- お役立ち記事
- Basics of quality assurance systems and supplier audits required of purchasing departments
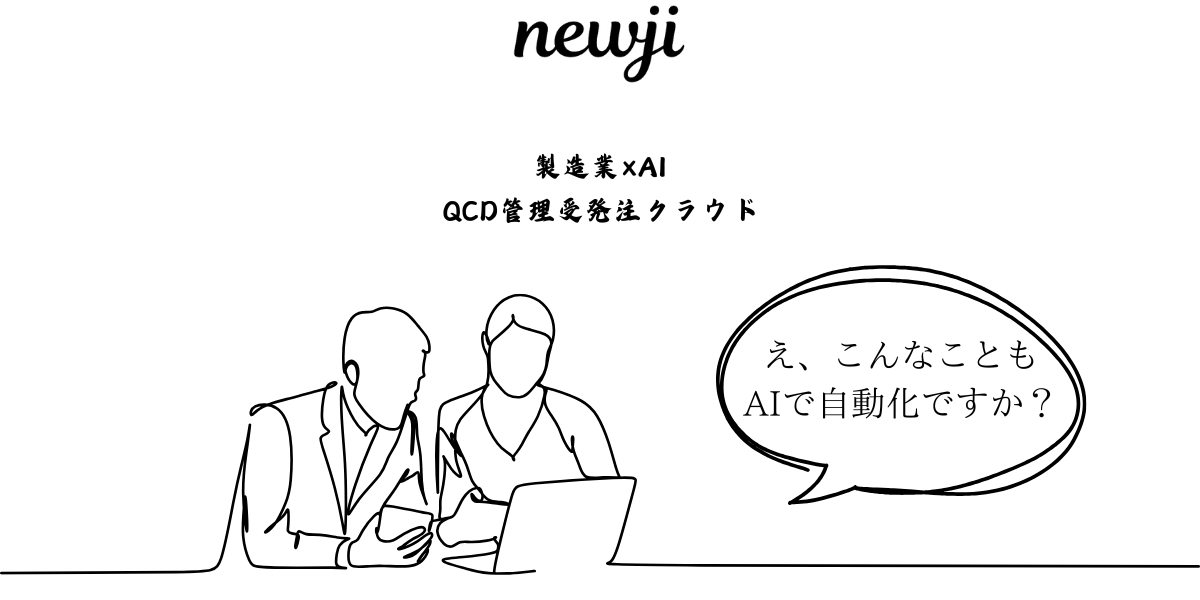
Basics of quality assurance systems and supplier audits required of purchasing departments
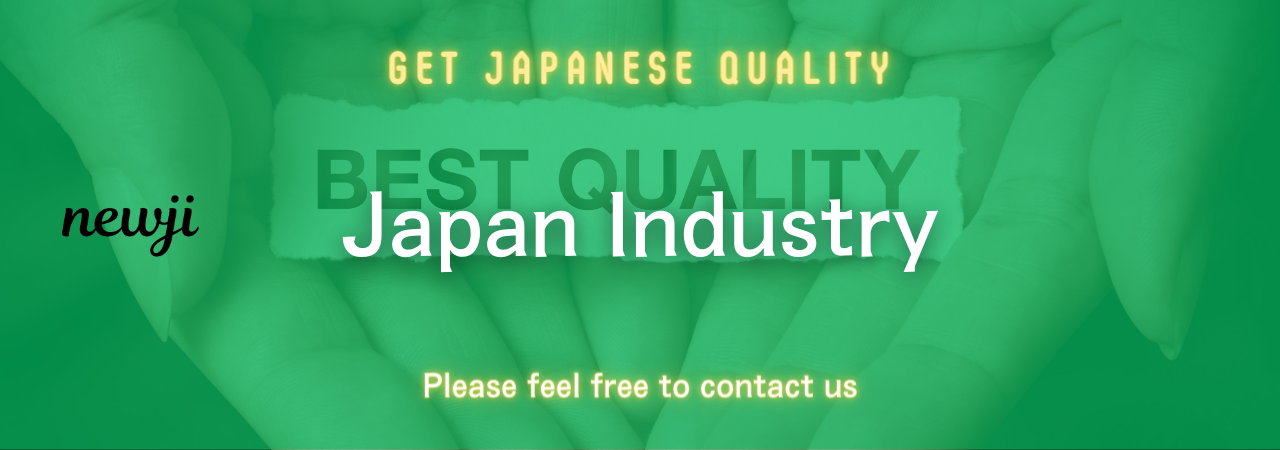
目次
Understanding Quality Assurance Systems
Quality assurance systems are essential for maintaining the integrity of products and services in any organization.
These systems are designed to ensure that products meet certain standards of quality and are free from defects.
They involve systematic processes that encompass everything from product design and development to production and distribution.
Quality assurance involves several key components.
Firstly, it includes defining the standards and specifications that products and services must meet.
These standards might be set by industry regulations, customer expectations, or a company’s own internal guidelines.
