- お役立ち記事
- Basics of sintering technology for metals and ceramics and how to utilize it for applications
月間76,176名の
製造業ご担当者様が閲覧しています*
*2025年3月31日現在のGoogle Analyticsのデータより
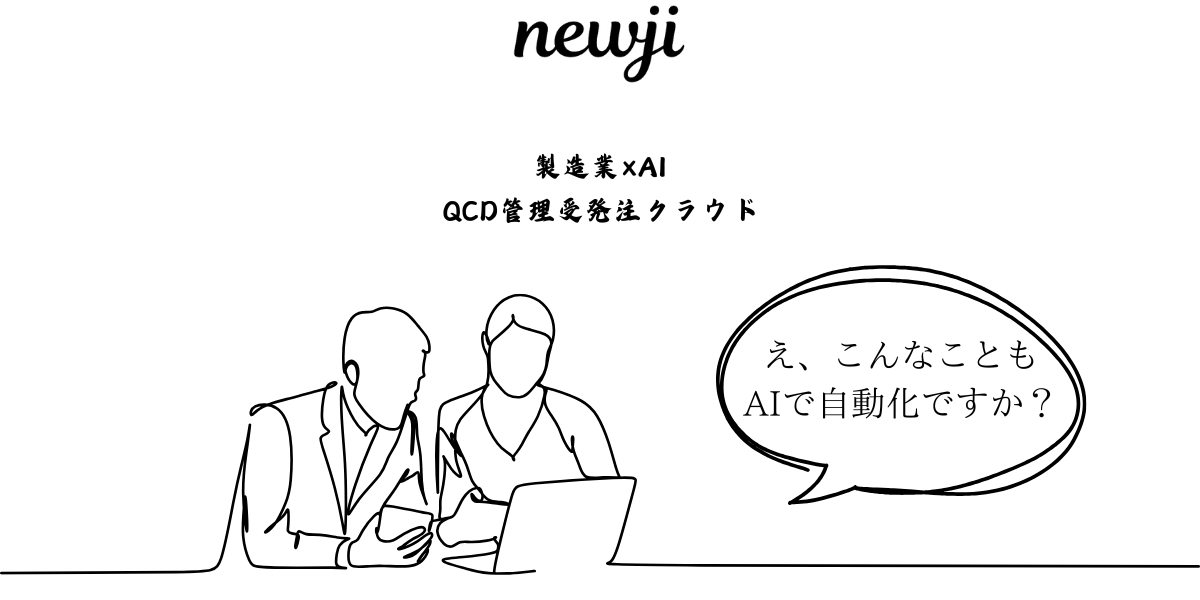
Basics of sintering technology for metals and ceramics and how to utilize it for applications
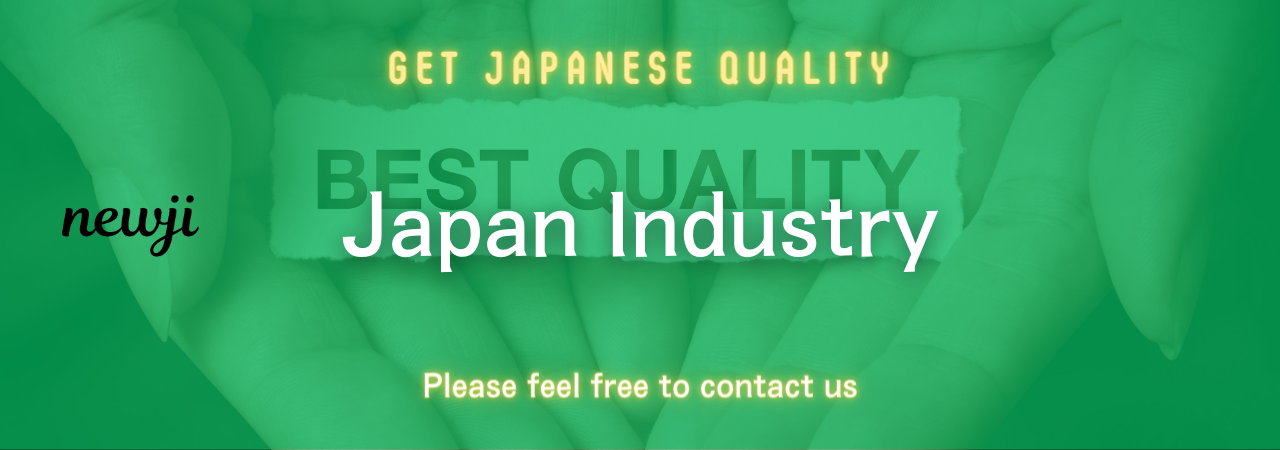
Sintering technology is a fascinating and versatile process that plays a crucial role in the manufacturing of both metals and ceramics. It is a method used to create solid materials by heating powdery substances below their melting points. This results in the particles bonding together to form a dense, strong mass. Understanding the basics of sintering technology can open up a world of potential applications in various industries, from automotive to electronics to medical devices.
