- お役立ち記事
- Basics of TPM activities and effective maintenance methods for equipment that new employees in the equipment management department should know
Basics of TPM activities and effective maintenance methods for equipment that new employees in the equipment management department should know
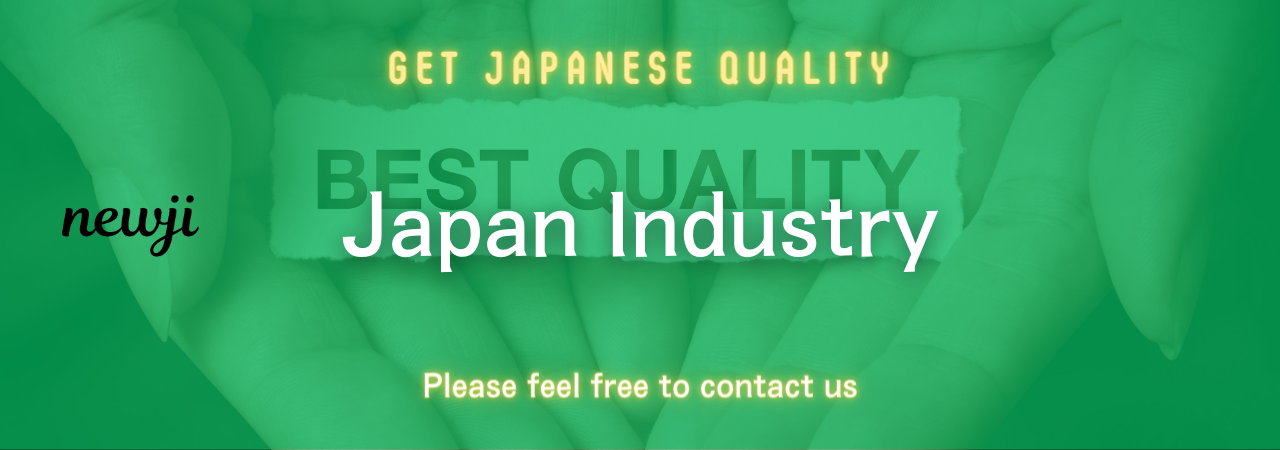
目次
Understanding TPM Activities
Total Productive Maintenance, commonly known as TPM, is an approach designed to improve the overall efficiency and productivity of equipment within an organization.
At its core, TPM aims to eliminate losses related to equipment and process failures.
These losses can include unplanned downtime, reduced speed, and quality defects, all of which can significantly impact the bottom line of any company.
TPM is not just a maintenance initiative; it is a holistic approach that involves everyone in the organization, from operators to management.
The aim is to promote a culture of shared responsibility for equipment maintenance and operational efficiency.
For new employees in the equipment management department, understanding TPM activities is crucial.
These activities are the foundation upon which efficient maintenance practices are built.
The Pillars of TPM
TPM is structured around eight foundational pillars, each serving a unique role in ensuring the optimal performance of equipment:
1. Autonomous Maintenance
Autonomous maintenance empowers operators to take part in routine maintenance tasks.
These tasks may include cleaning, inspecting, and lubricating equipment.
The objective is to foster a sense of ownership among operators, allowing them to identify irregularities and report them early.
2. Focused Improvement
This pillar emphasizes collective problem-solving efforts.
Teams identify equipment inefficiencies or areas requiring improvement and collaborate on developing strategic solutions.
The essence is continuous improvement, aiming to eliminate losses and improve the output quality.
3. Planned Maintenance
This aspect of TPM schedules maintenance activities based on data analysis and historical records.
By preemptively conducting maintenance, the likelihood of unexpected equipment failures can be reduced, ensuring smooth operation.
4. Quality Maintenance
Quality maintenance focuses on consistently producing high-quality products.
It involves setting high equipment performance standards and ensuring all equipment operates within these parameters.
5. Early Equipment Management
When new equipment is introduced, early equipment management ensures it is effectively integrated into existing systems.
This involves collaboration between design, manufacturing, and maintenance teams to ensure that new equipment is designed with maintainability in mind.
6. Training and Education
Knowledge is power, especially when it comes to equipment maintenance.
Training ensures that everyone involved is equipped with the necessary skills and information to perform their roles efficiently.
