- お役立ち記事
- Basics of transportation risks and quality control that new employees in the purchasing department need to know
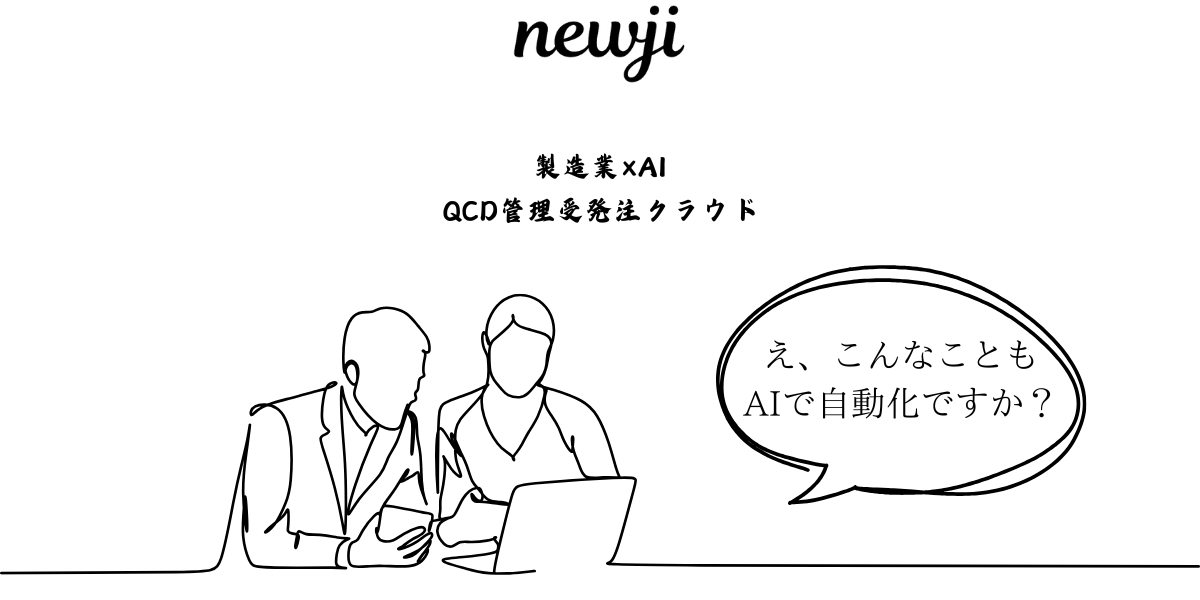
Basics of transportation risks and quality control that new employees in the purchasing department need to know
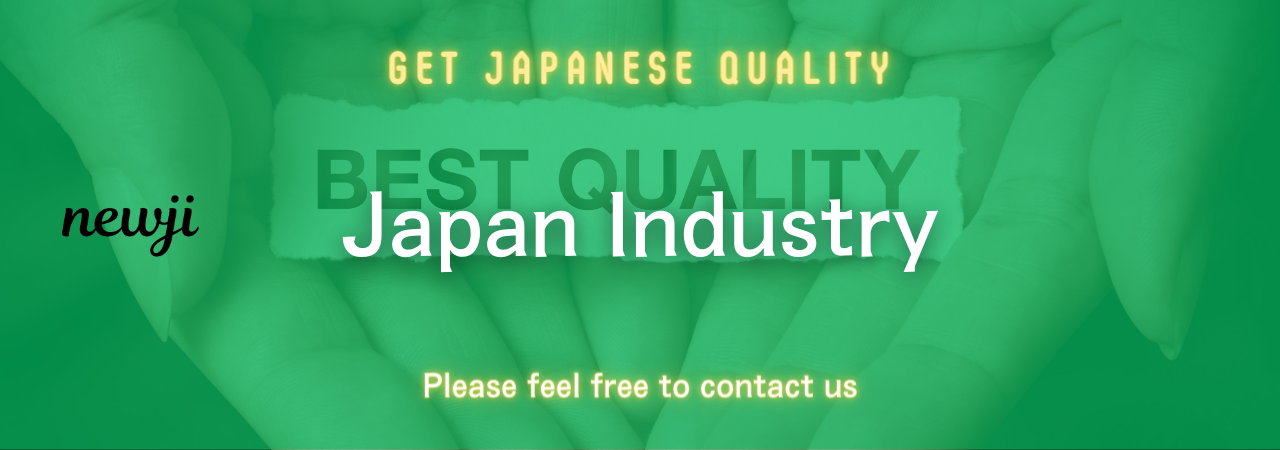
目次
Understanding Transportation Risks
Transportation risks refer to potential challenges and uncertainties that can occur during the movement of goods from one location to another.
These risks can have a significant impact on the purchasing and supply chain process, affecting delivery schedules, costs, and overall customer satisfaction.
As a new employee in the purchasing department, understanding these risks is crucial to ensuring smooth operations and maintaining high-quality standards.
From traffic congestion to unforeseen weather conditions, transportation risks vary and can disrupt the flow of goods, leading to delayed shipments and an increase in costs.
New employees must recognize these challenges and learn strategies to mitigate their effects.
