- お役立ち記事
- Basics of sliding mode control and application points for controller design
月間77,185名の
製造業ご担当者様が閲覧しています*
*2025年2月28日現在のGoogle Analyticsのデータより
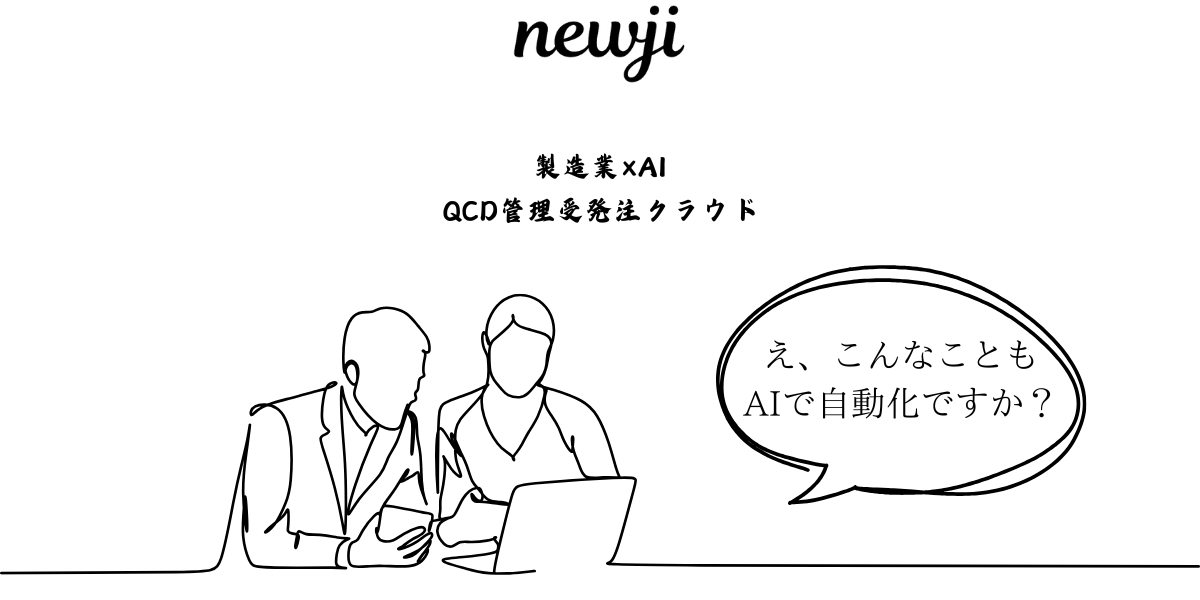
Basics of sliding mode control and application points for controller design
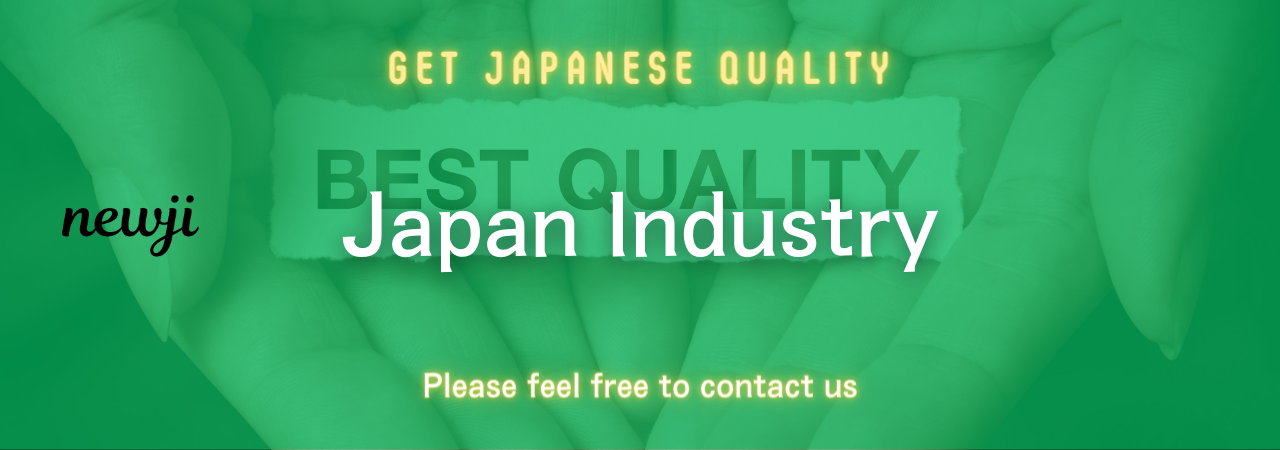
目次
Understanding Sliding Mode Control
Sliding mode control is a type of variable structure control system designed to drive the system’s state to converge to a predetermined “sliding surface” or “manifold” and maintain it thereafter.
This method is particularly effective for systems that are subject to uncertainties and disturbances, offering robustness and high performance.
The essence of sliding mode control lies in its ability to modify the structure of the controller according to the current state of the system, adapting dynamically to achieve desired behavior.
How Sliding Mode Control Works
Sliding mode control operates by creating a control law that enforces the system trajectories to reach and remain on the sliding surface.
The process involves:
1. **Designing a sliding surface:** This surface represents the desired behavior of the system.
