- お役立ち記事
- Basics of quality assurance system and risk assessment essential for procurement operations
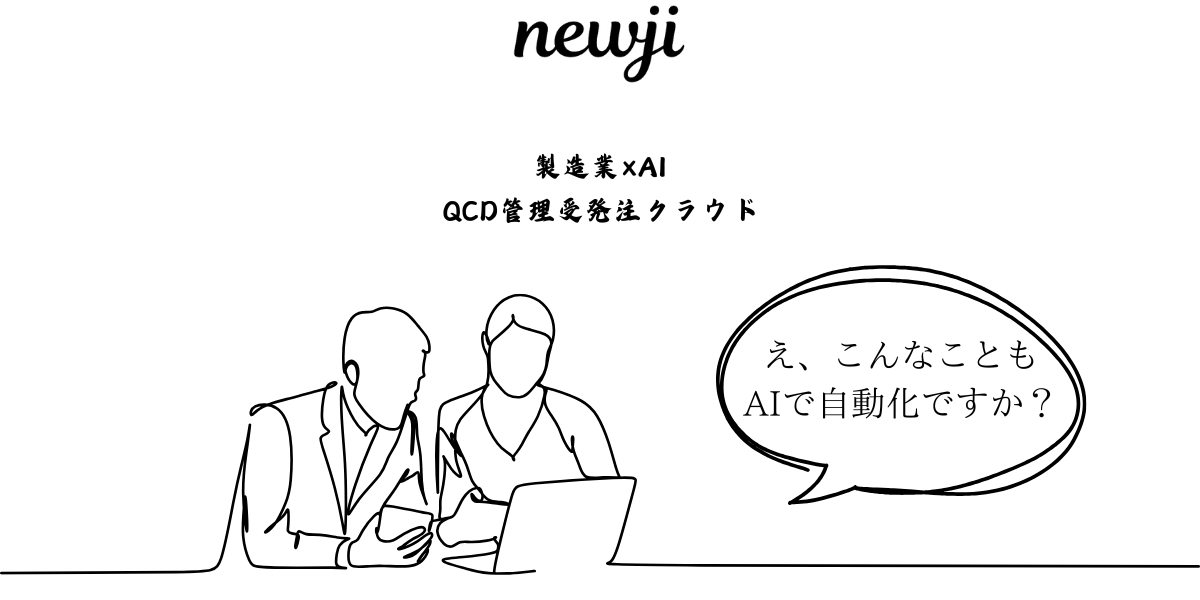
Basics of quality assurance system and risk assessment essential for procurement operations
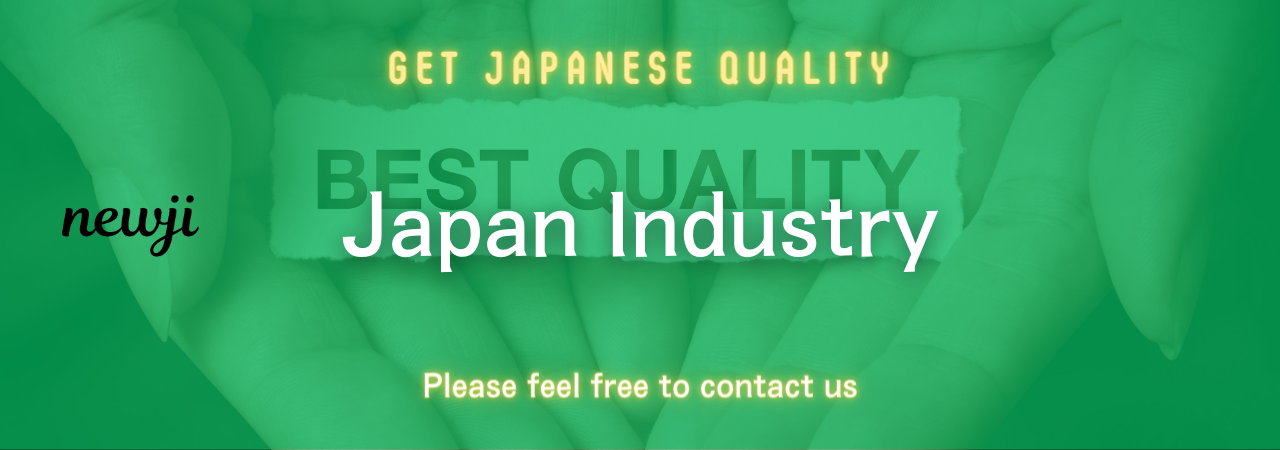
目次
Understanding Quality Assurance in Procurement
In the world of procurement, ensuring the quality of products and services is paramount.
Quality assurance plays a critical role in maintaining standards and customer satisfaction.
It’s a systematic process of checking to see whether the goods and services being provided meet specified requirements.
A quality assurance system is designed to prevent mistakes and defects in manufactured products and to avoid problems when delivering solutions or services to customers.
This process involves the assessment, planning, and control of production processes to ensure that each aspect of the procurement fulfills the desired quality.
For businesses involved in procurement, having a robust quality assurance system is not just about compliance.
It’s also about creating trust with your stakeholders by consistently delivering on your promises.