Types of Transportation Risks
1. **Traffic and Congestion:** One of the most common transportation risks is traffic delays, particularly in urban areas, which can result in longer transit times and delayed deliveries.
2. **Environmental Factors:** Weather-related events such as snowstorms, floods, or hurricanes can cause delays or damage to goods in transit.
3. **Equipment and Vehicle Breakdowns:** Mechanical issues with transportation equipment can be unpredictable and lead to delivery delays or the need for emergency logistics solutions.
4. **Regulatory Changes:** Changes in transportation regulations or customs requirements can impact the movement of goods across borders and affect delivery timelines.
5. **Security Threats:** The risk of theft, vandalism, or terrorism presents a security concern for goods in transit, potentially leading to financial losses and delays.
Mitigating Transportation Risks
Mitigating transportation risks involves understanding their possible impact and implementing strategies to reduce their likelihood or lessen their consequences.
1. **Route Planning and Optimization:** Planning optimal routes and using real-time traffic data can help avoid congestion and reduce transit times, thereby mitigating the risk of delays.
2. **Weather Monitoring:** Keeping an eye on weather forecasts and having contingency plans in place can help manage risks associated with adverse environmental conditions.
3. **Regular Maintenance Checks:** Keeping transportation vehicles in good working order through regular maintenance can minimize the risk of mechanical breakdowns during transit.
4. **Compliance and Training:** Staying updated with regulatory requirements and ensuring staff training can help mitigate risks associated with changes in transport laws and regulations.
5. **Security Measures:** Implementing security protocols and using technology like GPS tracking can help reduce the risk of theft and enhance the overall security of shipments.
Quality Control in Transportation
Quality control ensures that the goods being transported meet the required standards and specifications before they reach the end customer.
For the purchasing department, maintaining quality throughout the transportation process is vital to customer satisfaction and brand reputation.
Failing to manage quality can lead to goods being damaged, spoiled, or lost, and result in financial losses and strained supplier relationships.
New employees must familiarize themselves with quality control practices to ensure their company’s success.
Key Elements of Quality Control
1. **Inspection at Dispatch and Receipt:** Conducting thorough inspections of goods at both dispatch and receipt ensures that any damages or discrepancies are promptly identified and addressed.
2. **Temperature Control:** For perishable goods, maintaining appropriate temperature control is critical to preserving quality during transit.
3. **Proper Packaging:** Ensuring that goods are properly packed and secured can prevent damage during transportation and handling.
4. **Inventory Tracking:** Using inventory tracking systems can help monitor the movement of goods and provide real-time updates to stakeholders about the status of shipments.
5. **Supplier Communication:** Building strong relationships and maintaining open lines of communication with suppliers can help quickly resolve issues related to the quality of goods delivered.
Maintaining High Standards
Maintaining high standards in quality control requires a proactive approach and ongoing vigilance.
1. **Continuous Improvement:** Regularly reviewing and refining quality control processes can help identify areas for improvement and ensure they remain effective.
2. **Feedback Loops:** Establishing feedback mechanisms with customers and suppliers can provide valuable insights into potential quality issues and areas for enhancement.
3. **Standard Operating Procedures (SOPs):** Developing and enforcing SOPs can standardize quality control practices across the organization and ensure consistency.
4. **Skill Development:** Providing training and skill development opportunities for staff can keep them updated on best practices in quality control.
5. **Technology Utilization:** Leveraging technology, such as automated tracking and monitoring systems, can enhance the precision and efficiency of quality control efforts.
Conclusion
As a new employee in the purchasing department, understanding transportation risks and quality control is essential for managing the complex logistics of moving goods.
Recognizing potential transportation risks and implementing strategies to mitigate them can reduce disruptions in the supply chain.
Similarly, integrating effective quality control measures can help uphold the brand’s reputation by ensuring that goods arrive in optimal condition.
By learning these foundational concepts, new employees can contribute to smooth and efficient operations within their organization.
Remember, the key to success lies in continuous learning and adapting to evolving logistics challenges.
資料ダウンロード
QCD調達購買管理クラウド「newji」は、調達購買部門で必要なQCD管理全てを備えた、現場特化型兼クラウド型の今世紀最高の購買管理システムとなります。
ユーザー登録
調達購買業務の効率化だけでなく、システムを導入することで、コスト削減や製品・資材のステータス可視化のほか、属人化していた購買情報の共有化による内部不正防止や統制にも役立ちます。
NEWJI DX
製造業に特化したデジタルトランスフォーメーション(DX)の実現を目指す請負開発型のコンサルティングサービスです。AI、iPaaS、および先端の技術を駆使して、製造プロセスの効率化、業務効率化、チームワーク強化、コスト削減、品質向上を実現します。このサービスは、製造業の課題を深く理解し、それに対する最適なデジタルソリューションを提供することで、企業が持続的な成長とイノベーションを達成できるようサポートします。
オンライン講座
製造業、主に購買・調達部門にお勤めの方々に向けた情報を配信しております。
新任の方やベテランの方、管理職を対象とした幅広いコンテンツをご用意しております。
お問い合わせ
コストダウンが利益に直結する術だと理解していても、なかなか前に進めることができない状況。そんな時は、newjiのコストダウン自動化機能で大きく利益貢献しよう!
(Β版非公開)