- お役立ち記事
- Basics of strength analysis and how to utilize CAE for strength design and know-how
月間76,176名の
製造業ご担当者様が閲覧しています*
*2025年3月31日現在のGoogle Analyticsのデータより
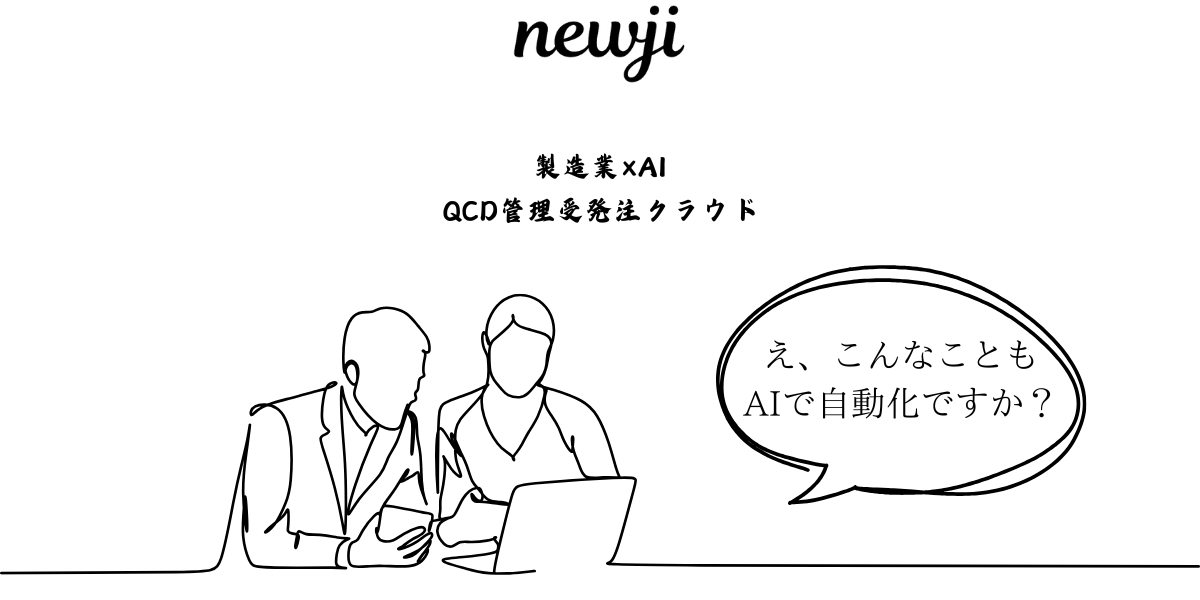
Basics of strength analysis and how to utilize CAE for strength design and know-how
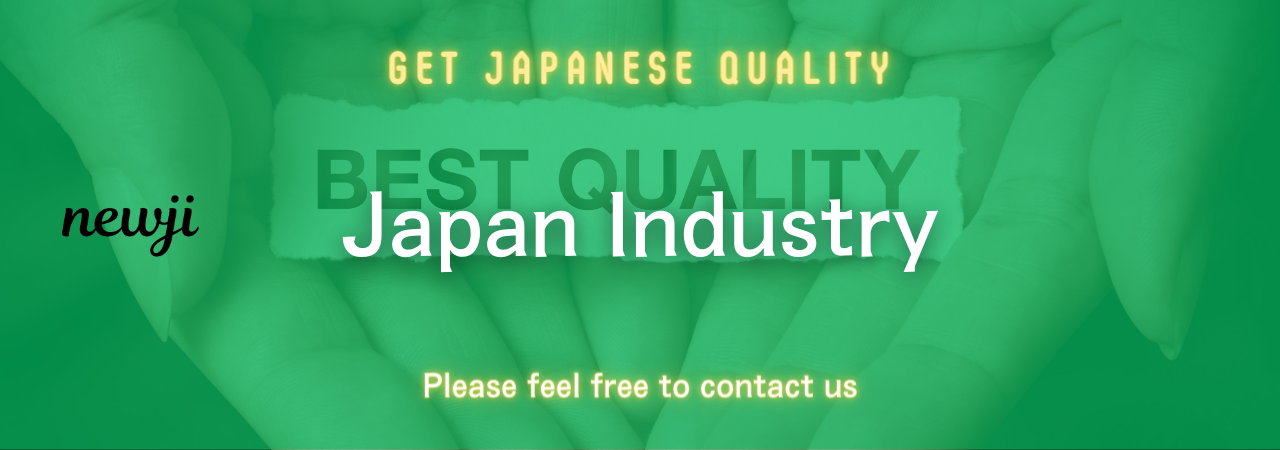
目次
Understanding Strength Analysis
Strength analysis is an essential component in the field of engineering and design.
It involves evaluating the ability of a structure or material to withstand applied forces without failure.
The goal is to ensure safety, reliability, and efficiency in various applications, from bridges and buildings to machinery and vehicles.
Strength analysis helps engineers identify potential weak points and optimize designs to prevent structural failures.
By understanding the principles of strength analysis, engineers can create designs that not only meet performance requirements but also withstand the demands of real-world use.
Key Principles of Strength Analysis
1. **Load Types**: Identifying the types of loads a structure may face is crucial.
Common load types include tension, compression, shear, and torsion.
Each type of load affects materials differently, and understanding their impact is crucial for accurate analysis.
2. **Material Properties**: The properties of materials, such as elasticity, plasticity, toughness, and hardness, play a significant role in strength analysis.
