- お役立ち記事
- Basics of surface hardening technology by heat treatment and its application to improve functionality
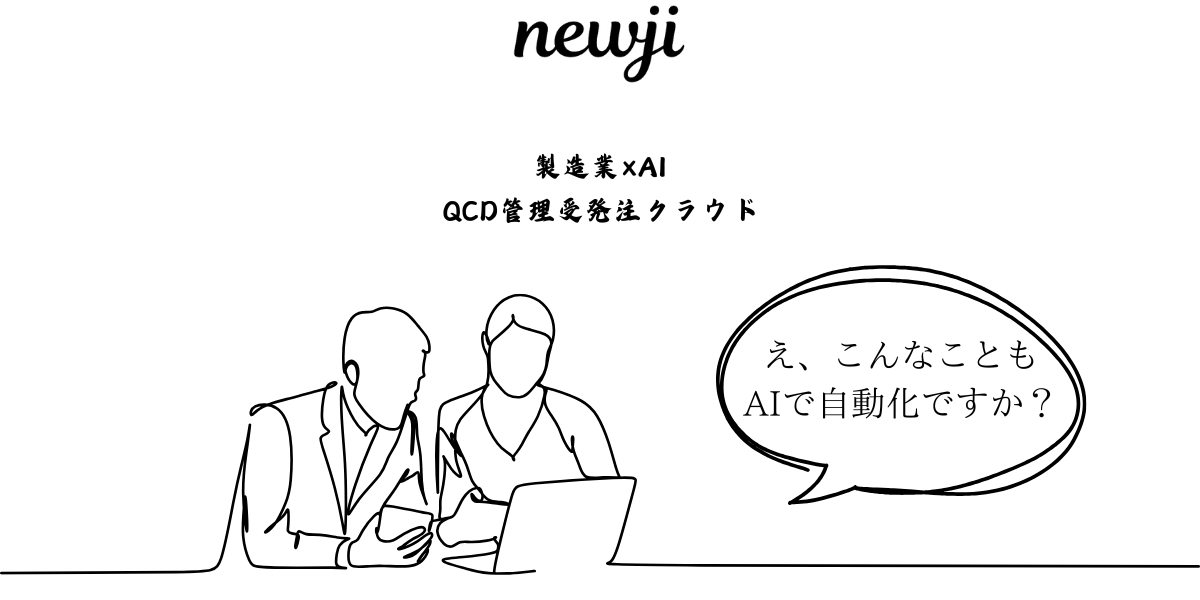
Basics of surface hardening technology by heat treatment and its application to improve functionality
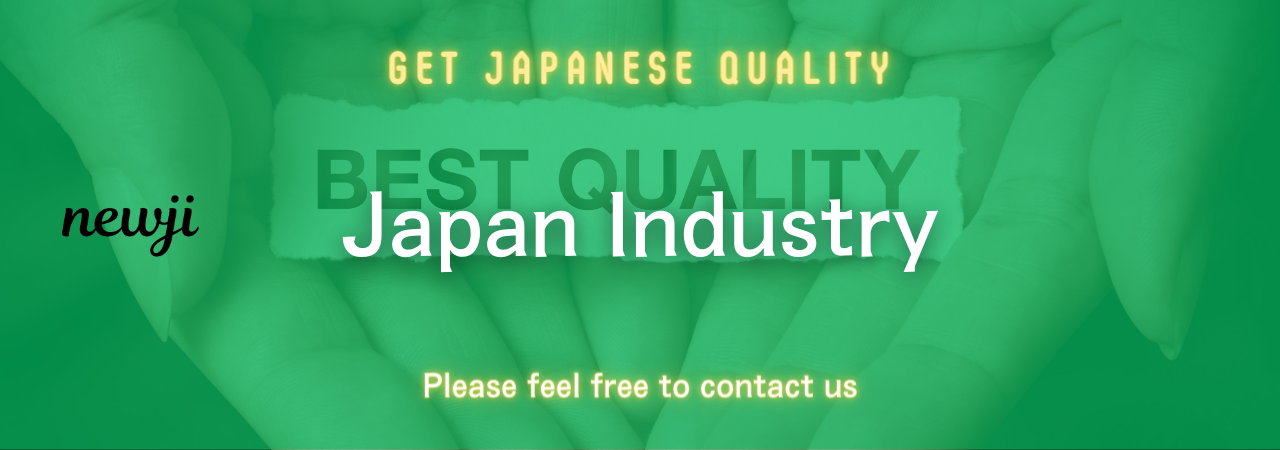
目次
Introduction to Surface Hardening Technology
Surface hardening is a heat treatment process that enhances the durability and wear resistance of metal components by altering their external surface properties.
This technology is vital in manufacturing as it extends the life of machinery parts, reduces maintenance costs, and improves overall functionality.
By providing an effective and efficient method to bolster the surface of metals, surface hardening allows manufacturers to optimize the performance of their products without compromising the innate properties of the core material.
The Basics of Heat Treatment
Heat treatment is a controlled process used to alter the physical and sometimes chemical properties of a material.
The main aim is to manufacture components that suit specific applications by enhancing desired material properties.
