- お役立ち記事
- Basics of Quality Function Deployment (QFD) that new employees in the quality control department of the electrical equipment manufacturing industry should learn
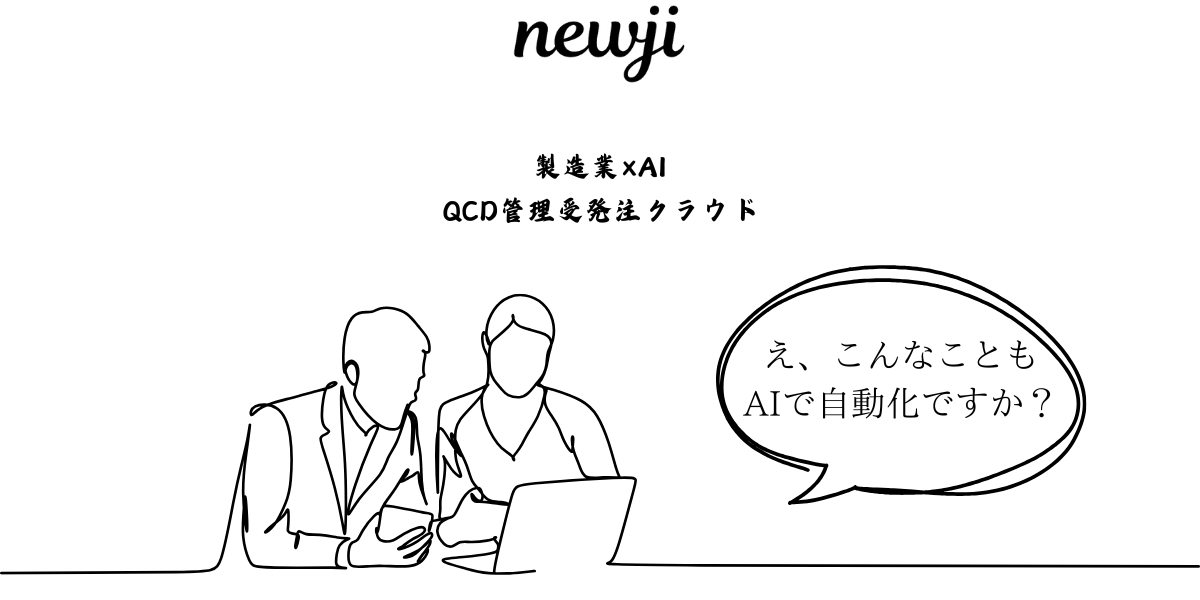
Basics of Quality Function Deployment (QFD) that new employees in the quality control department of the electrical equipment manufacturing industry should learn
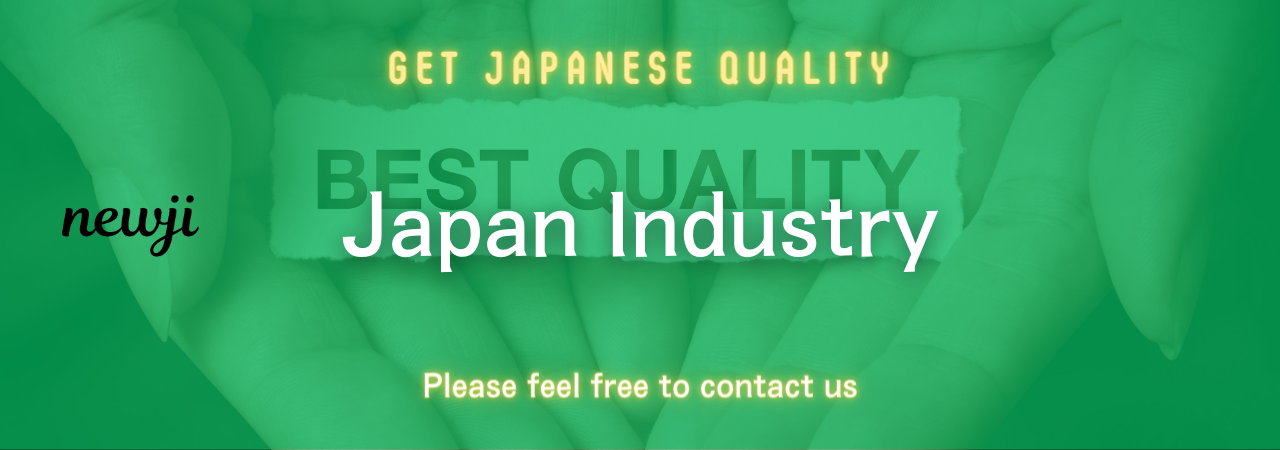
目次
Introduction to Quality Function Deployment (QFD)
Quality Function Deployment, commonly known as QFD, is a systematic approach used in the electrical equipment manufacturing industry to ensure customer needs and expectations are met in product design and development.
As a new employee in the quality control department, understanding QFD is essential as it’s a key tool that translates customer requirements into final product specifications.
This process ensures that every stage of production is aligned with what the customer values, significantly enhancing customer satisfaction and product quality.
