- お役立ち記事
- Basics of sequence control and examples of troubleshooting and troubleshooting
月間77,185名の
製造業ご担当者様が閲覧しています*
*2025年2月28日現在のGoogle Analyticsのデータより
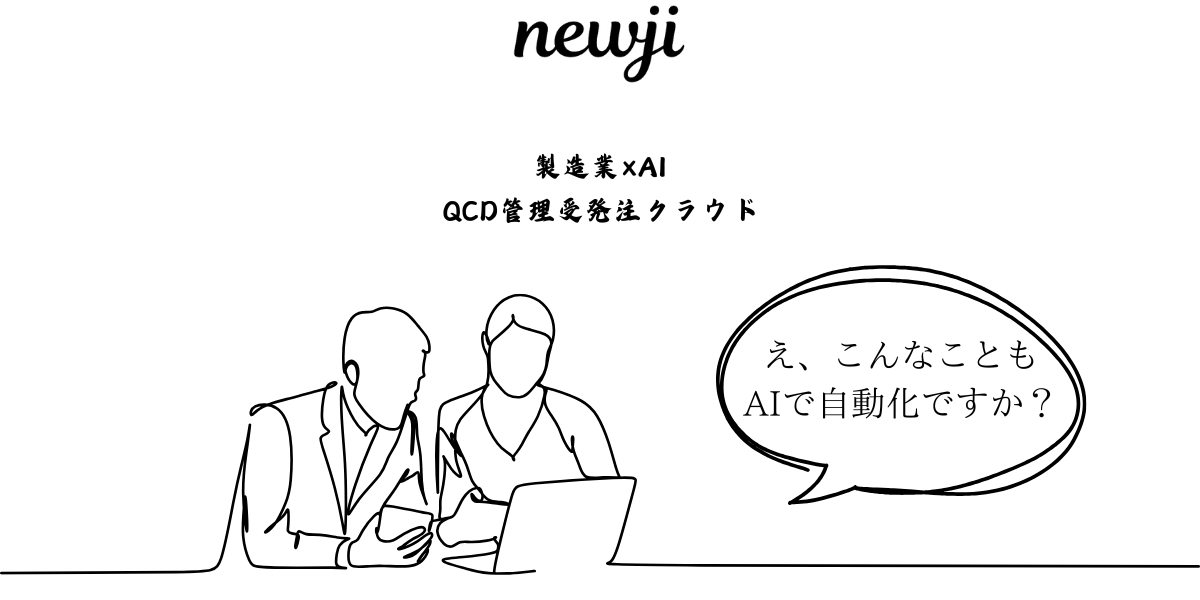
Basics of sequence control and examples of troubleshooting and troubleshooting
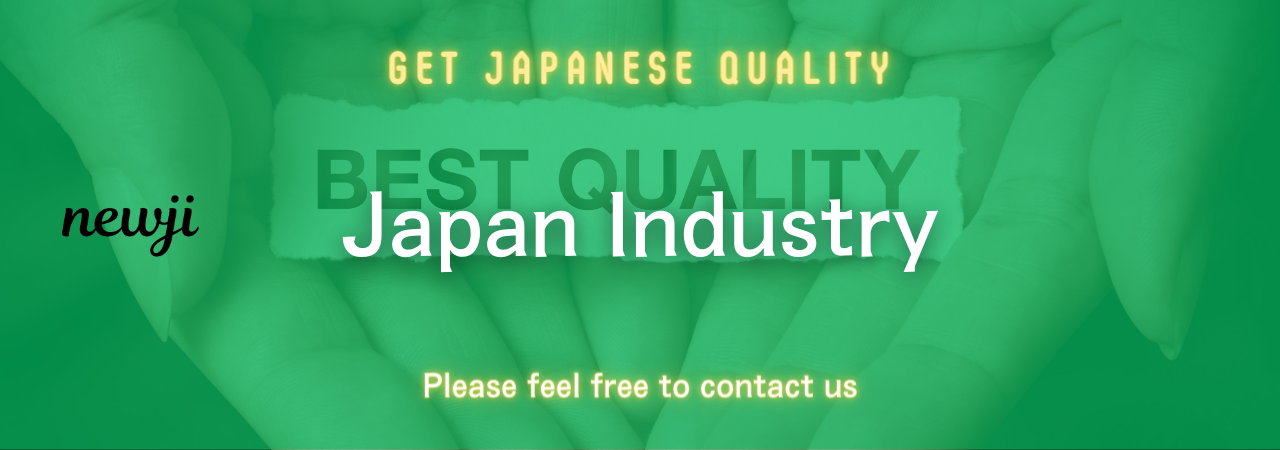
目次
Understanding Sequence Control
Sequence control is a fundamental concept in the realm of electrical engineering and automation.
It refers to the systematic handling and operation of devices in a pre-defined order to complete a specific task or set of tasks.
This could involve processes in manufacturing, household appliances, or even complex robotics, where precision and order are vital to function correctly.
At its core, sequence control works by following a series of steps or logic that are determined beforehand.
