- お役立ち記事
- Basics of safety design methods and risk reduction that mid-level employees in equipment technology departments should know
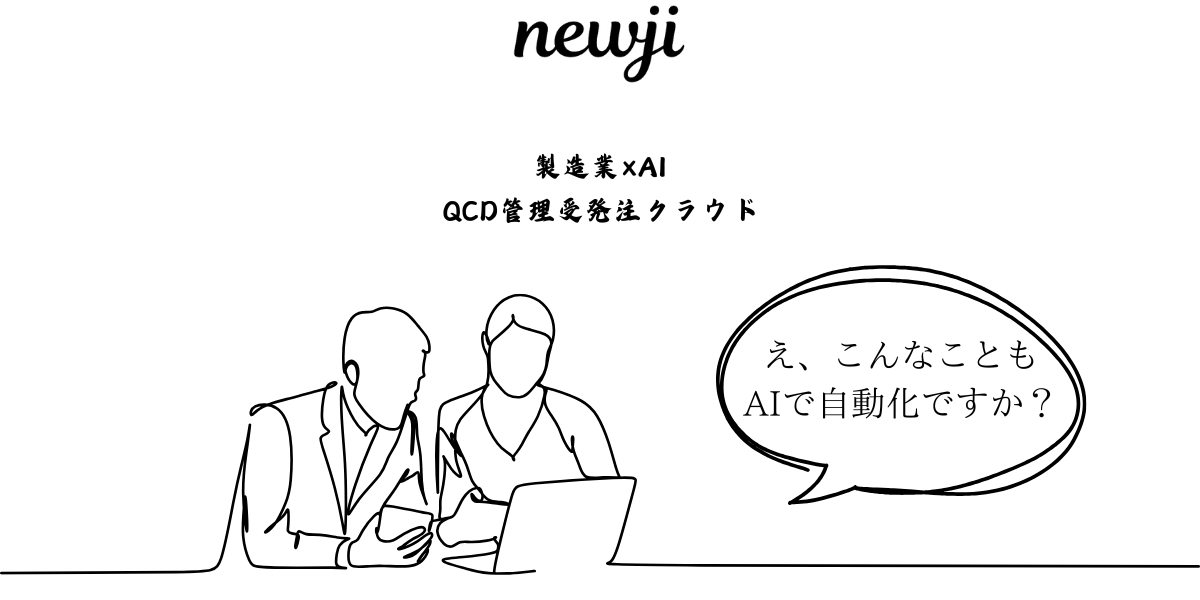
Basics of safety design methods and risk reduction that mid-level employees in equipment technology departments should know
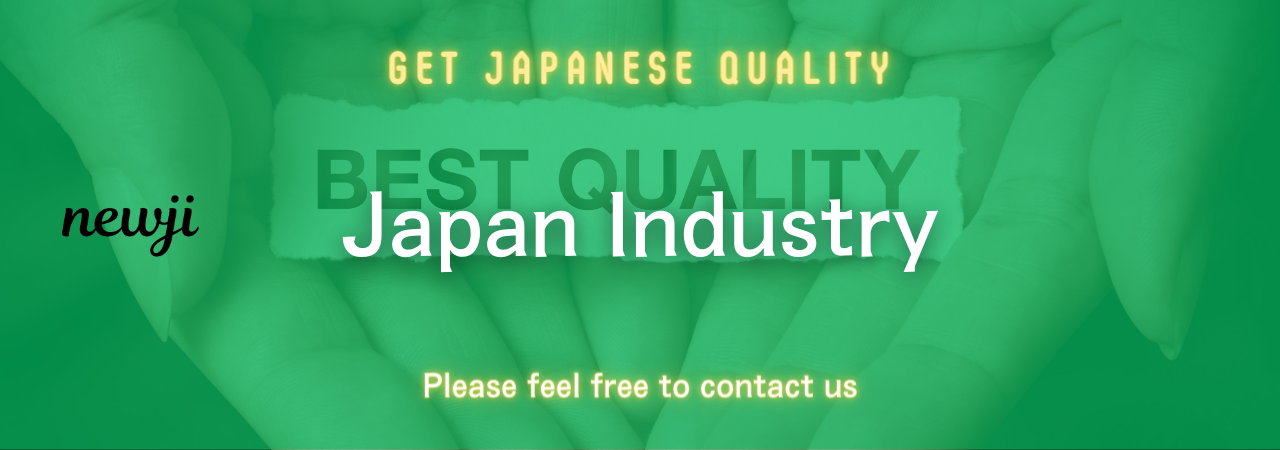
目次
Understanding Safety Design in Equipment Technology
Safety design is an essential aspect of engineering, especially in equipment technology.
It ensures that machines and devices are safe for use by minimizing risks and preventing accidents.
For mid-level employees in equipment technology departments, understanding the basics of safety design is crucial.
This knowledge not only improves workplace safety but also enhances the quality and reliability of the equipment.
The Importance of Safety Design
Incorporating safety design from the beginning of the equipment development process is vital.
It helps identify potential hazards and address them before the equipment goes into production.
The main objective is to protect users, operators, and the environment from harm.
Furthermore, safety design can lead to cost savings by reducing accidents and liability issues.