Next, quality assurance requires the implementation of processes to meet these standards.
This could involve setting up quality control checkpoints at various stages of production or ensuring that employees are trained to carry out their roles effectively.
Documentation is also a critical aspect, capturing procedures, quality checks, and corrective actions.
Importance in the Purchasing Department
For purchasing departments, quality assurance is particularly crucial.
The products and services they procure must meet company standards to maintain brand reputation and customer satisfaction.
A purchasing department needs to have quality assurance systems in place to evaluate and select suppliers who can provide quality materials consistently.
One way purchasing departments ensure quality is through supplier evaluations and audits.
These assessments help to identify reliable suppliers and maintain a good supply chain by ensuring consistency in quality.
This process not only mitigates risks but also builds strong relationships with suppliers who understand the company’s quality expectations.
Supplier Audits in the Purchasing Process
Supplier audits are a fundamental component of quality assurance in purchasing.
These audits ensure that suppliers adhere to the contract’s stipulated standards and practices.
By conducting audits, purchasing departments can verify that suppliers deliver quality goods and comply with quality control measures.
Supplier audits evaluate several areas, including the supplier’s production processes, quality control systems, and compliance with regulations.
The audit process might include onsite visits, reviews of documentation, interviews with key personnel, and assessment of facilities.
Benefits of Supplier Audits
There are several benefits to conducting supplier audits.
Firstly, they provide assurance that products and materials meet the required standards, reducing the risk of defects and recalls.
Supplier audits also help identify potential issues before they become significant problems, allowing for preventative measures to be implemented.
Another benefit is the increased transparency and communication between the supplier and the purchasing department.
Audits can lead to improved supplier performance by identifying areas for improvement and facilitating discussion about quality expectations.
Moreover, audits can strengthen supplier relationships.
By engaging in regular audits, purchasing departments demonstrate their commitment to quality and open channels for better collaboration, and shared objectives.
Implementing an Effective Quality Assurance System
An effective quality assurance system requires the involvement of various stakeholders within an organization, especially the purchasing department.
To begin with, the purchasing department should develop a clear quality assurance policy that aligns with organizational goals and objectives.
Training is another vital aspect.
Employees in the purchasing department should receive training on quality standards, auditing techniques, and ways to implement quality assurance processes effectively.
This ensures that everyone is on the same page and consistently upholding quality standards.
The use of technology can enhance the efficiency of quality assurance systems.
Utilizing quality management software can streamline processes by automating quality checks, documentation, and reporting.
This technology can provide real-time insights, helping purchasing departments to make informed decisions quickly.
Continuous Improvement and Feedback Loops
Continuous improvement is a crucial element of effective quality assurance systems.
Organizations should establish feedback loops to consistently enhance quality assurance processes and supplier performance.
Regularly reviewing performance metrics and audit results enables purchasing departments to identify trends, issues, and opportunities for improvement.
Quality assurance systems should always allow for flexibility and adaptation.
Incorporating feedback from suppliers and customers can help refine processes and improve overall quality.
Encouraging suppliers to adopt similar continuous improvement practices can lead to better results and stronger partnerships.
Conclusion
Quality assurance systems and supplier audits are indispensable for the purchasing departments of any organization.
They ensure that products and services meet the highest standards of quality, safeguarding the brand’s reputation and customer satisfaction.
By implementing a robust quality assurance system, purchasing departments can choose reliable suppliers, minimize risks, and foster collaborative relationships.
Audits, technology, and continuous improvement play essential roles.
When adopted strategically, these practices lead to enhanced performance, innovation, and long-term success.
It’s not just about checking boxes, but about embedding quality into every facet of the purchasing process.
資料ダウンロード
QCD調達購買管理クラウド「newji」は、調達購買部門で必要なQCD管理全てを備えた、現場特化型兼クラウド型の今世紀最高の購買管理システムとなります。
ユーザー登録
調達購買業務の効率化だけでなく、システムを導入することで、コスト削減や製品・資材のステータス可視化のほか、属人化していた購買情報の共有化による内部不正防止や統制にも役立ちます。
NEWJI DX
製造業に特化したデジタルトランスフォーメーション(DX)の実現を目指す請負開発型のコンサルティングサービスです。AI、iPaaS、および先端の技術を駆使して、製造プロセスの効率化、業務効率化、チームワーク強化、コスト削減、品質向上を実現します。このサービスは、製造業の課題を深く理解し、それに対する最適なデジタルソリューションを提供することで、企業が持続的な成長とイノベーションを達成できるようサポートします。
オンライン講座
製造業、主に購買・調達部門にお勤めの方々に向けた情報を配信しております。
新任の方やベテランの方、管理職を対象とした幅広いコンテンツをご用意しております。
お問い合わせ
コストダウンが利益に直結する術だと理解していても、なかなか前に進めることができない状況。そんな時は、newjiのコストダウン自動化機能で大きく利益貢献しよう!
(Β版非公開)