- お役立ち記事
- Basics of visual servo control and application to mobile robots
月間76,176名の
製造業ご担当者様が閲覧しています*
*2025年3月31日現在のGoogle Analyticsのデータより
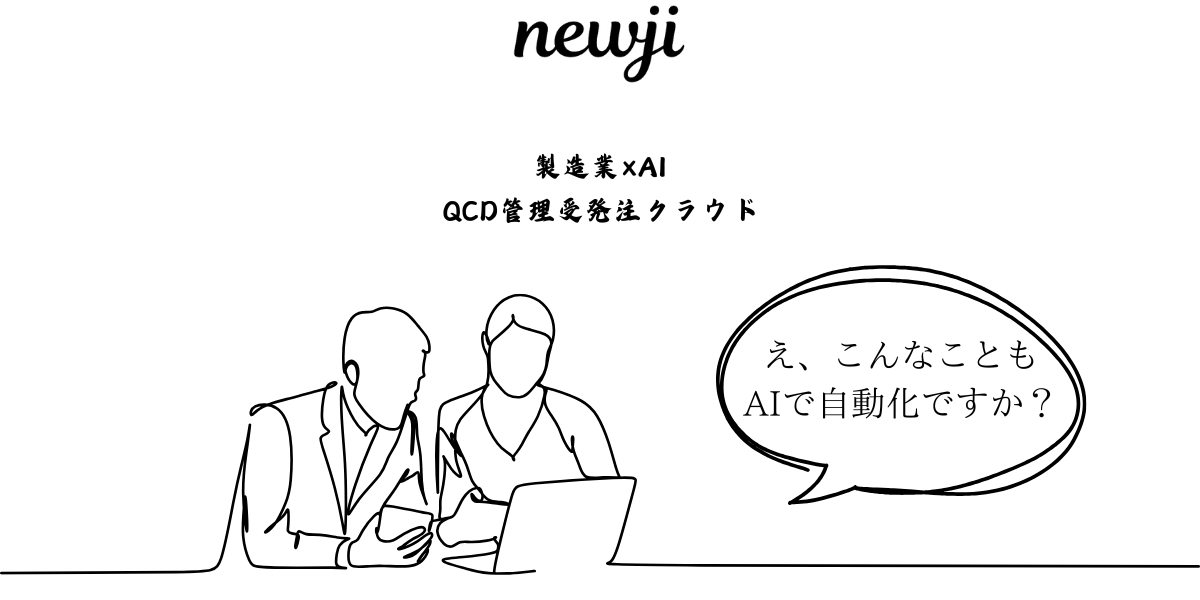
Basics of visual servo control and application to mobile robots
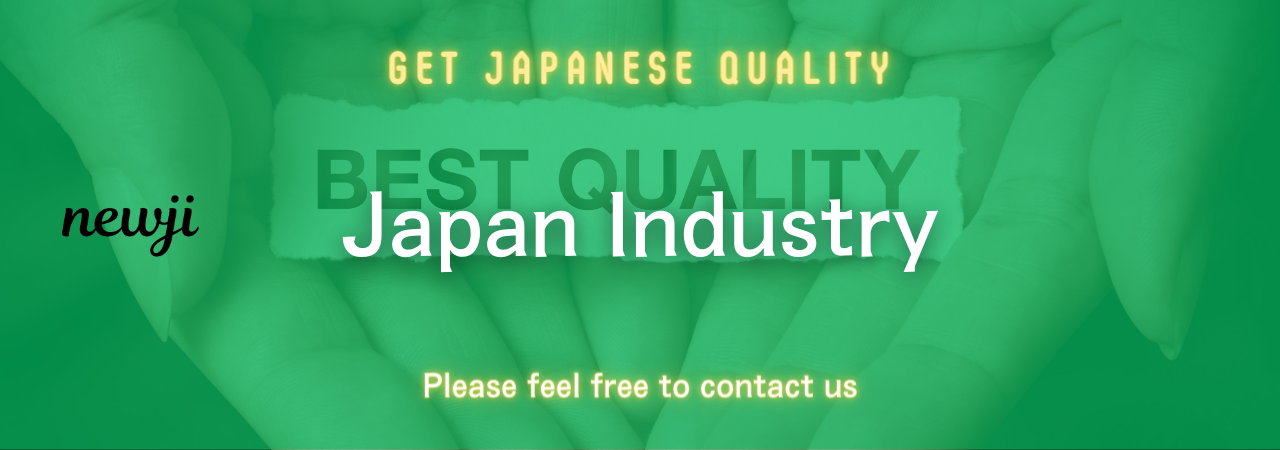
目次
Understanding Visual Servo Control
Visual servo control refers to the technique of using vision data to control the motion of a robot.
This involves using information from cameras or visual sensors to guide robotic movements, ensuring precision and efficiency.
In simpler terms, it helps a robot see and react to its environment, enabling it to perform tasks like picking items, assembling products, or navigating spaces.
Visual servo control is foundational in robotics, offering robots the ability to adapt to dynamic surroundings.
