- お役立ち記事
- Basics of powder/granule handling technology and know-how for troubleshooting
月間76,176名の
製造業ご担当者様が閲覧しています*
*2025年3月31日現在のGoogle Analyticsのデータより
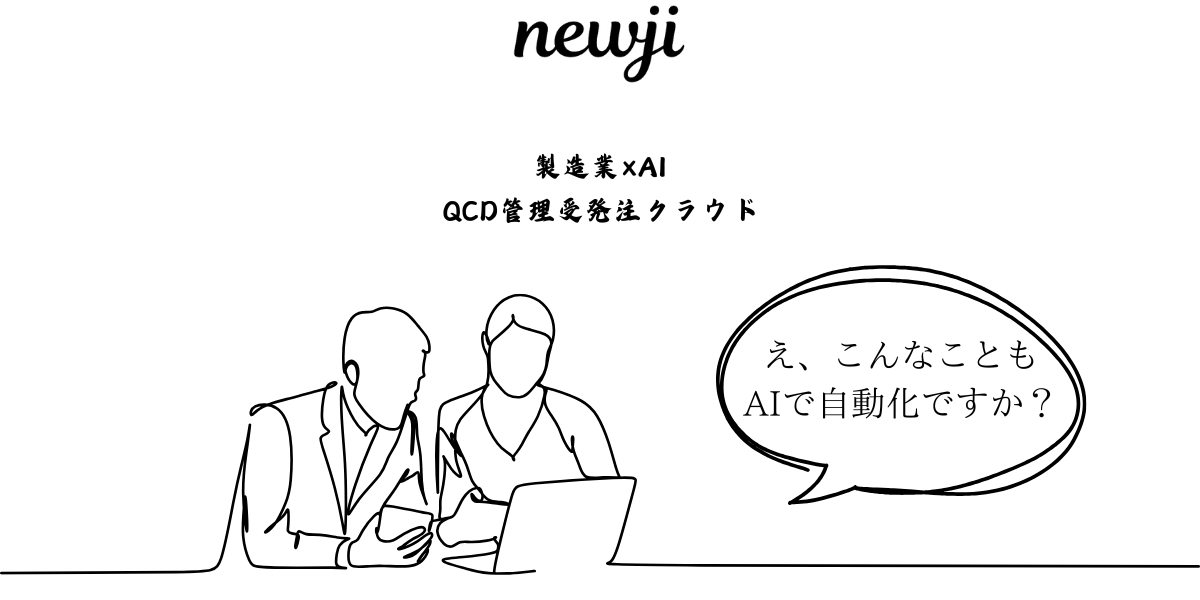
Basics of powder/granule handling technology and know-how for troubleshooting
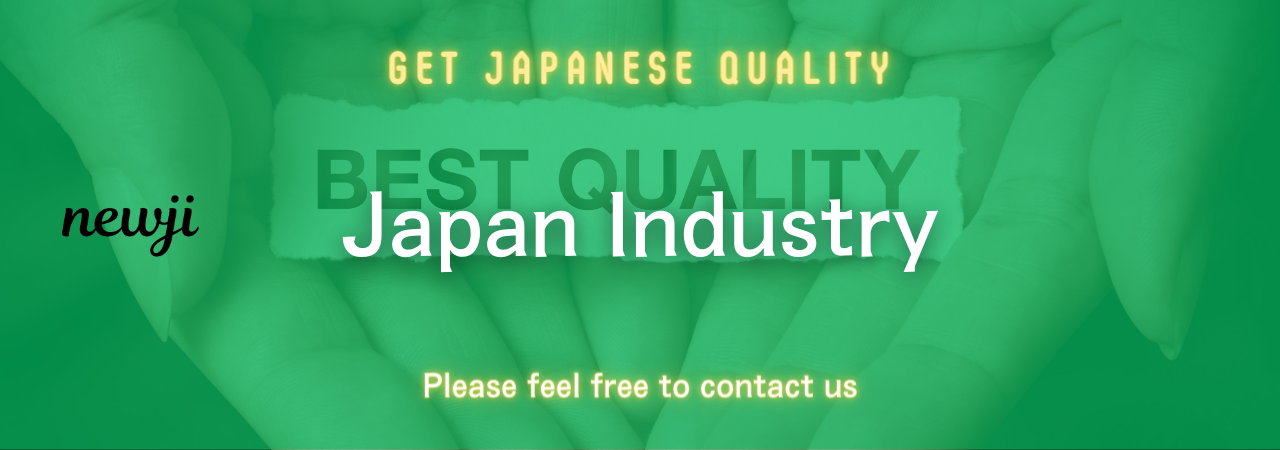
目次
Understanding Powder and Granule Handling
Handling powders and granules is a crucial part of many industries, including pharmaceuticals, food and beverages, chemicals, and construction.
The process involves managing small particles that can vary in size, shape, and flowability, which can significantly impact production efficiency and product quality.
Understanding the basics of this technology is essential for ensuring effective handling and processing.
The Importance of Particle Size
Particle size plays a vital role in the behavior of powders and granules.
It affects flowability, packing, surface area, and even the chemical reactivity of the materials involved.
For example, smaller particles tend to have higher surface areas, which can lead to increased reaction rates but may also result in handling challenges due to their tendency to clump.
