- お役立ち記事
- Basics of production line automation design and productivity improvement methods using IoT
月間77,185名の
製造業ご担当者様が閲覧しています*
*2025年2月28日現在のGoogle Analyticsのデータより
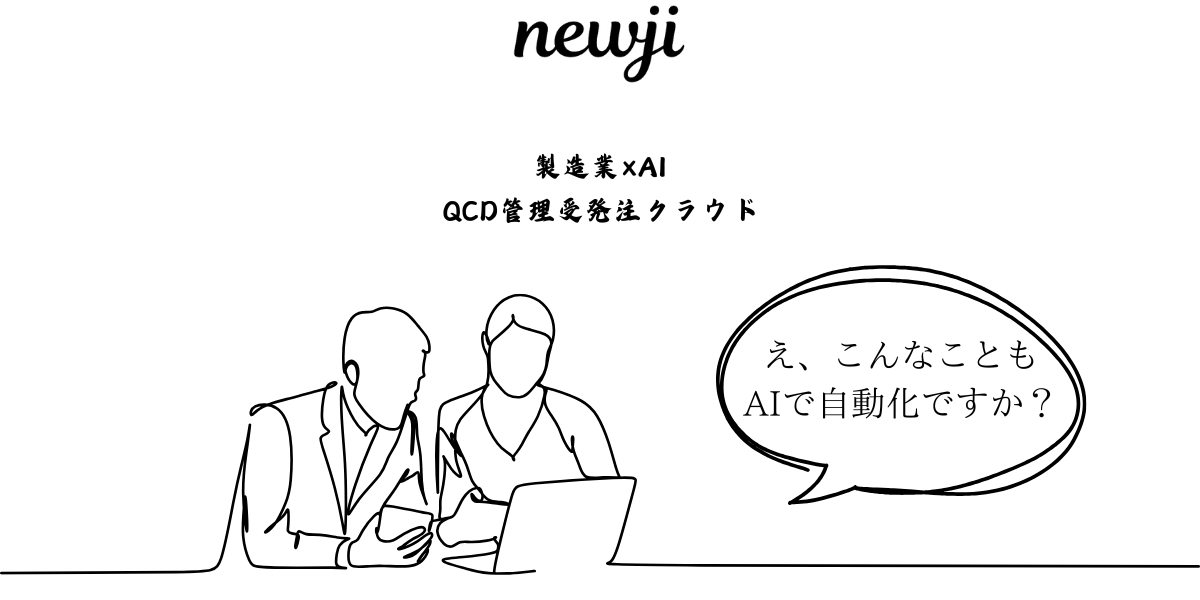
Basics of production line automation design and productivity improvement methods using IoT
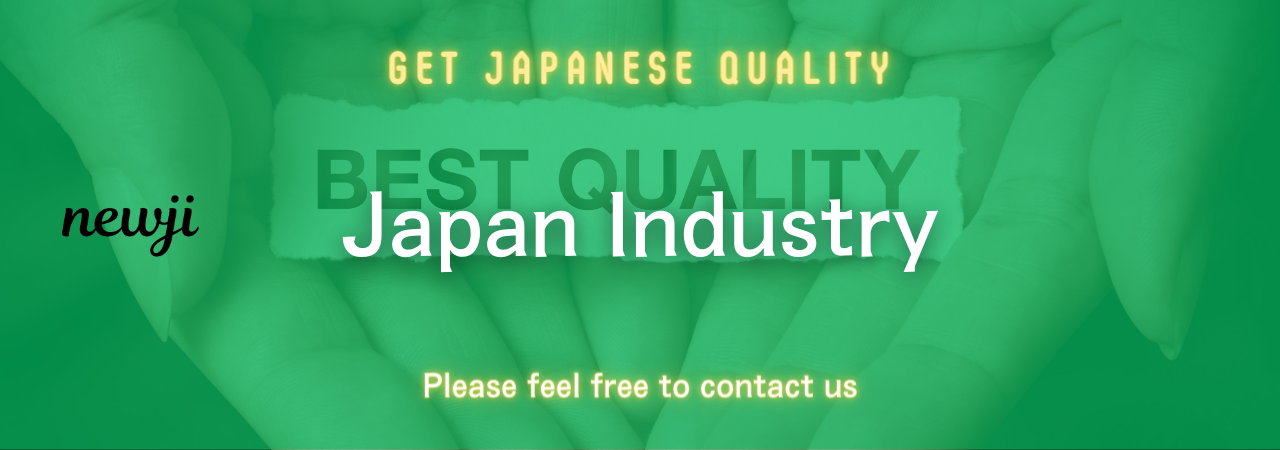
目次
Understanding Production Line Automation
Production line automation involves using technology to operate and control production processes with minimal human intervention.
Automation helps to streamline manufacturing operations, reduce errors, and enhance efficiency by using robots, control systems, and IT systems.
The main purpose of automation is to increase productivity, improve consistency, and ensure safety in the production line.
By integrating advanced technologies, companies can optimize production processes, minimize waste, and deliver high-quality products.
Key Components of a Production Line Automation System
A typical production line automation system includes several key components that work together seamlessly.
These components are essential for creating an efficient, automated manufacturing setup.
Robots and Machinery
Robots and automated machinery perform tasks traditionally done by humans.
