- お役立ち記事
- Basics of quality function deployment (QFD) and key points for effective quality and reliability improvement
月間76,176名の
製造業ご担当者様が閲覧しています*
*2025年3月31日現在のGoogle Analyticsのデータより
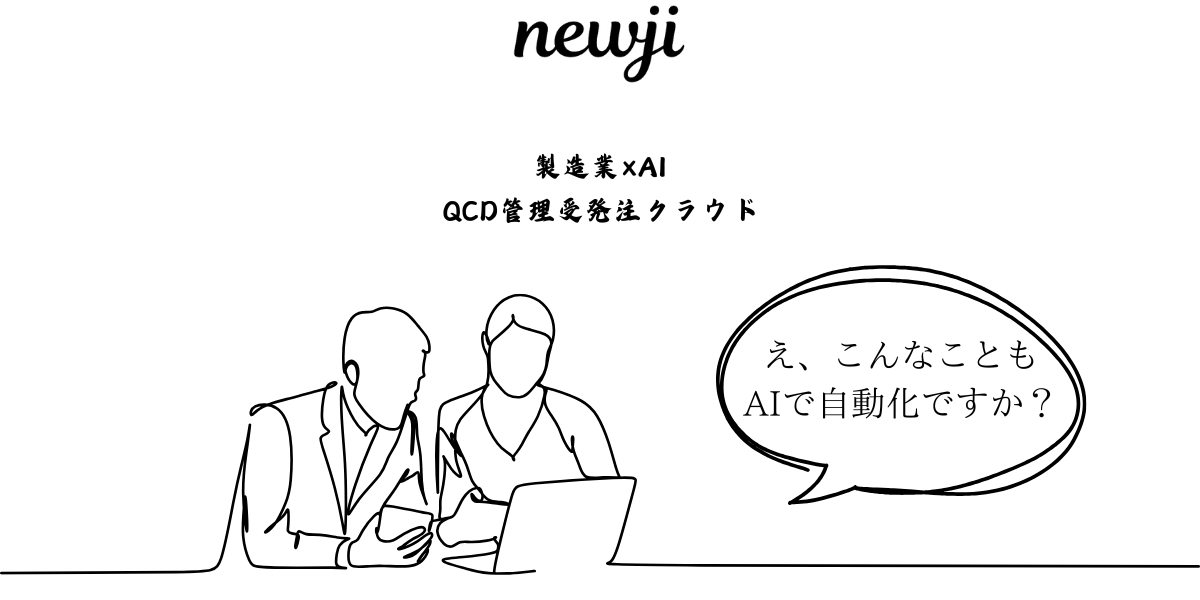
Basics of quality function deployment (QFD) and key points for effective quality and reliability improvement
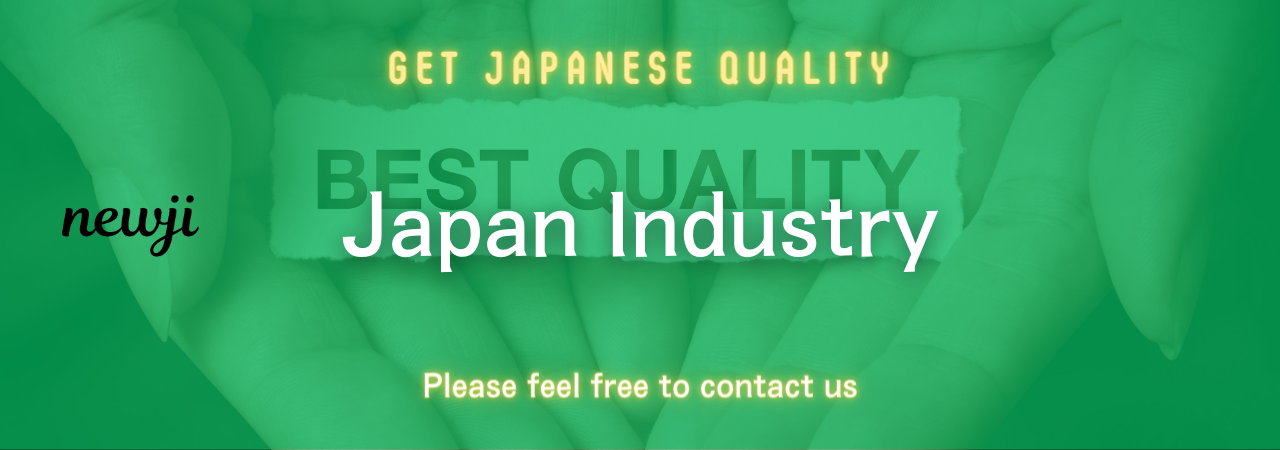
目次
Understanding Quality Function Deployment (QFD)
Quality Function Deployment, commonly referred to as QFD, is a structured approach used in the product development process.
It ensures that the voice of the customer (VoC) is captured and translated into technical requirements to create high-quality products.
The method originated in Japan in the late 1960s and has since gained international prominence due to its effectiveness in improving product quality and aligning design with customer needs.
QFD is crucial in bridging the gap between what customers want and what companies produce.
This method systematically maps customer demands into product specifications, ensuring that the final output aligns closely with user expectations.
The core focus of QFD is enhancing communication among various departments, such as marketing, design, engineering, and manufacturing, facilitating a seamless transition from concept to product launch.
The House of Quality
The House of Quality is the most widely recognized tool within the QFD method.
