- お役立ち記事
- Basics of supply chain and risk management that new employees in the purchasing department should know
Basics of supply chain and risk management that new employees in the purchasing department should know
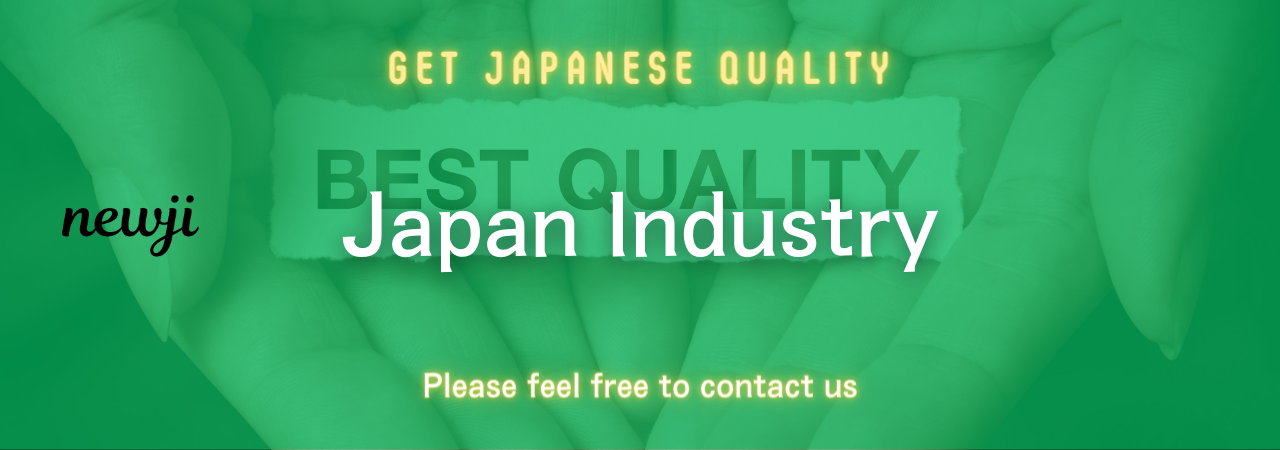
目次
Understanding Supply Chain Management
Supply chain management is an essential part of any business that deals with the production and distribution of goods.
It involves the coordination of various activities involved in delivering a product from the supplier to the customer.
For new employees in the purchasing department, understanding the basics of supply chain management is crucial.
This knowledge not only helps in procuring materials but also in ensuring the timely delivery of products to customers.
A supply chain is a network of suppliers, manufacturers, wholesalers, distributors, and retailers who work together to produce and distribute goods.
The goal of supply chain management is to improve efficiency, reduce costs, and increase customer satisfaction.
The Key Components of Supply Chain Management
To understand supply chain management, it’s critical to recognize its key components:
1. **Planning**: This is the step where companies decide how to operate the supply chain to produce goods that meet customer demand.
It involves forecasting demand, evaluating production capacity, and planning for resources.
2. **Sourcing**: This involves selecting suppliers that will provide the goods and services needed to create the product.
The purchasing department plays a crucial role in negotiating contracts and ensuring that suppliers meet standards.
3. **Manufacturing**: This is where the actual production happens.
It involves scheduling activities necessary for production, testing, packaging, and preparing for delivery.
4. **Delivery and Logistics**: This encompasses everything required to get the finished product into the hands of the consumers.
It involves warehousing, distribution, order management, and transportation.
5. **Returns**: Also known as reverse logistics, this process involves handling customer returns and defective products.
It ensures products are returned efficiently and appropriately handled or disposed of.
Importance of Risk Management in the Supply Chain
Risk management is an integral part of supply chain management.
It involves identifying, assessing, and mitigating risks that could disrupt the supply chain.
New employees in purchasing should be aware of the various types of risks and how to manage them effectively.
1. **Supply Risk**: This includes risks related to the inability of suppliers to meet demand.
