- お役立ち記事
- Basics of seal gasket packing technology and examples of leakage prevention
月間77,185名の
製造業ご担当者様が閲覧しています*
*2025年2月28日現在のGoogle Analyticsのデータより
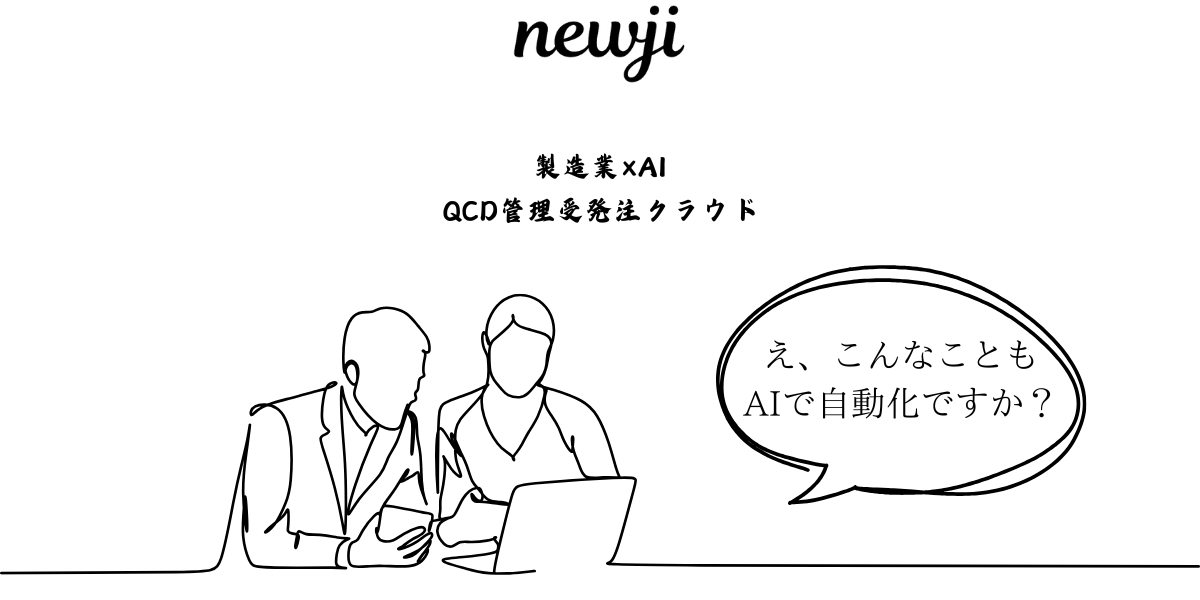
Basics of seal gasket packing technology and examples of leakage prevention
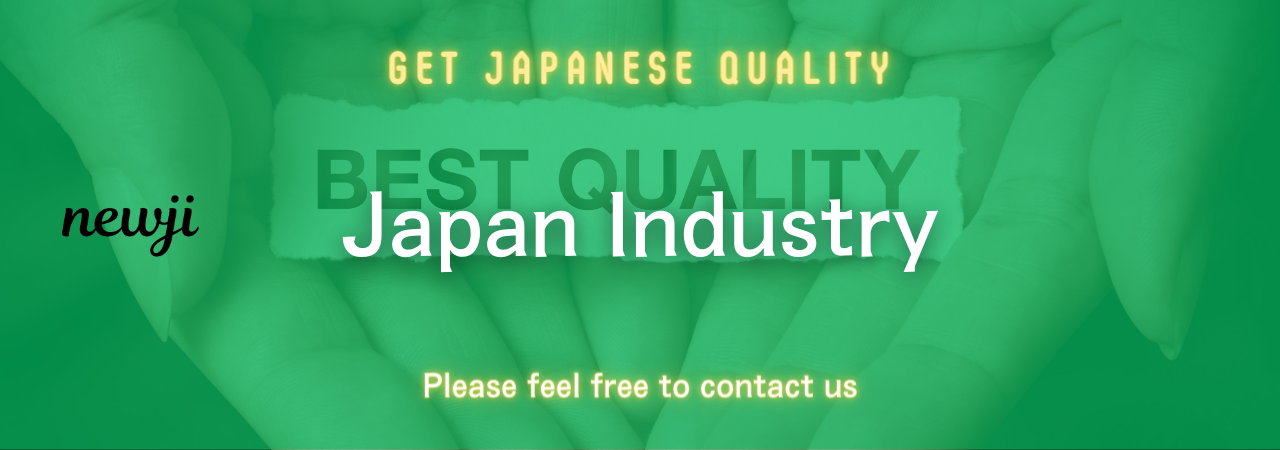
目次
Understanding Seal Gasket Packing Technology
Seal gasket packing technology plays a crucial role in a variety of industries, particularly those that involve fluid dynamics, pressure systems, and temperature extremes.
Gaskets are mechanical seals that fill the space between two or more mating surfaces, generally to prevent leakage from or into the joined objects while under compression.
These vital components ensure the integrity and efficiency of machinery by preventing leaks and protecting against external contaminants.
The technology behind seal gaskets is incredibly diverse, incorporating various materials and designs to meet the specific needs of an application.
From metal and rubber gaskets to complex composite materials, each type has its unique properties and benefits.
Understanding the basics of these technologies helps in selecting the right gasket for the job, thereby preventing leakage and maintaining system efficiency.
Different Types of Gaskets
There are several types of gaskets available, each designed to cater to specific conditions and requirements.
