する術だと理解していても、なかなか前に進めることができない状況。そんな時は、newjiのコストダウン自動化機能で大きく利益貢献しよう!
(Β版非公開)