- お役立ち記事
- Basics of sealing technology, causes of leakage, and countermeasure techniques
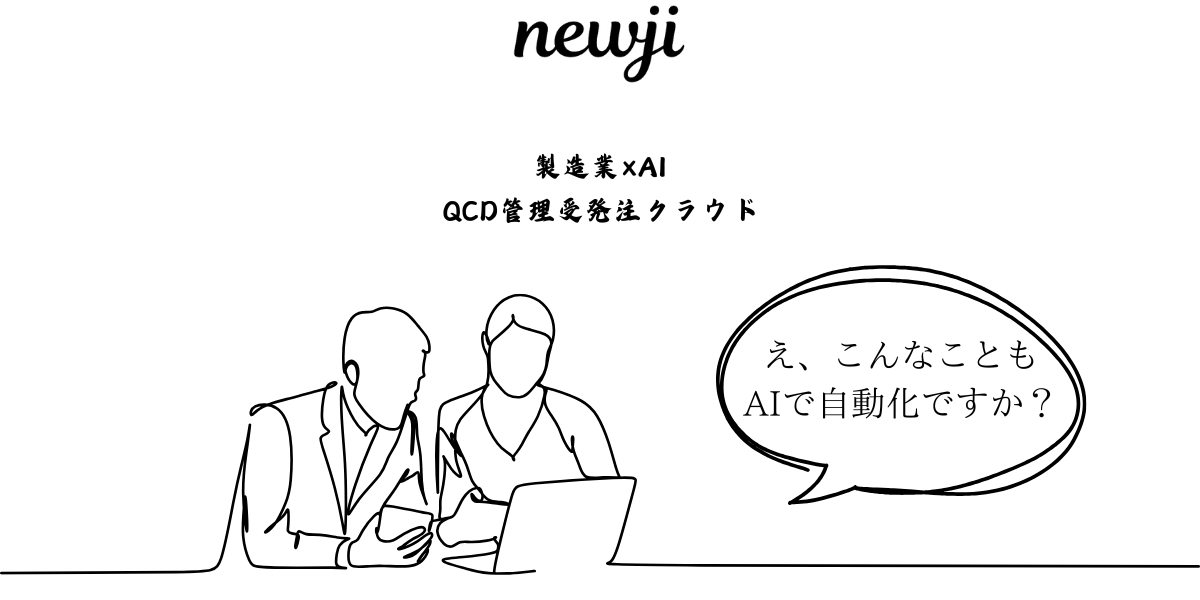
Basics of sealing technology, causes of leakage, and countermeasure techniques
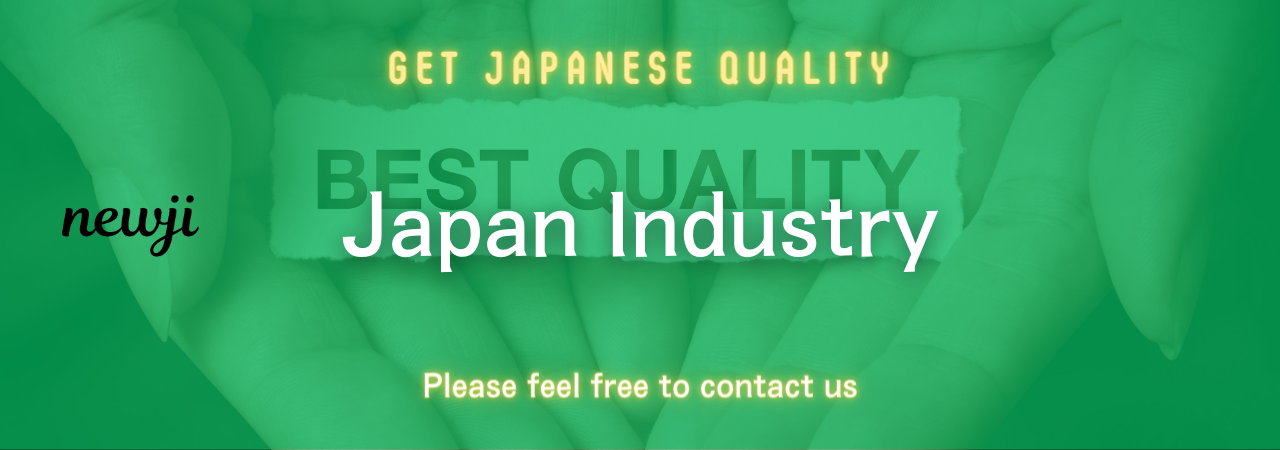
目次
Understanding Sealing Technology
Sealing technology plays a crucial role in various industries, ensuring that fluids and gases remain contained within systems, machinery, and devices.
From household plumbing to aerospace engineering, seals are essential components that prevent leaks and maintain pressure levels.
Seals can be found in engines, hydraulic systems, pumps, compressors, and even everyday items like washing machines and cars.
They come in different forms, including gaskets, O-rings, and mechanical seals.
Each type of seal is specifically designed to withstand the demands of its particular application, whether that’s withstanding high temperatures, pressures, or exposure to chemicals.
Types of Sealing Technology
There are several common types of sealing technologies, each suited for different applications:
1. **Gaskets**: Gaskets are flat seals used between stationary components to prevent leakage of fluids or gases.
