- お役立ち記事
- Basics of Weibull analysis and utilization and practical points of “reliability performance estimation method”
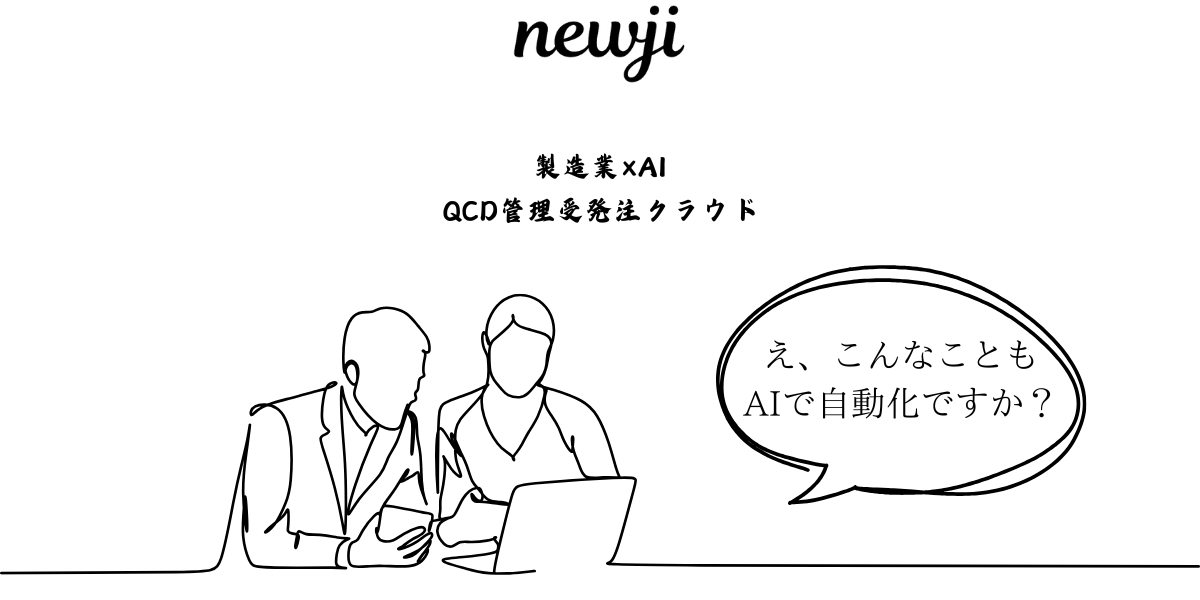
Basics of Weibull analysis and utilization and practical points of “reliability performance estimation method”
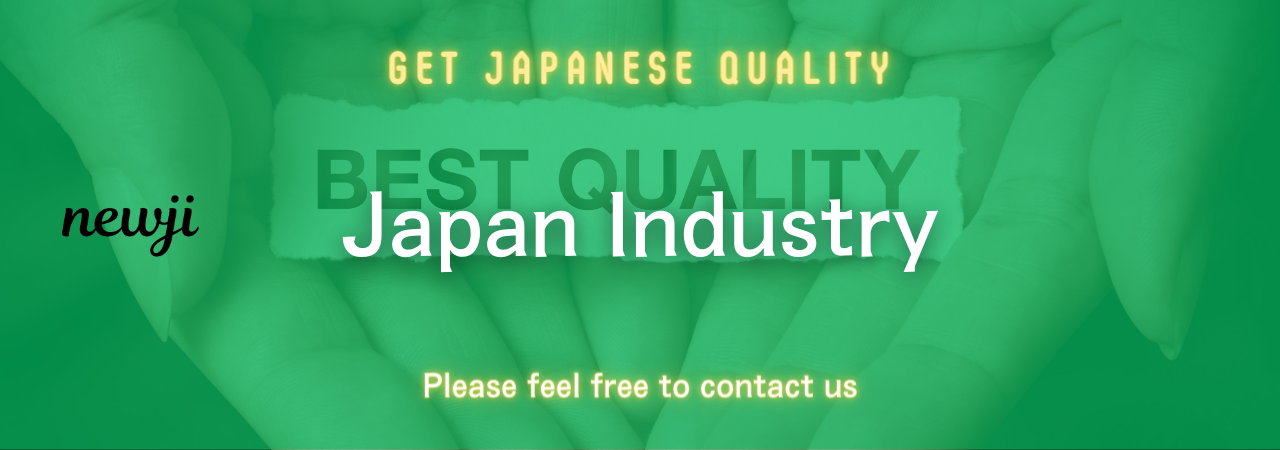
目次
Understanding Weibull Analysis
Weibull analysis is a statistical method used to evaluate reliability data, estimate life data distribution, and analyze failure times.
It’s primarily used in engineering, manufacturing, and quality control to assess product reliability and predict performance.
Hailed for its flexibility, Weibull analysis can model various types of data, making it particularly useful in fields where understanding equipment failure and lifetime distribution is crucial.
