- お役立ち記事
- Basics of sintering technology for metals and ceramics and how to utilize it for applications
月間77,185名の
製造業ご担当者様が閲覧しています*
*2025年2月28日現在のGoogle Analyticsのデータより
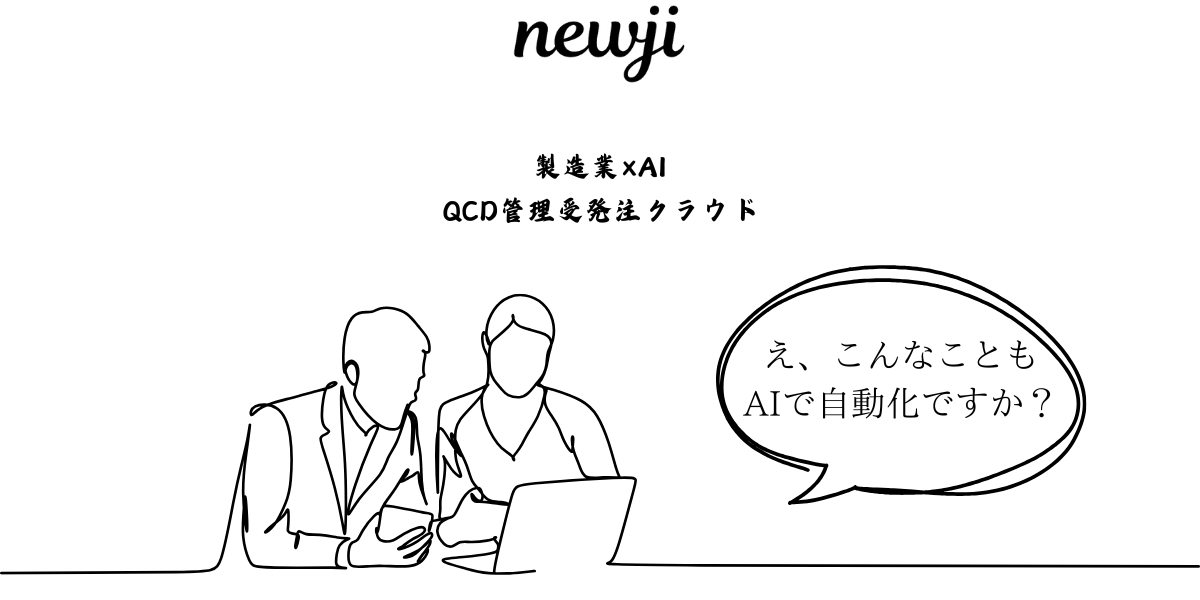
Basics of sintering technology for metals and ceramics and how to utilize it for applications
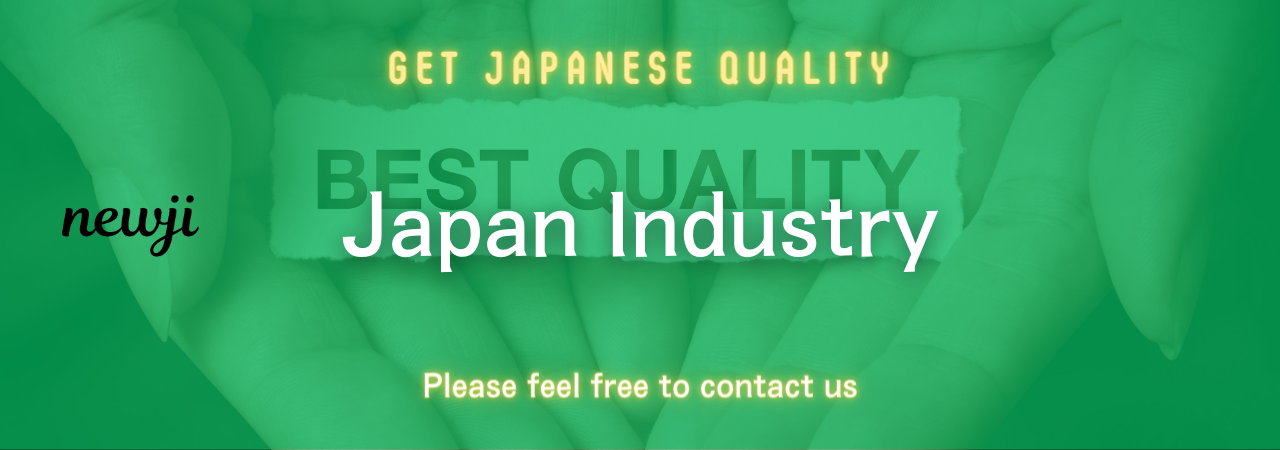
目次
Understanding Sintering Technology
Sintering is a vital process in the world of manufacturing, especially when dealing with metals and ceramics.
At its core, sintering involves consolidating powdered materials into a solid mass by applying heat and sometimes pressure without melting the material to the point of liquefaction.
This technology is not just a recent innovation; it has roots that stretch back thousands of years, with early human civilizations employing basic sintering techniques in their pottery and metalwork.
The objective of sintering is to increase the strength and structural integrity of a material by bonding the particles together.
This is achieved through the application of heat, which encourages the individual particles to bond at a molecular level, resulting in a denser and more durable material.
