- お役立ち記事
- Basics of Six Sigma methodology and quality improvement that new employees in the quality assurance department should know
Basics of Six Sigma methodology and quality improvement that new employees in the quality assurance department should know
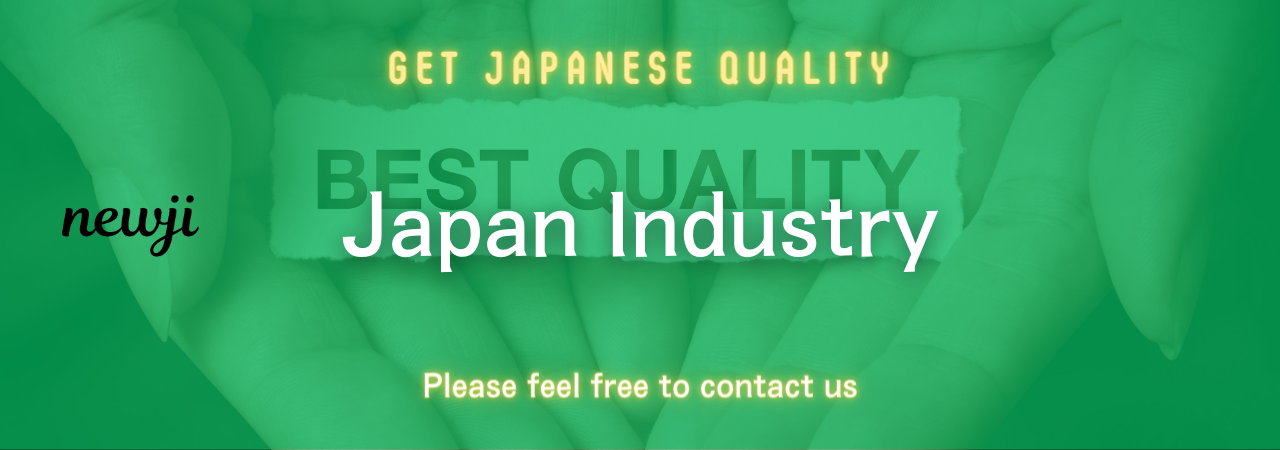
目次
Understanding Six Sigma
Six Sigma is a set of techniques and tools for quality improvement.
Developed by Motorola in the 1980s, it has become a cornerstone for businesses aiming to enhance their processes and deliver superior products.
Its primary goal is to reduce variation and defects in processes, ensuring that every outcome is consistent and meets customer expectations.
The term “Six Sigma” comes from statistics, where “sigma” represents a standard deviation from the process mean or target.
Achieving Six Sigma quality means that a process produces only 3.4 defects per million opportunities.
This level of precision enhances efficiency and ensures product consistency.
Key Principles of Six Sigma
At its core, Six Sigma relies on a few fundamental principles:
1. Customer Focus
Understanding the needs and expectations of customers is crucial.
This drives the creation of products that not only meet but often exceed customer satisfaction.
The voice of the customer (VOC) is central to shaping processes and improvements.
2. Data-Driven Decision Making
Every decision in Six Sigma is based on data.
This minimizes assumptions and ensures that changes are effective and grounded in real-world evidence.
Tools like the DMAIC process (Define, Measure, Analyze, Improve, Control) provide a structured approach to decision-making based on empirical data.
3. Process Improvement
Six Sigma continually seeks to improve existing processes by identifying inefficiencies and eliminating waste.
This approach helps streamline operations and fosters an environment of continuous improvement.
4. Collaboration
Teamwork within and across departments is vital.
Bringing diverse perspectives together often leads to innovative solutions and comprehensive improvements.
The DMAIC Process
DMAIC is a series of steps used by quality improvement teams to tackle problems systematically.
Define
The first step involves clearly defining the problem or project goals.
This step requires understanding who the customers are, what their needs are, and what the project’s objectives entail.
Establishing a clear project scope and setting goals with stakeholders helps guide the process.