It is especially critical for new employees who must familiarize themselves with specific equipment and maintenance processes.
7. Safety, Health, and Environment
Safety is non-negotiable in any workplace.
This pillar ensures that all maintenance activities are conducted safely, with the well-being of employees and environmental considerations in mind.
8. TPM in Administration
While TPM is often associated with the production floor, its principles can also enhance administrative functions.
Streamlining administrative processes can lead to increased efficiency and reduced waste.
Effective Maintenance Methods
Understanding TPM is one part of the equation; implementing effective maintenance methods is another crucial step.
Here are some key maintenance strategies that new employees should be aware of:
1. Preventive Maintenance
Preventive maintenance involves routine checks and repairs based on a predetermined schedule to prevent potential failures.
This method is proactive, focusing on keeping equipment in optimal condition rather than waiting for issues to arise.
2. Predictive Maintenance
This method relies on condition monitoring tools and technologies to predict when equipment might fail.
By analyzing data trends, maintenance can be performed just in time, thereby minimizing downtime and extending equipment life.
3. Corrective Maintenance
Corrective maintenance occurs after an equipment failure is detected.
While this might seem reactive, it often involves implementing solutions to prevent recurrence, thus aligning with TPM’s goal of continuous improvement.
4. Reliability-Centered Maintenance (RCM)
RCM is a structured process that identifies what needs to be done for equipment to perform reliably.
It balances the cost of maintenance with the cost of failure, ensuring resources are used efficiently.
Integrating New Employees into TPM Practices
The effectiveness of TPM hinges on collective effort and collaboration across all levels of the organization.
New employees play a vital role in this framework, and here’s how they can be integrated effectively:
Onboarding and Training
A comprehensive onboarding process can effectively introduce new hires to TPM principles and practices.
By familiarizing themselves with the company’s equipment and maintenance routines, new employees can understand their roles within the larger TPM framework.
Mentorship and Shadowing
Pairing new employees with experienced workers can offer practical insights and real-world understanding.
Through shadowing, new hires can see TPM principles in action, enabling them to grasp the nuances of equipment maintenance.
Engagement in Improvement Initiatives
Encouraging new employees to participate in focused improvement activities can foster a culture of innovation and ownership.
Involvement in initiatives allows them to contribute fresh perspectives while learning from seasoned team members.
Regular Feedback and Development
Regular feedback sessions can help track the progress of new employees in their understanding and implementation of TPM activities.
Providing constructive feedback and identifying areas for growth encourages a learning mindset essential for embracing TPM.
Conclusion
Understanding the basics of TPM and effective maintenance methods is crucial for new employees in the equipment management department.
TPM is more than a set of maintenance procedures; it is a culture that empowers every member of the organization to contribute to the efficiency and productivity of equipment.
By embracing its pillars, employing strategic maintenance methods, and effectively integrating new employees, organizations can achieve significant improvements in equipment performance and overall operational success.
資料ダウンロード
QCD調達購買管理クラウド「newji」は、調達購買部門で必要なQCD管理全てを備えた、現場特化型兼クラウド型の今世紀最高の購買管理システムとなります。
ユーザー登録
調達購買業務の効率化だけでなく、システムを導入することで、コスト削減や製品・資材のステータス可視化のほか、属人化していた購買情報の共有化による内部不正防止や統制にも役立ちます。
NEWJI DX
製造業に特化したデジタルトランスフォーメーション(DX)の実現を目指す請負開発型のコンサルティングサービスです。AI、iPaaS、および先端の技術を駆使して、製造プロセスの効率化、業務効率化、チームワーク強化、コスト削減、品質向上を実現します。このサービスは、製造業の課題を深く理解し、それに対する最適なデジタルソリューションを提供することで、企業が持続的な成長とイノベーションを達成できるようサポートします。
オンライン講座
製造業、主に購買・調達部門にお勤めの方々に向けた情報を配信しております。
新任の方やベテランの方、管理職を対象とした幅広いコンテンツをご用意しております。
お問い合わせ
コストダウンが利益に直結する術だと理解していても、なかなか前に進めることができない状況。そんな時は、newjiのコストダウン自動化機能で大きく利益貢献しよう!
(Β版非公開)