目次
What is Sintering?
Sintering is a process that involves the compaction and heating of powder materials. At its core, sintering is about making things stronger and more durable by enhancing the particle bonding of the material. During the sintering process, the powdered substance is compressed to a desired shape and heated in a controlled environment. The heat causes the particles to merge, reducing porosity and increasing the material’s overall strength.
The Sintering Process
The sintering process typically begins with the preparation of powders. These powders are very fine particles that can include metals or ceramics, depending on the final application of the material. The powder is then shaped into the desired form using a mold, applying pressure to compact the particles.
Once the shape is formed, it undergoes a heating cycle in a furnace. The temperature is high enough to activate diffusion between particles but not so high as to melt them completely. This balance is crucial, as it allows the particles to adhere to one another without losing the overall shape of the piece. After cooling, the result is a solid object with enhanced mechanical properties.
Applications of Sintering Technology
Sintering technology is utilized across various sectors due to its efficiency and the high-quality products it produces. Some common applications include:
Metallurgy
In the field of metallurgy, sintering is used to produce complex-shaped metal parts with high precision. It allows manufacturers to produce components that are hard to achieve with traditional casting methods. This is vital in industries where precision and strength are mandatory, such as aerospace and automotive.
Ceramics
For ceramics, sintering helps in achieving products with excellent mechanical, thermal, and chemical stability. Industries such as electronics and manufacturing make use of sintered ceramic components for their durability and resistance to wear and heat.
Medical Devices
Sintering is also popular in the production of medical implants and instruments. The ability to precisely control the size and density of the manufactured parts ensures functional and reliable medical devices that can withstand rigorous use.
Advantages of Sintering
Sintering technology offers several advantages that make it an appealing choice for manufacturers:
Material Efficiency
The sintering process minimizes material waste, as the component is formed from nearly 100% of the original powder material. This is especially beneficial in contexts where materials are costly or need to be used sparingly.
Cost-Effectiveness
Reducing the need for secondary processes such as machining and finishing makes sintering a cost-effective manufacturing method. Additionally, the ability to produce parts in a single process helps keep production expenses low.
Enhanced Properties
Sintered products often possess enhanced mechanical and physical properties compared to parts created through other methods. These include increased strength, wear resistance, and thermal stability.
Challenges in Sintering Technology
Despite its benefits, sintering technology presents some challenges:
Complexity of Process Control
Achieving the optimal balance of temperature, pressure, and time in the sintering process requires precise control to ensure quality. Deviations can lead to defects such as warping or incomplete sintering.
Limitations on Material Types
Not all materials are suitable for sintering. Some composites or highly reactive metals may not perform well under standard sintering conditions, potentially limiting their use.
Size Limitations
The size of components is also constrained by the capabilities of the presses and sintering furnaces available. Large parts may require alternative manufacturing methods.
Conclusion
Sintering technology remains a cornerstone in the manufacturing industry due to its ability to produce parts with exceptional strength and durability. Its applications in metallurgy, ceramics, and various other fields highlight its versatility and efficiency. However, successful sintering requires careful consideration of the material properties and process parameters to overcome challenges such as process control and material limitations.
Embracing the fundamentals of sintering technology enables industries to push the boundaries of what is possible, leading to innovative solutions and advancements in product quality. Understanding this intricate process is key to unlocking new opportunities in material engineering and industrial applications.
資料ダウンロード
QCD管理受発注クラウド「newji」は、受発注部門で必要なQCD管理全てを備えた、現場特化型兼クラウド型の今世紀最高の受発注管理システムとなります。
ユーザー登録
受発注業務の効率化だけでなく、システムを導入することで、コスト削減や製品・資材のステータス可視化のほか、属人化していた受発注情報の共有化による内部不正防止や統制にも役立ちます。
NEWJI DX
製造業に特化したデジタルトランスフォーメーション(DX)の実現を目指す請負開発型のコンサルティングサービスです。AI、iPaaS、および先端の技術を駆使して、製造プロセスの効率化、業務効率化、チームワーク強化、コスト削減、品質向上を実現します。このサービスは、製造業の課題を深く理解し、それに対する最適なデジタルソリューションを提供することで、企業が持続的な成長とイノベーションを達成できるようサポートします。
製造業ニュース解説
製造業、主に購買・調達部門にお勤めの方々に向けた情報を配信しております。
新任の方やベテランの方、管理職を対象とした幅広いコンテンツをご用意しております。
お問い合わせ
コストダウンが利益に直結する術だと理解していても、なかなか前に進めることができない状況。そんな時は、newjiのコストダウン自動化機能で大きく利益貢献しよう!
(β版非公開)