- お役立ち記事
- Basics of reverse engineering using 3D scanning that new employees in the design department of the precision machinery industry should learn
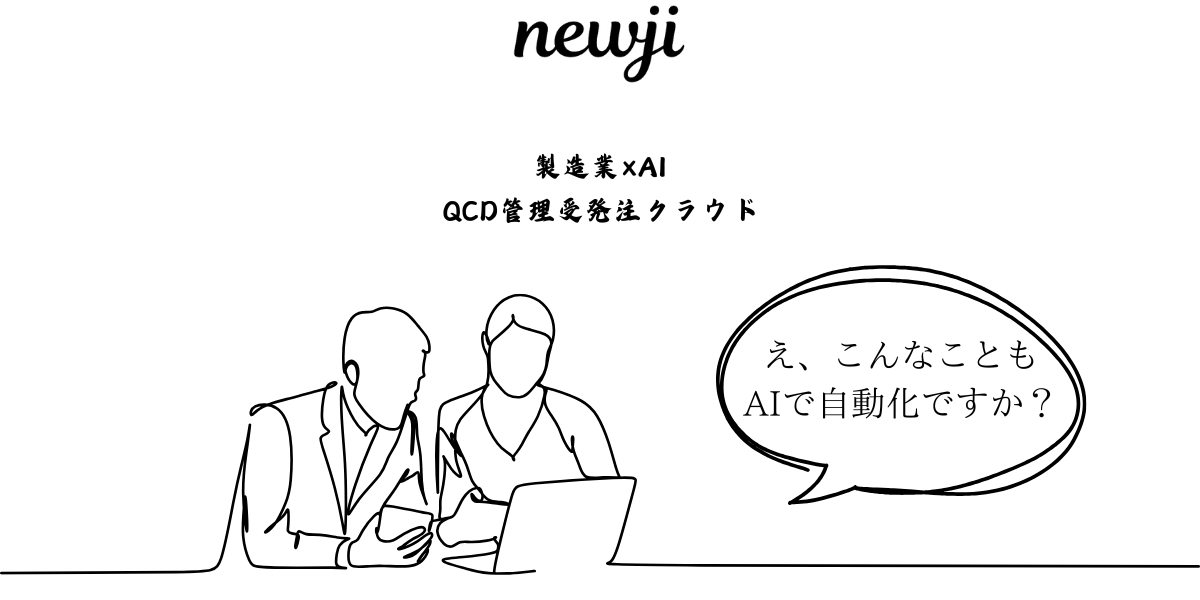
Basics of reverse engineering using 3D scanning that new employees in the design department of the precision machinery industry should learn
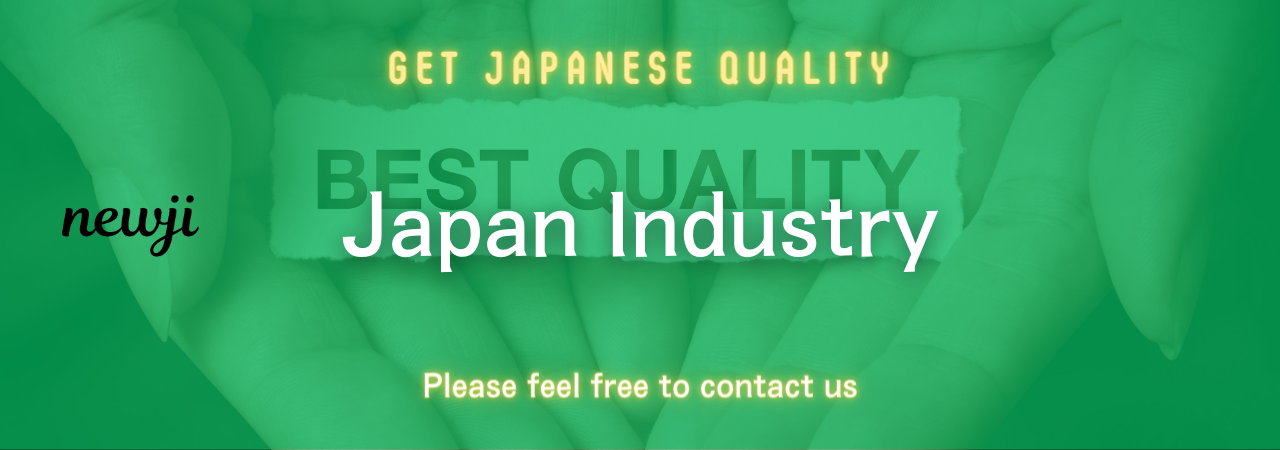
目次
Introduction to Reverse Engineering
Reverse engineering is a fascinating process that involves deconstructing an object to understand its design, function, and how it was manufactured.
In the precision machinery industry, 3D scanning plays a significant role in reverse engineering.
Understanding the basics of reverse engineering can empower new employees in the design department to contribute innovatively and effectively to their teams.
What is 3D Scanning?
