- お役立ち記事
- Basics of vibration, rotor vibration reduction measures and troubleshooting
月間77,185名の
製造業ご担当者様が閲覧しています*
*2025年2月28日現在のGoogle Analyticsのデータより
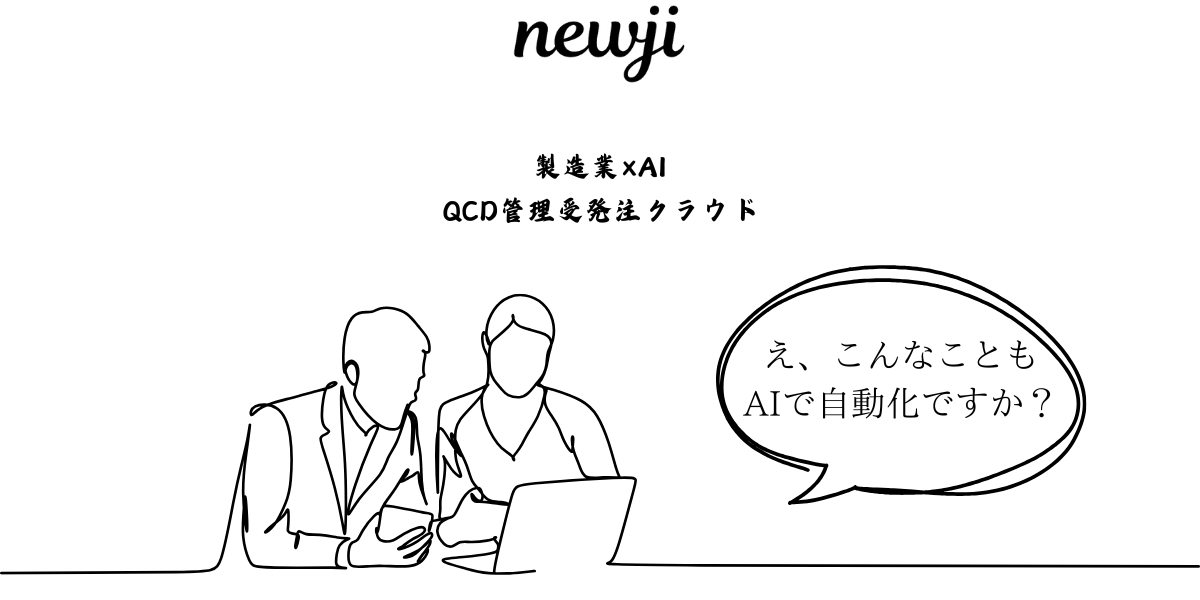
Basics of vibration, rotor vibration reduction measures and troubleshooting
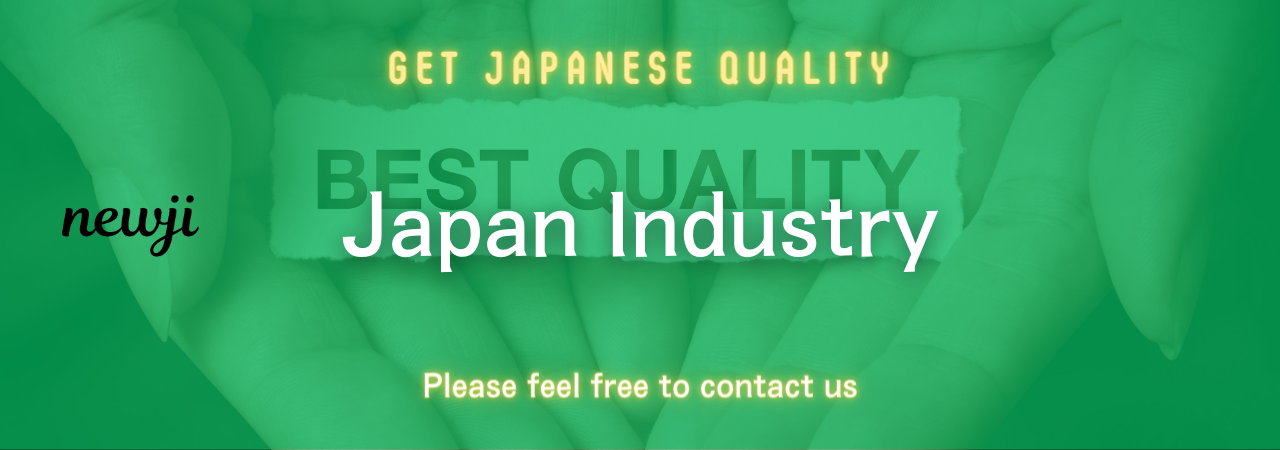
目次
Understanding Vibration
Vibration is a phenomenon that we encounter in our daily lives, although we might not always be aware of it.
In simple terms, vibration refers to the oscillation or repetitive motion of an object around an equilibrium point.
This motion can occur in different forms, like back-and-forth or up-and-down.
