- お役立ち記事
- Basics of sintering technology, evaluation methods, and how to utilize it for applications
月間76,176名の
製造業ご担当者様が閲覧しています*
*2025年3月31日現在のGoogle Analyticsのデータより
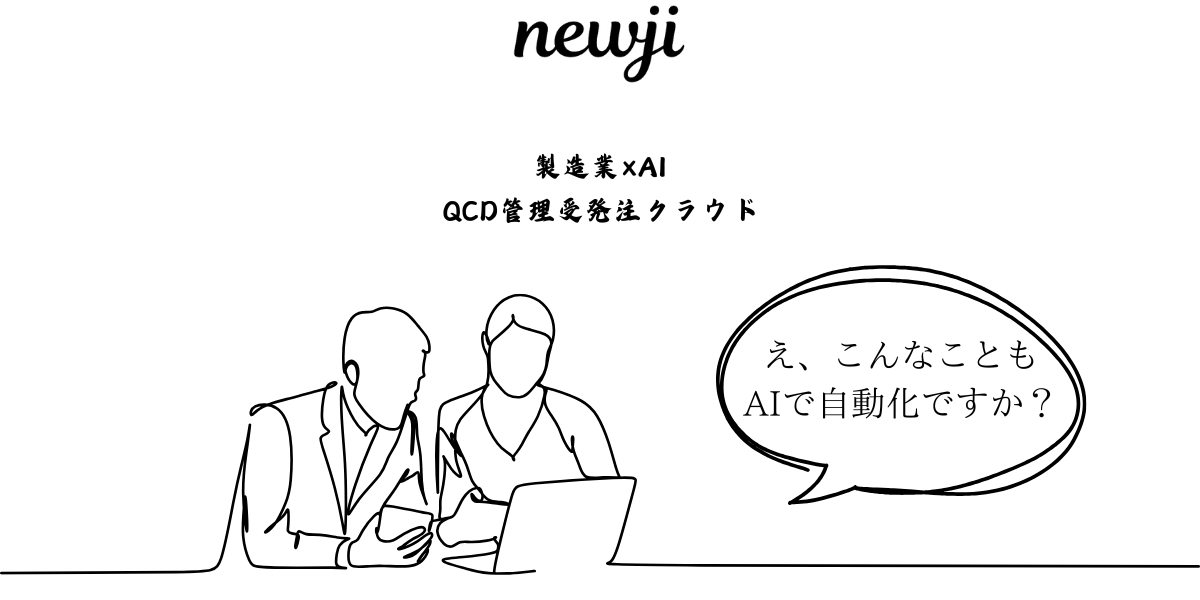
Basics of sintering technology, evaluation methods, and how to utilize it for applications
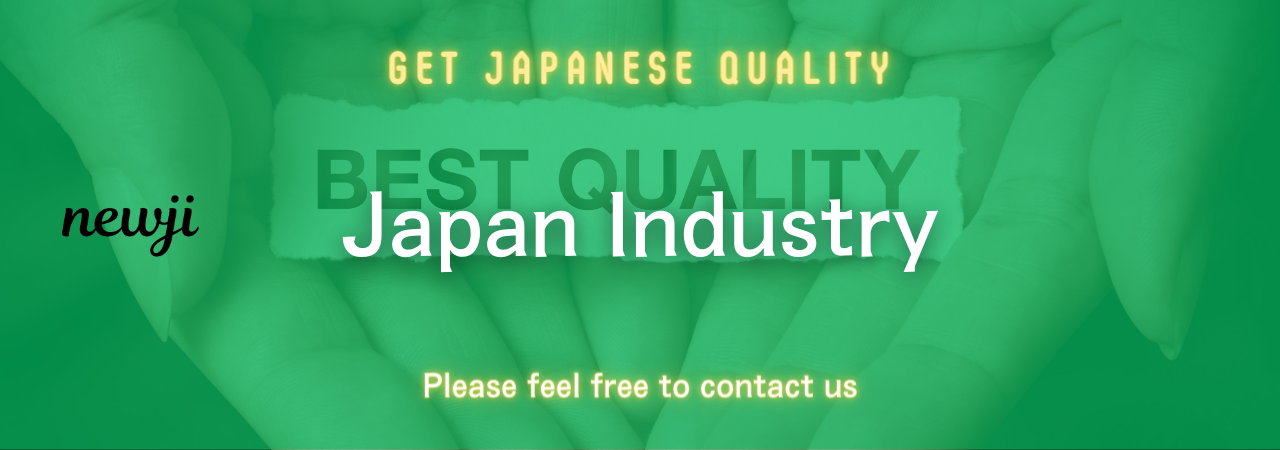
目次
Understanding Sintering Technology
Sintering technology is a crucial process in materials science and engineering, where powdered materials are transformed into solid structures through heat and pressure.
This technology is used widely across various industries, including ceramics, metallurgy, and even electronics.
The fundamental principle behind sintering is the use of thermal energy to consolidate particles, promoting diffusion without reaching their melting point.
Sintering allows the production of complex, high-strength components from powders that may otherwise be challenging to manufacture through traditional methods.
The Sintering Process
Sintering begins with the preparation of raw materials, which are typically in powder form.
These powders are carefully selected and mixed, often with additives, to achieve the desired chemical composition and properties.
Once the powder blend is ready, it is loaded into a mold or a die to form a green body, which is an unsintered compact held together by weak physical forces.