2. **Switching control law:** The control input is adjusted to drive the system state towards the sliding surface.
3. **Once on the surface:** The stability and robustness of the control system ensure the system’s state remains on the surface despite any disturbances.
The beauty of sliding mode control lies in its ability to reduce complex problems into simpler, manageable parts, thereby making controller design more straightforward.
Advantages of Sliding Mode Control
Sliding mode control offers several benefits, particularly for systems with inherent or external uncertainties.
Robustness to System Uncertainties
One of the primary advantages of sliding mode control is its robustness against system uncertainties and external disturbances.
By dynamically adjusting the controller structure, it ensures that performance is maintained across a wide range of conditions, considerably reducing the impacts of disturbances.
Simplicity in Design
The design process for sliding mode control systems is relatively straightforward due to the decoupling of control system design into two phases: reaching and sliding.
This allows for simplified modeling and analysis compared to many traditional control methods.
Fast Response and Adaptivity
Sliding mode control systems typically exhibit fast transient behavior and can adaptively respond to changes in system dynamics and environmental conditions.
This results in improved performance for time-critical applications.
Challenges in Sliding Mode Control
While sliding mode control presents numerous advantages, it is important to be aware of potential challenges associated with its design and implementation.
Chattering Phenomenon
A notable challenge in sliding mode control is the chattering phenomenon.
Chattering is an oscillation around the sliding surface caused by high-frequency switching actions of the controller.
This can result in wear and tear of components in practical systems and necessitates careful design to mitigate its effects.
Implementation Complexity
While the theoretical design might be simple, the practical implementation of sliding mode controllers can be more complex.
This complexity arises from the need to deal with discontinuous control laws and high-speed switching mechanisms.
Designing Controllers Using Sliding Mode Control
Implementing sliding mode control requires a methodical approach focused on establishing a robust control strategy that meets specific performance criteria.
Step 1: Define the System Model
The first step in designing a sliding mode controller is to define the mathematical model of the system.
This involves identifying the dynamics, which typically take the form of differential equations that represent the system’s behavior.
Step 2: Design the Sliding Surface
Once the system model is established, the next step is to design the sliding surface.
This surface should represent the desired state or behavior of the system.
A common choice for the sliding surface is a linear combination of the system states.
Step 3: Develop the Control Law
The control law governs how the system state is driven toward and maintained on the sliding surface.
This requires designing a switching function that minimizes the control error and achieves the desired system performance.
Step 4: Simulate and Validate the Controller
Before implementing the controller in a real-world application, it is essential to simulate its performance.
This allows for the examination of the system under various disturbances and uncertainties, ensuring robustness and accuracy.
Step 5: Implement the Controller
Once validated through simulation, the controller can be implemented on physical hardware.
Considerations such as sensor accuracy, processor speed, and actuator capabilities must be taken into account to ensure the controller operates effectively.
Applications of Sliding Mode Control
Sliding mode control finds applications across various fields due to its robustness and adaptability.
Automotive Systems
In automotive systems, sliding mode control is used for enhancing the performance of anti-lock braking systems (ABS) and traction control systems (TCS).
These applications benefit from the adaptive nature of sliding mode control to address the nonlinear and uncertain dynamics of vehicles.
Robotics
Robotic systems, especially those that require precise control in uncertain environments, utilize sliding mode control to achieve stability and accuracy.
This is particularly useful in robotic manipulators and mobile robots navigating complex terrains.
Power Electronics
Sliding mode control is applied in power electronics for controlling DC/DC converters and inverters, where fast dynamics and robustness to component variations are important.
Conclusion
Sliding mode control is a powerful tool for designing robust control systems capable of handling uncertainties and disturbances.
By focusing on the system model, sliding surface design, and control law development, engineers can implement effective control strategies across a broad range of applications.
Despite challenges like chattering, the versatility and strength of sliding mode control make it a valuable technique in modern control system design.
資料ダウンロード
QCD管理受発注クラウド「newji」は、受発注部門で必要なQCD管理全てを備えた、現場特化型兼クラウド型の今世紀最高の受発注管理システムとなります。
ユーザー登録
受発注業務の効率化だけでなく、システムを導入することで、コスト削減や製品・資材のステータス可視化のほか、属人化していた受発注情報の共有化による内部不正防止や統制にも役立ちます。
NEWJI DX
製造業に特化したデジタルトランスフォーメーション(DX)の実現を目指す請負開発型のコンサルティングサービスです。AI、iPaaS、および先端の技術を駆使して、製造プロセスの効率化、業務効率化、チームワーク強化、コスト削減、品質向上を実現します。このサービスは、製造業の課題を深く理解し、それに対する最適なデジタルソリューションを提供することで、企業が持続的な成長とイノベーションを達成できるようサポートします。
製造業ニュース解説
製造業、主に購買・調達部門にお勤めの方々に向けた情報を配信しております。
新任の方やベテランの方、管理職を対象とした幅広いコンテンツをご用意しております。
お問い合わせ
コストダウンが利益に直結する術だと理解していても、なかなか前に進めることができない状況。そんな時は、newjiのコストダウン自動化機能で大きく利益貢献しよう!
(β版非公開)