They are commonly used in flanges and joints.
Made from various materials like rubber, silicone, or metal, gaskets are designed to handle different temperature ranges and pressures.
2. **O-Rings**: O-rings are circular seals that sit in grooves to block the passage of fluids.
They are extremely versatile and used in a variety of industries.
O-rings are typically made from elastomers like nitrile rubber or silicone due to their flexibility and sealing capability.
3. **Mechanical Seals**: These are complex seals used in rotating equipment such as pumps and compressors.
Mechanical seals are engineered to prevent leaks between the rotating shaft and the stationary housing.
They consist of several components, like a rotating element and a stationary element, that work together to maintain a seal under pressure.
4. **Lip Seals**: Commonly used in rotating applications, lip seals have a flexible lip that rides against a shaft to prevent contaminants from entering and to keep lubricants from leaking out.
They are often used in automotive and machinery applications.
5. **Diaphragm Seals**: Used in pressure measurement systems, diaphragm seals separate the process medium from the pressure instrument to protect it while ensuring accurate readings.
Causes of Leakage in Sealing Systems
Despite the variety and sophistication of seal designs, leaks can occur due to numerous factors.
It’s essential to understand these causes to implement effective solutions.
Improper Installation
The effectiveness of a seal largely depends on its correct installation.
Improperly installed seals can lead to immediate or gradual leakage.
Care should be taken to ensure that seals are correctly aligned, seated, and tightened to the recommended specifications.
Using the right tools during installation is also critical to avoid damaging the seal.
Material Incompatibility
The choice of seal material is critical.
Materials must be compatible with the fluids or gases they contain to prevent degradation over time.
Choosing the wrong material can lead to chemical reactions that weaken the seal, causing leaks.
Wear and Tear
Seals are subject to wear and tear due to friction, pressure variations, and temperature fluctuations.
As seals age, they may lose their elasticity and fail to maintain a proper seal.
Regular maintenance and inspection can help identify worn seals before they lead to leaks.
Temperature Extremes
Seals must withstand the temperature extremes of their operating environments.
Exposure to excessive heat or cold can cause materials to expand, contract, or become brittle, potentially compromising the seal integrity.
Pressure Variations
Seals must handle the pressure levels expected in their specific applications.
Sudden spikes or drops in pressure can cause seals to deform or lose their sealing capability.
Countermeasure Techniques for Leakage Prevention
Effectively addressing leaks involves the use of countermeasure techniques designed to enhance seal performance and reliability.
Selecting Suitable Seal Materials
One of the primary steps in preventing leaks is the selection of the right seal material.
Choose materials based on their compatibility with the fluids or gases, as well as their ability to withstand the environmental conditions, such as temperature and pressure.
Regular Maintenance and Inspection
Regularly inspecting seals for signs of wear or damage is vital.
Scheduled maintenance helps detect potential issues early and allows for the replacement of seals before they fail completely.
This proactive approach minimizes unscheduled downtime and extends the life of equipment.
Proper Installation Techniques
Ensure that seals are installed using the recommended procedures and tools.
Training for personnel involved in seal installation can significantly reduce the likelihood of human error, which is a common cause of leaks.
Using Advanced Sealing Technologies
Advancements in sealing technology have led to new designs and materials that offer improved performance.
Implementing seals that incorporate innovative features, such as self-energizing designs or enhanced material compositions, can greatly reduce leakage risks.
Environmental Control
Control the operating environment to reduce the risk of seal failure.
For example, ensure that temperature and pressure levels remain within the design limits of the seal.
In aggressive chemical environments, consider using protective coatings or additional barriers to shield seals.
Conclusion
Sealing technology is a cornerstone in various industrial applications, ensuring the containment of fluids and gases while maintaining system integrity.
Understanding the causes of leaks and implementing effective countermeasures can enhance performance and prolong the lifespan of sealing systems.
By choosing suitable materials, ensuring proper installation, conducting regular maintenance, and adopting advanced sealing technologies, industries can minimize the risk of leaks and improve operational efficiency.
資料ダウンロード
QCD調達購買管理クラウド「newji」は、調達購買部門で必要なQCD管理全てを備えた、現場特化型兼クラウド型の今世紀最高の購買管理システムとなります。
ユーザー登録
調達購買業務の効率化だけでなく、システムを導入することで、コスト削減や製品・資材のステータス可視化のほか、属人化していた購買情報の共有化による内部不正防止や統制にも役立ちます。
NEWJI DX
製造業に特化したデジタルトランスフォーメーション(DX)の実現を目指す請負開発型のコンサルティングサービスです。AI、iPaaS、および先端の技術を駆使して、製造プロセスの効率化、業務効率化、チームワーク強化、コスト削減、品質向上を実現します。このサービスは、製造業の課題を深く理解し、それに対する最適なデジタルソリューションを提供することで、企業が持続的な成長とイノベーションを達成できるようサポートします。
オンライン講座
製造業、主に購買・調達部門にお勤めの方々に向けた情報を配信しております。
新任の方やベテランの方、管理職を対象とした幅広いコンテンツをご用意しております。
お問い合わせ
コストダウンが利益に直結する術だと理解していても、なかなか前に進めることができない状況。そんな時は、newjiのコストダウン自動化機能で大きく利益貢献しよう!
(Β版非公開)