The temperature used in sintering is typically below the melting point of the primary material, allowing it to maintain its shape and properties while enhancing its physical characteristics.
Benefits of Sintering Technology
Sintering technology offers numerous benefits that make it a preferred choice in various industries.
One of its primary advantages is the ability to create complex shapes and components that would be difficult or impossible to produce using traditional manufacturing methods.
This is particularly advantageous for industries requiring precision and intricate designs, such as aerospace, electronics, and medical devices.
Moreover, sintering allows for the production of parts with consistent and uniform properties.
Since the process happens at a molecular level, the resulting material is often more homogenous than those created through other means.
This uniformity leads to improved mechanical properties, such as increased hardness and strength, which are critical for components subject to high stress or load.
Another significant benefit of sintering is its cost-effectiveness.
The process can significantly reduce material wastage compared to subtractive manufacturing methods, where excess material is removed from a larger block.
Additionally, sintering requires less energy than processes that involve melting, further contributing to its cost efficiency.
Types of Sintering Technologies
Several types of sintering technologies are used, each catering to different materials and applications.
Understanding these types helps in selecting the right method for particular manufacturing needs.
Pressureless Sintering
This is one of the most common sintering methods, primarily used for ceramics and some metal alloys.
In pressureless sintering, the material is heated in a controlled environment without external pressure.
The only force driving the densification is the heat, which causes the particles to bond.
Pressure Sintering
Pressure sintering, often known as hot pressing, involves applying both heat and pressure to the material.
This method is used when pressureless sintering cannot achieve the desired density or strength.
Pressure sintering is particularly useful for producing parts from materials that are difficult to sinter, such as tungsten carbide.
Spark Plasma Sintering
Spark plasma sintering (SPS) is a modern technique that uses a pulsed electric current to generate heat rapidly.
This method allows for fast sintering at lower temperatures, preserving the microstructural properties of the material.
SPS is especially advantageous for sintering materials that are sensitive to temperature changes or have complex microstructures.
Applications of Sintering Technology
Sintering technology is utilized in a wide range of applications, thanks to its versatility and effectiveness in creating strong, complex components.
Automotive Industry
In the automotive sector, sintering is used to produce a variety of components, such as gears, bearings, and brake parts.
These components benefit from sintering’s ability to create uniform and durable materials, essential for withstanding the stresses of high-performance engines and braking systems.
Electronics
The electronics industry relies heavily on sintering to manufacture components such as integrated circuits, capacitors, and sensors.
Sintering enables the production of tiny, intricate parts that are essential for modern electronic devices.
The uniformity and precision of sintered components ensure reliability and performance in electronic applications.
Aerospace
Aerospace applications require materials that can withstand extreme conditions, such as high temperatures and pressures.
Sintering is used to create lightweight and strong components, such as turbine blades and structural parts, that meet the stringent demands of the aerospace sector.
Medical Devices
In the medical field, sintering technology is used to produce implants, surgical tools, and prosthetics.
The ability to create biocompatible and complex shapes makes sintering an ideal process for medical applications, where precision and reliability are paramount.
Future of Sintering Technology
The future of sintering technology is promising, with ongoing advancements aimed at enhancing its capabilities and applications.
Research is focused on developing new materials that are easier to sinter and have improved properties, such as increased toughness and thermal resistance.
Additionally, innovations in sintering techniques, such as faster processing times and lower energy consumption, are expected to expand the range of materials and industries that can benefit from this technology.
As technologies evolve, the ability to use computer simulations to model and predict the outcome of sintering processes will also improve.
This will lead to greater precision and efficiency, further cementing sintering’s place as a cornerstone of modern manufacturing.
In conclusion, sintering technology is a crucial component of the manufacturing landscape, offering unique advantages in terms of design flexibility, material efficiency, and production cost.
Its application across various industries highlights its importance and potential for future advancements.
Whether it’s creating the next generation of lightweight aerospace components or producing intricate electronic devices, sintering will continue to play a vital role in shaping the future of manufacturing.
資料ダウンロード
QCD管理受発注クラウド「newji」は、受発注部門で必要なQCD管理全てを備えた、現場特化型兼クラウド型の今世紀最高の受発注管理システムとなります。
ユーザー登録
受発注業務の効率化だけでなく、システムを導入することで、コスト削減や製品・資材のステータス可視化のほか、属人化していた受発注情報の共有化による内部不正防止や統制にも役立ちます。
NEWJI DX
製造業に特化したデジタルトランスフォーメーション(DX)の実現を目指す請負開発型のコンサルティングサービスです。AI、iPaaS、および先端の技術を駆使して、製造プロセスの効率化、業務効率化、チームワーク強化、コスト削減、品質向上を実現します。このサービスは、製造業の課題を深く理解し、それに対する最適なデジタルソリューションを提供することで、企業が持続的な成長とイノベーションを達成できるようサポートします。
製造業ニュース解説
製造業、主に購買・調達部門にお勤めの方々に向けた情報を配信しております。
新任の方やベテランの方、管理職を対象とした幅広いコンテンツをご用意しております。
お問い合わせ
コストダウンが利益に直結する術だと理解していても、なかなか前に進めることができない状況。そんな時は、newjiのコストダウン自動化機能で大きく利益貢献しよう!
(β版非公開)