The process typically involves heating the material to a high temperature, maintaining a certain temperature to allow transformation, and then cooling it in a controlled manner.
This treatment is not bound to metals but applies to various materials, including glass and ceramics, however, our focus is primarily on metals.
Understanding Surface Hardening
Surface hardening, a subset of heat treatment, selectively hardens the surface of metal parts while leaving the core softer and ductile.
This duality in properties allows the component to withstand high levels of stress and abrasion on the surface while remaining tough and resilient internally.
The process involves transforming the external layer of the metal into a hardened case, increasing the lifespan and performance of the component in industrial applications.
Common Methods of Surface Hardening
There are several methods of surface hardening, each with its unique applications and benefits.
Some of the most widely used techniques include:
1. Case Hardening
Case hardening, sometimes referred to as carburizing, involves infusing the metal’s surface with carbon or nitrogen to create a tough exterior layer.
The process is typically carried out by heating the metal in the presence of a carbonaceous material, resulting in a hardened exterior that is resistant to wear and tear.
2. Induction Hardening
In induction hardening, an electromagnetic field is used to rapidly heat the outer layer of a metal part.
The process is finely controlled and swift, making it ideal for creating hardened surfaces on selected sections of a component.
Following heating, the metal is quickly cooled or quenched, forming a hard layer due to the rapid transformation induced by the temperature differential.
3. Flame Hardening
Flame hardening employs an open flame to heat the surface of a metal component.
Like induction hardening, flame hardening is used to selectively harden specific areas without affecting the entire part.
Once the surface reaches a suitable temperature, it is rapidly cooled, creating a hardened layer.
4. Nitriding
Nitriding is a process where nitrogen is diffused into the surface of the steel.
This process does not require quenching and is achieved at relatively lower temperatures compared to other methods.
Nitriding produces a very hard and wear-resistant surface, making it suitable for parts that operate under high heat and stress.
Applications of Surface Hardening in Industry
Surface hardening technologies are employed across various industries to enhance the functionalities and longevity of metal components.
Automotive Industry
In the automotive sector, surface hardening is used to strengthen gears, crankshafts, and camshafts, which are subject to constant wear and operational stress.
Through selective hardening, these parts achieve extended service lives, contributing to more reliable and efficient vehicle performance.
Manufacturing and Machinery
For manufacturing equipment and heavy machinery, surface hardening is crucial in the enhancement of cutting tools, dies, and punches.
These tools endure heavy-duty use and require robust resistance to surface wear.
The extended life of these components results in significant cost savings by reducing the frequency of replacement and downtime due to equipment failure.
Aerospace
In aerospace applications, components such as turbine blades and engine parts benefit from surface hardening to tolerate extreme temperatures and stress.
The precise balance of hardness and toughness provided by these processes assures the reliability and safety of aerospace components.
Improving Functionality through Surface Hardening
The fundamental principle of surface hardening is to improve the functionality of components by focusing on their specific operational requirements.
By understanding and applying the appropriate hardening technique, engineers can enhance surface wear resistance, increase fatigue strength, and maintain core ductility.
This targeted approach to strengthening specific sections of a component optimizes performance, reduces mechanical failures, and supports innovation in design.
Moreover, surface hardening adapts to both traditional and cutting-edge manufacturing, including 3D printing and additive manufacturing.
Components created through these technologies often require post-production enhancement of surface properties to meet industry standards and ensure durability.
Conclusion
Surface hardening by heat treatment is a transformative technology that underpins modern manufacturing across various sectors.
By focusing on surface durability while preserving the core characteristics, these processes significantly improve the functional performance of metal parts.
As technological advancements continue to enhance the precision and efficacy of surface hardening techniques, their applications and benefits are expected to expand, playing a crucial role in innovative manufacturing solutions.
Understanding and implementing these processes can lead to cost-effective, durable, and highly functional components that meet the demanding requirements of today’s industrial landscape.
資料ダウンロード
QCD調達購買管理クラウド「newji」は、調達購買部門で必要なQCD管理全てを備えた、現場特化型兼クラウド型の今世紀最高の購買管理システムとなります。
ユーザー登録
調達購買業務の効率化だけでなく、システムを導入することで、コスト削減や製品・資材のステータス可視化のほか、属人化していた購買情報の共有化による内部不正防止や統制にも役立ちます。
NEWJI DX
製造業に特化したデジタルトランスフォーメーション(DX)の実現を目指す請負開発型のコンサルティングサービスです。AI、iPaaS、および先端の技術を駆使して、製造プロセスの効率化、業務効率化、チームワーク強化、コスト削減、品質向上を実現します。このサービスは、製造業の課題を深く理解し、それに対する最適なデジタルソリューションを提供することで、企業が持続的な成長とイノベーションを達成できるようサポートします。
オンライン講座
製造業、主に購買・調達部門にお勤めの方々に向けた情報を配信しております。
新任の方やベテランの方、管理職を対象とした幅広いコンテンツをご用意しております。
お問い合わせ
コストダウンが利益に直結する術だと理解していても、なかなか前に進めることができない状況。そんな時は、newjiのコストダウン自動化機能で大きく利益貢献しよう!
(Β版非公開)