- お役立ち記事
- Basics of production line layout design and application to factory automation
月間76,176名の
製造業ご担当者様が閲覧しています*
*2025年3月31日現在のGoogle Analyticsのデータより
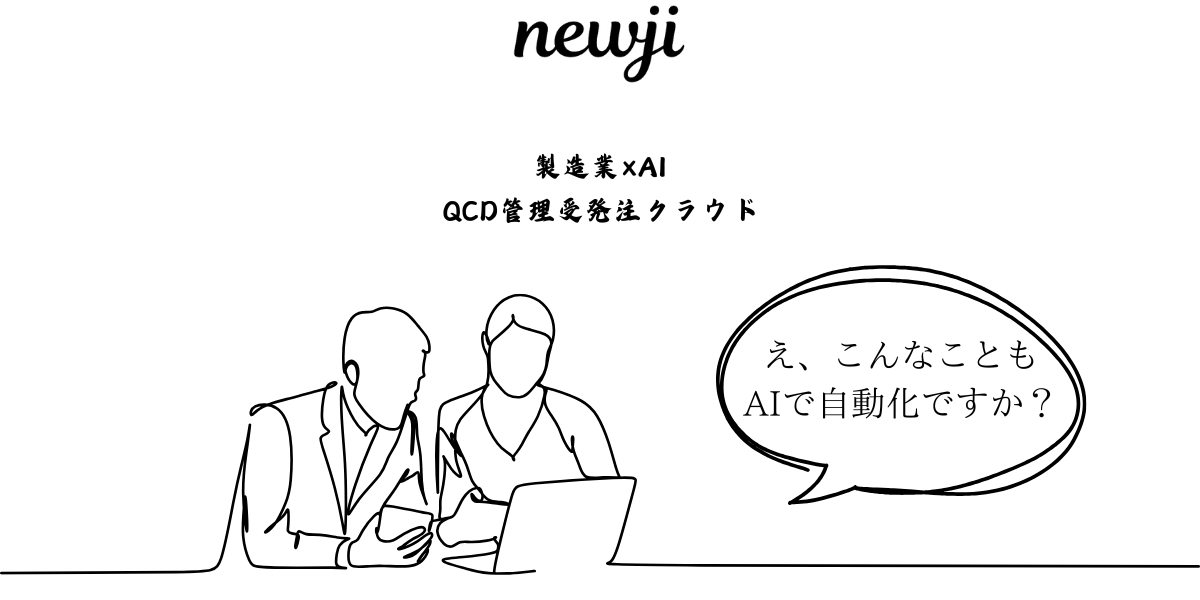
Basics of production line layout design and application to factory automation
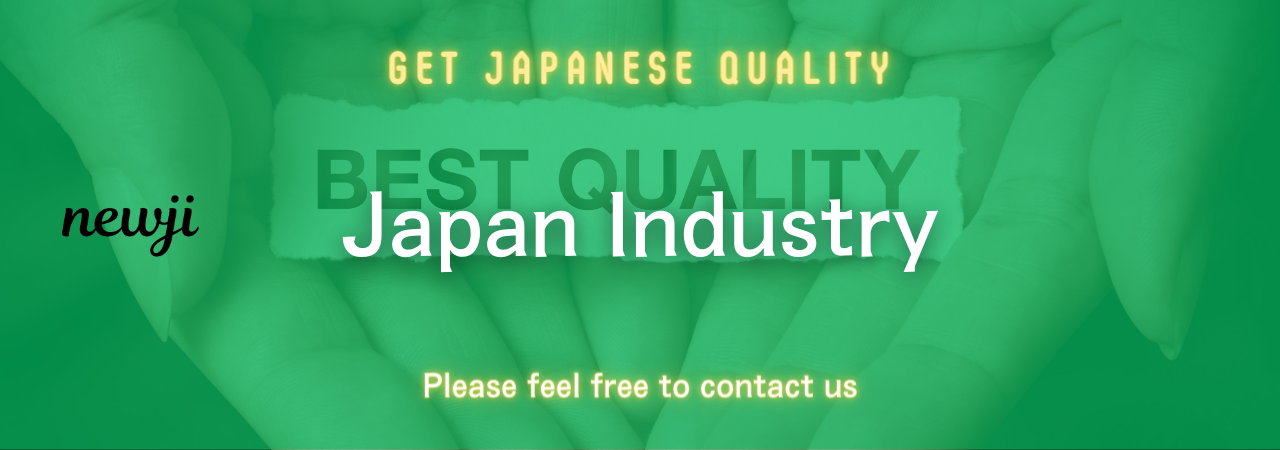
目次
Understanding Production Line Layout Design
Production line layout design is a crucial element in the manufacturing process that significantly impacts the efficiency and productivity of a factory.
The primary goal of layout design is to create a seamless flow of materials through the production process, minimizing waste and maximizing output.
Understanding the basics of production line layout design is essential for any business that aims to enhance its manufacturing processes and move towards factory automation.
A well-designed production line layout ensures that equipment and workstations are placed strategically to reduce the time and distance that products travel during the manufacturing process.
This can result in reduced labor costs, lower inventory levels, and improved quality control.
