- お役立ち記事
- Basics of tolerance design/design calculations and trouble prevention measures
月間76,176名の
製造業ご担当者様が閲覧しています*
*2025年3月31日現在のGoogle Analyticsのデータより
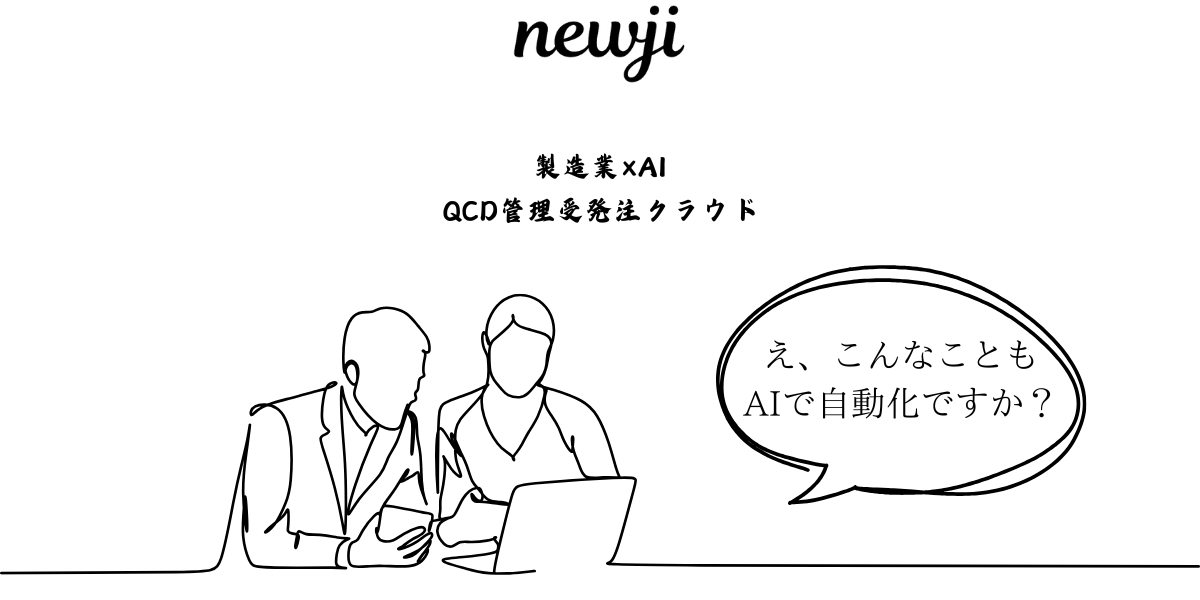
Basics of tolerance design/design calculations and trouble prevention measures
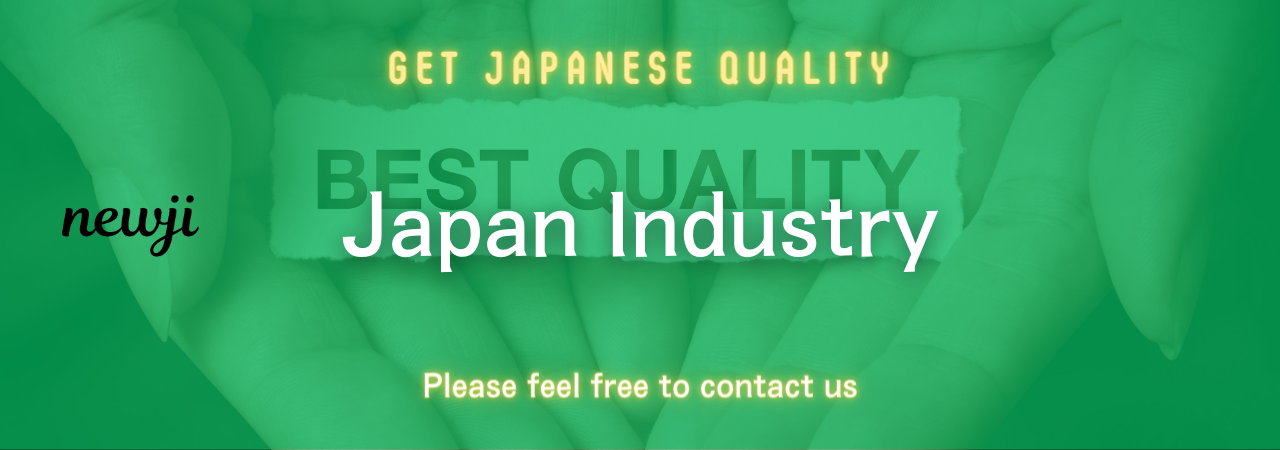
目次
Understanding Tolerance Design
Tolerance design is a fundamental aspect of engineering and manufacturing, playing a crucial role in ensuring that parts fit together correctly and function as intended.
At its core, tolerance design specifies the allowable limits of variation in a physical dimension, which can be due to manufacturing processes or material properties.
The main aim of tolerance design is to balance product performance with cost efficiency.
Too tight a tolerance can lead to increased manufacturing costs due to the need for precision machining, while too loose a tolerance could result in parts that do not fit or function properly.
Understanding how to apply tolerance design effectively involves knowledge of design calculations, material properties, and the manufacturing processes involved.
