- お役立ち記事
- Basics of resistance spot welding technology and application to aluminum dissimilar metal welding
月間77,185名の
製造業ご担当者様が閲覧しています*
*2025年2月28日現在のGoogle Analyticsのデータより
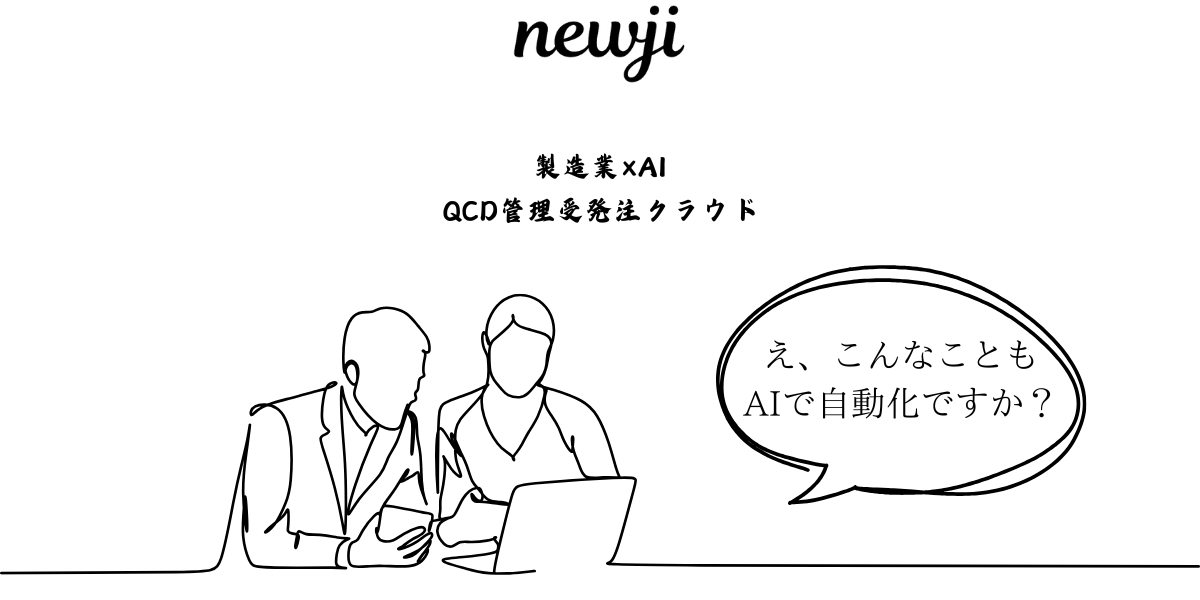
Basics of resistance spot welding technology and application to aluminum dissimilar metal welding
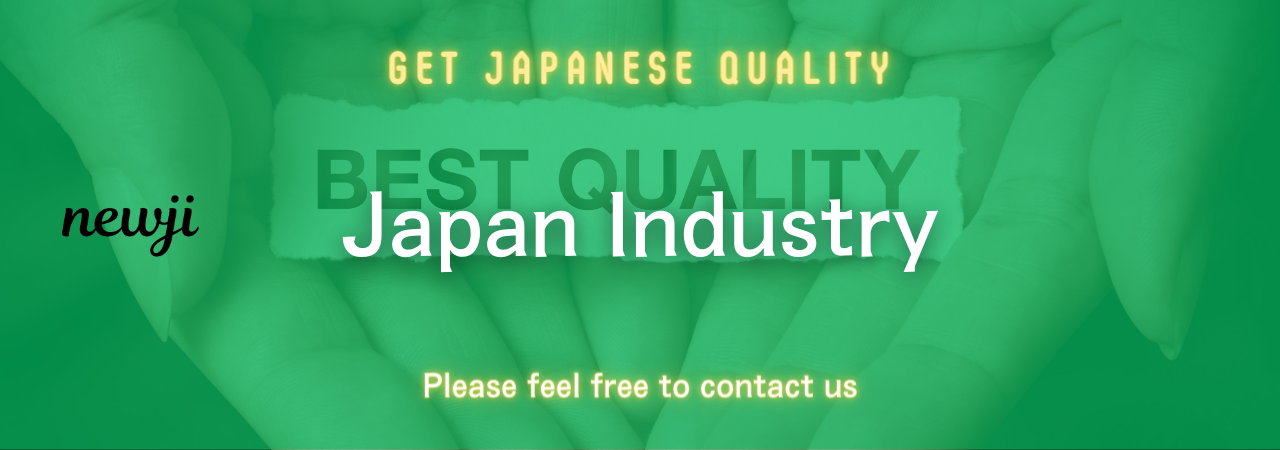
目次
Understanding Resistance Spot Welding
Resistance spot welding (RSW) is a popular welding technique used in manufacturing, known for its efficiency in joining metal sheets.
This process involves the fusion of metal surfaces by applying heat generated from the resistance to electric current flow.
The name “spot welding” comes from the fact that it welds at specific points rather than along a continuous seam.