Companies that prioritize safety are also more likely to gain a competitive edge.
They can reduce downtime, enhance employee satisfaction, and build a reputation for reliability.
Key Principles of Safety Design
Several key principles guide safety design in equipment technology.
These principles aim to prevent accidents and minimize risks associated with equipment use.
Identify Hazards
The first step in safety design is identifying potential hazards associated with the equipment.
Hazards can be mechanical, electrical, thermal, or chemical.
It’s important to conduct a thorough assessment to uncover these risks early in the design phase.
Risk Assessment
Once hazards are identified, the next step is to assess the risk associated with each hazard.
Risk assessment involves evaluating the likelihood of an accident occurring and its potential consequences.
This helps prioritize safety measures and determine which risks need the most attention.
Implement Safety Measures
Based on the risk assessment, safety measures should be implemented to minimize or eliminate risks.
These can include engineering controls, such as adding protective barriers or using safer materials.
Administrative controls, like training programs and safety procedures, are also crucial.
Regular Testing and Maintenance
Safety design is not a one-time process.
It requires continuous monitoring, testing, and maintenance to ensure equipment remains safe over time.
Regular inspections and updates are necessary to address new risks and improve safety measures.
Risk Reduction Strategies
Reducing risk involves a systematic approach to address potential hazards and ensure safety.
Here are some effective risk reduction strategies.
Incorporate Safety Features in Design
One of the most effective ways to reduce risk is by incorporating safety features directly into the equipment design.
This might include automatic shutdown systems, emergency stop buttons, and effective alarm systems.
Conduct Failure Mode and Effects Analysis (FMEA)
FMEA is a step-by-step approach for identifying all possible failures in a design, manufacturing, or assembly process.
It helps predict the impacts of potential failures and guides design enhancements to prevent them.
Promote a Safety Culture
Developing a safety-focused culture within the organization is key.
This involves training employees on safety protocols and encouraging them to report hazards.
Management should actively support safety initiatives and incorporate safety goals into performance evaluations.
Utilize Personal Protective Equipment (PPE)
While engineering controls are the first line of defense, PPE is essential when hazards cannot be eliminated.
Ensuring that employees have access to and use appropriate PPE can significantly reduce injury risks.
Evaluating the Effectiveness of Safety Design
Measuring the effectiveness of safety design is necessary to ensure that safety goals are being met.
This involves regular review and analysis of incident reports, safety audits, and employee feedback.
Continuous improvement is key, making adjustments and updates as new safety technologies and methods emerge.
Benchmarking and Standards
Adopting industry benchmarks and standards can help evaluate safety performance.
These provide guidelines and best practices for safety design, offering metrics for comparison.
Feedback and Improvement
Engaging with employees to gather feedback on safety measures can provide valuable insights.
This information can be used to improve existing safety procedures and address any gaps.
The Role of Technology in Safety Design
Technology plays a crucial role in enhancing safety design in equipment technology.
New advancements contribute to more effective and efficient safety solutions.
Integration of Smart Technologies
Smart technologies, such as IoT devices, enable real-time monitoring of equipment.
They provide data that can be used to predict failures and alert operators to potential hazards.
Computer-Aided Design (CAD) Software
CAD software aids in creating detailed models of equipment, helping to identify design flaws before manufacturing.
It allows for the simulation of different scenarios, testing safety features without physical prototypes.
Augmented Reality (AR) and Virtual Reality (VR)
AR and VR are being utilized for training purposes, allowing employees to practice safety procedures in a controlled virtual environment.
These technologies help reinforce safety knowledge and improve response times in real situations.
Understanding and implementing safety design methods are vital for mid-level employees in equipment technology departments.
By focusing on hazard identification, risk assessment, safety measures, and the integration of technology, they can significantly contribute to safer equipment and work environments.
This not only benefits the organization but also protects the well-being of its employees and end-users.
資料ダウンロード
QCD調達購買管理クラウド「newji」は、調達購買部門で必要なQCD管理全てを備えた、現場特化型兼クラウド型の今世紀最高の購買管理システムとなります。
ユーザー登録
調達購買業務の効率化だけでなく、システムを導入することで、コスト削減や製品・資材のステータス可視化のほか、属人化していた購買情報の共有化による内部不正防止や統制にも役立ちます。
NEWJI DX
製造業に特化したデジタルトランスフォーメーション(DX)の実現を目指す請負開発型のコンサルティングサービスです。AI、iPaaS、および先端の技術を駆使して、製造プロセスの効率化、業務効率化、チームワーク強化、コスト削減、品質向上を実現します。このサービスは、製造業の課題を深く理解し、それに対する最適なデジタルソリューションを提供することで、企業が持続的な成長とイノベーションを達成できるようサポートします。
オンライン講座
製造業、主に購買・調達部門にお勤めの方々に向けた情報を配信しております。
新任の方やベテランの方、管理職を対象とした幅広いコンテンツをご用意しております。
お問い合わせ
コストダウンが利益に直結する術だと理解していても、なかなか前に進めることができない状況。そんな時は、newjiのコストダウン自動化機能で大きく利益貢献しよう!
(Β版非公開)