- お役立ち記事
- Basics of torque control and product applications that new employees in the design department of the power tool manufacturing industry should know
Basics of torque control and product applications that new employees in the design department of the power tool manufacturing industry should know
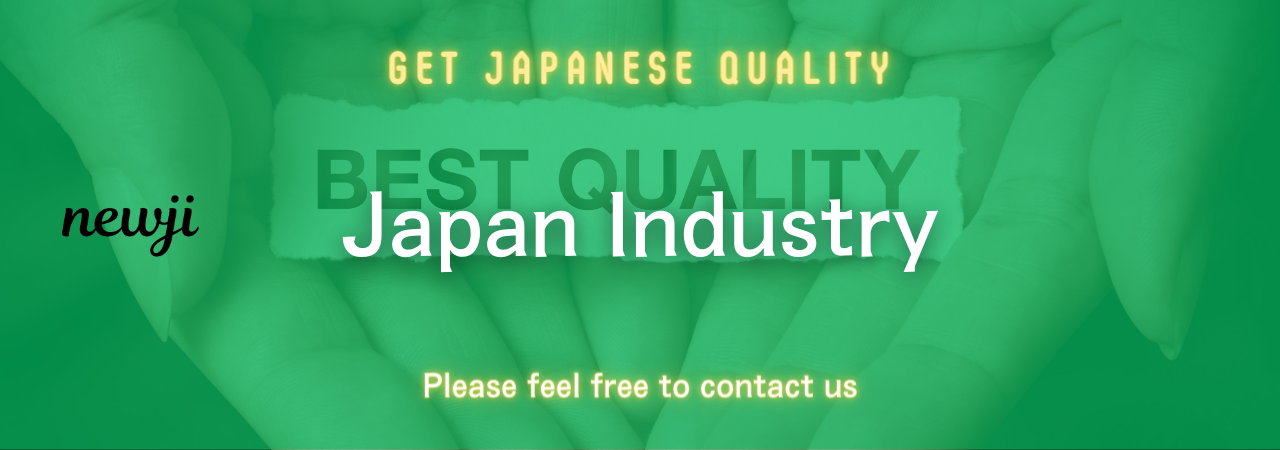
目次
Understanding Torque Control
Torque control is an essential concept within the design department of the power tool manufacturing industry.
It refers to the process of managing and regulating the power or force that causes rotation.
Torque is essentially the measure of how much force acting on an object causes that object to rotate.
In the context of power tools, this means controlling the force applied to fasteners or workpieces to ensure they are tightened or loosened to the correct specifications.
Torque is measured in units such as pound-feet (lb-ft) or newton-meters (Nm).
The proper control of torque is crucial, as it prevents issues such as fastener deformation or failure, and ensures a safe and efficient working environment.
For new employees in the design department, a strong understanding of torque is indispensable, as it plays a critical role in product performance and reliability.
Importance of Torque Control in Power Tools
Using power tools without appropriate torque control can lead to several issues.
Over-tightening can strip threads and damage both the tool and the material it’s being used on.
On the other hand, under-tightening can result in parts not being securely fastened, which can pose safety risks and affect product functionality.
Torque control in power tools ensures precision and repeatability in tasks.
This precision is particularly important in fields such as automotive or aerospace engineering, where components often need to be fastened with specific torque settings.
By understanding torque control, designers can create tools that meet these exacting standards, improving customer satisfaction and product reputation.
Types of Torque Control Mechanisms
There are various mechanisms used in the design of power tools to achieve torque control.
Understanding these can help new employees design more effective products.
Mechanical Clutches
Mechanical clutches are one of the oldest forms of torque control used in power tools.
They operate by disengaging the drive mechanism once a set torque level is met.
This mechanism is highly reliable and easy to service, making it a staple in many power tool designs.
Electronic Torque Control
With advancements in technology, electronic torque control systems have become prevalent.
These systems use sensors and microprocessors to precisely monitor torque levels and adjust power output accordingly.