It can stem from a variety of reasons, including natural disasters, political instability, or financial problems.
2. **Demand Risk**: This type of risk is associated with the unpredictable nature of consumer demand.
Changes in consumer preferences, economic downturns, and new market competitions can heavily impact demand.
3. **Operational Risk**: This involves risks related to internal processes, systems, or human errors.
For instance, a breakdown in communication between departments can lead to delays in production.
4. **Financial Risk**: Economic fluctuations, interest rate changes, and currency price changes can influence overall costs in the supply chain.
5. **Environmental Risk**: Risks related to environmental factors such as climate change, natural disasters, and environmental regulations.
These can impact suppliers and transportation routes.
Effective Strategies for Supply Chain Risk Management
Managing risks efficiently is key to a resilient supply chain.
Here are some strategies new purchasing employees can consider:
1. **Diversification of Suppliers**: Relying on a single supplier can be risky.
Building relationships with multiple suppliers in different locations can help mitigate risks associated with supplier disruptions.
2. **Demand Forecasting**: Use data analytics and modeling techniques to accurately forecast demand.
This will help in making informed inventory and procurement decisions.
3. **Invest in Technology**: Use supply chain management software to gain better visibility over the entire supply chain.
This helps in quickly identifying and addressing potential risks.
4. **Robust Communication**: Promote open communication channels among all stakeholders in the supply chain.
This helps in rapidly identifying issues and coordinating responses effectively.
5. **Establish Contingency Plans**: Prepare for potential disruptions by developing contingency plans.
Regularly update these plans based on new risks and changes in the market environment.
The Role of Purchasing in Supply Chain and Risk Management
Purchasing is a vital function within supply chain management.
It serves as the bridge between the company and its suppliers.
Purchasing teams are responsible for securing materials and services needed for production at the best possible terms.
Here’s how purchasing plays a critical role in the supply chain:
– **Supplier Relationship Management**: Building and maintaining strong relationships with suppliers ensures a smooth and reliable supply of materials.
– **Cost Management**: Purchasing teams work to negotiate contracts that keep costs low, thus enhancing the company’s profitability.
– **Quality Assurance**: They ensure that the materials procured meet the company’s quality standards and requirements.
– **Risk Mitigation**: By monitoring supplier performance and market trends, purchasing teams can identify potential risks and act proactively to mitigate them.
Understanding the basics of supply chain and risk management will greatly enhance the efficiency and effectiveness of new employees in the purchasing department.
As they grow into their roles, this knowledge will form a strong foundation for making informed decisions that contribute to the company’s success.
資料ダウンロード
QCD調達購買管理クラウド「newji」は、調達購買部門で必要なQCD管理全てを備えた、現場特化型兼クラウド型の今世紀最高の購買管理システムとなります。
ユーザー登録
調達購買業務の効率化だけでなく、システムを導入することで、コスト削減や製品・資材のステータス可視化のほか、属人化していた購買情報の共有化による内部不正防止や統制にも役立ちます。
NEWJI DX
製造業に特化したデジタルトランスフォーメーション(DX)の実現を目指す請負開発型のコンサルティングサービスです。AI、iPaaS、および先端の技術を駆使して、製造プロセスの効率化、業務効率化、チームワーク強化、コスト削減、品質向上を実現します。このサービスは、製造業の課題を深く理解し、それに対する最適なデジタルソリューションを提供することで、企業が持続的な成長とイノベーションを達成できるようサポートします。
オンライン講座
製造業、主に購買・調達部門にお勤めの方々に向けた情報を配信しております。
新任の方やベテランの方、管理職を対象とした幅広いコンテンツをご用意しております。
お問い合わせ
コストダウンが利益に直結する術だと理解していても、なかなか前に進めることができない状況。そんな時は、newjiのコストダウン自動化機能で大きく利益貢献しよう!
(Β版非公開)