- お役立ち記事
- Basics of production planning and key points for improving the efficiency of the PDCA cycle
月間76,176名の
製造業ご担当者様が閲覧しています*
*2025年3月31日現在のGoogle Analyticsのデータより
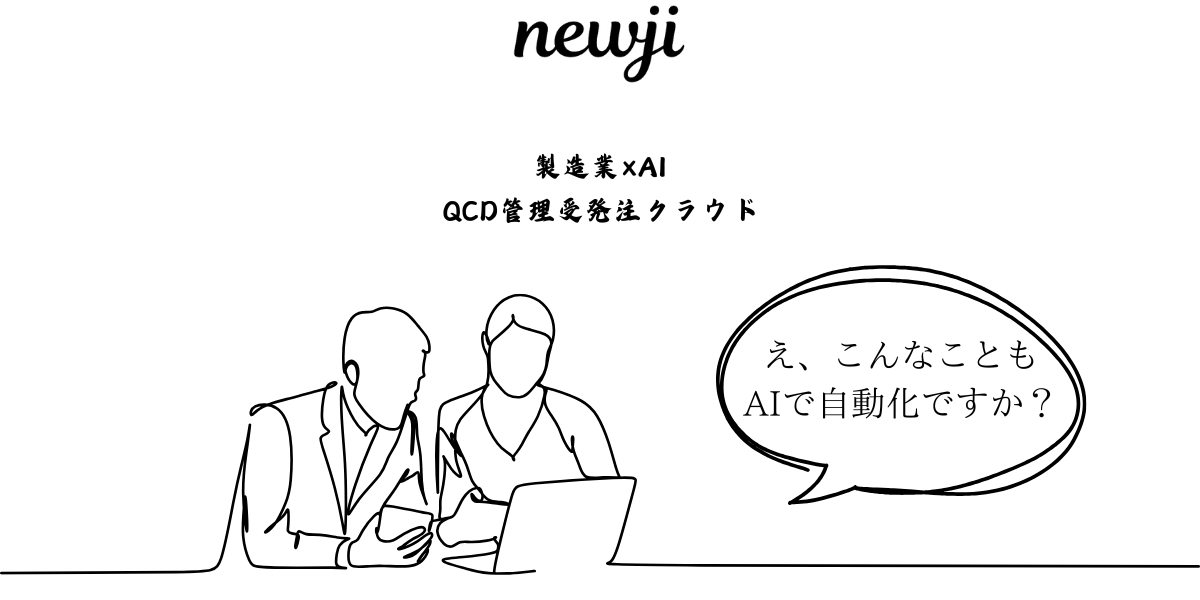
Basics of production planning and key points for improving the efficiency of the PDCA cycle
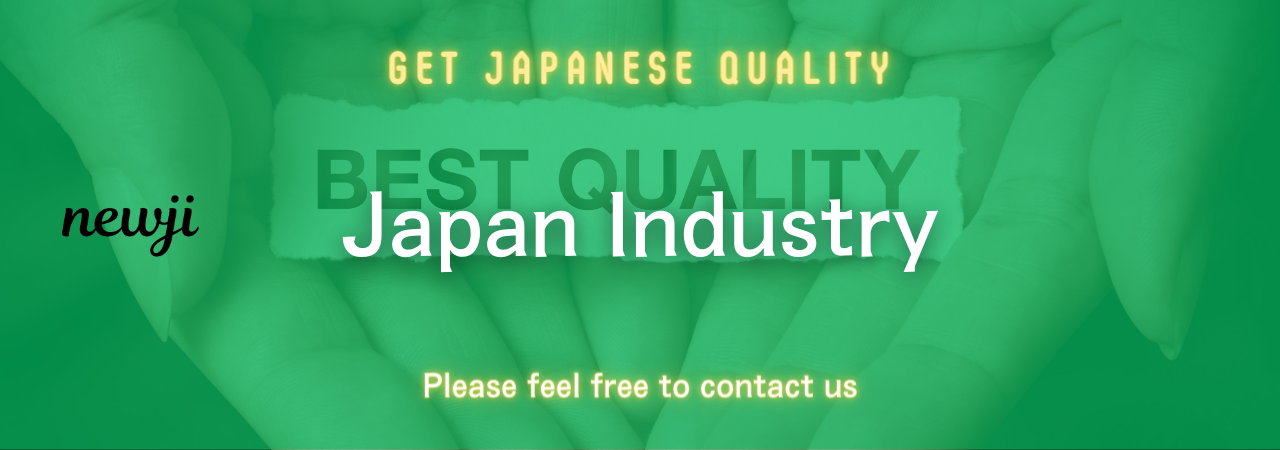
目次
Understanding Production Planning
Production planning is an essential aspect of the manufacturing process.
It involves the preparation, scheduling, and control of the production activities.
The main goal is to ensure that the manufacturing process runs smoothly, efficiently, and economically.
