- お役立ち記事
- Basics of TQM (Total Quality Management)
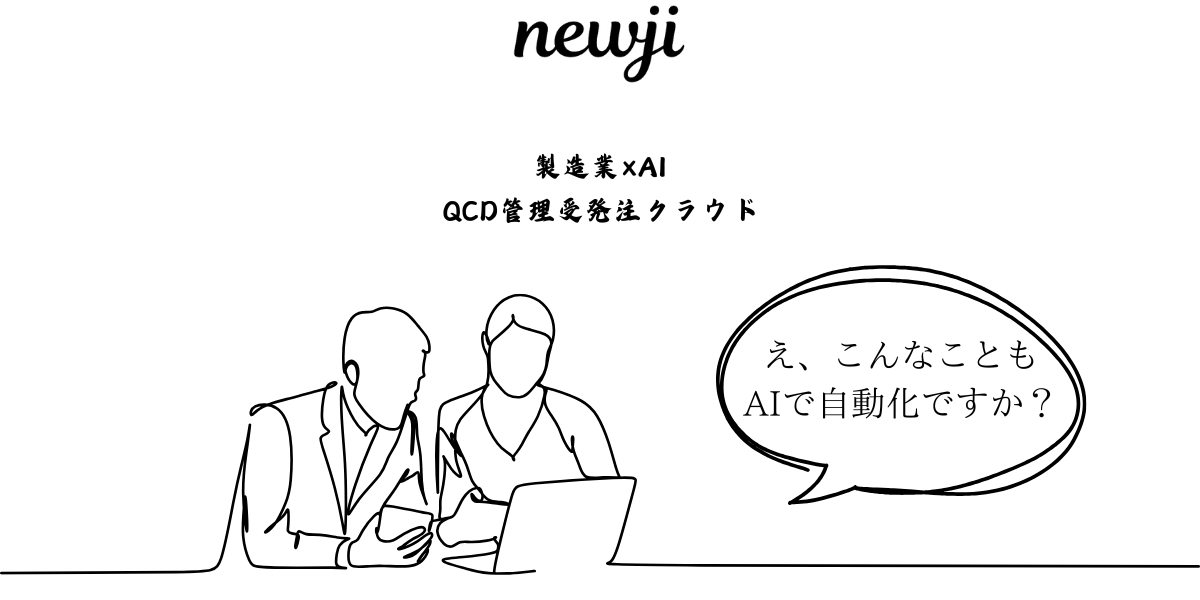
Basics of TQM (Total Quality Management)
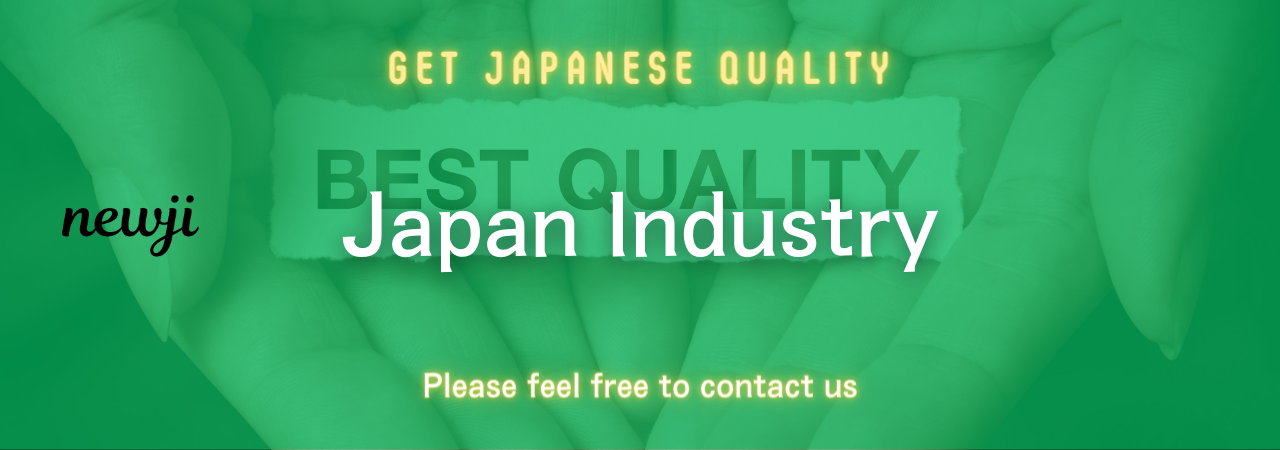
Total Quality Management, often abbreviated as TQM, is a structured approach to long-term success through customer satisfaction.
In this article, we’ll dive into the basics of TQM—what it is, its principles, and its benefits.
Whether you’re a business leader or someone interested in organizational management, understanding TQM can be incredibly beneficial.
目次
What is Total Quality Management?
Total Quality Management is a management strategy aimed at embedding awareness of quality in all organizational processes.
It involves a cultural shift where every employee is committed to improving quality and maintaining high standards.
This approach encompasses all aspects of the organization, from the products and services offered to the interactions between employees and customers.
TQM is built on the idea that long-term success is achieved through customer satisfaction.
This requires continuous improvement in all areas of the organization.
