- お役立ち記事
- Basics of strength analysis using CAE, how to utilize it in strength design, and its key points
Basics of strength analysis using CAE, how to utilize it in strength design, and its key points
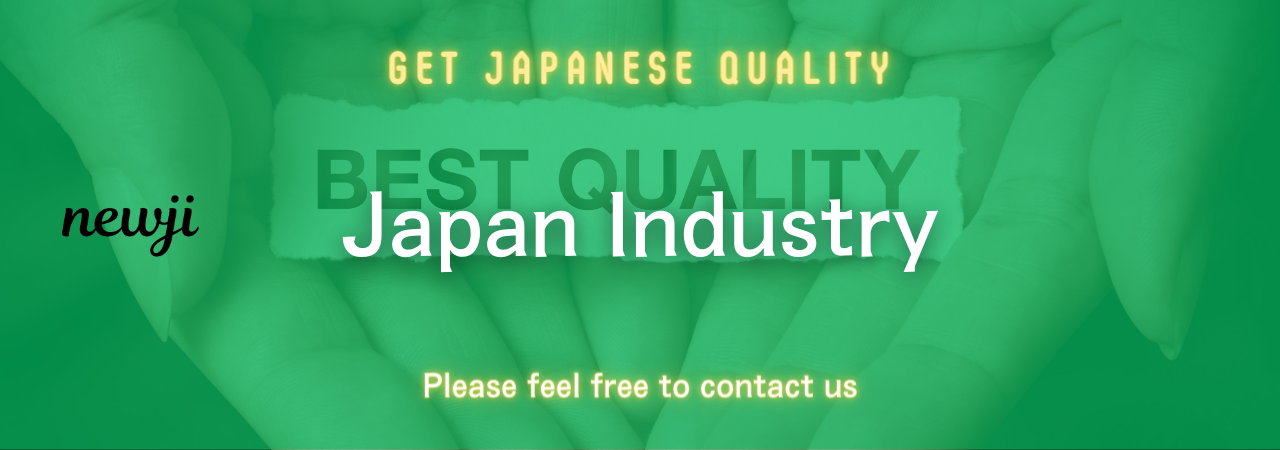
目次
Understanding the Basics of Strength Analysis Using CAE
Strength analysis is an essential process in the development of any product or structure, ensuring that it can withstand the forces and stresses it will encounter during its lifecycle.
Computer-Aided Engineering (CAE) has revolutionized the way engineers conduct strength analysis, making it faster, more accurate, and more cost-effective.
CAE tools allow engineers to simulate real-world conditions and predict the performance of materials and products before they are physically manufactured.
What is CAE?
Computer-Aided Engineering (CAE) encompasses the use of computer software to aid in engineering tasks.
CAE tools are commonly used to perform simulations and analyses such as Finite Element Analysis (FEA), Computational Fluid Dynamics (CFD), and Multibody Dynamics (MBD).
These tools help engineers to optimize designs, improve product quality, and reduce costs.
In the context of strength analysis, CAE allows engineers to evaluate the mechanical properties of materials and the structural integrity of components under various loading conditions.
The Role of FEA in Strength Analysis
Finite Element Analysis (FEA) is a key component of strength analysis in CAE.
It involves subdividing a large problem into smaller, simpler parts known as finite elements.
These elements are then analyzed individually, and the results are combined to predict the behavior of the entire system.
FEA is particularly useful for calculating stress, strain, and deformation of materials under different loading conditions.
This enables engineers to identify potential weaknesses in a design and make the necessary modifications before physical prototypes are built.
Advantages of Using CAE for Strength Analysis
One of the primary advantages of using CAE for strength analysis is the ability to simulate complex and realistic scenarios that would be challenging to reproduce experimentally.
CAE tools allow engineers to analyze multiple loading conditions, such as static, dynamic, thermal, and fatigue loads.
Consequently, this versatility can lead to a more comprehensive understanding of how a product will perform in the real world.
Furthermore, CAE significantly reduces both development time and costs.
Prototypes and physical testing, which can be expensive and time-consuming, are minimized, as engineers can conduct virtual experiments and identify issues early in the design process.
Moreover, CAE tools are capable of managing vast amounts of data and complex calculations much faster than manual computation methods, leading to accelerated design cycles.
Using CAE in Strength Design
Strength design is a critical aspect of the engineering process, aiming to ensure that structures are safe and functional while optimizing material use and cost.