Measure
In this phase, data collection begins.
Measuring current processes clarifies the extent of the problem and establishes a baseline for improvement.
Accurate data collection is essential in understanding the existing process performance.
Analyze
Once data is gathered, it is analyzed to identify root causes of defects or inefficiencies.
Various tools, such as process mapping, root cause analysis, and statistical analyses, assist in pinpointing where and why issues occur.
Improve
Solutions to problems identified in the previous phase are developed and tested.
By piloting changes and modifications, teams can assess their effectiveness before widespread implementation.
This phase is iterative, often requiring multiple tests and iterations.
Control
Change management and standardization ensure that improvements are sustained over time.
Control plans and monitoring systems help maintain process gains.
Through this, organizations can prevent regression and ensure continuous benefits.
Six Sigma Tools
There are various tools employed within Six Sigma methodologies to assist teams in improving quality:
1. Cause and Effect Diagram (Fishbone)
This visualization helps teams brainstorm potential causes of a problem and identify its roots.
The fishbone diagram categorizes potential causes to facilitate deeper analysis.
2. Control Charts
These are used to monitor process behavior over time.
By tracking variation, these charts help identify trends and keep processes aligned with set goals.
3. Pareto Chart
The Pareto Principle suggests that 80% of problems are often the result of 20% of causes.
Pareto charts aid in identifying those critical few causes that should be prioritized for resolution.
4. Failure Mode and Effects Analysis (FMEA)
FMEA helps teams identify potential failures in a process or product and the effects these failures might have.
By evaluating risks and their impact, teams can develop strategies to mitigate them.
Implementing Six Sigma as a New Employee
For new employees in the quality assurance department, understanding and integrating Six Sigma principles is essential.
Here are a few steps to facilitate the transition:
1. Learn the Language
Familiarize yourself with Six Sigma terminology and concepts.
Reading foundational texts and guidelines will provide a solid understanding of what Six Sigma entails.
2. Engage in Training
Seek out training opportunities within the organization.
Many companies offer Six Sigma training courses that provide hands-on experience with tools and techniques.
3. Join or Form a Team
Participate in existing projects or form a team for improvement projects.
Collaboration is key; working with experienced colleagues provides insights and broadens understanding.
4. Focus on Data
Develop a keen eye for data and its implications in processes.
Gathering, analyzing, and interpreting data is foundational to making informed decisions in Six Sigma.
Conclusion
Embracing Six Sigma methodologies can significantly impact an organization’s performance and output quality.
By understanding its principles, tools, and processes, new employees in quality assurance can become pivotal assets in driving continuous improvement.
Commitment to learning and applying these concepts ensures both personal growth and organizational success.
資料ダウンロード
QCD調達購買管理クラウド「newji」は、調達購買部門で必要なQCD管理全てを備えた、現場特化型兼クラウド型の今世紀最高の購買管理システムとなります。
ユーザー登録
調達購買業務の効率化だけでなく、システムを導入することで、コスト削減や製品・資材のステータス可視化のほか、属人化していた購買情報の共有化による内部不正防止や統制にも役立ちます。
NEWJI DX
製造業に特化したデジタルトランスフォーメーション(DX)の実現を目指す請負開発型のコンサルティングサービスです。AI、iPaaS、および先端の技術を駆使して、製造プロセスの効率化、業務効率化、チームワーク強化、コスト削減、品質向上を実現します。このサービスは、製造業の課題を深く理解し、それに対する最適なデジタルソリューションを提供することで、企業が持続的な成長とイノベーションを達成できるようサポートします。
オンライン講座
製造業、主に購買・調達部門にお勤めの方々に向けた情報を配信しております。
新任の方やベテランの方、管理職を対象とした幅広いコンテンツをご用意しております。
お問い合わせ
コストダウンが利益に直結する術だと理解していても、なかなか前に進めることができない状況。そんな時は、newjiのコストダウン自動化機能で大きく利益貢献しよう!
(Β版非公開)