- お役立ち記事
- Basics of static electricity countermeasures and equipment maintenance points that new employees in the equipment management department of the electronic equipment manufacturing industry should know
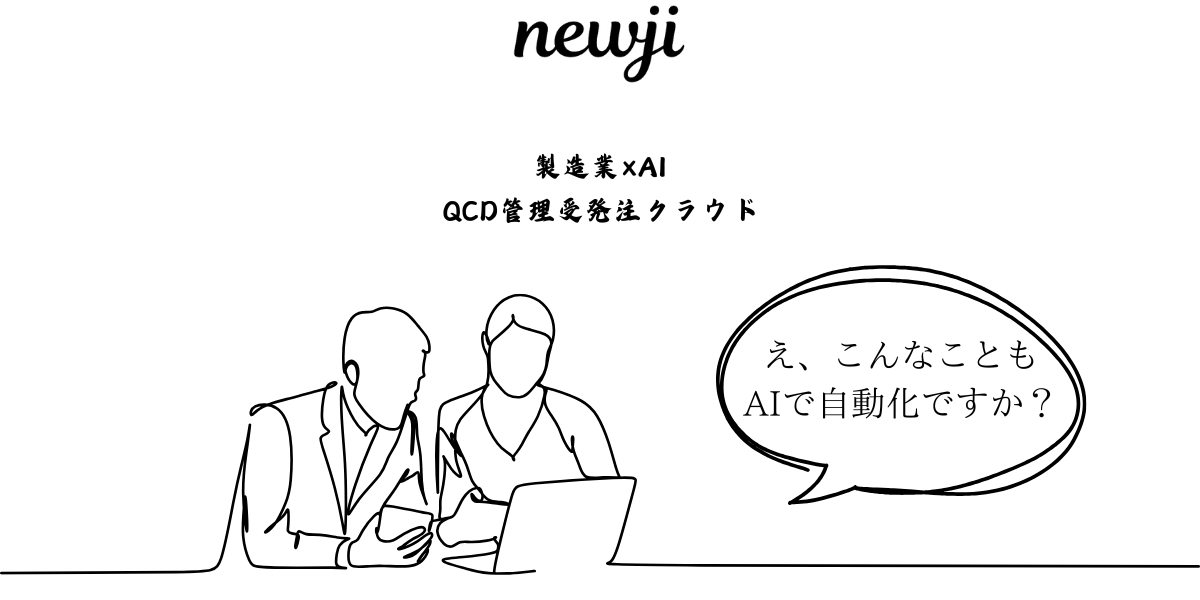
Basics of static electricity countermeasures and equipment maintenance points that new employees in the equipment management department of the electronic equipment manufacturing industry should know
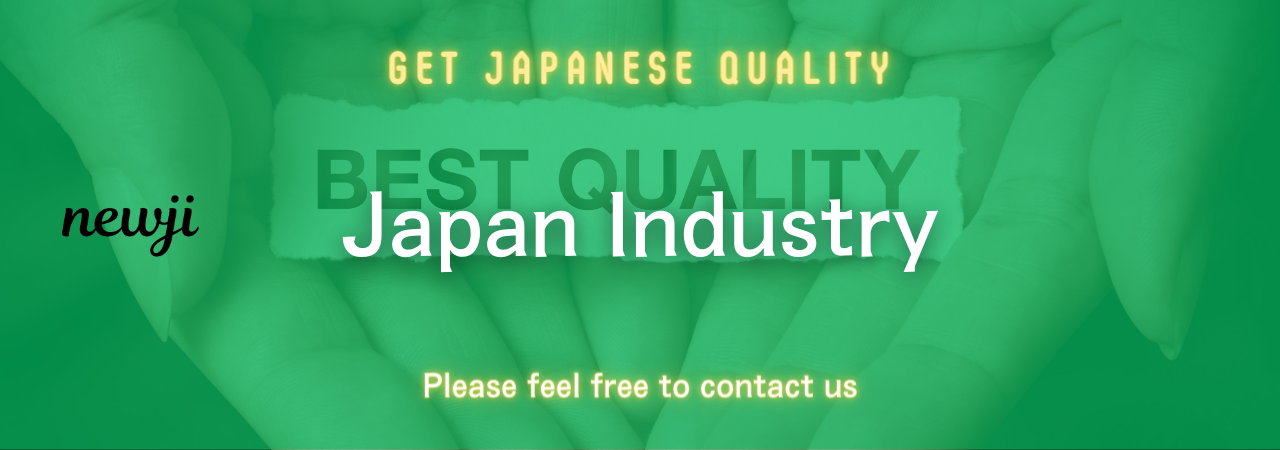
目次
Understanding Static Electricity in Electronic Equipment
Static electricity is a common and often unnoticed phenomenon that can have significant consequences in electronic equipment manufacturing.
It is caused by the imbalance of electrical charges within or on the surface of a material.
This imbalance leads to a sudden discharge of electricity when two objects come into contact or near each other.
In an environment where sensitive electronic components are created or assembled, static electricity can lead to electrostatic discharge (ESD).
