- お役立ち記事
- Benchmarking method for improving procurement efficiency in the manufacturing industry
月間76,176名の
製造業ご担当者様が閲覧しています*
*2025年3月31日現在のGoogle Analyticsのデータより
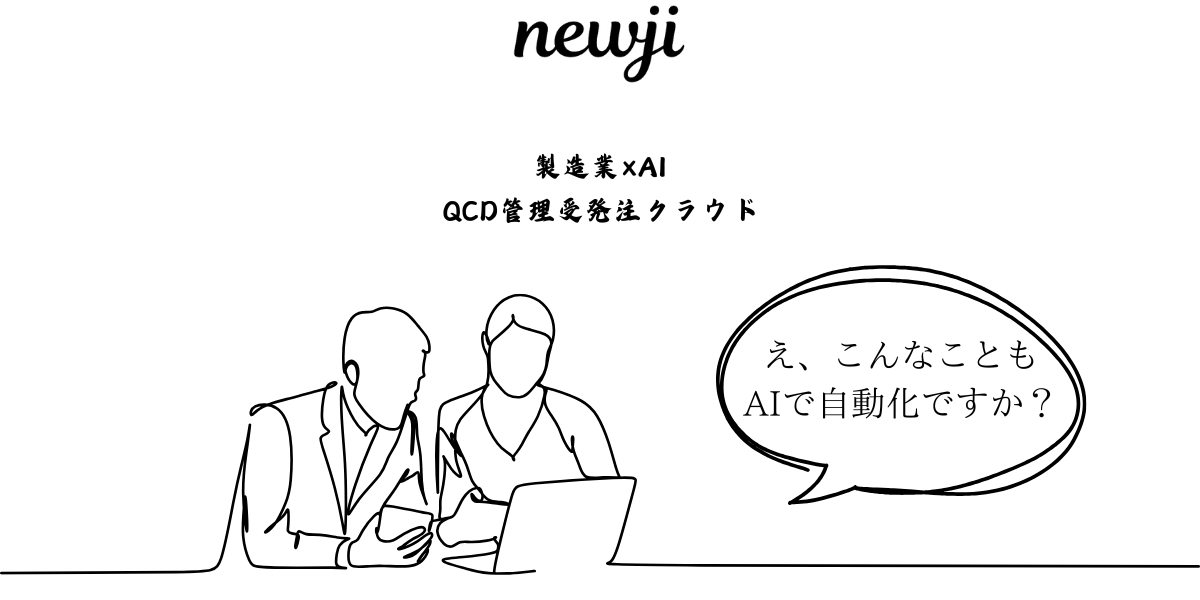
Benchmarking method for improving procurement efficiency in the manufacturing industry
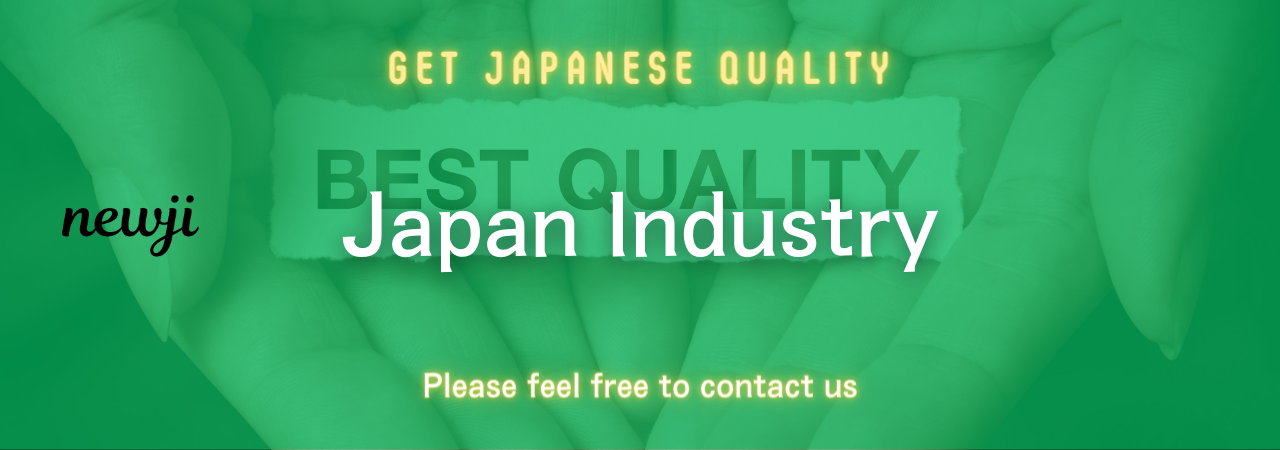
Improving procurement efficiency in the manufacturing industry is crucial for maintaining competitiveness and profitability.
One effective approach to enhancing procurement processes is through benchmarking.
This method allows organizations to compare and measure their procurement practices against industry best practices or competitors, identifying areas where improvements can be made.