The ultimate aim is to cultivate an environment where improvement is ongoing and ingrained in the company culture.
Principles of TQM
To understand TQM better, let’s look at its key principles.
Customer Focus
At the heart of TQM is an unwavering focus on the customer.
The goal is to meet and exceed customer expectations consistently.
This requires understanding customer needs and aligning the organizational processes to fulfill these requirements.
Total Employee Involvement
For TQM to be effective, every employee must be involved and committed.
This includes top management as well as frontline workers.
An inclusive workplace culture fosters better teamwork, communication, and collaboration.
People are empowered to take responsibility and make decisions that contribute to quality improvement.
Process-Centered Approach
In TQM, the focus is on processes.
A process-centered approach means understanding and managing interrelated processes as a system.
Focusing on the process helps in identifying areas of improvement and making the necessary changes to enhance quality.
Integrated System
TQM views an organization as a unified whole, composed of interconnected processes.
This holistic view ensures that the organization’s goals and objectives are consistently met.
Every department should align with these overarching goals to achieve cohesive quality improvement.
Strategic and systematic approach
A strategic and systematic approach to improving quality involves setting long-term goals and objectives.
These goals should align with the organization’s vision and mission.
A systematic method ensures that these goals are achieved efficiently.
Continual Improvement
TQM is all about continuous improvement.
In an ever-changing business environment, standing still can mean falling behind.
Continuous improvement keeps an organization adaptable and responsive to new challenges and opportunities.
Fact-Based Decision Making
In TQM, decisions are made based on solid data and analysis.
Rather than relying on gut instinct, organizations use statistical tools and techniques to drive decision-making.
This helps in identifying trends, understanding problems, and finding effective solutions.
Communication
Effective communication is crucial in TQM.
Clear, open channels of communication ensure that everyone is aware of quality goals and their role in achieving them.
It helps in building trust and commitment among employees.
Benefits of TQM
Implementing Total Quality Management comes with a plethora of benefits.
Here are some of the key advantages:
Improved Customer Satisfaction
By focusing on customer needs and delivering consistent quality, organizations can significantly enhance customer satisfaction.
Satisfied customers are more likely to become loyal, repeat customers, and may even recommend the business to others.
Enhanced Operational Efficiency
A process-centered approach leads to better efficiency.
By continually improving processes, organizations can eliminate waste, reduce errors, and increase productivity.
Better Employee Engagement
When employees are involved and empowered, their job satisfaction increases.
A committed workforce is more motivated and productive, making meaningful contributions to the organization.
Higher Market Share
Organizations that successfully implement TQM often see a rise in their market share.
Delivering high-quality products and services helps differentiate the business from competitors.
Cost Reduction
Quality improvements often lead to cost savings.
Reduced waste, fewer errors, and more efficient processes translate into lower operational costs.
Challenges in Implementing TQM
While TQM offers numerous benefits, implementing it is not without its challenges.
Here are a few obstacles organizations might face:
Resistance to Change
One of the biggest challenges can be resistance from employees.
People are often comfortable with the status quo and may be reluctant to adopt new practices.
Lack of Management Commitment
For TQM to be successful, commitment from top management is crucial.
Without their support, it’s hard to foster a culture of continuous improvement.
Inadequate Training
Employees need to be adequately trained in TQM principles and practices.
Without proper training, they may not fully understand their role in the quality improvement process.
Poor Communication
Effective implementation requires clear and open communication.
Without it, employees might not be fully aware of the TQM goals and their responsibilities.
Conclusion
Total Quality Management is a powerful strategy for achieving long-term success through customer satisfaction.
By adhering to its principles—such as customer focus, total employee involvement, and continual improvement—organizations can reap numerous benefits.
While there may be challenges, the rewards of implementing TQM far outweigh the obstacles.
Understanding the basics of TQM is the first step toward creating a culture of quality in your organization.
It’s a journey of continuous improvement, where every member is committed to enhancing quality in every facet of the organization.
資料ダウンロード
QCD調達購買管理クラウド「newji」は、調達購買部門で必要なQCD管理全てを備えた、現場特化型兼クラウド型の今世紀最高の購買管理システムとなります。
ユーザー登録
調達購買業務の効率化だけでなく、システムを導入することで、コスト削減や製品・資材のステータス可視化のほか、属人化していた購買情報の共有化による内部不正防止や統制にも役立ちます。
NEWJI DX
製造業に特化したデジタルトランスフォーメーション(DX)の実現を目指す請負開発型のコンサルティングサービスです。AI、iPaaS、および先端の技術を駆使して、製造プロセスの効率化、業務効率化、チームワーク強化、コスト削減、品質向上を実現します。このサービスは、製造業の課題を深く理解し、それに対する最適なデジタルソリューションを提供することで、企業が持続的な成長とイノベーションを達成できるようサポートします。
オンライン講座
製造業、主に購買・調達部門にお勤めの方々に向けた情報を配信しております。
新任の方やベテランの方、管理職を対象とした幅広いコンテンツをご用意しております。
お問い合わせ
コストダウンが利益に直結する術だと理解していても、なかなか前に進めることができない状況。そんな時は、newjiのコストダウン自動化機能で大きく利益貢献しよう!
(Β版非公開)