The Importance of Design Calculations
Design calculations are integral to setting appropriate tolerances.
These calculations help engineers predict the performance of a component under specific conditions and determine the dimensional limits within which it will operate reliably.
Failure to perform accurate design calculations can lead to costly errors, such as parts not fitting together or a product that fails prematurely.
Several key factors influence design calculations, including load conditions, material properties, and environmental factors such as temperature and humidity.
Accurately assessing these factors ensures that tolerances are not only achievable but also meet functional requirements.
For instance, when designing a gear, calculations must ensure that the teeth can withstand the forces they will encounter without excessive wear.
If tolerances are set too tightly, the gears might not mesh correctly; if too loosely, they might generate noise or fail under load.
Common Challenges in Tolerance Design
Designing with tolerances presents several challenges, particularly when dealing with complex assemblies or when working on innovative new products.
One common challenge is maintaining dimensional accuracy across different parts and materials, each of which can behave differently under manufacturing or operating conditions.
Material inconsistencies can affect how a part expands or contracts.
As such, the properties of the materials being used must be carefully considered when setting tolerances.
Materials like metals and plastics have different rates of thermal expansion, which must be accounted for in the design stage.
Another challenge is the cumulative effect of tolerances in an assembly.
When multiple parts come together, each with its own tolerance, these can add up, potentially leading to functional issues.
This is known as tolerance stack-up, and managing it requires careful planning and design calculation.
Strategies for Managing Tolerance Problems
Managing tolerance issues effectively involves employing several strategies.
One approach is to use a combination of computer-aided design and simulation tools to model the assembly’s behavior before production.
These tools enable the visualization of how parts will interact, allowing engineers to identify and address potential tolerance issues early in the design process.
Another strategy is to design for adjustability.
This can involve adding features that allow for some degree of movement or adjustment during assembly, helping to compensate for tolerance variations.
Such designs ensure that even if parts are slightly out of tolerance, the final assembly will still function as intended.
Additionally, employing statistical methods such as Six Sigma can enhance tolerance design.
These methods focus on reducing variability in manufacturing processes, which can help keep parts within the desired tolerance range.
Trouble Prevention Measures in Tolerance Design
Preventing problems related to tolerance design involves both proactive and reactive measures.
Proactively, engineers must conduct thorough design reviews and prototype testing to ensure that tolerances are feasible and functional.
Regular communication between design, manufacturing, and quality assurance teams is also critical to address potential issues swiftly.
Design reviews are vital for identifying potential tolerance challenges early on.
By assembling a diverse team with expertise in various areas of the product lifecycle, companies can ensure that a wide range of perspectives and insights are brought to bear, significantly reducing the likelihood of oversight.
On the reactive side, having a robust quality assurance process that includes inspections and testing can help catch tolerance issues before products reach the consumer.
This process often includes using precision measurement tools to verify that parts meet specified tolerances and function properly under real-world conditions.
The Role of Continuous Improvement in Tolerance Design
Continuous improvement is another essential component of effective tolerance design.
Regularly revisiting and refining the design process can help identify areas for improvement, reducing both costs and the likelihood of errors.
Implementing feedback loops, where information from manufacturing defects or customer feedback leads to design modifications, can also enhance tolerance design.
By analyzing this data, companies can gain insights into where processes can be optimized or updated to maintain product quality.
Moreover, investing in employee training and development ensures that engineering teams remain aware of the latest best practices and technologies in tolerance design.
Educated engineers are better equipped to set accurate tolerances, foresee potential issues, and devise creative solutions.
In conclusion, mastery of tolerance design is critical for producing functional, reliable, and cost-effective products.
It requires a solid understanding of design calculations, challenges associated with manufacturing variations, and effective problem-prevention measures.
Organizations that invest in robust tolerance design practices can significantly enhance product quality, improve efficiency, and maintain competitive advantage in the marketplace.
資料ダウンロード
QCD管理受発注クラウド「newji」は、受発注部門で必要なQCD管理全てを備えた、現場特化型兼クラウド型の今世紀最高の受発注管理システムとなります。
ユーザー登録
受発注業務の効率化だけでなく、システムを導入することで、コスト削減や製品・資材のステータス可視化のほか、属人化していた受発注情報の共有化による内部不正防止や統制にも役立ちます。
NEWJI DX
製造業に特化したデジタルトランスフォーメーション(DX)の実現を目指す請負開発型のコンサルティングサービスです。AI、iPaaS、および先端の技術を駆使して、製造プロセスの効率化、業務効率化、チームワーク強化、コスト削減、品質向上を実現します。このサービスは、製造業の課題を深く理解し、それに対する最適なデジタルソリューションを提供することで、企業が持続的な成長とイノベーションを達成できるようサポートします。
製造業ニュース解説
製造業、主に購買・調達部門にお勤めの方々に向けた情報を配信しております。
新任の方やベテランの方、管理職を対象とした幅広いコンテンツをご用意しております。
お問い合わせ
コストダウンが利益に直結する術だと理解していても、なかなか前に進めることができない状況。そんな時は、newjiのコストダウン自動化機能で大きく利益貢献しよう!
(β版非公開)