- お役立ち記事
- Basics of topology optimization and how to use it with 3D printers
Basics of topology optimization and how to use it with 3D printers
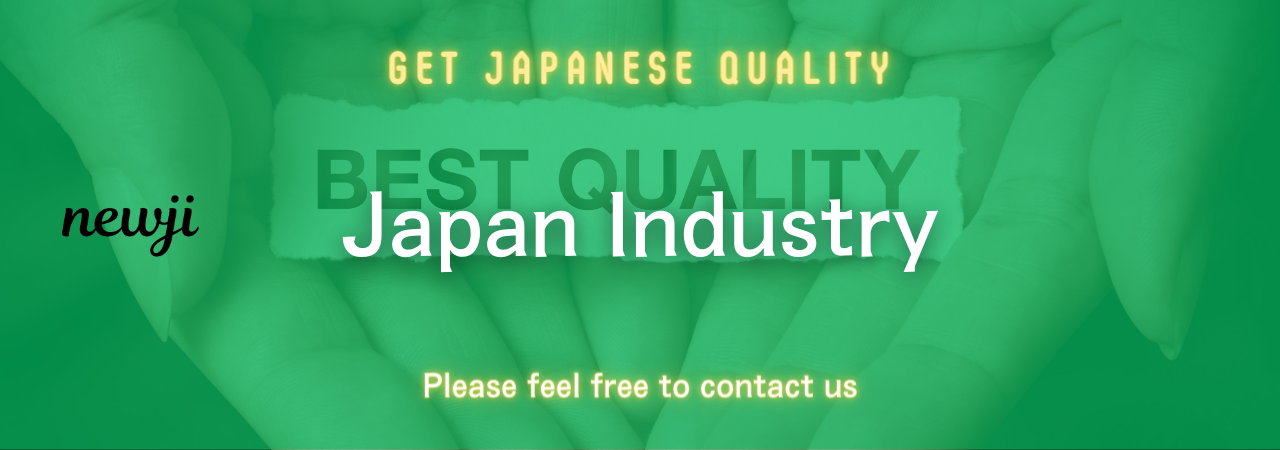
目次
Understanding Topology Optimization
Topology optimization is a powerful mathematical method used in engineering to optimize the material distribution within a given design space.
The primary goal is to create structures that maximize performance while minimizing material usage.
This process improves the functionality and sustainability of designs by identifying the best configurations for specific requirements.
In topology optimization, engineers and designers input the design parameters, constraints, and objectives.
The algorithm then generates optimized structures, which often have complex shapes that traditional engineering methods might not naturally conceive.
This approach allows for innovative solutions that improve strength, reduce weight, and achieve desired performance levels.
Key Concepts in Topology Optimization
To fully grasp topology optimization, it’s essential to understand some of its fundamental concepts.
The three core components of this method are the design domain, the objective function, and constraints.
Design Domain
The design domain refers to the space where material distribution can be optimized.
It encompasses the boundaries within which the material can be placed.
This space is typically defined by the dimensions of the desired object or component and any fixed boundaries or interfaces that are part of the design.
Objective Function
The objective function in topology optimization defines the goal of the optimization process.
Common objectives include minimizing weight, maximizing strength, minimizing material usage, or optimizing the structural performance of a component under specific load conditions.
The objective function guides the optimization algorithm by determining how different design iterations are evaluated and ranked.
Constraints
Constraints are the limitations placed on the design to ensure it meets specific criteria.
These can include physical restrictions, such as manufacturing capabilities or load-bearing requirements, as well as additional criteria like cost or material availability.
Constraints help ensure that the optimized design is both practical and feasible for real-world applications.
Benefits of Topology Optimization
Topology optimization offers several advantages over traditional design methods, making it a valuable tool for engineers and designers.
Enhanced Performance
By optimizing the material distribution, topology optimization creates designs that maximize performance while minimizing waste.
This leads to stronger, more efficient structures that can better withstand loads and stresses, ultimately improving the durability and longevity of the component.
Material Efficiency
One of the most significant advantages of topology optimization is its potential to reduce material consumption.
