- お役立ち記事
- Basics of TPM activities and effective equipment maintenance techniques that new leaders of equipment technology departments should learn
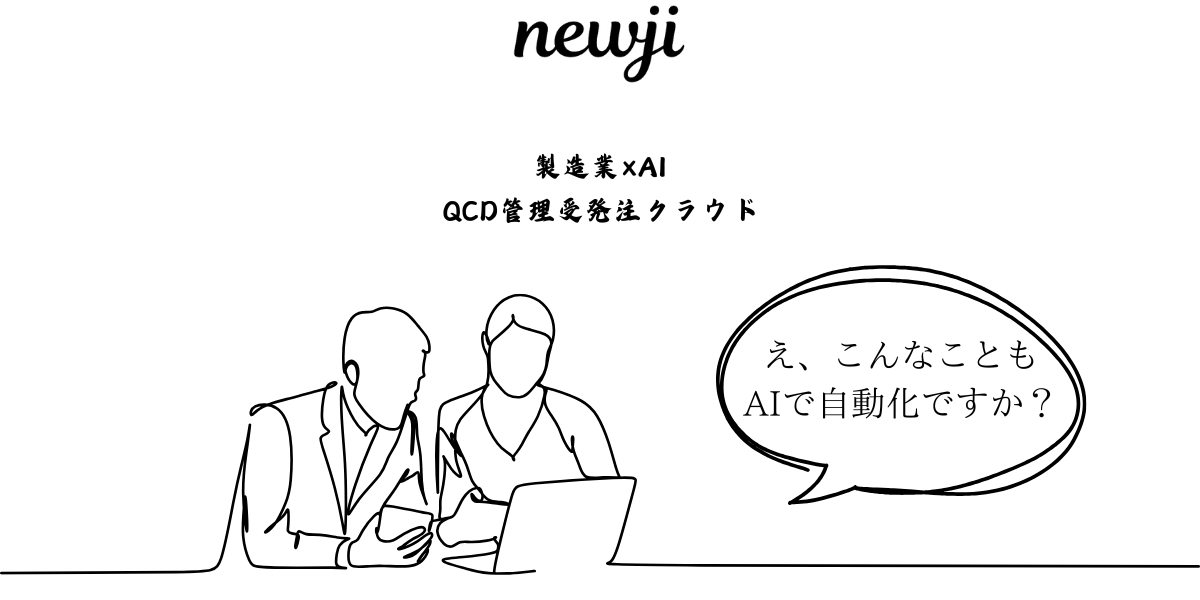
Basics of TPM activities and effective equipment maintenance techniques that new leaders of equipment technology departments should learn
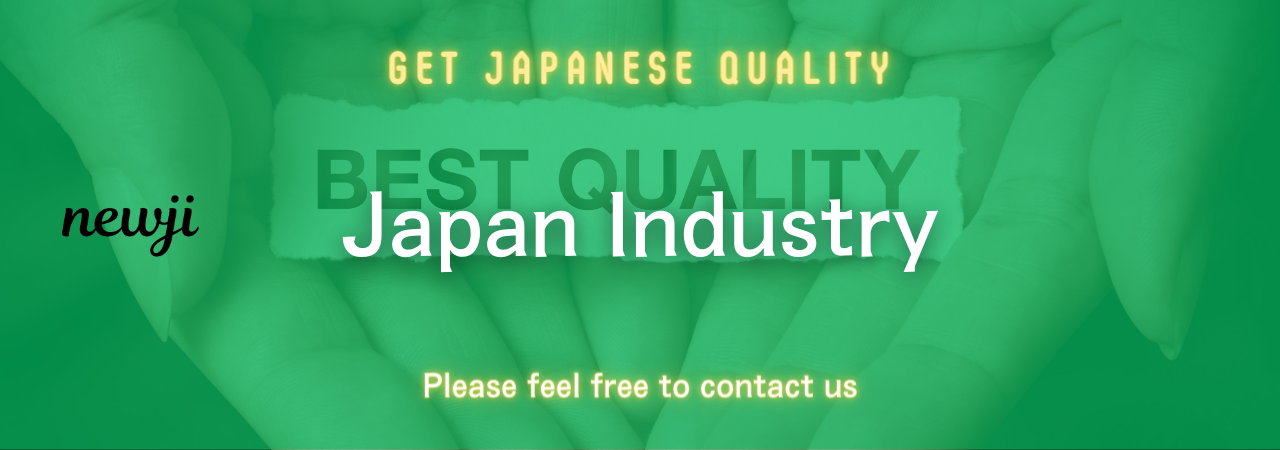
目次
Understanding TPM Activities
Total Productive Maintenance (TPM) is a holistic approach to equipment maintenance that aims to achieve perfect production.
This means no breakdowns, no small stops, and no defects.
TPM encapsulates the idea that everyone in the organization needs to participate in maintenance activities.
In TPM, operators are encouraged to be involved in their own equipment care, which fosters a sense of ownership and responsibility.
This involvement leads to proactive upkeep and early problem identification, which are critical for reducing unexpected downtime.
Regular training and skills development are essential to implementing TPM effectively, ensuring that all employees can contribute meaningfully.
TPM comprises several pillars, each focused on different aspects of equipment maintenance.
Understanding these pillars is crucial for new leaders in equipment technology departments.