The Process of Spot Welding
The RSW process begins with sheet metal being placed between two electrodes.
A high electric current is passed through these electrodes and subsequently through the metal, generating heat.
This heat, combined with the pressure exerted by the electrodes, melts the metal at the contact point.
Once the current is stopped, the molten metal solidifies, forming a weld “nugget” that holds the sheets together.
Advantages of Resistance Spot Welding
One of the primary advantages of resistance spot welding is its speed and efficiency.
The process can be automated, making it suitable for high-volume production environments like the automotive industry.
Another benefit is the ability to weld without additional filler materials, which reduces costs and simplifies the process.
Additionally, spot welding creates minimal distortion, maintaining the integrity and shape of the assembled components.
With the right equipment, it’s possible to make consistent and repeatable welds, ensuring high-quality joints.
Challenges with Aluminum Welding
Despite being effective with steel sheets, resistance spot welding faces challenges when it comes to aluminum dissimilar metal welding.
Aluminum is known for its high thermal and electrical conductivity, making it difficult to generate the necessary heat for welding using traditional RSW methods.
Furthermore, aluminum has a lower melting point compared to steel and forms an oxide layer that can impact weld quality.
These factors can lead to issues such as inconsistent welds and increased electrode wear, posing challenges for manufacturers aiming to use aluminum in their projects.
Spot Welding Techniques for Aluminum
Several adaptations and techniques have been developed to address the challenges of welding aluminum.
Increasing the amount of electrical current and pressure applied during welding can help achieve the necessary heat generation.
This approach, however, requires specialized equipment capable of handling the increased current demands.
Another method involves the use of electrode materials specifically designed to combat the higher wear rates experienced when welding aluminum.
These materials can prolong the life of the electrodes and ensure more stable weld quality over time.
Some manufacturers opt for pre-treating the aluminum surface to remove the oxide layer.
This step ensures a cleaner interface for welding, leading to stronger and more reliable joints.
Applications of Spot Welding in Industry
Resistance spot welding is widely used across various industries, thanks to its efficiency and cost-effectiveness.
In the automotive industry, it is essential for assembling vehicle bodies, contributing to the lightweight design of modern cars by allowing the use of aluminum components.
The aerospace industry also benefits from resistance spot welding.
Aircraft manufacturers rely on this technique to create both structural and non-structural components, prioritizing joint strength and reliability.
The Rise of Dissimilar Metal Welding
With growing demands for innovative, lightweight structures, manufacturers often need to join dissimilar metals, such as aluminum with steel.
This need has driven advancements in resistance spot welding technology to accommodate the unique properties of different metals.
One technique to facilitate dissimilar metal welding involves using interlayers or transition joints.
These components are placed between the two metals to create a more compatible interface, reducing the mismatch in thermal and electric properties.
Such strategies enhance the overall quality and durability of the welds.
The Future of Resistance Spot Welding
As industries continue to innovate and evolve, resistance spot welding technology must advance accordingly.
Research and development efforts focus on improving welding equipment and techniques to handle the challenges posed by dissimilar metals.
Emerging trends in digitalization and automation also promise to enhance the resistance spot welding process.
Smart welding systems equipped with sensors and real-time monitoring capabilities can improve quality control and reduce the risk of defects.
Such technologies enable better process optimization, ensuring consistent and reliable welds.
Conclusion
Resistance spot welding remains a versatile and essential technique in manufacturing, particularly for applications requiring speed and efficiency.
While aluminum dissimilar metal welding presents challenges, advances in technology and materials hold promise for overcoming these barriers.
By continuing to innovate and adapt, industries can fully leverage the benefits of resistance spot welding, paving the way for future developments in manufacturing.
資料ダウンロード
QCD管理受発注クラウド「newji」は、受発注部門で必要なQCD管理全てを備えた、現場特化型兼クラウド型の今世紀最高の受発注管理システムとなります。
ユーザー登録
受発注業務の効率化だけでなく、システムを導入することで、コスト削減や製品・資材のステータス可視化のほか、属人化していた受発注情報の共有化による内部不正防止や統制にも役立ちます。
NEWJI DX
製造業に特化したデジタルトランスフォーメーション(DX)の実現を目指す請負開発型のコンサルティングサービスです。AI、iPaaS、および先端の技術を駆使して、製造プロセスの効率化、業務効率化、チームワーク強化、コスト削減、品質向上を実現します。このサービスは、製造業の課題を深く理解し、それに対する最適なデジタルソリューションを提供することで、企業が持続的な成長とイノベーションを達成できるようサポートします。
製造業ニュース解説
製造業、主に購買・調達部門にお勤めの方々に向けた情報を配信しております。
新任の方やベテランの方、管理職を対象とした幅広いコンテンツをご用意しております。
お問い合わせ
コストダウンが利益に直結する術だと理解していても、なかなか前に進めることができない状況。そんな時は、newjiのコストダウン自動化機能で大きく利益貢献しよう!
(β版非公開)