- お役立ち記事
- Basics of powder metallurgy technology and application to industrial products
月間76,176名の
製造業ご担当者様が閲覧しています*
*2025年3月31日現在のGoogle Analyticsのデータより
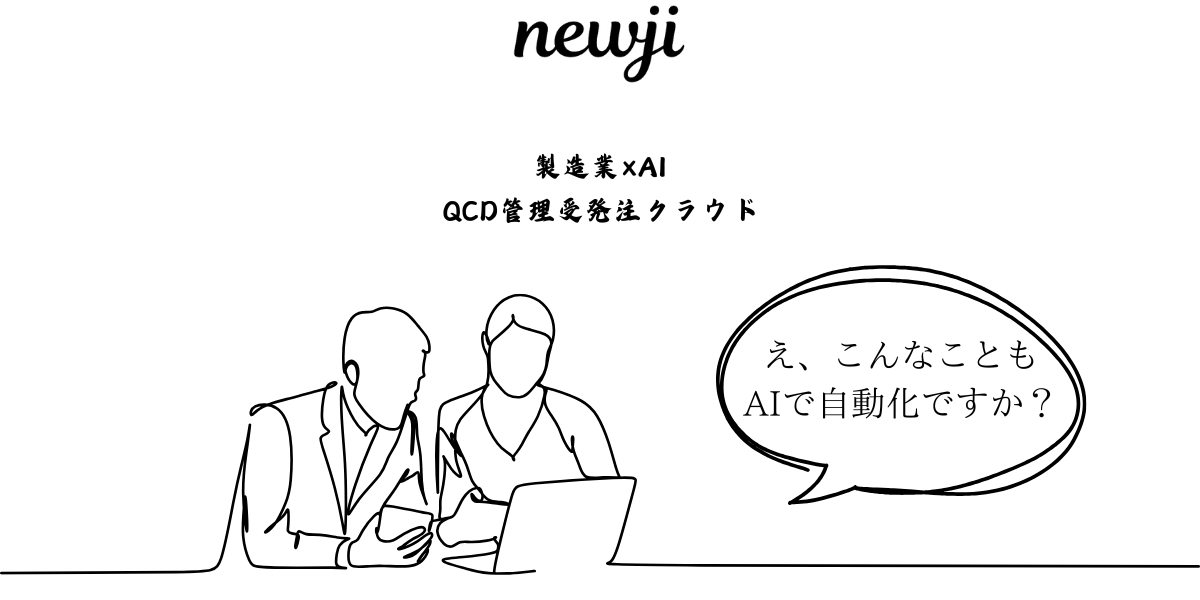
Basics of powder metallurgy technology and application to industrial products
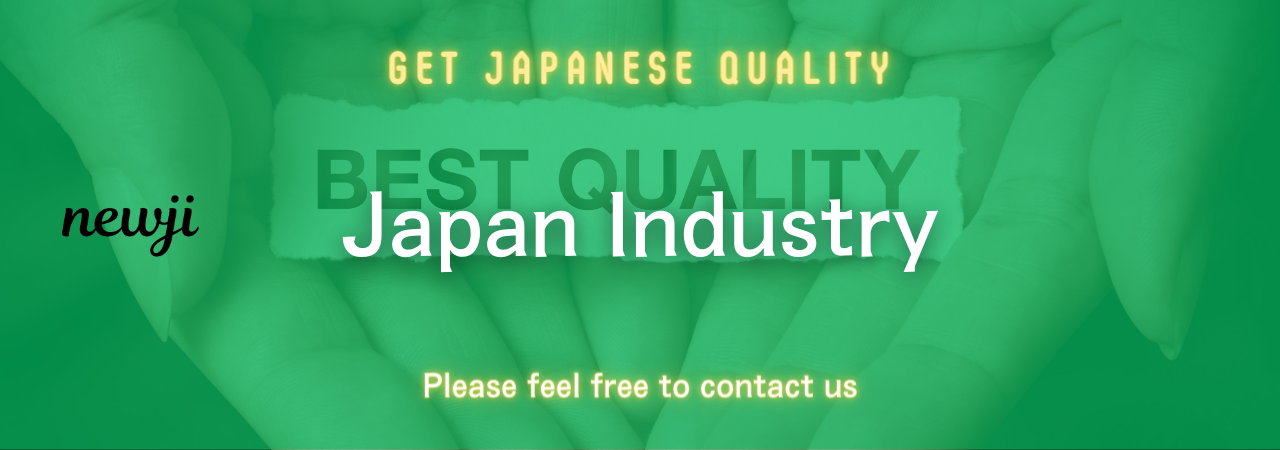
目次
Understanding Powder Metallurgy: An Introduction
Powder metallurgy is a fascinating and complex field that involves creating various products from metal powders.
This technology has a broad range of applications, offering numerous benefits in different industrial sectors.
Before diving into its applications, let’s grasp the basics of what powder metallurgy is and how it functions.
In simple terms, powder metallurgy is a process of turning metal powders into solid metal objects by heating them in controlled environments.
The process typically comprises four main steps: powder production, blending, compacting, and sintering.
Each step contributes to the creation of a finished product with the desired properties.