Vibrations can be classified into two main types: free vibration and forced vibration.
Free Vibration
Free vibration occurs when an object is set into motion and then allowed to vibrate on its own without any external force acting on it.
A simple example of free vibration is a swinging pendulum.
Once it’s pushed, it continues to oscillate until it gradually comes to rest due to friction and air resistance.
Forced Vibration
Forced vibration, on the other hand, takes place when an external force continuously acts on the object, causing it to vibrate.
A common example of this is a vibrating washing machine.
As the motor runs, it generates forces that cause the machine to vibrate.
Rotor Vibration Reduction Measures
Rotors are critical components in machinery that often experience vibration.
Excessive rotor vibration can lead to mechanical failures and reduced operational efficiency.
Therefore, it’s vital to implement measures to reduce or control these vibrations.
Regular Maintenance
One of the first steps in reducing rotor vibration is regular maintenance.
This includes checking for misalignments, imbalances, and wear and tear of components.
Proper lubrication and ensuring that bolts and fittings are secure can also minimize vibration.
Balancing
Balancing is a crucial technique in reducing rotor vibrations.
It involves adjusting the distribution of mass around the rotor to ensure that it rotates smoothly.
Unbalanced rotors can lead to excessive vibration, which might cause damage to the machinery.
Vibration Damping
Vibration damping techniques are used to absorb or reduce the amplitude of vibrations.
Materials like rubber, dampers, or vibration isolators can be installed to significantly decrease vibration transmission.
Alignment
Proper alignment of the rotor with other connected components is essential.
Misalignment can lead to increased vibration levels, which in turn cause mechanical stress and potential failures.
Precision alignment tools are often used to ensure optimal alignment.
Monitoring Systems
Installing vibration monitoring systems can aid in detecting issues early.
These systems can alert operators to any sudden changes in vibration levels, allowing quick intervention and preventive maintenance.
Troubleshooting Vibration Issues
When dealing with vibration issues, it is crucial to have a systematic approach to identify and solve the problems.
Here’s a step-by-step guide to troubleshooting vibration issues:
Identify the Symptoms
Start by identifying the symptoms of excessive vibration.
This could be unusual noises, increased temperatures, or physical vibrations felt by operators.
Documenting these symptoms helps in narrowing down the potential causes.
Measure Vibration
Use vibration measurement tools to assess the current vibration levels.
These tools, like accelerometers or vibration analyzers, provide precise data on vibration patterns and amplitudes.
Analyze the Data
Carefully analyze the vibration data to identify patterns or abnormalities.
Look for any frequencies that stand out, which might indicate specific issues such as misalignment or imbalance.
Inspect the Machinery
Perform a thorough inspection of the machinery.
Check for visible signs of wear and tear, damaged components, or out-of-place parts.
Consider using non-destructive testing methods for detecting internal faults.
Implement Solutions
Based on the findings, implement appropriate solutions.
This could involve balancing, aligning, replacing worn parts, or updating maintenance practices.
It’s essential to verify that the solutions effectively reduce vibration levels.
Continuous Monitoring
After resolving the issues, continue to monitor vibration levels to ensure the problem does not recur.
Regular monitoring facilitates early detection of potential issues before they escalate.
Conclusion
Understanding the basics of vibration and implementing effective rotor vibration reduction measures are crucial for maintaining machinery efficiency and longevity.
Regular maintenance, balancing, alignment, and vibration monitoring can significantly mitigate vibration issues.
In cases where vibration problems occur, a systematic troubleshooting approach helps identify and rectify the root causes.
By prioritizing vibration control and prevention, industries can optimize their equipment’s performance and avoid costly disruptions.
資料ダウンロード
QCD管理受発注クラウド「newji」は、受発注部門で必要なQCD管理全てを備えた、現場特化型兼クラウド型の今世紀最高の受発注管理システムとなります。
ユーザー登録
受発注業務の効率化だけでなく、システムを導入することで、コスト削減や製品・資材のステータス可視化のほか、属人化していた受発注情報の共有化による内部不正防止や統制にも役立ちます。
NEWJI DX
製造業に特化したデジタルトランスフォーメーション(DX)の実現を目指す請負開発型のコンサルティングサービスです。AI、iPaaS、および先端の技術を駆使して、製造プロセスの効率化、業務効率化、チームワーク強化、コスト削減、品質向上を実現します。このサービスは、製造業の課題を深く理解し、それに対する最適なデジタルソリューションを提供することで、企業が持続的な成長とイノベーションを達成できるようサポートします。
製造業ニュース解説
製造業、主に購買・調達部門にお勤めの方々に向けた情報を配信しております。
新任の方やベテランの方、管理職を対象とした幅広いコンテンツをご用意しております。
お問い合わせ
コストダウンが利益に直結する術だと理解していても、なかなか前に進めることができない状況。そんな時は、newjiのコストダウン自動化機能で大きく利益貢献しよう!
(β版非公開)