These steps are programmed into a system, which could be a programmable logic controller (PLC) or a microcontroller, to ensure that tasks are carried out in the right order and at the right time.
This not only enhances efficiency but also ensures safety, as each step is meticulously planned and executed without deviation.
How Sequence Control Works
To grasp the intricacies of sequence control, one must first understand the components that make up these systems.
Typically, a sequence control system comprises sensors, actuators, controllers, and something that holds the program logic, like a PLC.
1. **Sensors**: These are responsible for gathering real-time data from the environment.
They might monitor temperature, pressure, position, or other factors critical to the process.
2. **Controllers**: These interpret the data collected by sensors.
The controller processes this input and makes decisions based on the pre-written program logic.
3. **Actuators**: These execute the actions required by the controller.
Once the decision is made, actuators physically manipulate the mechanisms like opening valves, starting motors, or activating lights.
In a simple household example, consider a washing machine.
The sensors could detect water levels and weight of the laundry; the controller decides how long to rinse or spin based on this data; and the actuators would physically turn the drum or pump out water as programmed.
Common Troubleshooting Scenarios in Sequence Control
Even the most sophisticated sequence control systems can run into issues.
Identifying and solving these issues is crucial to maintaining efficiency.
Here are some common problems and troubleshooting scenarios.
Sensor Malfunctions
Sensors are integral to the system as they provide the input data required for decision-making.
A failure or error in a sensor can lead to incorrect decisions and hence, process disruptions.
**Troubleshooting Tips:**
– **Calibration Checks**: Regular calibration ensures sensors provide accurate data.
Miscalibration could lead to deviations in performance and should be checked first.
– **Replace or Repair**: Sometimes, sensors might be physically damaged.
Inspecting for signs of wear or damage and replacing them can often resolve issues.
Controller Issues
The controller is the brain of the operation.
If it fails, processes cannot proceed correctly, leading to stagnation or faulty operation.
**Troubleshooting Tips:**
– **Software Diagnostics**: Run a diagnostics test on the software to check for bugs or faulty logic.
Updating the software or re-writing specific logic sequences might be necessary.
– **Hardware Issues**: Ensure the controller device is physically functional.
Check power connections and ensure there’s no visible hardware damage.
Actuator Problems
Actuators implement the decisions made by the controller.
If they fail, the system’s physical operations will come to a halt.
**Troubleshooting Tips:**
– **Mechanical Inspection**: Check for any obstructions or wear that might hinder their movement.
Lubricate if necessary to ensure smooth operation.
– **Signal Testing**: Confirm that the actuators are receiving the correct signals from the controller.
If not, inspect the wiring and connections.
Examples of Sequence Control in Action
Sequence control is more prevalent than most people realize, existing in common appliances and industrial machines that we rely on daily.
Manufacturing Assembly Lines
In manufacturing, assembly lines often rely on sequence control for efficiency and precision.
Each product might pass through various stages such as welding, painting, or assembly.
The timing and order in which these operations occur is crucial.
Sequence control systems in these settings can minimize downtime and maximize throughput.
Automated Packaging Systems
Packaging processes in industries like food and beverages are another example.
These systems need to fill, seal, and label products swiftly and accurately.
Sequence control ensures that errors do not occur, such as filling a carton before opening it or sealing before labeling.
Conclusion
Sequence control is pivotal in both household and industrial settings, underscoring the operations of numerous systems we encounter daily.
Its ability to streamline processes while enhancing safety and efficiency makes it a cornerstone in automation technology.
Understanding its components, troubleshooting common issues, and recognizing its various applications can greatly enhance our interactions with automated systems.
With advancements in technology, sequence control systems continue to evolve, offering more sophisticated solutions to complex challenges across different industries.
資料ダウンロード
QCD管理受発注クラウド「newji」は、受発注部門で必要なQCD管理全てを備えた、現場特化型兼クラウド型の今世紀最高の受発注管理システムとなります。
ユーザー登録
受発注業務の効率化だけでなく、システムを導入することで、コスト削減や製品・資材のステータス可視化のほか、属人化していた受発注情報の共有化による内部不正防止や統制にも役立ちます。
NEWJI DX
製造業に特化したデジタルトランスフォーメーション(DX)の実現を目指す請負開発型のコンサルティングサービスです。AI、iPaaS、および先端の技術を駆使して、製造プロセスの効率化、業務効率化、チームワーク強化、コスト削減、品質向上を実現します。このサービスは、製造業の課題を深く理解し、それに対する最適なデジタルソリューションを提供することで、企業が持続的な成長とイノベーションを達成できるようサポートします。
製造業ニュース解説
製造業、主に購買・調達部門にお勤めの方々に向けた情報を配信しております。
新任の方やベテランの方、管理職を対象とした幅広いコンテンツをご用意しております。
お問い合わせ
コストダウンが利益に直結する術だと理解していても、なかなか前に進めることができない状況。そんな時は、newjiのコストダウン自動化機能で大きく利益貢献しよう!
(β版非公開)