Powder Production: The Foundation
The first stage of powder metallurgy is powder production, which is crucial since the properties of the powder influence the final product’s characteristics.
There are several methods for producing metal powders, including atomization, reduction, electrolysis, and mechanical alloying.
Atomization involves breaking a molten metal stream into small droplets, which then solidify into powder particles.
Reduction is a chemical process that transforms metal oxides into powders using a reducing gas, such as hydrogen or carbon monoxide.
Electrolysis separates metals from their compounds through an electrical process, while mechanical alloying blends and grinds different metal powders to achieve a homogeneous mixture.
Blending: Preparing the Mixture
The next phase is blending, where different metal powders are mixed to ensure the distribution of particle sizes and compositions is uniform.
Additives such as lubricants may be included to improve the flow or compactibility of the mix.
It’s essential that the blend is uniform to achieve the desired properties in the final product.
Compacting: Shaping the Powder
Once blending is complete, the compacting process takes place.
This step involves pressing the powder blend into a desired shape using a die under high pressure.
The objective is to produce a “green” compact with sufficient strength to hold its form before sintering.
Compacting permits the creation of complex and precise shapes that may be challenging or impossible with other manufacturing techniques.
It’s also an energy-efficient step compared to processes that require melting metals.
Sintering: Solidifying the Structure
Sintering is the final step where the “green” compact is heated to a temperature below the metal’s melting point.
During this step, particles adhere to each other and create a solid structure.
The temperature and environment within the sintering furnace are carefully controlled to optimize the metallic bonds and enhance the mechanical properties of the finished product.
Sintering is pivotal as it enhances density, mechanical strength, and integrity of the product without the need for melting.
This step enables the formation of materials that are both strong and wear-resistant.
Applications in Industrial Products
Powder metallurgy is used in a wide array of industries, providing solutions that other manufacturing methods cannot.
Below are some critical applications of this technology in various sectors.
Automotive Industry: Enhancing Performance
In the automotive industry, powder metallurgy is instrumental in producing components like gears, bearings, shafts, and synchronizer rings.
The method is favored for its accuracy, material efficiency, and ability to produce parts with intricate designs.
Automotive components made by powder metallurgy contribute to reduced vehicle weight, improved fuel efficiency, and lower emissions.
Tools and Hardware: Combining Strength and Precision
The production of cutting tools, fasteners, and machinery parts is another important application of powder metallurgy.
These components benefit from enhanced wear resistance and surface hardness, attributes essential for tools operating under tough conditions.
This technology ensures high precision and functionality, even in complex geometries, which is crucial for minute and detailed hardware parts.
Aerospace Industry: Meeting High Standards
In aerospace, the demand for lightweight yet robust components is paramount.
Powder metallurgy is used to manufacture parts such as turbine disks and engine components that are critical to aircraft performance.
These components often require superior strength-to-weight ratios and high resistance to extreme conditions, achievable through precise control over material compositions.
Medical Sector: Creating Customized Solutions
The medical field also benefits from powder metallurgy, especially in producing surgical instruments and implants.
The technology allows for the development of biocompatible materials, crucial for implant devices used within the human body.
Customized implants tailored to specific patient requirements demonstrate the significant advancements made possible through powder metallurgy.
Consumer Electronics: Fostering Innovation
Lastly, the consumer electronics sector sees innovation through powder metallurgy in components such as magnetic materials and electrical contacts.
These materials improve the efficiency and longevity of devices, contributing to enhanced performance in everyday electronics like smartphones and laptops.
Conclusion: The Future of Powder Metallurgy
Powder metallurgy continues to evolve, opening doors to new applications and significant advancements in industrial manufacturing.
Its ability to create components with unique properties and complex shapes while minimizing waste makes it an appealing choice across various sectors.
As technology progresses, the scope for powder metallurgy will expand, leading to more innovative solutions and sustainable manufacturing practices.
Understanding the basics of powder metallurgy helps one appreciate its role in shaping the future of industrial products, serving as a testament to the remarkable capabilities of this technology.
資料ダウンロード
QCD管理受発注クラウド「newji」は、受発注部門で必要なQCD管理全てを備えた、現場特化型兼クラウド型の今世紀最高の受発注管理システムとなります。
ユーザー登録
受発注業務の効率化だけでなく、システムを導入することで、コスト削減や製品・資材のステータス可視化のほか、属人化していた受発注情報の共有化による内部不正防止や統制にも役立ちます。
NEWJI DX
製造業に特化したデジタルトランスフォーメーション(DX)の実現を目指す請負開発型のコンサルティングサービスです。AI、iPaaS、および先端の技術を駆使して、製造プロセスの効率化、業務効率化、チームワーク強化、コスト削減、品質向上を実現します。このサービスは、製造業の課題を深く理解し、それに対する最適なデジタルソリューションを提供することで、企業が持続的な成長とイノベーションを達成できるようサポートします。
製造業ニュース解説
製造業、主に購買・調達部門にお勤めの方々に向けた情報を配信しております。
新任の方やベテランの方、管理職を対象とした幅広いコンテンツをご用意しております。
お問い合わせ
コストダウンが利益に直結する術だと理解していても、なかなか前に進めることができない状況。そんな時は、newjiのコストダウン自動化機能で大きく利益貢献しよう!
(β版非公開)