CAE tools play a crucial role in this process by providing the necessary information to make informed design decisions.
Design Optimization Through CAE
One important application of CAE in strength design is design optimization.
CAE enables engineers to explore various design configurations and material selections to achieve the most efficient and effective solution.
FEA can be used to simulate and compare different designs, allowing engineers to determine which configurations offer the best performance characteristics without compromising strength or integrity.
By integrating CAE into the initial stages of the design process, engineers can implement changes that significantly enhance a product’s performance and ensure safety margins are met while keeping material costs in check.
Enhancing Safety with CAE
Safety is paramount in strength design, and CAE tools provide engineers with the data necessary to ensure that structures can withstand anticipated loads and stresses.
By simulating worst-case scenarios and stress concentration points, engineers can identify potential failure modes and make necessary reinforcements in critical areas.
This not only ensures compliance with safety standards but also provides peace of mind that the structure will perform reliably even under unexpected conditions.
Reducing Material Waste
Another advantage of using CAE in strength design is its ability to reduce material waste.
Through precise simulations, engineers can determine the exact amount of material required to achieve the desired strength and durability.
By avoiding over-designing, which often leads to unnecessary material usage and increased weights, CAE aids in creating more sustainable and cost-effective products.
Key Points to Consider in Strength Analysis Using CAE
Although CAE provides numerous benefits, achieving accurate and reliable results depends on several key considerations.
Understanding Material Properties
One crucial factor in strength analysis is the accurate representation of material properties.
CAE tools rely on material data to simulate how materials will respond under different conditions.
This requires precise information about the material’s behavior, such as its elasticity, plasticity, and thermal properties.
Misrepresenting these properties can lead to inaccurate predictions, so it’s crucial to use validated material data from trustworthy sources.
Setting Appropriate Boundary Conditions
Boundary conditions specify how a model interacts with its environment, including constraints and loads applied to a structure.
Incorrectly defining these conditions can significantly impact the accuracy of the analysis.
It is essential to apply realistic constraints and loading scenarios to ensure that the simulation results reflect actual service conditions.
Mesh Quality and Refinement
The quality of the mesh in FEA simulations is another critical factor that affects the accuracy of results.
A fine mesh with appropriately sized elements captures more detail, leading to more accurate simulations.
However, a balance must be struck, as too fine a mesh can significantly increase computation time and resources.
Mesh refinement should focus on areas of high stress or complexity to achieve accurate results without rendering the simulation impractical.
Interpreting Results with Caution
Finally, it is important to interpret CAE results with caution, understanding that they are approximations of reality.
While CAE provides valuable insights, engineers must consider factors not accounted for in the simulations, such as manufacturing imperfections and environmental variations.
Validating results with experimental data whenever possible enhances confidence in the analysis and ensures robustness in design.
In conclusion, CAE has transformed strength analysis and design, offering powerful tools to optimize and validate engineering solutions.
By understanding the fundamentals and key considerations of CAE, engineers can harness its full potential, delivering products that are both safe and efficient.
資料ダウンロード
QCD調達購買管理クラウド「newji」は、調達購買部門で必要なQCD管理全てを備えた、現場特化型兼クラウド型の今世紀最高の購買管理システムとなります。
ユーザー登録
調達購買業務の効率化だけでなく、システムを導入することで、コスト削減や製品・資材のステータス可視化のほか、属人化していた購買情報の共有化による内部不正防止や統制にも役立ちます。
NEWJI DX
製造業に特化したデジタルトランスフォーメーション(DX)の実現を目指す請負開発型のコンサルティングサービスです。AI、iPaaS、および先端の技術を駆使して、製造プロセスの効率化、業務効率化、チームワーク強化、コスト削減、品質向上を実現します。このサービスは、製造業の課題を深く理解し、それに対する最適なデジタルソリューションを提供することで、企業が持続的な成長とイノベーションを達成できるようサポートします。
オンライン講座
製造業、主に購買・調達部門にお勤めの方々に向けた情報を配信しております。
新任の方やベテランの方、管理職を対象とした幅広いコンテンツをご用意しております。
お問い合わせ
コストダウンが利益に直結する術だと理解していても、なかなか前に進めることができない状況。そんな時は、newjiのコストダウン自動化機能で大きく利益貢献しよう!
(Β版非公開)