The three main categories include:
1. **Metallic Gaskets**: These are made of metals such as stainless steel, iron, or copper. They are ideal for high-pressure and high-temperature applications. Their strength and durability make them suitable for use in industries such as oil and gas, chemical processing, and power generation. Examples include spiral wound gaskets and ring type joints.
2. **Non-Metallic Gaskets**: These gaskets are made from materials like rubber, PTFE, or graphite. Non-metallic gaskets are commonly used in applications involving lower temperatures and pressures. They provide excellent flexibility and compressibility, making them ideal for water systems, food processing equipment, and HVAC systems.
3. **Composite Gaskets**: This category combines metallic and non-metallic materials. Composite gaskets are designed to offer the benefits of both materials, providing a balance of strength, flexibility, and chemical compatibility. They are suitable for applications that face variable temperature and pressure conditions.
Key Considerations in Gasket Selection
Choosing the appropriate gasket for an application involves considering various factors to ensure effective sealing and performance. Key considerations include:
– **Temperature and Pressure**: Understanding the operational conditions of the system is essential. Different materials have different tolerance ranges for temperature and pressure. Selecting a gasket that can withstand these conditions will prevent failures and potential leaks.
– **Chemical Compatibility**: The gasket material must be compatible with the substances it will contact. For instance, certain chemicals might degrade rubber gaskets, so a more resistant material would be necessary.
– **Environmental Impact**: Consider factors like exposure to sunlight, ozone, or other environmental elements that could affect the gasket material. Materials with high UV resistance may be necessary for outdoor applications.
– **Physical Properties**: This includes the size, shape, and thickness of the gasket, which must align with the dimensions of the equipment. Proper fit and compression ensure an effective seal.
Examples of Leakage Prevention with Gaskets
Effective gasket implementation can significantly minimize the risk of leakage. Here are some examples of how different gaskets prevent leakage across various applications:
Industrial Piping Systems
In industrial piping, spiral wound gaskets are often used due to their ability to maintain a tight seal under fluctuating pressures and temperatures.
They are effective in sealing pipe flange connections, ensuring that fluids do not escape the piping system.
Their resilient design allows them to handle the stress of expansion and contraction, common in metallic pipes used in chemical and petrochemical industries.
Automotive Engines
Cylinder head gaskets in automotive engines play a vital role in preventing leakage of combustion gases and coolant.
Made from composite materials that combine the strength of metal with the flexibility of composite layers, these gaskets ensure a tight, durable seal.
Proper gasket selection and installation help in maintaining engine performance and longevity, while preventing leaks that could lead to engine overheating or failure.
Food and Beverage Equipment
In the food and beverage industry, non-metallic gaskets such as those made from PTFE are widely used due to their chemical resistance and compliance with food safety standards.
PTFE gaskets provide an effective seal in processing equipment, preventing leaks of liquids, gases, and contaminants.
Their inertness makes them ideal for applications where purity and hygiene are paramount.
Maintaining Long-Term Gasket Performance
To ensure the long-term effectiveness of seal gaskets, regular maintenance and inspections are critical. Here are some guidelines:
– **Routine Checks**: Regular inspection helps in early detection of wear and tear or degradation. This allows for timely replacements before gasket failure leads to leakage.
– **Proper Installation**: Ensure that gaskets are installed correctly, using the appropriate tools and following manufacturer guidelines. Over-tightening or misalignment can compromise the seal.
– **Environmental Monitoring**: Continuously monitor environmental conditions such as temperature and pressure to ensure they remain within the gasket’s tolerance limits. This helps in identifying potential stressors that could affect the gasket’s performance.
– **Material Upgrades**: With technological advancement, new gasket materials and designs are continually being developed. Staying updated on these innovations can lead to upgrading to more efficient options, enhancing the sealing performance over time.
In conclusion, understanding the basics of seal gasket packing technology is crucial for selecting the right gasket and preventing leakage.
By considering factors like material compatibility, temperature, and pressure, industries can maintain efficient operations and protect the integrity of their systems.
Regular maintenance and proper installation further ensure long-term effectiveness, keeping systems running smoothly and securely.
資料ダウンロード
QCD管理受発注クラウド「newji」は、受発注部門で必要なQCD管理全てを備えた、現場特化型兼クラウド型の今世紀最高の受発注管理システムとなります。
ユーザー登録
受発注業務の効率化だけでなく、システムを導入することで、コスト削減や製品・資材のステータス可視化のほか、属人化していた受発注情報の共有化による内部不正防止や統制にも役立ちます。
NEWJI DX
製造業に特化したデジタルトランスフォーメーション(DX)の実現を目指す請負開発型のコンサルティングサービスです。AI、iPaaS、および先端の技術を駆使して、製造プロセスの効率化、業務効率化、チームワーク強化、コスト削減、品質向上を実現します。このサービスは、製造業の課題を深く理解し、それに対する最適なデジタルソリューションを提供することで、企業が持続的な成長とイノベーションを達成できるようサポートします。
製造業ニュース解説
製造業、主に購買・調達部門にお勤めの方々に向けた情報を配信しております。
新任の方やベテランの方、管理職を対象とした幅広いコンテンツをご用意しております。
お問い合わせ
コストダウンが利益に直結する術だと理解していても、なかなか前に進めることができない状況。そんな時は、newjiのコストダウン自動化機能で大きく利益貢献しよう!
(β版非公開)