By identifying unnecessary material and eliminating it, designers can create components that are lighter and require less raw material.
This not only reduces production costs but also minimizes environmental impact by conserving resources.
Innovative Design Solutions
Topology optimization allows for the exploration of unconventional design solutions.
The resulting structures often have organic shapes that are challenging to conceive through traditional design methods.
This creative freedom can lead to groundbreaking innovations in fields like aerospace, automotive, and biomedical engineering.
Compatibility with 3D Printing
The rise of 3D printing technology has made it easier to realize the complex shapes generated by topology optimization.
Additive manufacturing techniques can produce intricate geometries with minimal waste, making them ideal for deploying optimized designs.
The compatibility between topology optimization and 3D printing offers an exciting opportunity for pushing the boundaries of engineering and design.
How to Use Topology Optimization with 3D Printers
Integrating topology optimization with 3D printing requires a series of steps that overlap both digital and physical manufacturing processes.
Define Design Specifications
Start by clearly defining the design requirements, including the design domain, load conditions, and any essential constraints.
This information serves as the foundation for the topology optimization process and ensures that the final design meets all necessary criteria.
Run Topology Optimization Software
Numerous software packages are available that specialize in topology optimization.
These programs utilize advanced algorithms to evaluate countless design iterations and identify the optimal material distribution.
Once the input parameters are set, the software will produce an optimized design that meets the specified objectives and constraints.
Refine the Design
After the topology optimization process, the resulting design might require additional refinement.
This could involve smoothing surfaces, ensuring all features are manufacturable, and reinforcing specific areas.
Refinement is crucial to ensure the design not only meets performance goals but is also suitable for production.
Prepare for 3D Printing
Once refined, convert the digital model into a format compatible with 3D printers, such as a stereolithography (.STL) file.
This preparation includes deciding on the material and settings for the printing process.
Understanding the nuances of the chosen 3D printing technology helps ensure accurate reproduction of the optimized design.
3D Print the Final Design
With the model ready, the final step is to 3D print the optimized design.
Depending on the complexity and purpose of the design, it may be necessary to conduct multiple prints to verify and test performance outcomes.
This iterative process allows for further refinement based on physical testing and evaluation.
Conclusion
Topology optimization is a transformative tool in modern engineering and design.
By leveraging advanced algorithms and innovative techniques, it maximizes structural performance while minimizing material usage and waste.
When combined with 3D printing, topology optimization unlocks the potential for creating intricate, highly efficient components that traditional manufacturing struggles to achieve.
Understanding the fundamental principles of topology optimization and how to effectively integrate them with 3D printing can give engineers and designers a significant advantage in realizing innovative and sustainable solutions.
As the technology continues to advance, the possibilities for topology optimization and 3D printing are virtually limitless, driving the future of design and production.
資料ダウンロード
QCD調達購買管理クラウド「newji」は、調達購買部門で必要なQCD管理全てを備えた、現場特化型兼クラウド型の今世紀最高の購買管理システムとなります。
ユーザー登録
調達購買業務の効率化だけでなく、システムを導入することで、コスト削減や製品・資材のステータス可視化のほか、属人化していた購買情報の共有化による内部不正防止や統制にも役立ちます。
NEWJI DX
製造業に特化したデジタルトランスフォーメーション(DX)の実現を目指す請負開発型のコンサルティングサービスです。AI、iPaaS、および先端の技術を駆使して、製造プロセスの効率化、業務効率化、チームワーク強化、コスト削減、品質向上を実現します。このサービスは、製造業の課題を深く理解し、それに対する最適なデジタルソリューションを提供することで、企業が持続的な成長とイノベーションを達成できるようサポートします。
オンライン講座
製造業、主に購買・調達部門にお勤めの方々に向けた情報を配信しております。
新任の方やベテランの方、管理職を対象とした幅広いコンテンツをご用意しております。
お問い合わせ
コストダウンが利益に直結する術だと理解していても、なかなか前に進めることができない状況。そんな時は、newjiのコストダウン自動化機能で大きく利益貢献しよう!
(Β版非公開)