They can handle repetitive tasks with precision, speed, and reliability, reducing the risk of human error.
Robots can be programmed to perform tasks like welding, assembly, packing, and quality inspections.
Control Systems
Control systems manage and regulate the operation of machines on the production line.
They ensure that every component functions smoothly and according to plan.
Control systems can range from simple programmable logic controllers (PLCs) to complex distributed control systems (DCS).
Sensors and Actuators
Sensors collect real-time data from the production line, such as temperature, pressure, and motion.
This data is vital for making informed decisions and maintaining quality control.
Actuators then translate these decisions into actions, controlling mechanisms such as motors and valves.
The Role of IoT in Production Line Automation
The Internet of Things (IoT) plays a crucial role in modernizing production line automation.
By connecting machines, devices, and sensors through the internet, IoT enables real-time data exchange and analytics.
Data Collection and Analysis
With IoT, manufacturers can collect and analyze large volumes of data from the production floor.
This data provides insights into machine performance, product quality, and process efficiency.
By analyzing this data, companies can identify bottlenecks, predict maintenance needs, and optimize production schedules.
Remote Monitoring and Control
IoT allows for remote monitoring and control of production lines.
Managers can access critical information and control systems from any location using internet-enabled devices.
This capability improves response times to issues and reduces downtime.
Predictive Maintenance
IoT helps in implementing predictive maintenance strategies, which preempt machine failures before they occur.
By using sensor data, manufacturers can recognize pattern deviations indicating wear or malfunction, scheduling maintenance proactively.
This approach extends equipment life, avoids unexpected failures, and reduces maintenance costs.
Improving Productivity with Automation and IoT
Enhancing productivity is a primary goal for most manufacturing companies, and automation combined with IoT can deliver significant improvements.
Reducing Downtime
One of the major benefits of automation is its ability to minimize downtime.
Automation systems can detect and address issues quickly, reducing overall production interruptions.
With IoT, these systems gain additional intelligence, allowing for better scheduling of maintenance activities and quicker resolution of problems.
Enhancing Flexibility
Automated systems offer increased operational flexibility.
They can handle a wide range of tasks and adapt to new production configurations faster than manual setups.
IoT further enhances this flexibility by enabling real-time adjustments based on demand and material availability.
Ensuring Quality
Consistent quality is paramount in manufacturing.
Automation helps maintain high standards by eliminating human errors and performing precise operations.
IoT enhances quality control through constant monitoring, real-time feedback, and data-driven decision-making.
This ensures each product meets specified standards, reducing waste and rework.
Optimizing Resource Utilization
Efficient use of resources, including energy and materials, is crucial for sustainable production.
Automation systems achieve this by optimizing machine operations and reducing wastage.
With IoT, resources can be monitored and evaluated meticulously, allowing for smarter use and minimized costs.
Challenges and Considerations in Automation Design
Despite the numerous benefits of automation and IoT, several challenges must be addressed when designing an automated production line.
Initial Investment Costs
Setting up an automated production line requires significant initial investment in equipment and technologies.
Companies should conduct thorough cost-benefit analyses to ensure the potential gains outweigh the expenses.
Integration with Existing Systems
Integrating new automated systems with existing machinery and software can be complex.
Manufacturers must assess compatibility and ensure seamless communication between all system components.
Data Security
IoT-connected systems are vulnerable to cybersecurity threats.
Manufacturers must implement robust security measures to protect sensitive data and ensure the integrity of production operations.
Workforce Adaptation
As automation reduces the need for routine manual labor, companies must consider workforce adaptations.
This may involve reskilling workers for more advanced roles in managing, maintaining, and improving automated systems.
In conclusion, production line automation with the integration of IoT offers transformative benefits in terms of productivity, efficiency, and quality.
While there are challenges to overcome, the right strategy and planning can lead to a successful implementation, unlocking significant potential for any manufacturing operation.
By leveraging these technologies, businesses can remain competitive in an ever-evolving industrial landscape.
資料ダウンロード
QCD管理受発注クラウド「newji」は、受発注部門で必要なQCD管理全てを備えた、現場特化型兼クラウド型の今世紀最高の受発注管理システムとなります。
ユーザー登録
受発注業務の効率化だけでなく、システムを導入することで、コスト削減や製品・資材のステータス可視化のほか、属人化していた受発注情報の共有化による内部不正防止や統制にも役立ちます。
NEWJI DX
製造業に特化したデジタルトランスフォーメーション(DX)の実現を目指す請負開発型のコンサルティングサービスです。AI、iPaaS、および先端の技術を駆使して、製造プロセスの効率化、業務効率化、チームワーク強化、コスト削減、品質向上を実現します。このサービスは、製造業の課題を深く理解し、それに対する最適なデジタルソリューションを提供することで、企業が持続的な成長とイノベーションを達成できるようサポートします。
製造業ニュース解説
製造業、主に購買・調達部門にお勤めの方々に向けた情報を配信しております。
新任の方やベテランの方、管理職を対象とした幅広いコンテンツをご用意しております。
お問い合わせ
コストダウンが利益に直結する術だと理解していても、なかなか前に進めることができない状況。そんな時は、newjiのコストダウン自動化機能で大きく利益貢献しよう!
(β版非公開)