Production planning helps companies meet their delivery deadlines while maintaining product quality.
At its core, production planning seeks to balance demand and supply.
It considers various factors such as raw material availability, production capacity, and workforce capabilities.
Effective production planning minimizes waste and enhances productivity.
Types of Production Planning
There are several types of production planning, each tailored to specific manufacturing needs.
– **Job Production Planning**: This focuses on producing customized products that are tailored to individual customer requirements.
It is commonly used in industries where bespoke production is necessary, like shipbuilding or custom machinery.
– **Batch Production Planning**: This method involves producing goods in batches or groups.
It’s used in scenarios where products are similar but not identical, allowing for adjustments in the production process between batches.
– **Flow Production Planning**: Also known as mass production, this type focuses on producing standardized items in large quantities.
It’s typical in industries like automotive manufacturing, where the production line is continuously running.
Each type of production planning has its own set of advantages and challenges.
Choosing the right method depends on the product type, production volume, and business goals.
The PDCA Cycle in Production Planning
The PDCA cycle stands for Plan, Do, Check, and Act.
It’s a management method used to achieve continuous improvement in processes.
In production planning, the PDCA cycle is an invaluable tool for optimizing operations and enhancing efficiency.
Plan
In the planning stage, goals are set based on the analysis of current production capabilities and market demands.
This involves forecasting demand, calculating production capacity, and determining the resources needed.
A detailed production schedule is also created to outline the steps necessary to achieve the set goals.
Do
The “Do” phase involves implementing the plans developed in the previous stage.
It includes executing the production schedule, coordinating resources, and ensuring the workforce understands their roles.
Effective communication and coordination are crucial during this phase to prevent disruptions and maintain workflow.
Check
In the checking stage, the actual performance is measured against the planned objectives.
This involves monitoring production outputs, quality control checks, and resource utilization.
Any discrepancies or deviations from the plan are recorded for analysis.
Act
The “Act” phase focuses on taking corrective actions based on the insights gained from the “Check” phase.
If the goals are not met, adjustments to the production process are made.
This stage helps in refining strategies, improving efficiency, and ultimately enhancing product quality.
Key Points for Improving PDCA Cycle Efficiency
For businesses looking to improve the efficiency of their PDCA cycle, several key points can be considered.
Clear Goal Setting
Setting clear, measurable goals at the planning stage is crucial.
Goals should be specific, attainable, and time-bound.
This clarity ensures everyone in the organization understands what is expected and can work towards the same objectives.
Data-Driven Decisions
Relying on accurate data for decision-making is essential.
Invest in systems that provide real-time data on production metrics, inventory levels, and market trends.
This information helps in making informed decisions throughout the PDCA cycle.
Employee Training and Engagement
A well-trained workforce is vital for the successful implementation of production plans.
Regular training sessions ensure employees are aware of the latest production techniques and safety protocols.
Engaging employees and encouraging feedback can also lead to valuable insights and improvements in the production process.
Regular Review and Adjustment
The production process should be regularly reviewed to identify areas for improvement.
This is particularly important in the “Check” phase of the PDCA cycle.
Regular reviews help in identifying patterns, resolving persistent issues, and optimizing processes.
Conclusion
Understanding the basics of production planning and effectively utilizing the PDCA cycle can significantly improve efficiency and production outcomes.
By setting clear goals, making data-driven decisions, investing in employee development, and regularly reviewing processes, businesses can enhance their production capabilities.
Continuous improvement through the PDCA cycle ensures a business remains competitive and can quickly adapt to changes in demand and market conditions.
Incorporating these strategies into your production planning can lead to substantial gains in productivity and efficiency, ultimately contributing to long-term business success.
資料ダウンロード
QCD管理受発注クラウド「newji」は、受発注部門で必要なQCD管理全てを備えた、現場特化型兼クラウド型の今世紀最高の受発注管理システムとなります。
ユーザー登録
受発注業務の効率化だけでなく、システムを導入することで、コスト削減や製品・資材のステータス可視化のほか、属人化していた受発注情報の共有化による内部不正防止や統制にも役立ちます。
NEWJI DX
製造業に特化したデジタルトランスフォーメーション(DX)の実現を目指す請負開発型のコンサルティングサービスです。AI、iPaaS、および先端の技術を駆使して、製造プロセスの効率化、業務効率化、チームワーク強化、コスト削減、品質向上を実現します。このサービスは、製造業の課題を深く理解し、それに対する最適なデジタルソリューションを提供することで、企業が持続的な成長とイノベーションを達成できるようサポートします。
製造業ニュース解説
製造業、主に購買・調達部門にお勤めの方々に向けた情報を配信しております。
新任の方やベテランの方、管理職を対象とした幅広いコンテンツをご用意しております。
お問い合わせ
コストダウンが利益に直結する術だと理解していても、なかなか前に進めることができない状況。そんな時は、newjiのコストダウン自動化機能で大きく利益貢献しよう!
(β版非公開)