- お役立ち記事
- Basics of risk analysis methods at manufacturing sites and application to safety measures
月間76,176名の
製造業ご担当者様が閲覧しています*
*2025年3月31日現在のGoogle Analyticsのデータより
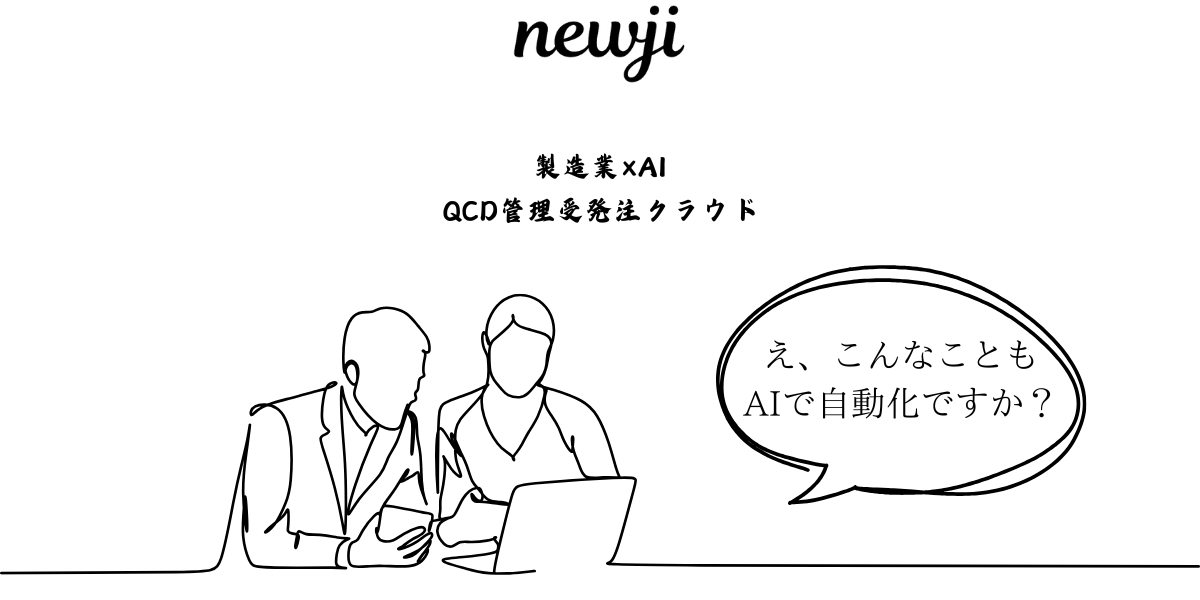
Basics of risk analysis methods at manufacturing sites and application to safety measures
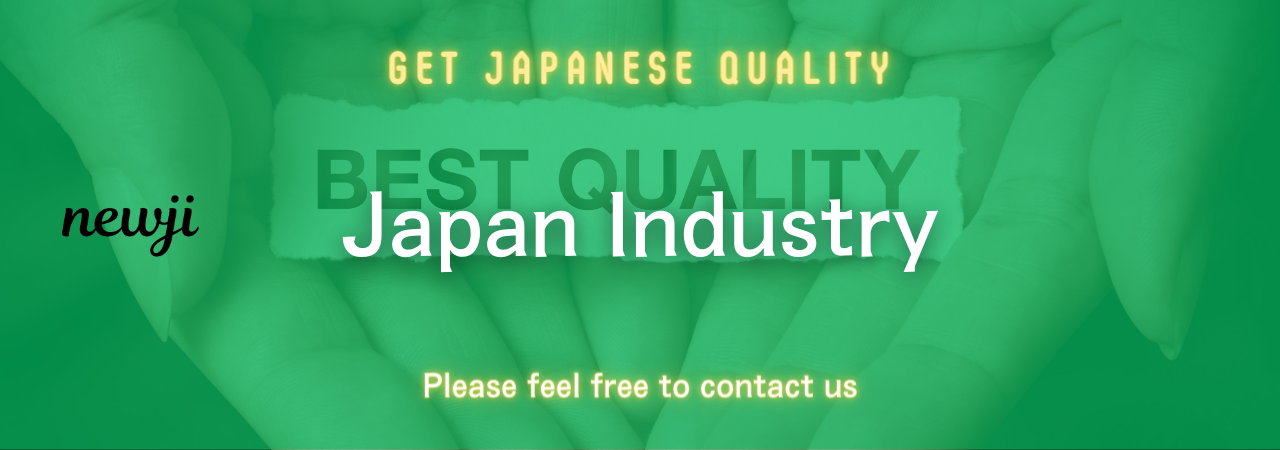
目次
Understanding Risk Analysis in Manufacturing
Risk analysis is an essential process in manufacturing, focusing on identifying, assessing, and managing potential risks that could negatively impact production and safety.
By understanding the basics of risk analysis methods, manufacturers can implement effective safety measures to protect both workers and equipment.
The primary goal of risk analysis is to minimize hazards and prevent accidents or disruptions within the manufacturing processes.