Moreover, with technological advancements in factory automation, production line layouts must be adaptable to incorporate new machinery and processes seamlessly.
Types of Production Line Layouts
There are several types of production line layouts, each suited for different manufacturing needs and processes.
Here are the most common types:
1. Product Layout
The product layout, also known as a production line or assembly line layout, is designed for the mass production of a single product or a few similar products.
In this layout, workstations and equipment are arranged in a linear order based on the sequence of operations needed to manufacture a product.
This type of layout is effective for high-volume production as it allows for the efficient movement of materials and quick assembly.
However, it lacks flexibility, making it less suitable for processes that require variation or customization.
2. Process Layout
Process layout groups similar machines and processes together, providing flexibility in operations.
This type of layout is ideal for manufacturing facilities that produce a variety of products or custom items.
In a process layout, machines are arranged by function.
For example, all cutting machines may be grouped together in one area, while all welding machines are in another.
This allows for easy adaptation to changes in production planning and scheduling.
3. Cellular Layout
Cellular layout, or cellular manufacturing, combines elements of both product and process layouts.
It organizes workstations or machines into cells that handle the production of a family of products similar in design or component needs.
Each cell operates like a small assembly line, and materials move through the cell in a more controlled and efficient manner.
This layout improves the flow of materials and reduces waiting times, making it suitable for flexible production processes.
4. Fixed-Position Layout
In a fixed-position layout, the product remains stationary while workers and machines move around it to perform manufacturing tasks.
This layout is often used for the assembly of large, heavy products or constructions, such as ships, airplanes, or buildings.
While it requires extensive planning and coordination, a fixed-position layout allows for customization and is adaptable to a wide range of projects.
Key Considerations in Layout Design
Designing a production line layout involves several key considerations to ensure efficiency and productivity:
Workflow
Workflow is a critical factor in layout design.
Processes should be arranged to facilitate smooth and logical transitions between workstations, minimizing the movement and handling of materials.
This leads to faster production times and reduced labor costs.
Space Utilization
Efficient use of space is crucial in production line layout design.
An optimal layout maximizes the use of available space while allowing for safe and unimpeded movement of workers and materials.
Consideration should also be given to future expansions or modifications in the layout.
Flexibility
Flexibility is increasingly important in today’s dynamic manufacturing environments.
Production layouts should be designed to accommodate changes in demand, production volumes, or processes.
A flexible layout can quickly adapt to new technologies, products, or market demands.
Safety
Safety should never be compromised in layout design.
Safe working conditions and appropriate safety measures must be considered, such as emergency exits, clear signage, and protective equipment.
Implementing Factory Automation
The integration of factory automation into production line layouts is a growing trend aimed at enhancing productivity and reducing operational costs.
Automation involves using machines, robotics, and computerized systems to perform tasks traditionally completed by human labor.
Automation can improve production consistency, quality control, and efficiency.
However, successful implementation requires careful planning and optimization of production line layouts.
Strategies for Automation
To integrate automation effectively, consider the following strategies:
Identify Automation Opportunities
Assess current manufacturing processes to identify repetitive, labor-intensive tasks that can benefit from automation.
Look for processes that require precision or pose health risks to workers.
Choose the Right Technology
Choose automation technologies that align with your manufacturing needs and production goals.
Consider factors such as scalability, cost, and compatibility with existing machinery.
Train the Workforce
Train the workforce to operate and maintain automated systems.
Skilled operators play a vital role in ensuring that automation systems run smoothly and efficiently.
Evaluate and Optimize
Continuously evaluate the performance of automated systems and optimize processes for improvement.
Regular maintenance and upgrades are essential to maximize the benefits of automation.
Production line layout design and factory automation are essential to modern manufacturing processes.
By understanding the fundamentals of layout design and considering the benefits of automation, businesses can streamline operations, reduce costs, and improve product quality.
It requires a balanced approach, combining efficient layout design with the strategic implementation of automation technologies, ultimately paving the way for enhanced productivity and competitiveness in the market.
資料ダウンロード
QCD管理受発注クラウド「newji」は、受発注部門で必要なQCD管理全てを備えた、現場特化型兼クラウド型の今世紀最高の受発注管理システムとなります。
ユーザー登録
受発注業務の効率化だけでなく、システムを導入することで、コスト削減や製品・資材のステータス可視化のほか、属人化していた受発注情報の共有化による内部不正防止や統制にも役立ちます。
NEWJI DX
製造業に特化したデジタルトランスフォーメーション(DX)の実現を目指す請負開発型のコンサルティングサービスです。AI、iPaaS、および先端の技術を駆使して、製造プロセスの効率化、業務効率化、チームワーク強化、コスト削減、品質向上を実現します。このサービスは、製造業の課題を深く理解し、それに対する最適なデジタルソリューションを提供することで、企業が持続的な成長とイノベーションを達成できるようサポートします。
製造業ニュース解説
製造業、主に購買・調達部門にお勤めの方々に向けた情報を配信しております。
新任の方やベテランの方、管理職を対象とした幅広いコンテンツをご用意しております。
お問い合わせ
コストダウンが利益に直結する術だと理解していても、なかなか前に進めることができない状況。そんな時は、newjiのコストダウン自動化機能で大きく利益貢献しよう!
(β版非公開)