Such a system allows organizations to meet regulatory standards and customer expectations, thus fostering long-term relationships with clients.
The Role of Quality Assurance Systems
Quality assurance systems are essential for streamlining procurement operations.
They serve as an integral part of the operational framework that organizations deploy to enhance efficiency and reduce waste.
By implementing these systems, procurement teams can mitigate risks, lower costs, and improve the overall performance of the supply chain.
Firstly, these systems help in defining the quality objectives and metrics that need to be achieved.
They provide clear guidelines on what is required from suppliers.
Such systems also ensure that the products delivered are free from defects and meet both statutory and regulatory requirements.
Secondly, quality assurance systems foster continuous improvement.
By analyzing performance data, organizations can identify areas for improvement and implement changes that enhance efficiency.
Finally, these systems support supplier evaluation and development by providing a benchmark for assessing suppliers’ capabilities and performance.
The Basics of Risk Assessment in Procurement
Risk assessment is a critical component of procurement operations.
It’s about identifying, analyzing, and managing potential risks that could impact the procurement process.
A thorough risk assessment helps in making informed decisions, thus safeguarding the organization against unforeseen scenarios.
The first step in risk assessment involves identifying potential risks.
This includes everything from supplier reliability issues, quality concerns, delivery delays, and even financial risks.
By understanding these risks, procurement teams can prioritize them based on the likelihood of occurrence and the potential impact.
Once risks have been identified, they need to be evaluated.
This involves analyzing the probability of each risk occurring and understanding its impact on the organization.
Risk assessment tools like a risk matrix can be used to assess the significance of each risk.
After evaluation, appropriate risk mitigation strategies need to be developed.
This might involve selecting more reliable suppliers, requiring additional quality checks, diversifying the supplier base, or even revisiting contractual agreements to include risk-sharing clauses.
Importance of Integrating Quality Assurance and Risk Assessment
When integrated properly, quality assurance and risk assessment can provide a holistic approach to managing procurement operations.
Quality assurance focuses on ensuring that procured goods and services meet the desired standards, while risk assessment ensures that potential challenges are identified and managed proactively.
For instance, having a quality assurance system that includes regular supplier audits can help in identifying suppliers that may pose a risk to the supply chain.
This proactive approach allows procurement teams to make informed decisions about which suppliers to engage with and which to avoid.
Moreover, by integrating these systems, organizations can achieve better compliance with industry standards and regulations.
This not only reduces the risk of legal penalties but also enhances the reputation of the business.
Effective integration also facilitates better communication and collaboration between various departments within an organization.
When quality assurance and risk management teams work together, they provide valuable insights that can lead to improved procurement strategies.
Best Practices for Implementing Quality Assurance and Risk Assessment
To effectively implement quality assurance and risk assessment systems, there are several best practices that organizations should consider.
Firstly, ensure that there’s clear leadership and accountability.
Leadership commitment is essential for driving the organization’s quality and risk management agenda forward.
Assign clear roles and responsibilities to team members to foster accountability.
Secondly, invest in training and development.
Equip your procurement staff with the necessary skills and knowledge to implement and manage quality assurance and risk management processes effectively.
Thirdly, leverage technology.
Use modern tools for data collection, analysis, and reporting.
Automation can significantly enhance the efficiency of quality assurance and risk assessment processes.
Fourthly, engage suppliers in the quality assurance process.
Collaborate closely with suppliers to ensure they understand your standards and expectations.
Provide feedback to suppliers and work with them to improve their processes.
Finally, continuously review and adapt your systems.
As business environments and industry standards evolve, organizations must update their quality assurance and risk assessment strategies to remain relevant and effective.
Conclusion
In conclusion, quality assurance and risk assessment are foundational elements in procurement operations.
Both functions are critical for ensuring that products and services delivered meet the necessary standards and for safeguarding the organization against potential risks.
By implementing these systems effectively, organizations can enhance their operational efficiency, reduce waste, and build strong relationships with stakeholders.
資料ダウンロード
QCD調達購買管理クラウド「newji」は、調達購買部門で必要なQCD管理全てを備えた、現場特化型兼クラウド型の今世紀最高の購買管理システムとなります。
ユーザー登録
調達購買業務の効率化だけでなく、システムを導入することで、コスト削減や製品・資材のステータス可視化のほか、属人化していた購買情報の共有化による内部不正防止や統制にも役立ちます。
NEWJI DX
製造業に特化したデジタルトランスフォーメーション(DX)の実現を目指す請負開発型のコンサルティングサービスです。AI、iPaaS、および先端の技術を駆使して、製造プロセスの効率化、業務効率化、チームワーク強化、コスト削減、品質向上を実現します。このサービスは、製造業の課題を深く理解し、それに対する最適なデジタルソリューションを提供することで、企業が持続的な成長とイノベーションを達成できるようサポートします。
オンライン講座
製造業、主に購買・調達部門にお勤めの方々に向けた情報を配信しております。
新任の方やベテランの方、管理職を対象とした幅広いコンテンツをご用意しております。
お問い合わせ
コストダウンが利益に直結する術だと理解していても、なかなか前に進めることができない状況。そんな時は、newjiのコストダウン自動化機能で大きく利益貢献しよう!
(Β版非公開)