- お役立ち記事
- Basics of the latest plating technology, defect countermeasures, and quality improvement techniques
月間76,176名の
製造業ご担当者様が閲覧しています*
*2025年3月31日現在のGoogle Analyticsのデータより
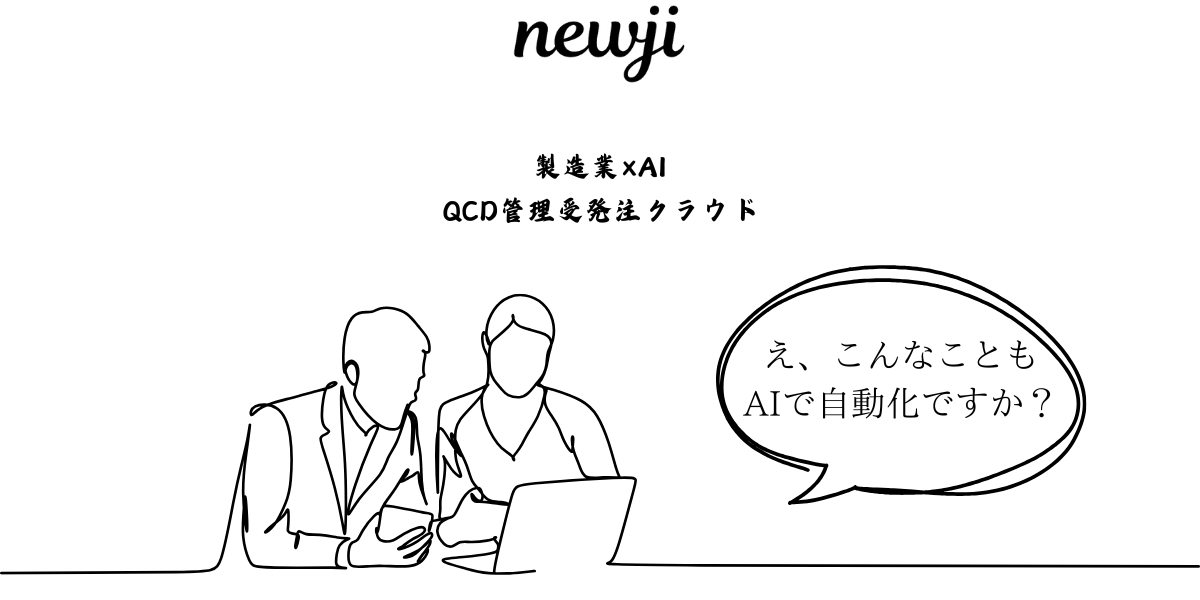
Basics of the latest plating technology, defect countermeasures, and quality improvement techniques
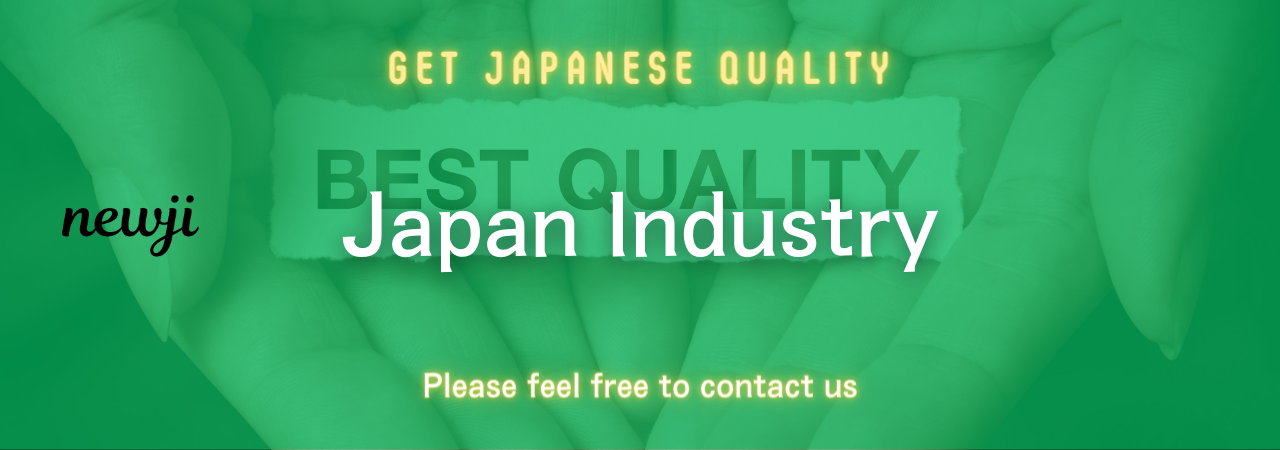
目次
Understanding the Basics of Latest Plating Technology
Plating technology has become an essential component in various manufacturing sectors, including electronics, automotive, and aerospace industries.
It involves depositing a metal coating on a surface to enhance its properties, such as corrosion resistance, electrical conductivity, and aesthetic appeal.
With the evolution of technology, the methods of plating have advanced significantly, offering better efficiency and quality.
The latest plating technologies incorporate high-precision processes that allow for minimal material usage while maximizing performance.
Some of the key plating methods include electroplating, electroless plating, and immersion plating.
Each of these techniques has distinct applications and benefits, depending on the desired outcomes.
Electroplating is perhaps the most common method, utilizing an electrical current to reduce metal cations dissolved in a solution to form a coherent metal coating on an electrode.