In the modern production environment, where complex machinery and intricate processes are prevalent, risk analysis is vital for sustaining operational efficiency and safety.
Common Risk Analysis Methods
There are several risk analysis methods used in manufacturing, each serving specific purposes and providing different insights.
Hazard Identification and Risk Assessment (HIRA)
HIRA is a comprehensive method used to identify potential hazards in a manufacturing setting.
This involves examining every aspect of a manufacturing process to pinpoint areas where hazards may arise.
Once these hazards are identified, they are evaluated based on their likelihood and potential impact.
The findings are then used to develop strategies for mitigating or eliminating the risks.
Failure Mode and Effects Analysis (FMEA)
FMEA is a systematic method aimed at identifying where and how a process might fail.
It involves analyzing each step of a process and predicting points where failures could occur, as well as the potential effects these failures might have.
By doing so, teams can prioritize issues that need immediate attention and develop solutions to prevent failures before they happen.
Fault Tree Analysis (FTA)
FTA is a deductive risk analysis technique used to identify the root causes of undesirable events.
Through constructing a fault tree diagram, individuals can trace the pathways that lead to system failures.
FTA helps in visualizing the connections between different causes and determining which combinations are most likely to lead to a failure.
Preliminary Hazard Analysis (PHA)
PHA is employed in the early stages of process design to foresee any potential hazards.
It doesn’t delve into specifics but provides an overview to ensure fundamental risks are addressed.
By carrying out a PHA during the planning phase, manufacturers can implement changes early on, reducing the potential for hazards during production.
Application of Risk Analysis for Safety Measures
Once risks have been identified and assessed, the next step is to apply appropriate safety measures to mitigate these risks.
Here are some strategies often used in manufacturing:
Implementing Engineering Controls
Engineering controls involve designing or modifying equipment to eliminate or reduce exposure to hazards.
Examples include installing machine guards, improving ventilation systems, and incorporating automation to limit human contact with dangerous equipment.
Establishing Administrative Controls
Administrative controls include changes in workplace policies or procedures to reduce the risk of incidents.
This could involve limiting access to hazardous areas, rotating staff to minimize exposure, or providing specialized training for high-risk tasks.
Personal Protective Equipment (PPE)
PPE serves as the last line of defense against manufacturing hazards.
By supplying workers with the necessary gear such as gloves, helmets, and protective eyewear, employers can further diminish the risk of injuries or accidents.
Regular Safety Training
Continuous training for employees is crucial in building a strong safety culture within a manufacturing plant.
Regular workshops and drills ensure that workers are well-versed in safety protocols and emergency procedures, enabling them to respond effectively in case of an unexpected event.
The Importance of Ongoing Risk Analysis
Risk analysis is not a one-time effort but a continuous process.
Manufacturing environments are dynamic, and so are the risks associated with them.
Technological advancements and changes in production processes can introduce new hazards.
Therefore, regular risk assessments are necessary to keep safety measures up-to-date and effective.
In addition, ongoing risk analysis allows manufacturers to evaluate the effectiveness of their safety measures.
By collecting data on incidents and near-misses, organizations can refine their strategies and ensure that their risk management plans are efficient and relevant to the current production environment.
Conclusion
Understanding and implementing risk analysis methods are critical to ensuring safety at manufacturing sites.
With techniques like HIRA, FMEA, FTA, and PHA, manufacturers can identify and address potential hazards before they manifest into significant issues.
Combining these methods with engineering and administrative controls, PPE, and continuous training ensures a comprehensive approach to safety.
Ultimately, a commitment to ongoing risk analysis and safety enhancements not only protects workers and equipment but also contributes to sustainable and efficient manufacturing operations.
資料ダウンロード
QCD管理受発注クラウド「newji」は、受発注部門で必要なQCD管理全てを備えた、現場特化型兼クラウド型の今世紀最高の受発注管理システムとなります。
ユーザー登録
受発注業務の効率化だけでなく、システムを導入することで、コスト削減や製品・資材のステータス可視化のほか、属人化していた受発注情報の共有化による内部不正防止や統制にも役立ちます。
NEWJI DX
製造業に特化したデジタルトランスフォーメーション(DX)の実現を目指す請負開発型のコンサルティングサービスです。AI、iPaaS、および先端の技術を駆使して、製造プロセスの効率化、業務効率化、チームワーク強化、コスト削減、品質向上を実現します。このサービスは、製造業の課題を深く理解し、それに対する最適なデジタルソリューションを提供することで、企業が持続的な成長とイノベーションを達成できるようサポートします。
製造業ニュース解説
製造業、主に購買・調達部門にお勤めの方々に向けた情報を配信しております。
新任の方やベテランの方、管理職を対象とした幅広いコンテンツをご用意しております。
お問い合わせ
コストダウンが利益に直結する術だと理解していても、なかなか前に進めることができない状況。そんな時は、newjiのコストダウン自動化機能で大きく利益貢献しよう!
(β版非公開)