The Pillars of TPM
TPM is built on eight foundational pillars that ensure comprehensive coverage of all aspects of equipment care.
1. **Autonomous Maintenance**:
Operators are trained to take responsibility for basic maintenance tasks like cleaning, lubricating, and inspecting their machines.
This empowers them and can significantly reduce equipment malfunctions.
2. **Planned Maintenance**:
This involves scheduling maintenance activities based on machine data, usage history, or seasonal changes.
Planned maintenance helps in reducing unexpected breakdowns and lengthens equipment lifespan.
3. **Quality Maintenance**:
Focused on identifying and eliminating causes of quality defects.
It involves setting quality standards and ensuring equipment operates within those parameters.
4. **Focused Improvement**:
Also known as continuous improvement, this pillar focuses on small, incremental changes to improve efficiency and productivity.
Brainstorming sessions and collaborative problem-solving are common practices here.
5. **Early Equipment Management**:
Integration of maintenance considerations in the design and installation stages of new equipment.
This ensures that new machinery is easy to maintain and operates efficiently from day one.
6. **Training and Education**:
Training programs for employees helps in improving their skills and understanding of equipment maintenance requirements.
Education fosters a culture of continuous learning and competency development.
7. **Safety, Health, and Environment**:
Ensures that maintenance activities do not compromise the safety of employees or the environment.
Maintenance procedures are reviewed to ensure they meet safety standards.
8. **TPM in Administration**:
Extending TPM principles to administrative functions to eliminate waste and improve operational efficiency across the organization.
Effective Equipment Maintenance Techniques
Maintaining equipment effectively requires a mix of traditional and modern techniques.
Adopting these techniques can significantly impact productivity and cost-effectiveness.
Predictive Maintenance
Predictive maintenance involves using data and analytics to predict equipment failures before they occur.
Technologies like sensors and IoT (Internet of Things) devices collect real-time data on equipment performance.
This data is then analyzed to identify patterns and signs of wear and tear.
New leaders should ensure that predictive maintenance technologies are integrated to minimize downtime.
It requires investing in software and training employees to interpret data accurately and take timely action.
Root Cause Analysis (RCA)
When a problem occurs, performing a Root Cause Analysis is crucial.
RCA is a systematic process used to identify the root causes of faults or problems.
It involves asking why the problem occurred and digging deeper until the fundamental issue is uncovered.
By understanding the root cause, you can implement solutions that prevent the problem from recurring.
New leaders should encourage a culture of problem-solving and learning from past mistakes.
Regular Inspections and Audits
Scheduled inspections and audits play a vital role in the maintenance strategy.
Regular checks help in identifying hidden issues and verifying that maintenance procedures are followed correctly.
Leaders should establish clear schedules for inspections and ensure that all equipment is audited for compliance with safety and operational standards.
Standardized Work Procedures
Standardizing work procedures ensures that maintenance tasks are performed uniformly.
Documentation of processes allows team members to follow the best practices and ensures consistency.
This standardization reduces errors and ensures high-quality maintenance work.
New leaders should ensure that all employees are trained in and adhere to these standardized procedures.
Building a Culture of Maintenance Excellence
For TPM to be truly effective, it’s essential to foster a culture where every team member understands the importance of maintenance.
Encouraging Open Communication
Facilitate open communication channels where operators and maintenance personnel can share insights and provide feedback.
Understanding challenges faced on the shop floor can help in developing effective solutions.
Recognition and Incentives
Recognizing and rewarding employees for their proactive maintenance efforts can boost morale and encourage continuous improvement.
Incentives can motivate teams to achieve higher standards and strive for excellence.
Continuous Learning and Improvement
Commit to ongoing training programs and workshops that keep the team updated with the latest maintenance techniques and technologies.
Promoting a continuous improvement mindset aligns with the TPM philosophy.
Conclusion
As a new leader in the equipment technology department, mastering TPM activities and effective maintenance techniques is a critical part of driving your team towards increased productivity and efficiency.
By embracing a comprehensive maintenance strategy, integrating modern technologies, and fostering a culture of excellence, you can ensure that your equipment operates reliably and contributes positively to your organization’s success.
資料ダウンロード
QCD調達購買管理クラウド「newji」は、調達購買部門で必要なQCD管理全てを備えた、現場特化型兼クラウド型の今世紀最高の購買管理システムとなります。
ユーザー登録
調達購買業務の効率化だけでなく、システムを導入することで、コスト削減や製品・資材のステータス可視化のほか、属人化していた購買情報の共有化による内部不正防止や統制にも役立ちます。
NEWJI DX
製造業に特化したデジタルトランスフォーメーション(DX)の実現を目指す請負開発型のコンサルティングサービスです。AI、iPaaS、および先端の技術を駆使して、製造プロセスの効率化、業務効率化、チームワーク強化、コスト削減、品質向上を実現します。このサービスは、製造業の課題を深く理解し、それに対する最適なデジタルソリューションを提供することで、企業が持続的な成長とイノベーションを達成できるようサポートします。
オンライン講座
製造業、主に購買・調達部門にお勤めの方々に向けた情報を配信しております。
新任の方やベテランの方、管理職を対象とした幅広いコンテンツをご用意しております。
お問い合わせ
コストダウンが利益に直結する術だと理解していても、なかなか前に進めることができない状況。そんな時は、newjiのコストダウン自動化機能で大きく利益貢献しよう!
(Β版非公開)