3D scanning is a technology that captures the shape and size of a physical object by collecting data on its surface.
This data is then used to create a digital 3D model.
The process extends beyond simple measurements, providing detailed representations of an object for further analysis and design.
Types of 3D Scanners
Several types of 3D scanners are available, each offering different capabilities.
Common types include laser scanners, structured light scanners, and photogrammetry.
– **Laser Scanners:** These use laser beams to measure the distance between the scanner and the object, creating a point cloud that represents the object’s surface.
– **Structured Light Scanners:** These project light patterns onto the object and capture the deformation of these patterns to determine the object’s shape.
– **Photogrammetry:** This method uses photos taken from various angles to reconstruct a digital model, relying heavily on powerful software to process the images.
The Role of 3D Scanning in Reverse Engineering
In the context of reverse engineering, 3D scanning is used to create accurate digital replicas of physical parts.
These replicas can be analyzed and modified to improve the design or to reproduce parts without existing blueprints or CAD models.
Benefits of Using 3D Scanning
3D scanning offers multiple benefits in reverse engineering:
– **Accuracy:** Captures precise details of complex geometries, which are often difficult to measure manually.
– **Efficiency:** Reduces the time needed to gather data compared to traditional measurement methods, speeding up the reverse engineering process.
– **Versatility:** Applicable to a wide range of materials and sizes, from small precision components to large machinery parts.
Steps in the Reverse Engineering Process
Reverse engineering with 3D scanning involves several key steps:
Step 1: Initial Planning
Before starting, it’s crucial to define the purpose of reverse engineering.
Be it product enhancement, replication, or performance analysis, having a clear goal guides the entire process.
Step 2: Scanning the Object
Choose the appropriate 3D scanner based on the object’s size, material, and complexity.
The scanning phase consists of capturing the object from multiple angles, ensuring that all surfaces are scanned for a complete model.
Step 3: Creating a Digital Model
The data gathered from the scan is processed using specialized software to produce a detailed 3D model.
This step may require cleaning up the data, aligning different scans, and reconstructing any missing parts of the model.
Step 4: Analyzing and Redesigning
With a digital model in place, engineers can analyze the design to examine the object’s structure, materials, and potential points of failure.
If redesigning is necessary, this 3D model is used as a foundation, allowing modifications or enhancements to be made digitally.
Step 5: Producing the Part
Finally, the updated or replicated design is manufactured, often using CNC machining, 3D printing, or other fabrication methods.
Applications of Reverse Engineering in Precision Machinery
Reverse engineering serves numerous purposes in precision machinery:
– **Legacy Part Reproduction:** Enables the production of components that lack existing designs, ensuring continued functionality of machinery and devices.
– **Quality Control:** Allows for comparison between manufactured parts and original designs to ensure adherence to specifications.
– **Product Improvement:** Reveals insights that lead to design enhancements and improved performance.
Challenges in Reverse Engineering
While powerful, reverse engineering with 3D scanning also presents challenges:
– **Complex Geometries:** Scanning intricate parts can be difficult, requiring high-resolution scanners and advanced software.
– **Data Handling:** Managing and processing large sets of data can be computationally demanding.
– **Cost:** Initial setup costs for scanners and software can be high, though they are generally offset by the savings in time and increased accuracy.
Conclusion
Understanding the basics of reverse engineering using 3D scanning can significantly benefit new employees in the design department of the precision machinery industry.
This knowledge enables them to participate actively in improving product designs, replicating existing parts, and ensuring quality control.
While challenges exist, the benefits of 3D scanning make it an indispensable tool in modern design and engineering.
With continued practice and learning, new employees can harness this technology to make meaningful contributions in their field.
資料ダウンロード
QCD調達購買管理クラウド「newji」は、調達購買部門で必要なQCD管理全てを備えた、現場特化型兼クラウド型の今世紀最高の購買管理システムとなります。
ユーザー登録
調達購買業務の効率化だけでなく、システムを導入することで、コスト削減や製品・資材のステータス可視化のほか、属人化していた購買情報の共有化による内部不正防止や統制にも役立ちます。
NEWJI DX
製造業に特化したデジタルトランスフォーメーション(DX)の実現を目指す請負開発型のコンサルティングサービスです。AI、iPaaS、および先端の技術を駆使して、製造プロセスの効率化、業務効率化、チームワーク強化、コスト削減、品質向上を実現します。このサービスは、製造業の課題を深く理解し、それに対する最適なデジタルソリューションを提供することで、企業が持続的な成長とイノベーションを達成できるようサポートします。
オンライン講座
製造業、主に購買・調達部門にお勤めの方々に向けた情報を配信しております。
新任の方やベテランの方、管理職を対象とした幅広いコンテンツをご用意しております。
お問い合わせ
コストダウンが利益に直結する術だと理解していても、なかなか前に進めることができない状況。そんな時は、newjiのコストダウン自動化機能で大きく利益貢献しよう!
(Β版非公開)