The Origin and Importance of QFD
QFD was developed in Japan in the late 1960s by Yoji Akao, aiming to improve product quality by integrating customer feedback directly into the design and production processes.
In an industry as dynamic and competitive as electrical equipment manufacturing, integrating QFD into your workflow can lead to better quality products and higher customer satisfaction.
QFD helps in identifying the voice of the customer (VoC) and translating it into company-specific requirements.
This direct link between customer needs and product development ensures that resources are efficiently allocated to creating products that truly matter to the end-user.
The Phases of QFD
The QFD process can be broken down into several phases, each focusing on a different aspect of product development.
1. Product Planning
During this phase, the primary goal is to capture customer needs through various means such as surveys, interviews, and focus groups.
Data collected is often organized into a planning matrix known as the House of Quality.
This matrix visually represents customer desires and the company’s ability to meet those expectations.
2. Product Design
Once customer needs are pinpointed, the next phase involves converting these needs into specific product features and specifications.
Design engineers work closely with quality control professionals to ensure that the design is feasible and meets customer demands.
This phase is crucial for aligning product specs with customer expectations and technological possibilities.
3. Process Planning
Here, the focus shifts from product design to the processes involved in manufacturing.
The aim is to create a blueprint that describes every step of the production, ensuring that each stage supports the desired quality attributes.
It involves creating process charts and identifying critical operations and parameters.
4. Production Planning
The final phase ensures that the production process maintains the quality standards set in the initial phases.
Feedback loops and quality checks are established to detect any deviations early, ensuring a smooth transition from concept to finished product.
It ensures that all parts of the production chain contribute to the overall quality goals.
The Benefits of Implementing QFD
Implementing QFD in your quality control operations brings numerous benefits that can significantly impact your organization’s overall performance.
Improved Customer Satisfaction
By directly incorporating customer feedback into every aspect of product development, QFD helps ensure that the final product meets or exceeds customer expectations.
Streamlined Communication
QFD requires collaboration across various departments—from marketing to design and manufacturing.
This cross-functional teamwork improves communication, reduces misunderstandings, and aligns all parties towards a common goal.
Resource Efficiency
Identifying customer priorities early in the process enables the team to focus resources on what truly matters, eliminating unnecessary expenditures and optimizing resource allocation.
Reduced Time to Market
By addressing potential design flaws and customer dissatisfaction early, QFD can help speed up the development process.
It minimizes the risk of time-consuming revisions later on, ensuring quicker transitions from concept to market-ready product.
Challenges and Considerations in QFD
While QFD offers substantial benefits, it is not without challenges.
New employees need to be aware of these to effectively navigate the process.
Complexity and Time-Consumption
The QFD process can be complex, demanding time and commitment from all involved.
Proper training and a structured approach are essential to manage this complexity efficiently.
Data Accuracy and Relevance
Gathering accurate customer data is crucial in maintaining the effectiveness of the QFD process.
Inaccurate or outdated information can lead to misguided product specifications and dissatisfaction.
Cross-Department Collaboration
Successful QFD implementation requires seamless collaboration across various departments.
This can sometimes be challenging, but fostering a culture of communication and cooperation can facilitate smoother interactions.
Conclusion
As a new member of the quality control department in the electrical equipment manufacturing industry, mastering QFD is a critical skill.
Its role in aligning customer needs with product development is invaluable, driving higher customer satisfaction and product quality.
By understanding the phases of QFD, recognizing its benefits, and acknowledging the challenges, you can contribute to more effective and efficient quality control processes.
Be patient as you learn the intricacies of QFD, and take advantage of any training resources available.
Your efforts will pay off in producing products that not only meet but exceed customer expectations, strengthening your company’s position in the market.
資料ダウンロード
QCD調達購買管理クラウド「newji」は、調達購買部門で必要なQCD管理全てを備えた、現場特化型兼クラウド型の今世紀最高の購買管理システムとなります。
ユーザー登録
調達購買業務の効率化だけでなく、システムを導入することで、コスト削減や製品・資材のステータス可視化のほか、属人化していた購買情報の共有化による内部不正防止や統制にも役立ちます。
NEWJI DX
製造業に特化したデジタルトランスフォーメーション(DX)の実現を目指す請負開発型のコンサルティングサービスです。AI、iPaaS、および先端の技術を駆使して、製造プロセスの効率化、業務効率化、チームワーク強化、コスト削減、品質向上を実現します。このサービスは、製造業の課題を深く理解し、それに対する最適なデジタルソリューションを提供することで、企業が持続的な成長とイノベーションを達成できるようサポートします。
オンライン講座
製造業、主に購買・調達部門にお勤めの方々に向けた情報を配信しております。
新任の方やベテランの方、管理職を対象とした幅広いコンテンツをご用意しております。
お問い合わせ
コストダウンが利益に直結する術だと理解していても、なかなか前に進めることができない状況。そんな時は、newjiのコストダウン自動化機能で大きく利益貢献しよう!
(Β版非公開)