They provide greater accuracy and flexibility compared to mechanical clutches and can be programmed for different applications.
Hydraulic and Pneumatic Systems
Hydraulic and pneumatic systems are often used in industrial settings where high torque applications are required.
These systems rely on fluid or air pressure to control torque, offering precise control in demanding environments.
Applications of Torque Control in Product Design
New employees should be aware that torque control plays a critical role in various stages of product design and application.
Designing for User Safety
Incorporating torque control not only enhances tool performance but also ensures user safety.
By preventing over-tightening, torque-controlled tools reduce the risk of stripping or breaking fasteners, which can lead to accidents.
Understanding how to integrate torque control effectively into products can be a valuable skill for designers.
Quality Assurance and Regulatory Standards
Products with proper torque control align with industry standards and regulations, which often specify torque requirements for specific applications.
Designing tools that adhere to these standards is crucial to pass quality assurance tests and avoid legal issues.
Improving Product Lifespan
Correct torque control can also extend the life of both the tool and the materials it is used on.
By ensuring that fasteners are tightened to the correct specifications, undue stress on the components is minimized, leading to a longer lifespan.
Challenges and Solutions in Torque Control
Torque control presents several challenges for designers, but understanding these can help new design employees create innovative solutions.
Dealing with Torque Variability
Factors such as thread condition, lubrication, and environmental conditions can affect torque.
To counteract these variabilities, advanced sensors and algorithms can be incorporated into tool designs to provide adaptive torque control.
Cost versus Precision
High precision torque control systems can significantly increase production costs.
Designers must balance the need for accuracy with affordability to create competitive products.
Achieving this balance might involve selecting the appropriate mechanisms that offer necessary precision without unnecessary expense.
Maintaining Tool Ergonomics
When adding torque control mechanisms, it’s important to maintain the tool’s ergonomic design.
Making tools heavier or more cumbersome can reduce efficiency and user comfort.
New designers should strive to integrate torque control features without compromising the tool’s usability.
The Future of Torque Control in Power Tools
As technology continues to advance, so too will the methods of torque control in power tools.
Smart Tool Integration
The rise of smart technology sees the integration of advanced torque control features such as data tracking and feedback systems.
These systems not only control torque but also provide users and manufacturers with valuable data to monitor usage and improve tools continually.
Eco-Friendly Innovations
Developing tools with enhanced torque control can help in sustainable practices.
By reducing waste and energy consumption through precision control, power tool manufacturers can contribute to environmental conservation efforts.
For new employees in the design department, understanding the basics of torque control and its applications is vital.
With the right knowledge and skills, they can contribute to designing innovative, safe, and efficient power tools that meet the demands of modern industries.
資料ダウンロード
QCD調達購買管理クラウド「newji」は、調達購買部門で必要なQCD管理全てを備えた、現場特化型兼クラウド型の今世紀最高の購買管理システムとなります。
ユーザー登録
調達購買業務の効率化だけでなく、システムを導入することで、コスト削減や製品・資材のステータス可視化のほか、属人化していた購買情報の共有化による内部不正防止や統制にも役立ちます。
NEWJI DX
製造業に特化したデジタルトランスフォーメーション(DX)の実現を目指す請負開発型のコンサルティングサービスです。AI、iPaaS、および先端の技術を駆使して、製造プロセスの効率化、業務効率化、チームワーク強化、コスト削減、品質向上を実現します。このサービスは、製造業の課題を深く理解し、それに対する最適なデジタルソリューションを提供することで、企業が持続的な成長とイノベーションを達成できるようサポートします。
オンライン講座
製造業、主に購買・調達部門にお勤めの方々に向けた情報を配信しております。
新任の方やベテランの方、管理職を対象とした幅広いコンテンツをご用意しております。
お問い合わせ
コストダウンが利益に直結する術だと理解していても、なかなか前に進めることができない状況。そんな時は、newjiのコストダウン自動化機能で大きく利益貢献しよう!
(Β版非公開)