It serves as a visual representation of the relationship between customer requirements and the company’s ability to meet those needs.
The structure resembles a house, which is why it’s named the House of Quality.
This matrix helps teams prioritize features and functions based on customer importance ratings.
The House of Quality consists of several key components:
1. **Customer Requirements (What’s):** These are the features or qualities that customers demand.
2. **Technical Descriptors (How’s):** These represent the company’s technical response to customer requirements.
3. **Relationship Matrix:** This is the core of the House of Quality, demonstrating how each technical descriptor meets customer requirements.
4. **Competitive Benchmarking:** This section compares the company’s product against competitors to identify areas of improvement.
5. **Importance Ratings:** Reflect the priority of each customer requirement.
By systematically analyzing these elements, organizations can identify the most critical areas affecting quality and deploy their resources more efficiently.
Benefits of Implementing QFD
QFD offers numerous benefits, pivotal in producing high-quality products that resonate with customer needs.
– **Enhanced Customer Satisfaction:** By focusing on customer requirements, products are more likely to meet or exceed customer expectations, leading to increased satisfaction and loyalty.
– **Reduced Time to Market:** Clearly defined requirements and streamlined communication across departments help accelerate the product development cycle.
– **Cost Efficiency:** Identifying and addressing potential issues early in the design process reduces the need for costly modifications at later stages.
– **Improved Cross-Functional Collaboration:** QFD fosters collaboration across different teams, encouraging a unified approach to achieving project goals.
These benefits collectively contribute to producing high-caliber products while minimizing wasted resources.
Key Steps in QFD Process
Implementing QFD typically involves a series of structured steps, ensuring each crucial aspect of development is addressed systematically.
1. **Identify Customer Needs:** Use surveys, interviews, and focus groups to gather comprehensive customer insights.
2. **Translate Needs into Specifications:** Convert customer needs into measurable technical specifications.
3. **Develop the House of Quality:** Construct the House of Quality matrix to visualize the relationship between customer needs and technical descriptors.
4. **Prioritize Requirements:** Use the matrix to assign priority levels and focus on aspects with the highest impact on quality.
5. **Analyze Competitive Products:** Conduct a comparative analysis to determine strengths and weaknesses relative to competitors.
6. **Develop and Implement Solutions:** Formulate solutions to meet prioritized requirements and integrate these into product design.
7. **Review and Modify:** Regularly assess the process and make necessary adjustments based on feedback and evolving customer needs.
Through these steps, QFD ensures that the end product is precisely aligned with market demands, enhancing quality and reliability.
Challenges and Limitations of QFD
While QFD is a powerful tool, it comes with its own set of challenges that companies need to navigate.
– **Complexity:** The detailed analysis required can make QFD seem complex and time-consuming, particularly for teams unaccustomed to its structure.
– **Resource Intensive:** Implementing QFD necessitates significant input from various departments, which can strain resources if not managed properly.
– **Dependence on Accurate Data:** The success of QFD heavily relies on accurate and comprehensive data on customer needs, which can be difficult to obtain.
Despite these challenges, careful planning and a dedicated team can make QFD an invaluable part of the product development process.
Improving Quality and Reliability with QFD
For QFD to truly enhance quality and reliability, focusing on certain key points can significantly uplift the process’s effectiveness.
1. **Customer-Centric Approach:** Always prioritize understanding and fulfilling customer needs; personalization increases satisfaction and product relevance.
2. **Cross-Functional Teams:** Encourage collaboration across various departments to foster different perspectives and solutions.
3. **Continuous Feedback:** Implement a systematic approach for gathering feedback throughout the product lifecycle to make timely and relevant improvements.
4. **Training and Expertise:** Ensure that team members are well-versed in QFD techniques and understand the importance of each step in the process.
5. **Regular Updates:** As market conditions and consumer preferences change, regularly update customer requirements and technical specifications.
By integrating these practices into the QFD framework, companies can significantly enhance their ability to produce reliable, high-quality products that stand out in competitive markets.
A disciplined approach to QFD not only improves product attributes but also leads to substantial organizational growth through customer satisfaction and operational efficiency.
Incorporating key points for effective implementation can transform QFD from a mere process into a strategic advantage.
資料ダウンロード
QCD管理受発注クラウド「newji」は、受発注部門で必要なQCD管理全てを備えた、現場特化型兼クラウド型の今世紀最高の受発注管理システムとなります。
ユーザー登録
受発注業務の効率化だけでなく、システムを導入することで、コスト削減や製品・資材のステータス可視化のほか、属人化していた受発注情報の共有化による内部不正防止や統制にも役立ちます。
NEWJI DX
製造業に特化したデジタルトランスフォーメーション(DX)の実現を目指す請負開発型のコンサルティングサービスです。AI、iPaaS、および先端の技術を駆使して、製造プロセスの効率化、業務効率化、チームワーク強化、コスト削減、品質向上を実現します。このサービスは、製造業の課題を深く理解し、それに対する最適なデジタルソリューションを提供することで、企業が持続的な成長とイノベーションを達成できるようサポートします。
製造業ニュース解説
製造業、主に購買・調達部門にお勤めの方々に向けた情報を配信しております。
新任の方やベテランの方、管理職を対象とした幅広いコンテンツをご用意しております。
お問い合わせ
コストダウンが利益に直結する術だと理解していても、なかなか前に進めることができない状況。そんな時は、newjiのコストダウン自動化機能で大きく利益貢献しよう!
(β版非公開)