目次
Understanding Benchmarking in Procurement
Benchmarking is a systematic process used to evaluate the performance of procurement activities by comparing them against those of leading organizations in the manufacturing sector.
The main goal is to identify best practices, performance gaps, and strategies for improving efficiency.
By doing so, businesses can enhance their procurement processes, reduce costs, and improve overall supply chain performance.
Benefits of Benchmarking
There are several advantages to using benchmarking within procurement:
1. **Identifying Best Practices**: Benchmarking helps organizations to pinpoint what industry leaders are doing right, allowing them to incorporate these practices into their procedures.
2. **Performance Improvement**: Through benchmarking, manufacturers can identify areas where their procurement operations fall short and implement strategies for improvement.
3. **Cost Reduction**: By comparing themselves to top-performing companies, manufacturers can find ways to reduce costs, whether through better negotiation tactics or more efficient supply chain management.
4. **Enhanced Strategic Planning**: Understanding where an organization stands in the industry enables better strategic planning and resource allocation.
Steps to Benchmark Procurement Efficiency
Engaging in effective benchmarking involves several key steps:
Selecting Comparable Companies
Start by identifying companies within the manufacturing industry that have similar procurement needs but excel in efficiency.
These could include direct competitors or businesses known for their procurement excellence.
Defining Key Metrics
To ensure a meaningful comparison, it’s essential to define the metrics that will be used in the benchmarking process.
These might include cost savings, negotiation effectiveness, supplier diversity, purchase order cycle time, and supplier lead time.
Choose metrics that align with your organizational goals and enable you to measure the most critical aspects of procurement.
Data Collection
Gather data from selected companies as well as from your organization.
This data can be obtained through surveys, interviews, industry reports, or outsourcing firms specializing in benchmarking.
It’s crucial to ensure the data is accurate, relevant, and up-to-date.
Analyzing the Data
Once collected, analyze the data to identify performance gaps between your organization and the benchmark companies.
This will involve looking at both quantitative metrics (like cost savings percentages) and qualitative aspects (such as supplier relationship management).
Identifying Improvement Opportunities
With the performance gaps in hand, determine specific areas where improvements can be made.
For example, if your purchase order cycle time is significantly longer than the benchmark, look into streamlining that process.
Implementing Changes
Develop a detailed action plan to address identified gaps.
This plan should outline steps to improve efficiency, assign responsibilities for each task, and set deadlines.
Communication and training are crucial components to ensure everyone involved understands and buys into the changes.
Monitoring Progress
Continuous monitoring and evaluation are key to successful benchmarking.
Regularly check progress against the action plan to ensure that improvements are taking place.
Make adjustments as necessary and celebrate milestones to maintain momentum.
Challenges in Benchmarking
While benchmarking is a powerful tool, there are challenges that organizations may face:
Data Availability
Accessing the right data can be difficult.
Sometimes companies are unwilling to share their internal data, and external sources may not always be reliable.
Comparability
Even if data is available, ensuring that it’s comparable across different companies or industries can be tricky due to differences in size, structure, or market conditions.
Resistance to Change
Implementing changes based on benchmarking findings can often meet resistance from staff.
Overcoming this requires strong leadership and a clear communication strategy highlighting the benefits of change.
Conclusion
Benchmarking is a vital method for improving procurement efficiency in the manufacturing industry.
By systematically comparing procurement practices with those of industry leaders, organizations can leverage best practices and close performance gaps.
Despite challenges in data collection and change management, the benefits of benchmarking – including cost savings, strategic insights, and enhanced performance – make it an essential strategy for any company looking to gain a competitive edge in their supply chain operations.
As with all continuous improvement efforts, success depends on commitment and persistence, making benchmarking a long-term yet worthwhile endeavor.
資料ダウンロード
QCD管理受発注クラウド「newji」は、受発注部門で必要なQCD管理全てを備えた、現場特化型兼クラウド型の今世紀最高の受発注管理システムとなります。
ユーザー登録
受発注業務の効率化だけでなく、システムを導入することで、コスト削減や製品・資材のステータス可視化のほか、属人化していた受発注情報の共有化による内部不正防止や統制にも役立ちます。
NEWJI DX
製造業に特化したデジタルトランスフォーメーション(DX)の実現を目指す請負開発型のコンサルティングサービスです。AI、iPaaS、および先端の技術を駆使して、製造プロセスの効率化、業務効率化、チームワーク強化、コスト削減、品質向上を実現します。このサービスは、製造業の課題を深く理解し、それに対する最適なデジタルソリューションを提供することで、企業が持続的な成長とイノベーションを達成できるようサポートします。
製造業ニュース解説
製造業、主に購買・調達部門にお勤めの方々に向けた情報を配信しております。
新任の方やベテランの方、管理職を対象とした幅広いコンテンツをご用意しております。
お問い合わせ
コストダウンが利益に直結する術だと理解していても、なかなか前に進めることができない状況。そんな時は、newjiのコストダウン自動化機能で大きく利益貢献しよう!
(β版非公開)