This stage is essential to give the material its initial shape.
The actual sintering takes place in a furnace.
The green body is exposed to high temperatures, usually between 70% to 90% of the material’s melting point.
During this heating phase, the particles begin to bond together through diffusion, which is the movement of atoms or molecules.
This bonding leads to a reduction in porosity and an increase in density, making the structure more robust and refined.
Evaluation Methods for Sintered Materials
To optimize and ensure the quality of sintered products, evaluation methods are employed to assess their properties and performance.
These methods help in understanding how effectively the sintering process has transformed the powdered materials into a cohesive, functional product.
Density Measurement
One of the primary evaluation metrics for sintered materials is density.
A successful sintering process aims to achieve a high density, indicating effective reduction in porosity.
Density measurements are conducted using techniques like Archimedes’ principle, where the volume and mass of the sample are used to calculate its density.
This is crucial as higher density typically correlates with improved mechanical properties.
Microstructural Analysis
The microstructure of a sintered product can reveal important insights into the success of the process.
Microscopic techniques such as scanning electron microscopy (SEM) and transmission electron microscopy (TEM) are utilized to observe the surface morphology and internal structure of the material.
These analyses reveal information on pore distribution, grain boundaries, and any phase transformations that may have occurred during sintering.
Mechanical Testing
Sintered materials often undergo mechanical testing to evaluate their strength, hardness, and toughness.
Common tests include tensile strength, compressive strength, and hardness testing.
These properties are essential to know, especially if the material will be subjected to mechanical stress in its application.
The correlation between microstructure and mechanical properties can help in refining the sintering process for superior performance.
Applications of Sintering Technology
Sintering is a versatile technology that finds applications across a wide range of fields.
Its ability to create materials with bespoke properties makes it invaluable in both traditional and cutting-edge industries.
Metallurgical Applications
In metallurgy, sintering is used to develop various metal parts and components.
It is particularly prevalent in the production of parts for the automotive and aerospace industries, such as gears, bearings, and turbine blades.
Sintering allows for the utilization of metal powders, making the process efficient and cost-effective, especially for complex shapes and intricate designs.
Ceramic Applications
Ceramics benefit significantly from sintering technology.
The process is employed in crafting items ranging from everyday household products to advanced technical ceramics used in electronics and medical devices.
Sintering helps achieve the desired hardness and thermal resistance, essential characteristics in ceramic applications.
Electronic Applications
In the electronics industry, sintering is used for creating materials like ferrites and piezoelectrics, which are crucial in the manufacture of sensors, inductors, and other electronic components.
The precise control offered by sintering ensures that these materials have the necessary electrical properties for optimal functionality.
Utilizing Sintering in Innovative Applications
Advancements in sintering technology continue to drive innovation in material applications.
Researchers and engineers are exploring new ways to harness sintering for emerging technologies and industry needs.
Additive Manufacturing
Sintering is integrated into additive manufacturing processes like 3D printing, particularly in Selective Laser Sintering (SLS).
This has opened new avenues for producing complex geometries and structures in a more efficient and flexible manner.
The combination of sintering and 3D printing is especially promising for rapid prototyping and personalized manufacturing solutions.
Advanced Material Development
The quest for developing advanced materials such as composites and high-performance alloys often relies on sintering technology.
The ability to manipulate compositions and include nanoparticles in sintering processes has led to the development of novel materials with enhanced mechanical and electrical properties.
Environmental and Energy Applications
Sintering contributes to environmental sustainability and energy efficiency.
It is used in producing catalytic converters and fuel cells, vital for reducing emissions and promoting cleaner energy technologies.
The tailored properties achieved through sintering make it an ideal choice for creating materials that address environmental challenges.
In conclusion, sintering technology plays an indispensable role in the manufacturing and development of materials across numerous industries.
From traditional applications in metallurgy and ceramics to cutting-edge developments in electronics and environmental solutions, sintering remains a powerful tool for innovation.
By understanding the basics of sintering, its evaluation methods, and the potential applications, we can better harness this technology to meet the demands of modern society.
資料ダウンロード
QCD管理受発注クラウド「newji」は、受発注部門で必要なQCD管理全てを備えた、現場特化型兼クラウド型の今世紀最高の受発注管理システムとなります。
ユーザー登録
受発注業務の効率化だけでなく、システムを導入することで、コスト削減や製品・資材のステータス可視化のほか、属人化していた受発注情報の共有化による内部不正防止や統制にも役立ちます。
NEWJI DX
製造業に特化したデジタルトランスフォーメーション(DX)の実現を目指す請負開発型のコンサルティングサービスです。AI、iPaaS、および先端の技術を駆使して、製造プロセスの効率化、業務効率化、チームワーク強化、コスト削減、品質向上を実現します。このサービスは、製造業の課題を深く理解し、それに対する最適なデジタルソリューションを提供することで、企業が持続的な成長とイノベーションを達成できるようサポートします。
製造業ニュース解説
製造業、主に購買・調達部門にお勤めの方々に向けた情報を配信しております。
新任の方やベテランの方、管理職を対象とした幅広いコンテンツをご用意しております。
お問い合わせ
コストダウンが利益に直結する術だと理解していても、なかなか前に進めることができない状況。そんな時は、newjiのコストダウン自動化機能で大きく利益貢献しよう!
(β版非公開)