Electroless plating, on the other hand, relies on an autocatalytic reaction to deposit a metal layer without applying an external electrical power source.
Immersion plating is typically used for applying thin metal layers.
This method involves immersing the substrate into a plating solution, allowing the desired metal ions to displace substrate ions through a simple exchange process.
Each of these techniques is utilized based on specific industrial requirements and the characteristics of the materials involved.
Common Defects in Plating and Their Countermeasures
While plating offers numerous benefits, various defects can occur during the process, impacting the quality and functionality of the final product.
Understanding these defects and implementing effective countermeasures can help maintain high standards of quality.
One common defect is poor adhesion, which can result in the peeling or flaking of the metal coating.
To prevent this, it is crucial to ensure that the substrate surface is meticulously cleaned and prepared before the plating process.
Pre-treatment techniques such as degreasing, pickling, or using adhesion-promoting agents can significantly enhance coating adhesion.
Another defect is uneven plating thickness, which can affect the performance of the coated part.
Adjusting the plating bath composition and carefully monitoring the plating parameters, such as current density and bath temperature, can help achieve uniform thickness.
Pitting is yet another defect characterized by the formation of small cavities on the plated metal surface.
This can be minimized by incorporating proper agitation in the plating bath to avoid trapping air and impurities.
Additionally, maintaining stringent control over the plating bath’s chemical composition can help reduce the risk of pitting.
Discoloration or dull plating is also a concern, especially in decorative applications.
Optimizing the plating bath chemistry and imposing stringent control over operational conditions, like pH and temperature, can mitigate this issue.
Quality Improvement Techniques in Plating
Improving the quality of plated products is crucial for meeting stringent industrial standards and increasing competitiveness.
There are several strategies manufacturers can employ to elevate quality in plating processes.
One effective technique is adopting automated plating systems.
Automation ensures consistency and precision, significantly reducing the likelihood of human errors that can lead to plating defects.
Automated systems can control the plating bath composition, temperature, and current density, enhancing reproducibility.
Implementing real-time monitoring and control systems is another approach to quality improvement.
These systems can promptly detect anomalies or deviations from desired parameters, enabling quick corrective actions that ensure the plating process remains stable and within specifications.
Utilizing high-purity raw materials ensures the production of high-quality plated products.
Impurities in the plating bath can introduce defects like pitting or rough surfaces.
Sourcing high-grade chemicals and regularly replacing and filtering the plating solutions help maintain optimal quality.
Furthermore, introducing preventive maintenance schedules for plating equipment can mitigate unexpected downtimes and maintain process efficiency.
Regular inspections and maintenance of rectifiers, anodes, and filtration systems prolong the life of the equipment and ensure consistent plating quality.
Training and skill development for operators also play a critical role in ensuring quality.
Operators equipped with in-depth knowledge of plating technologies, defect identification, and mitigation strategies can significantly contribute to improving overall process outcomes.
The Role of Research and Development in Plating Technology
Research and development (R&D) in plating technology are pivotal in driving innovation and maintaining a competitive edge.
R&D initiatives focus on exploring new materials and processes that enhance the efficiency and environmental-friendliness of plating methods.
Efforts are being made to develop eco-friendly plating solutions that minimize or eliminate the use of hazardous substances such as cyanide and hexavalent chromium.
These solutions aim to reduce the environmental impact of plating while maintaining or improving product quality.
Advanced research also contributes to the development of nanotechnology-based coatings, which offer superior properties, including enhanced wear resistance and reduced friction.
These coatings extend the lifespan of components, particularly in harsh environments.
Collaborations between academic institutions and industry players facilitate the creation and dissemination of new knowledge and technologies.
Such partnerships help in addressing the evolving needs of the market and pave the way for future advancements in plating technology.
Conclusion
The advancements in plating technology offer substantial benefits to various industries by improving product durability, functionality, and appearance.
However, to fully capitalize on these benefits, understanding the common plating defects and implementing effective quality improvement techniques is essential.
Continued investment in research and development will foster the growth of innovative and sustainable plating solutions, ensuring that industries can meet modern demands with superior quality products.
By leveraging these insights, manufacturers can enhance their processes, ultimately leading to improved competitiveness in the global market.
資料ダウンロード
QCD管理受発注クラウド「newji」は、受発注部門で必要なQCD管理全てを備えた、現場特化型兼クラウド型の今世紀最高の受発注管理システムとなります。
ユーザー登録
受発注業務の効率化だけでなく、システムを導入することで、コスト削減や製品・資材のステータス可視化のほか、属人化していた受発注情報の共有化による内部不正防止や統制にも役立ちます。
NEWJI DX
製造業に特化したデジタルトランスフォーメーション(DX)の実現を目指す請負開発型のコンサルティングサービスです。AI、iPaaS、および先端の技術を駆使して、製造プロセスの効率化、業務効率化、チームワーク強化、コスト削減、品質向上を実現します。このサービスは、製造業の課題を深く理解し、それに対する最適なデジタルソリューションを提供することで、企業が持続的な成長とイノベーションを達成できるようサポートします。
製造業ニュース解説
製造業、主に購買・調達部門にお勤めの方々に向けた情報を配信しております。
新任の方やベテランの方、管理職を対象とした幅広いコンテンツをご用意しております。
お問い合わせ
コストダウンが利益に直結する術だと理解していても、なかなか前に進めることができない状況。そんな時は、newjiのコストダウン自動化機能で大きく利益貢献しよう!
(β版非公開)