Foundation of Weibull Distribution
The Weibull distribution, named after Swedish mathematician Waloddi Weibull, is a continuous probability distribution.
It’s capable of modeling a wide range of behaviors observed in failure data, depending on its parameters.
The primary parameters of the Weibull distribution are:
– **Shape parameter (beta):** Determines the failure rate trend.
A beta less than one indicates that the failure rate decreases over time.
A beta equal to one points to a constant failure rate.
A beta higher than one suggests that the failure rate increases over time.
– **Scale parameter (eta):** Reflects the characteristic life of a product, which is the point at which 63.2% of units are expected to fail under normal conditions.
Applications of Weibull Analysis
Weibull analysis is valuable in a variety of practices:
– **Reliability Engineering:** Engineers use Weibull analysis for reliability testing, life data analysis, and reliability prediction.
It helps determine if a product will perform its intended function over a specified period without failure.
– **Quality Control:** By analyzing and optimizing manufacturing processes, Weibull analysis helps in improving product quality and minimizing defects.
– **Preventive Maintenance:** Maintenance programs use Weibull analysis to predict failures and schedule maintenance before they occur, reducing downtime and saving costs.
Reliability Performance Estimation
Reliability performance estimation involves predicting the likelihood that a product or system will function as expected under a given set of conditions and for a specified time period.
This process is crucial for decision-making in design, manufacturing, and maintenance strategies.
Steps to Perform Reliability Performance Estimation
1. **Data Collection and Analysis:**
Gathering accurate failure data is the first step in estimating reliability performance.
This data typically includes time-to-failure or cycles to failure information, which is then analyzed using statistical techniques such as Weibull.
2. **Model Selection and Parameter Estimation:**
Choose the correct model distribution that fits the failure data.
In many cases, the Weibull distribution is selected due to its adaptability.
Parameters are estimated using methods like Maximum Likelihood Estimation (MLE) or Rank Regression.
3. **Reliability Calculation:**
Calculate the reliability of the product at different time intervals.
This provides insights into the probability of survival over time, allowing organizations to plan appropriately for replacements or improvements.
4. **Decision Making:**
Use the insights obtained from reliability calculations to make informed decisions on improvements in design, materials, or processes to enhance product reliability.
Practical Points for Effective Utilization
– **Regular Data Updates:** As new failure data becomes available, regularly update your analysis to reflect the most accurate reliability predictions.
– **Consider Environmental Factors:** Account for environmental stresses that products may face as these can significantly impact reliability data.
– **Combine with Other Methods:** Pair Weibull analysis with other reliability techniques, such as Failure Modes and Effects Analysis (FMEA), for comprehensive insights.
– **Training and Expertise:** Ensure that personnel conducting Weibull analysis are well-trained and understand both the statistical methods and the practical implications of their results.
Challenges and Considerations
While Weibull analysis provides robust tools for predicting and improving reliability, several challenges and considerations deserve attention:
– **Data Limitations:** Obtaining accurate failure data can be challenging, especially in cases where failures are infrequent or testing is impractical.
– **Correct Model Selection:** Selecting the wrong model can lead to inaccurate predictions.
Understanding the failure mechanisms and historical data patterns is crucial.
– **Interpretation of Results:** Misinterpretation of Weibull parameters can lead to incorrect conclusions.
It’s important to understand what the parameters genuinely represent about the product’s reliability.
Conclusion
Weibull analysis is a powerful tool for assessing and predicting product reliability.
By understanding its principles and applying its methods correctly, engineers and quality professionals can enhance product design, optimize maintenance strategies, and improve overall product performance.
Through diligent data collection, model selection, and analysis, organizations can significantly increase their understanding of product behavior over time and make well-informed decisions to drive reliability and quality improvements.
資料ダウンロード
QCD調達購買管理クラウド「newji」は、調達購買部門で必要なQCD管理全てを備えた、現場特化型兼クラウド型の今世紀最高の購買管理システムとなります。
ユーザー登録
調達購買業務の効率化だけでなく、システムを導入することで、コスト削減や製品・資材のステータス可視化のほか、属人化していた購買情報の共有化による内部不正防止や統制にも役立ちます。
NEWJI DX
製造業に特化したデジタルトランスフォーメーション(DX)の実現を目指す請負開発型のコンサルティングサービスです。AI、iPaaS、および先端の技術を駆使して、製造プロセスの効率化、業務効率化、チームワーク強化、コスト削減、品質向上を実現します。このサービスは、製造業の課題を深く理解し、それに対する最適なデジタルソリューションを提供することで、企業が持続的な成長とイノベーションを達成できるようサポートします。
オンライン講座
製造業、主に購買・調達部門にお勤めの方々に向けた情報を配信しております。
新任の方やベテランの方、管理職を対象とした幅広いコンテンツをご用意しております。
お問い合わせ
コストダウンが利益に直結する術だと理解していても、なかなか前に進めることができない状況。そんな時は、newjiのコストダウン自動化機能で大きく利益貢献しよう!
(Β版非公開)