In many industries, controlling particle size is critical for achieving the desired product characteristics.
Therefore, understanding the methods for measuring and manipulating particle size is essential for effective powder and granule processing.
Flowability and Its Challenges
Flowability refers to how easily a powder or granule can move through processing equipment.
It is influenced by factors such as particle size, shape, density, humidity, and electrostatic charges.
Poor flowability can lead to blockages, inconsistent dosing, and inefficient processing.
One common issue is the tendency of powders to clump or adhere to surfaces, which can obstruct flow and cause material loss.
To address this, various techniques such as vibration, air entrainment, and surface modifications might be applied to improve flowability.
Understanding Segregation
Segregation occurs when different particles within a powder or granule mixture separate due to differences in size, density, or shape during processing.
This can lead to inconsistent product quality and affect the final product’s functionality and appearance.
Several strategies can be employed to minimize segregation, including careful control of particle size distribution, using gentle mixing techniques, and employing equipment designed to reduce shear and turbulence.
Equipment Used in Powder and Granule Handling
Various types of equipment are used for handling powders and granules, each with unique features to address specific challenges.
Hoppers and Silos
Hoppers and silos are used for storage and dispensing.
They must be designed to ensure smooth discharge and prevent issues such as bridging (where material forms an arch preventing flow) and rat-holing (where a channel forms in the material, disrupting flow).
Conveyors
Conveyors, such as pneumatic and mechanical conveyors, are employed to transport materials between processing stages.
They are chosen based on factors like distance, speed, and sensitivity of the particles to handling.
Sifters and Screens
Sifters and screens are used to separate particles based on size, ensuring uniformity and quality in the final product.
They must be chosen considering the particle size, shape, and required throughput.
Mills and Grinders
For reducing particle size, mills and grinders are utilized.
The type of mill—such as ball mills, hammer mills, or jet mills—depends on the desired size reduction, material properties, and required precision.
Troubleshooting Common Issues
Inevitably, challenges and problems arise during powder and granule handling.
Having a systematic approach to troubleshooting can minimize downtime and improve process efficiency.
Identifying the Problem
The first step in troubleshooting is identifying the root cause of the issue.
Is the problem related to flowability, segregation, or equipment malfunction?
Gathering data from sensors and monitoring equipment can provide valuable insights into where and why issues occur.
Developing Solutions
Once the problem is identified, brainstorm potential solutions.
If the issue is related to flowability, consider modifying particle size or shape, adjusting humidity levels, or altering equipment settings.
For segregation issues, review the mixing process or explore equipment upgrades to reduce disparities in particle properties.
Implementing Changes
Any changes should be tested on a small scale before full implementation.
Monitoring the results carefully to ensure that the modifications effectively address the issue without introducing new problems is essential.
Continuous Improvement
Regularly reviewing and refining processes is crucial for maintaining efficient powder and granule handling.
By conducting routine evaluations and embracing new technologies, businesses can stay ahead of challenges and optimize their operations.
Best Practices for Efficient Handling
Implementing best practices can significantly enhance the efficiency and effectiveness of powder and granule handling:
Maintain Equipment Regularly
Regular maintenance of equipment helps prevent breakdowns and prolongs the lifespan of machinery, reducing the risk of costly downtime.
Train Personnel Adequately
Ensuring that staff are well-trained in handling techniques and familiar with the equipment and potential hazards can lead to more efficient and safer operations.
Optimize Environmental Conditions
Control environmental factors such as humidity and temperature to maintain ideal conditions for handling and processing powders and granules.
Embrace Technological Advances
Stay informed about advances in technology and equipment design that can improve handling processes, such as automation and advanced monitoring systems.
By understanding the essentials of powder and granule handling and following best practices, industries can enhance their operations and deliver high-quality products consistently.
Ultimately, investing in the right knowledge and technology leads to efficient processes, reduced waste, and increased profitability.
資料ダウンロード
QCD管理受発注クラウド「newji」は、受発注部門で必要なQCD管理全てを備えた、現場特化型兼クラウド型の今世紀最高の受発注管理システムとなります。
ユーザー登録
受発注業務の効率化だけでなく、システムを導入することで、コスト削減や製品・資材のステータス可視化のほか、属人化していた受発注情報の共有化による内部不正防止や統制にも役立ちます。
NEWJI DX
製造業に特化したデジタルトランスフォーメーション(DX)の実現を目指す請負開発型のコンサルティングサービスです。AI、iPaaS、および先端の技術を駆使して、製造プロセスの効率化、業務効率化、チームワーク強化、コスト削減、品質向上を実現します。このサービスは、製造業の課題を深く理解し、それに対する最適なデジタルソリューションを提供することで、企業が持続的な成長とイノベーションを達成できるようサポートします。
製造業ニュース解説
製造業、主に購買・調達部門にお勤めの方々に向けた情報を配信しております。
新任の方やベテランの方、管理職を対象とした幅広いコンテンツをご用意しております。
お問い合わせ
コストダウンが利益に直結する術だと理解していても、なかなか前に進めることができない状況。そんな時は、newjiのコストダウン自動化機能で大きく利益貢献しよう!
(β版非公開)