Components of Visual Servo Control
Visual servo control systems typically comprise several key components.
The visual sensor, usually a camera, captures images or video from the robot’s surroundings.
The motion controller processes these visuals to determine how the robot should move.
An actuator then converts these commands into physical motion, adjusting the robot’s position or orientation.
The feedback loop between the sensor and controller is essential for this process, continually updating to refine the robot’s actions.
Types of Visual Servo Control
1. **Position-Based Visual Servo (PBVS):**
This method uses images to determine the position of an object relative to the robot.
PBVS processes the camera images to calculate exact positions and orientations, allowing precise control of the robot’s movements.
While highly accurate, it requires complex algorithms and may struggle with dynamic or unpredictable environments.
2. **Image-Based Visual Servo (IBVS):**
IBVS focuses on features within the image itself, such as shapes or edges, to guide motion.
Instead of calculating positions, it adjusts the robot’s movements based on changes to these features within the camera’s view.
IBVS is robust in dynamic environments but might lack accuracy if the image changes significantly or rapidly.
3. **Hybrid Visual Servo Control:**
This integrates both PBVS and IBVS, utilizing the strengths of each approach.
By combining precise positional data with feature-based adjustments, hybrid systems achieve both accuracy and adaptability.
These systems are ideal for complex tasks where both precision and reaction to changes are critical.
Applications of Visual Servo Control in Mobile Robots
Visual servo control is increasingly being applied to mobile robots, enhancing their ability to navigate and operate autonomously.
Navigation and Path Planning
Mobile robots equipped with visual servo control can autonomously navigate through complex environments.
By processing visual data, these robots determine their route and avoid obstacles in real-time.
This capability is crucial for tasks in warehouses, hospitals, and urban environments where dynamic changes and obstacles are common.
Object Tracking and Following
Another application is object tracking, where robots follow moving objects or maintain a fixed distance from them.
This function is beneficial in surveillance, logistics, and service industries.
For instance, a mobile robot can deliver items by following a human operator or track packages in a distribution center.
Assembly and Manufacturing
In manufacturing, visual servo control enables mobile robots to perform assembly tasks with precision.
Robots equipped with vision sensors can work alongside humans, assembling parts with accuracy.
This not only improves efficiency but also allows for automation in fields requiring flexibility and adaptability.
Inspection and Maintenance
Mobile robots use visual servo control for inspection tasks in industries like oil and gas, nuclear, and aviation.
They can navigate environments, spotting defects or anomalies with precision.
This capability minimizes human risk and enhances efficiency in maintaining critical infrastructure.
Challenges and Future Directions
While visual servo control offers significant advantages, it faces challenges that require ongoing research and development.
Complex Environments
Handling complex or unstructured environments remains a challenge for visual servo systems.
Ongoing developments in AI and machine learning aim to improve system adaptability and decision-making capabilities.
Processing Speed
Visual data processing demands significant computational power.
Future advancements in processors and algorithms are necessary to enhance speed and responsiveness, enabling real-time navigation and task execution.
Integration with Other Sensors
Combining visual servo control with other sensors like lidar or radar could improve accuracy and reliability.
Multisensory integration can offer robust solutions for environments where visual data alone is insufficient.
Advancements in AI and Machine Learning
AI and machine learning play a pivotal role in advancing visual servo control.
These technologies enhance the ability of robots to interpret and react to complex visual data, improving adaptability and performance.
In conclusion, visual servo control is a transformative technology in robotics, especially for mobile robots.
By enabling robots to perceive and react to their environments, it lays the foundation for advanced applications across multiple industries.
As technology advances, the capabilities and applications of visual servo control will continue to expand, driving innovation in autonomous systems.
資料ダウンロード
QCD管理受発注クラウド「newji」は、受発注部門で必要なQCD管理全てを備えた、現場特化型兼クラウド型の今世紀最高の受発注管理システムとなります。
ユーザー登録
受発注業務の効率化だけでなく、システムを導入することで、コスト削減や製品・資材のステータス可視化のほか、属人化していた受発注情報の共有化による内部不正防止や統制にも役立ちます。
NEWJI DX
製造業に特化したデジタルトランスフォーメーション(DX)の実現を目指す請負開発型のコンサルティングサービスです。AI、iPaaS、および先端の技術を駆使して、製造プロセスの効率化、業務効率化、チームワーク強化、コスト削減、品質向上を実現します。このサービスは、製造業の課題を深く理解し、それに対する最適なデジタルソリューションを提供することで、企業が持続的な成長とイノベーションを達成できるようサポートします。
製造業ニュース解説
製造業、主に購買・調達部門にお勤めの方々に向けた情報を配信しております。
新任の方やベテランの方、管理職を対象とした幅広いコンテンツをご用意しております。
お問い合わせ
コストダウンが利益に直結する術だと理解していても、なかなか前に進めることができない状況。そんな時は、newjiのコストダウン自動化機能で大きく利益貢献しよう!
(β版非公開)