Knowing how materials behave under different conditions helps predict their performance.
3. **Stress and Strain**: Stress is the force applied to a material, while strain is the deformation it experiences.
Analyzing stress and strain relationships helps determine how a material will respond to different forces.
4. **Factor of Safety**: This is a design principle that involves using a safety margin to account for uncertainties in material properties, load assumptions, and environmental conditions.
It ensures that structures operate safely beyond anticipated loads.
5. **Failure Theories**: Engineers use various failure theories to predict when materials might fail under specific conditions.
Common theories include maximum stress, maximum strain, and von Mises stress.
Introduction to Computer-Aided Engineering (CAE)
Computer-Aided Engineering (CAE) is a technology-driven approach that utilizes computers to assist in engineering analysis tasks.
CAE plays a critical role in strength analysis by providing sophisticated tools that simulate real-world conditions and predict the performance of designs.
Through CAE, engineers can conduct virtual tests on materials and structures, allowing for the identification of potential issues before physical prototypes are built.
How CAE Enhances Strength Design
1. **Simulation and Modeling**: CAE software allows engineers to create detailed models of designs and simulate different load conditions.
This enables them to study stress distribution, identify weak points, and make necessary adjustments to enhance structural integrity.
2. **Optimization**: With CAE, engineers can optimize designs by testing various configurations and selecting the most efficient one.
This results in cost-effective and resource-efficient solutions that meet all performance criteria.
3. **Rapid Prototyping**: CAE speeds up the design process by reducing the need for physical prototypes.
Engineers can iterate faster and test multiple design variations, ultimately leading to the best possible outcome.
4. **Cost Reduction**: By identifying potential issues early in the design phase, CAE helps eliminate costly errors and reduces the need for extensive physical testing.
This not only saves money but also shortens time-to-market for products.
5. **Enhanced Collaboration**: CAE tools facilitate better communication and collaboration among engineering teams.
They provide a common platform for sharing and visualizing design data, fostering a more integrated approach to problem-solving.
Practical Applications of CAE in Strength Analysis
CAE is employed across various industries to enhance strength analysis and design processes.
Automotive Industry
In the automotive industry, strength analysis using CAE is vital for ensuring vehicle safety and performance.
CAE tools help engineers simulate crash scenarios, optimize material usage, and improve overall vehicle aerodynamics.
This ensures vehicles meet safety standards while optimizing fuel efficiency and reducing emissions.
Aerospace Industry
The aerospace industry heavily relies on CAE for designing aircraft components that withstand extreme conditions.
Engineers use CAE to simulate aerodynamic forces, thermal stresses, and fatigue loading to develop reliable and lightweight structures.
CAE allows for innovations in materials and design processes, pushing the boundaries of what is possible in aerospace engineering.
Construction and Civil Engineering
In construction and civil engineering, CAE aids in designing safe and durable infrastructure projects.
Strength analysis ensures buildings can withstand natural forces like wind, earthquakes, and heavy loads.
CAE tools help engineers design efficient layouts and identify potential failure points, leading to safer and more sustainable structures.
Manufacturing Industry
Manufacturers use CAE to improve product design and production processes.
By simulating manufacturing conditions and testing material properties, CAE helps identify defects and optimize production lines.
This enhances product quality and reduces wastage, contributing to a more sustainable manufacturing approach.
Best Practices for Using CAE in Strength Analysis
1. **Accurate Data Input**: Ensure all relevant material properties, load conditions, and environmental factors are accurately inputted into the CAE software for precision in simulations.
2. **Validation and Verification**: Always validate simulation results with real-world testing to verify assumptions and improve accuracy.
3. **Continuous Learning**: Stay updated on the latest advancements in CAE technology and best practices to leverage the full potential of these tools in design processes.
4. **Collaboration and Communication**: Encourage open communication among team members to share insights and improve overall design efficiency.
5. **Iterative Approach**: Use CAE iteratively throughout a project from concept to final design to continually refine and enhance the design.
By integrating CAE into strength analysis, engineers are better equipped to create designs that withstand real-world challenges while optimizing for efficiency and innovation.
It is an invaluable tool that enhances the capabilities of engineering teams across various sectors.
資料ダウンロード
QCD管理受発注クラウド「newji」は、受発注部門で必要なQCD管理全てを備えた、現場特化型兼クラウド型の今世紀最高の受発注管理システムとなります。
ユーザー登録
受発注業務の効率化だけでなく、システムを導入することで、コスト削減や製品・資材のステータス可視化のほか、属人化していた受発注情報の共有化による内部不正防止や統制にも役立ちます。
NEWJI DX
製造業に特化したデジタルトランスフォーメーション(DX)の実現を目指す請負開発型のコンサルティングサービスです。AI、iPaaS、および先端の技術を駆使して、製造プロセスの効率化、業務効率化、チームワーク強化、コスト削減、品質向上を実現します。このサービスは、製造業の課題を深く理解し、それに対する最適なデジタルソリューションを提供することで、企業が持続的な成長とイノベーションを達成できるようサポートします。
製造業ニュース解説
製造業、主に購買・調達部門にお勤めの方々に向けた情報を配信しております。
新任の方やベテランの方、管理職を対象とした幅広いコンテンツをご用意しております。
お問い合わせ
コストダウンが利益に直結する術だと理解していても、なかなか前に進めることができない状況。そんな時は、newjiのコストダウン自動化機能で大きく利益貢献しよう!
(β版非公開)