ESD can damage or destroy electronic components, which are often crucial and expensive parts of any electronic device.
Thus, it is essential for new employees in the equipment management department to understand the basics of static electricity and learn how to manage it effectively.
The Damage Caused by Static Electricity
Static electricity might seem harmless, but in the context of electronic manufacturing, it poses a significant threat.
ESD can cause immediate damage to electronic components, leading to malfunction or even complete failure.
This damage is often not immediately visible but can manifest as a surprise failure during the operation of the device, resulting in costly repairs and maintenance.
Moreover, static electricity can result in data loss or corruption.
In an industry where precision and reliability are paramount, data integrity is critical.
Therefore, preventing ESD is not just about protecting physical components but also about safeguarding the data and ensuring reliable performance.
Identifying Static Electricity Sources
New employees should be able to identify potential sources of static electricity within the manufacturing environment.
Common sources include human operators, equipment, and even the materials being used.
Walking across a carpet or rubbing against certain materials can generate significant static electricity.
Similarly, plastic components or packaging materials can become charged, posing a risk to electronics.
Knowing where static electricity originates helps in planning effective countermeasures.
Focusing on these primary sources allows the equipment management team to implement strategies that minimize the risk of ESD events.
Effective Countermeasures Against Static Electricity
Implementing effective countermeasures is essential for preventing ESD damage.
Here are some basic strategies that new employees should be familiar with:
1. Grounding and Bonding
Grounding is one of the most effective ways to control static electricity.
By providing a path for the electrical charge to dissipate safely into the ground, you can prevent a buildup of static charge.
All equipment and operators should be properly grounded to ensure effective static electricity management.
Bonding involves connecting all conductive objects that are part of the process or in the work area so that they maintain a common electrical potential.
This reduces the risk of electrical charge transfer between objects.
2. Use of Antistatic Mats and Wrist Straps
Antistatic mats provide a controlled path to dissipate excess static charge while offering a level of comfort for workers.
These mats are typically made of materials that resist static electricity and are often used in work areas where sensitive electronics are handled.
Wrist straps are worn by operators to ensure they are grounded, preventing any charge accumulation.
These are particularly effective when operators have to work with highly sensitive components directly.
3. Controlling Environmental Conditions
The environment plays a significant role in the generation of static electricity.
A higher humidity level reduces static charge buildup.
Using humidifiers in the workplace can help maintain an optimal level of humidity to prevent static electricity.
Additionally, maintaining a clean work environment free of dust and particulates can also help reduce static electricity as these elements often act as conductors for static charge.
Regular Equipment Maintenance
Routine maintenance is crucial to managing static electricity effectively.
Employees should perform regular checks on all equipment, ensuring they are in good working condition and that any grounding or anti-static measures are operational.
Inspecting grounding connections and ensuring equipment is clean and free of static-inducing contaminants will help in mitigating the risks associated with ESD.
Any broken equipment should be repaired or replaced immediately to maintain safety standards.
Training and Awareness
Continuous education and training for all employees in the equipment management department are vital.
While new employees will receive initial training, staying updated on the best practices and technological advances in static electricity control is essential.
Conducting regular workshops and seminars will ensure everyone is aware of the latest methods and tools for preventing ESD.
Conclusion
Static electricity might be a small scientific curiosity for most, but in the world of electronic equipment manufacturing, it is a force that must be managed with precision.
Understanding the causes and implementing effective countermeasures can prevent costly damage and maintain the reliability of electronic products.
For new employees in the equipment management department, grasping the basics of static electricity control and adhering to maintenance best practices will ensure both product quality and job efficiency.
By actively participating in training and constantly striving to enhance environmental control measures, employees can contribute significantly to the success of their organization in the electronic manufacturing industry.
資料ダウンロード
QCD調達購買管理クラウド「newji」は、調達購買部門で必要なQCD管理全てを備えた、現場特化型兼クラウド型の今世紀最高の購買管理システムとなります。
ユーザー登録
調達購買業務の効率化だけでなく、システムを導入することで、コスト削減や製品・資材のステータス可視化のほか、属人化していた購買情報の共有化による内部不正防止や統制にも役立ちます。
NEWJI DX
製造業に特化したデジタルトランスフォーメーション(DX)の実現を目指す請負開発型のコンサルティングサービスです。AI、iPaaS、および先端の技術を駆使して、製造プロセスの効率化、業務効率化、チームワーク強化、コスト削減、品質向上を実現します。このサービスは、製造業の課題を深く理解し、それに対する最適なデジタルソリューションを提供することで、企業が持続的な成長とイノベーションを達成できるようサポートします。
オンライン講座
製造業、主に購買・調達部門にお勤めの方々に向けた情報を配信しております。
新任の方やベテランの方、管理職を対象とした幅広いコンテンツをご用意しております。
お問い合わせ
コストダウンが利益に直結する術だと理解していても、なかなか前に進めることができない状況。そんな時は、newjiのコストダウン自動化機能で大きく利益貢献しよう!
(Β版非公開)